Introducción
El procesamiento de chapa se refiere al procesamiento en frío de placas de metal de menos de 6 mm. Se puede dividir en dos categorías: procesamiento de estampado, adecuado para la producción en masa, y procesamiento de chapa metálica CNC, adecuado para la producción de lotes pequeños. Esta publicación se centra en analizar y mejorar la ondulación del corte durante el corte y corte por láser de chapa metálica en la producción de lotes pequeños.
El procesamiento de chapa metálica tiene una amplia gama de aplicaciones en industrias como chasis y gabinetes, electrodomésticos, productos de hardware, instrumentos y medidores, vallas publicitarias, lámparas y fabricación de máquinas. Se caracteriza por su rápida velocidad de procesamiento, ciclo corto, pequeña deformación superficial y capacidad para procesar diversos materiales sin herramientas adicionales.
En los últimos años, nuestra empresa ha desarrollado la industria de bibliotecas de discos ópticos para satisfacer la demanda del mercado de lotes pequeños y productos diversos. La parte central de la caja de la biblioteca de discos ópticos es el componente de acción interna, que desempeña un papel crucial en el rendimiento general del mecanismo. La precisión de las dimensiones del proceso de los productos de chapa central dentro del gabinete requiere ±0,1 mm.
Para garantizar la precisión del procesamiento, nuestra empresa utiliza la máquina de estampado láser de fibra óptica de Amada para el corte y corte por láser de productos de chapa metálica, que tiene una precisión de procesamiento de ±0,07 mm/1000 mm.
Sin embargo, durante el proceso de corte y borrado por láser, pueden ocurrir fenómenos de corte anormales, como ondulaciones y rebabas, lo que provoca defectos en el producto y mayores costos de procesamiento.
Mediante un análisis exhaustivo y una comparación de productos defectuosos, se descubrió que la ondulación del corte ocurre principalmente en productos más grandes, con una tasa de defectos de aproximadamente el 10%. Por el contrario, los productos más pequeños tienen una tasa de defectos inferior al 1%. Para reducir las pérdidas de producción y los costes de procesamiento, es fundamental analizar y estudiar el proceso de corte por láser.
Estado de corte y borrado
La máquina compuesta se utiliza para cortar y estampar con láser láminas de metal, con la abrazadera de la máquina sujetando la lámina de metal y moviéndose a lo largo de las direcciones X e Y, como se ilustra en la Fig. 1, que muestra el equipo de procesamiento de lámina de metal y el procesamiento. área.
Sin embargo, durante el procesamiento continuo, la tensión local de la placa se libera, debilitando gradualmente su resistencia y provocando que la placa se tambalee durante el movimiento. Como resultado, se producen ondulaciones en el corte por láser, lo que da lugar a productos mal procesados. El tamaño de la corrugación de corte también se ve afectado por varios factores, como la dirección de procesamiento del producto, la posición de procesamiento inicial y el orden de eliminación del producto, como se muestra en la Figura 2 y la Figura 3.
Además, al cortar productos de gran tamaño se produce una mayor liberación de tensión en la lámina, provocando que la lámina se agite aún más durante el corte de las piezas restantes. Esto da como resultado un corte ondulado, lo que genera mayores costos de procesamiento y desperdicio de material.
Para minimizar este tipo de ocurrencias, es fundamental asegurar la estabilidad y resistencia de la lámina durante el proceso de corte, especialmente cuando se trata de productos de gran tamaño que requieren tiempos de procesamiento más prolongados.
