Índice técnico principal del método de conducción del cortador láser
ataque
La carrera de una cortadora láser es el rango de procesamiento que puede realizar, lo que determina el tamaño máximo de pieza que se puede procesar y es un parámetro fundamental.
El rango de procesamiento más común actualmente es de 3 mx 1,5 m, lo que ofrece un buen equilibrio entre capacidades mecánicas, rango de procesamiento y costos de fabricación.
Sin embargo, a medida que el nivel industrial mundial continúa mejorando, la proporción de modelos más grandes ha aumentado año tras año.
Precisión de posicionamiento
Como máquinas herramienta especializadas, las máquinas de corte por láser son similares a las máquinas herramienta en frío tradicionales. El marco general de transmisión es esencialmente el mismo. Sin embargo, el corte por láser normalmente no se utiliza para fines de mecanizado de precisión, por lo que la precisión absoluta de la transmisión es ligeramente menor que la de las máquinas herramienta NC en frío.
La precisión de posicionamiento de la máquina refleja el posicionamiento del fabricante, la entrada del producto y el grado de precisión de las piezas de transmisión seleccionadas. Sin embargo, para el corte por láser, la precisión del posicionamiento no tiene un efecto significativo en el resultado final del procesamiento, como las tolerancias del tamaño de la pieza y la calidad de la sección cortada.
Sin embargo, para cortes finos, el equipo de corte por láser puede cortar con precisión dentro de una docena de micrones de la hendidura, lo que está al mismo nivel que la precisión operativa del cortador por láser. En este punto, la precisión del posicionamiento se vuelve muy importante.
Precisión de reposicionamiento
La precisión de reposicionamiento lograda por una máquina de corte por láser depende en gran medida del juego inverso de la cadena de transmisión, que es similar al mecanizado en frío tradicional.
La holgura inversa de la máquina de corte por láser también tiene cierta influencia en la rugosidad de la sección cortada. Los usuarios que son muy exigentes con la calidad del corte de secciones deben prestar mucha atención a este indicador.
Velocidad de posicionamiento
La velocidad de posicionamiento, que es el parámetro técnico más evidente visualmente, es un índice clave al que todos los fabricantes de cortadoras láser prestan atención. A menudo se utiliza como criterio principal para clasificar las propiedades mecánicas y las clases de cortadores láser.
En la actualidad, los mejores modelos han superado sucesivamente la velocidad de posicionamiento de un solo eje de 100 m/min. La alta velocidad de posicionamiento tiene un impacto significativo en la mejora de la eficiencia del procesamiento de hojas.
Sin embargo, para láminas de espesor medio, debido a las limitaciones de la velocidad de corte, reducir el tiempo total de procesamiento puede no ser tan crucial.
Fuerza motriz
Debido a la alta flexibilidad del procesamiento láser, el corte a alta velocidad de piezas complejas se ha convertido en el método principal para que varios fabricantes exhiban propiedades mecánicas.
El corte a alta velocidad requiere una salida de par elevada al motor. La cadena de transmisión requiere alta eficiencia y respuesta rápida para garantizar la precisión del seguimiento y cumplir con los requisitos de supresión. Por tanto, la aceleración es tan crítica como la velocidad de posicionamiento.
Sin embargo, existe un equilibrio entre alta velocidad y alta aceleración. Esto requiere que los fabricantes de cortadores equilibren cuidadosamente la relación y encuentren la solución óptima mediante el cálculo y la experimentación.
Rigidez de transmisión
Durante el proceso de alta velocidad de una máquina de corte por láser, la tensión interna de la cadena de transmisión puede fluctuar violentamente. Si la rigidez de la transmisión es insuficiente, fácilmente puede causar distorsión de la vía y una respuesta lenta de la salida final. Esto hace que la precisión de la operación dinámica esté lejos de valores de medición bajos o estáticos, lo que puede afectar la precisión dimensional y la rugosidad de la pieza de trabajo.
Sin embargo, este índice no es fácil de cuantificar.
4 métodos de conducción de máquinas de corte por láser
Transmisión por correa síncrona
La correa síncrona de distribución (mostrada en la Figura 1) se compone principalmente de poleas y correas.
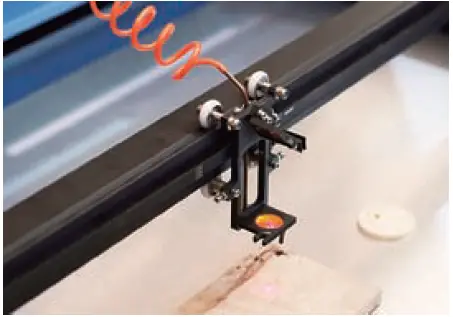
Fig.1 Transmisión por correa síncrona
Normalmente, la rueda motriz y el servomotor también utilizan un reductor para amplificar el par cuando se utiliza la correa dentada síncrona (como se muestra en la Figura 1).
La correa síncrona de distribución tiene ventajas como velocidad rápida, bajo nivel de ruido, bajo costo, sin necesidad de lubricación y fácil mantenimiento. Sin embargo, tiene desventajas como diferencias de rigidez, fácil desgaste, baja precisión y pequeña fuerza motriz. Por lo tanto, es adecuado para aplicaciones de bajo costo, carga ligera y alta velocidad.
Se utiliza ampliamente en equipos de marcado y corte por láser de pequeña y mediana potencia, que son de bajo costo y no requieren alta precisión.
Para equipos de corte por láser de alta velocidad y alta precisión, la precisión de funcionamiento de la correa síncrona obviamente no es suficiente y la capacidad de carga tampoco es suficiente para impulsar directamente piezas móviles pesadas, rígidas y de gran tamaño. La disposición más común es colocarlo en la cadena de transmisión de husillos de bolas de alta velocidad y otras instituciones para formar una transmisión de dos etapas.
En el producto básico de las máquinas de corte por láser de alta potencia, el accionamiento del eje Z es impulsado directamente por la correa síncrona (como se muestra en la figura 2).
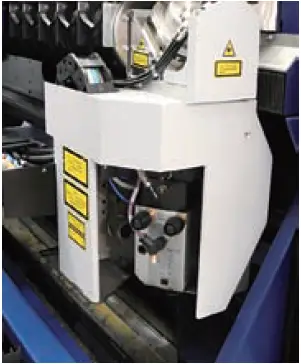
Fig.2 El movimiento superior e inferior del cabezal de corte de secciones del eje z es impulsado por la correa sincrónica.
Para una máquina bidimensional con un sistema de tres ejes, la precisión de la transmisión del eje z normalmente no afecta la precisión y calidad del corte.
Este diseño aprovecha de manera inteligente los beneficios de la transmisión por correa síncrona, como velocidad rápida, bajo nivel de ruido y bajo costo, evitando al mismo tiempo la desventaja de la baja precisión.
Accionamiento por husillo de bolas
El husillo de bolas (que se muestra en la Figura 3) es un mecanismo de accionamiento comúnmente utilizado en varios tipos de equipos de procesamiento en frío. Esta tecnología ha sido ampliamente desarrollada y su costo es razonable.
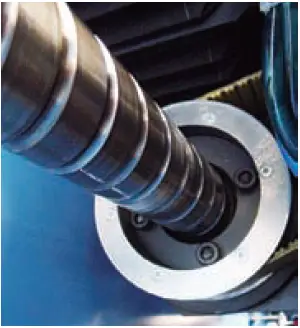
Fig.3 Tuerca de husillo de bolas giratoria
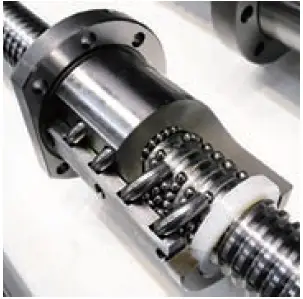
Fig.4 Estructura interna del husillo de bolas.
El husillo de bolas es un mecanismo de accionamiento ampliamente utilizado en diversos equipos de procesamiento en frío debido a su capacidad para lograr un juego cero y mantener una alta eficiencia de transmisión y rigidez mediante la aplicación de presión previa o excursión de alimentación. También puede alcanzar hasta un 95% de eficiencia de transmisión, lo que lo convierte en un método de conducción ideal para una variedad de aplicaciones.
Sin embargo, el uso de un husillo de bolas en una máquina de corte por láser tiene limitaciones. Debido a su peso, el husillo de bolas normalmente se apoya en dos extremos, lo que produce una cierta inclinación en el centro del husillo. Esta desviación puede causar inestabilidad, especialmente a altas velocidades.
Para resolver este problema, se debe seleccionar alambrón más grueso, lo que puede aumentar los costos de fabricación y suponer una carga más pesada para el motor. Por lo tanto, el husillo de bolas es una excelente opción para métodos de accionamiento en cortadoras láser con carrera corta y área de corte pequeña, ya que su precisión, velocidad y costo son adecuados para tales aplicaciones.