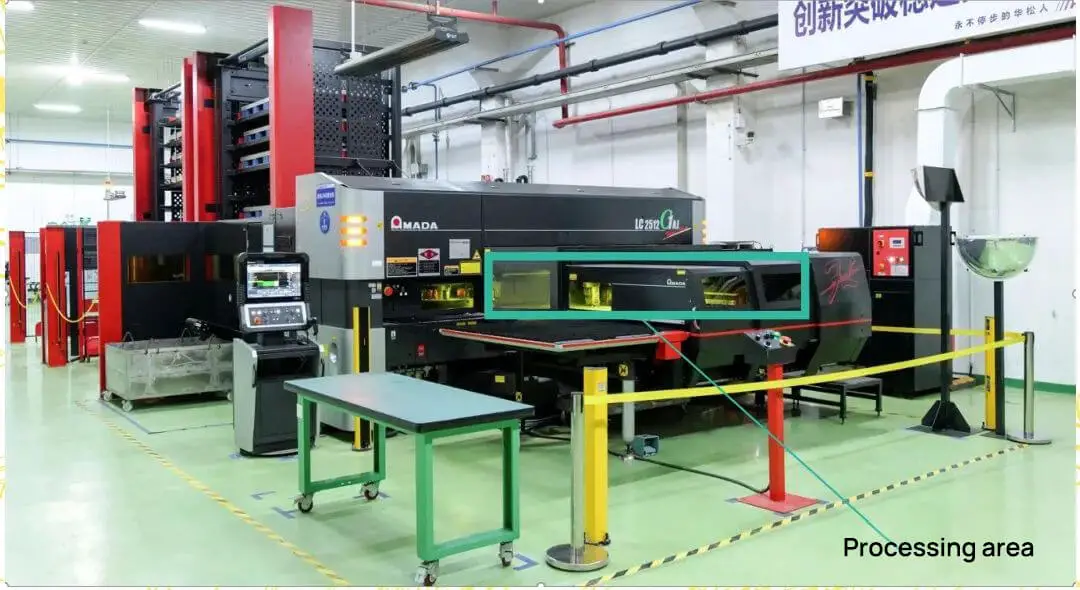
Fig.1 Equipo de procesamiento y área de procesamiento.
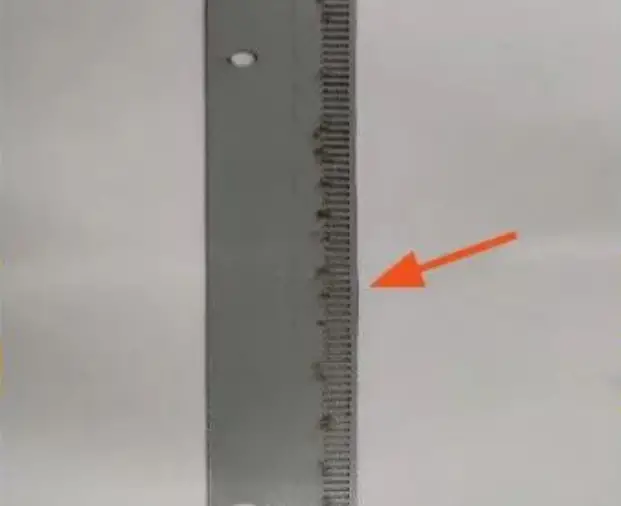
Fig. 2 estado de corrugación de corte 1
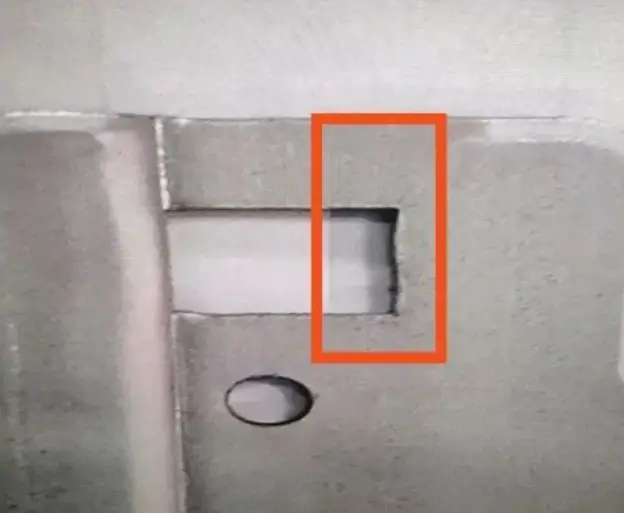
Fig. 3 corte de corrugación estado 2
Factores que influyen en el corte del rizo.
Posición inicial del procesamiento del producto.
Durante el proceso de corte, la posición inicial de los productos juega un papel crucial en la generación de ondas de corte. Normalmente, el mecanizado comienza en el extremo más alejado de la abrazadera o en el extremo más cercano a la abrazadera.