Sin embargo, para aplicaciones de carrera larga (≥3 m) y alta velocidad (≥60 m/min), integrar un destornillador de bolas no es el método ideal. Si bien es posible lograr aplicaciones de carrera larga y alta velocidad con un husillo de bolas girando la tuerca o agregando un dispositivo de soporte auxiliar para evitar el movimiento de la tuerca, estas soluciones son técnicamente desafiantes y enfrentan desafíos importantes en términos de costo y confiabilidad.
Engranaje y cremallera
La cremallera se combina comúnmente con reductores de engranajes planetarios o reductores de tornillo sin fin de turbina para igualar la inercia y amplificar el torque. Algunos fabricantes también utilizan motores torque para conexión directa al engranaje final.
Los bastidores de alta precisión son similares a los husillos de bolas en términos de precisión de posicionamiento, ya que pueden alcanzar fácilmente una precisión de posicionamiento de 0,03 mm/m, que es mayor que la precisión requerida para el corte por láser.
En cuanto a la velocidad, el engranaje y la cremallera pueden lograr varias combinaciones cambiando el número de dientes del engranaje y la relación de velocidad del reductor. No hay límite para la velocidad crítica del husillo de bolas, lo que facilita que los servomotores funcionen en rangos de alta velocidad y acorta el paso equivalente para impulsar grandes cargas de inercia con motores más pequeños.
El límite teórico de engranajes y cremalleras puede alcanzar los 400 m/min, y es fácil alcanzar velocidades de hasta 100 m/min.
Tanto los dientes rectos como los torcidos se utilizan ampliamente en las máquinas de corte por láser. Los dientes torcidos son más fáciles de instalar y detectar y pueden lograr una mayor precisión operativa bajo la misma precisión de mecanizado y condiciones de instalación.
La ventaja de los dientes torcidos es que tienen una capacidad de carga ligeramente mayor bajo la misma carga, lo que hace que el diseño sea más compacto. Además, la diferencia más significativa entre los dos tipos es que el ruido de los dientes torcidos es relativamente bajo a altas velocidades, lo que proporciona un mejor entorno operativo para los operadores.
Mientras la base pueda mantener suficiente precisión y rigidez, el recorrido del bastidor se puede extender casi indefinidamente, con lo que los costos de fabricación aumentan linealmente.
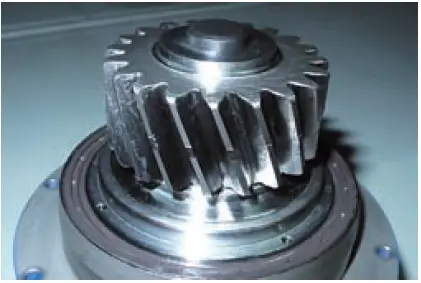
Fig.5 Accionamiento del engranaje de soldadura láser
Sin embargo, la rejilla (Figura 6) también tiene sus desventajas. Por ejemplo, requiere una mayor precisión de mecanizado de la base y el proceso de instalación es más complicado en comparación con el husillo de bolas. Además, debido a la necesidad de lubricación y expansión térmica, hay un juego específico entre la cremallera y el piñón, mientras que el reductor planetario en la cadena de transmisión tiene un juego pequeño pero notable. La acumulación de estos factores dificulta que la cremallera logre un efecto de funcionamiento sin juego, como en el caso de un husillo de bolas.
El uso de motores duales, reductores duales u otros medios elásticos puede compensar estas desventajas, pero esto da como resultado indicadores desfavorables de peso, coste y capacidad de conducción.
Sin embargo, afortunadamente, con un diseño razonable y una construcción precisa, un bastidor de dos etapas puede cumplir con los requisitos de precisión del corte por láser convencional actual. Y todavía hay un amplio margen de desarrollo.
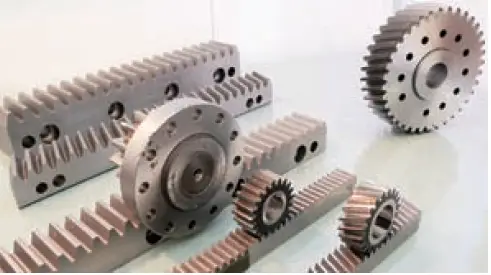
Fig.6 Bastidor de precisión de la máquina de corte por láser
Con una consideración integral, la precisión del piñón y cremallera es capaz de satisfacer las demandas del corte por láser. Este sistema de accionamiento ofrece flexibilidad en la selección, maximiza el rendimiento del servomotor y facilita el logro de un alto rendimiento dinámico.
Como resultado, el accionamiento por cremallera se ha convertido en la principal solución para las máquinas de corte por láser de alta potencia.
Motor lineal
Los motores lineales, como nuevo modo de conducción, se han utilizado ampliamente en diversos equipos NC, incluidas las máquinas de corte por láser.
A continuación se muestran algunas de las claras ventajas de los motores lineales:
(1) No hay contacto mecánico y la transmisión se genera en el entrehierro, lo que no produce desgaste directo del componente impulsor.
(2) La carrera es teóricamente ilimitada y el rendimiento del motor lineal no se ve afectado por los cambios en la ruta.
(3) Puede proporcionar un amplio rango de velocidades desde varios micrómetros hasta varios metros por segundo, siendo la alta velocidad una ventaja destacada.
(4) La aceleración es significativa, hasta 10 g.
(5) Se pueden lograr alta precisión y repetibilidad. Como se elimina el enlace intermedio, la precisión del sistema depende del elemento sensor de posición. Con un dispositivo de retroalimentación adecuado, la precisión operativa final puede alcanzar el nivel submicrónico. Esta característica ha encontrado una amplia aplicación en el campo del corte por láser de precisión.
Gracias por solicitar una revisión de contenido. Aquí está la versión revisada:
Debido a las ventajas de los motores lineales, las máquinas de corte por láser con motores lineales han establecido récords de velocidad y aceleración en la industria. Parece que el motor lineal podría eventualmente reemplazar a los tornillos de bolas y las cremalleras como mecanismo de accionamiento principal para las máquinas de corte por láser.
Sin embargo, con la adopción generalizada de los motores lineales, han surgido nuevos problemas que no se habían previsto anteriormente:
(1) El motor lineal consume mucha energía, especialmente con cargas y aceleraciones elevadas. La corriente instantánea de la máquina puede sobrecargar significativamente el sistema eléctrico del taller.
(2) Se produce una alta vibración debido a la baja rigidez dinámica del motor lineal, que no puede amortiguar el efecto de amortiguación, lo que genera vibraciones resonantes a altas velocidades en otras partes de la máquina.
(3) El motor eléctrico lineal fijado en la parte inferior del banco genera una cantidad significativa de calor. La posición de instalación no favorece la disipación natural del calor, lo que plantea un desafío importante para el control termostático de la cortadora láser.
(4) El eje del motor impulsado por el motor lineal, especialmente el eje vertical, debe estar equipado con un mecanismo de bloqueo adicional, como una abrazadera guía, para garantizar un funcionamiento seguro. Esto aumenta el costo y la complejidad de la cortadora láser.
(5) El motor lineal genera un fuerte campo magnético y atrae limaduras de hierro, lo que puede ser problemático en entornos de corte por láser con una gran cantidad de polvo metálico diminuto que el láser derrite y enfría. Mantener la limpieza interna se convierte en un desafío.
Aunque fabricantes extranjeros como MAZAK y AMADA han introducido modelos motorizados lineales totales o parciales para demostrar su competencia técnica y establecer récords de velocidad, los precios elevados y los rendimientos modestos han hecho que el mercado sea menos receptivo a este tipo de modelos.
A pesar del excelente rendimiento del motor lineal, persisten problemas prácticos en la aplicación de accionamientos de máquinas de corte por láser. Aunque representa una tendencia a futuro, aún queda mucho trabajo por hacer para solucionar estos problemas.
Conclusión
La búsqueda de una excelente respuesta dinámica es un objetivo común entre muchos equipos de mecanizado CNC de precisión, especialmente para el mecanizado de alta velocidad en máquinas de corte por láser.
Lograr este objetivo requiere un diseño de sistema amplio y complejo.
En esencia, una buena carga (ligera, alta rigidez, pequeña inercia), una cadena de transmisión robusta (alta rigidez, respuesta rápida, bajo juego, alta eficiencia, baja fricción) y un motor potente (adaptación de inercia, respuesta rápida, par fuerte). son precisos.
Sin embargo, la mayoría de estos factores entran en conflicto entre sí, lo que hace necesario seleccionarlos científicamente y diseñar el sistema de propulsión de manera razonable.
Cada fabricante tiene su propia comprensión y enfoque únicos para seleccionar y equilibrar estos factores para lograr los mejores resultados.