Si el producto se procesa desde una posición alejada de la pinza, como se muestra en la Fig. 4, finalmente se puede cortar la placa en el extremo de la pinza. Este enfoque puede garantizar que la tensión de la placa no se libere antes de tiempo, lo que a su vez garantiza la resistencia y estabilidad de la placa durante el movimiento, evitando en última instancia la aparición de ondulaciones cortantes.
Por otro lado, cuando el producto se procesa desde una posición cercana a la pinza, como se muestra en la Figura 5, la tensión de la placa no se ve comprometida significativamente al comienzo del procesamiento, por lo que es menos probable que se produzcan ondulaciones de corte. Sin embargo, el corte continuo de la placa cerca del extremo de la abrazadera liberará gradualmente la tensión de la placa, lo que provocará que la placa sea inestable durante el movimiento.
Cuando el procesamiento se aleja gradualmente de la abrazadera, es probable que los productos periféricos tengan ondulaciones de corte debido a una resistencia insuficiente de la placa. Por lo tanto, durante la programación, es esencial asegurarse de que los productos se corten comenzando desde el extremo más alejado de la pinza y luego progresivamente hacia el final de la pinza. Este enfoque garantiza la resistencia de la placa y elimina la generación de ondas cortantes.
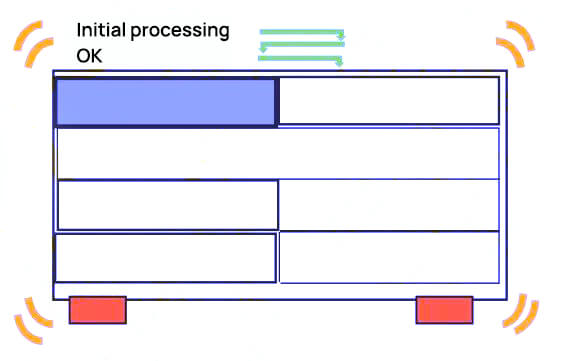
Fig. 4 Buena posición de procesamiento inicial
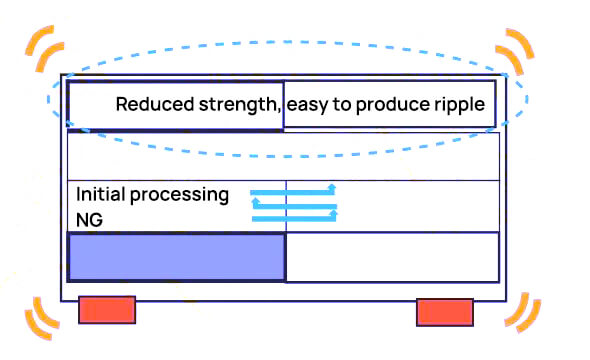
Fig. 5 La posición de procesamiento inicial es mala
Posición del punto de corte y dirección de mecanizado.
Durante el proceso de corte de chapa, el punto de entrada donde comienza el corte se convertirá naturalmente en el punto de salida cuando se complete el corte.
Seleccionar un punto de entrada adecuado puede reducir la probabilidad de que se produzcan ondas de corte.
Al inicio del proceso de corte, debido a la buena resistencia de la lámina, el punto de entrada y la dirección de corte no tienen mucho impacto. Sin embargo, a medida que el proceso de corte se acerca a su fin, el punto de entrada y la dirección del corte se vuelven cruciales para determinar si se producirán ondulaciones de corte en los productos restantes.
Para evitar generar ondas de corte, asegúrese de que los productos cerca del extremo de la abrazadera tengan suficiente resistencia.
Si se selecciona el punto de entrada en el medio del producto y el corte se realiza en el sentido de las agujas del reloj o en el sentido contrario a las agujas del reloj, se cortará primero la parte inferior del producto. Esto da como resultado la liberación de tensión de la placa, lo que reduce la resistencia y estabilidad del producto. En consecuencia, pueden producirse ondulaciones de corte locales, como se muestra en la Figura 6.
Si se selecciona el punto de entrada en el extremo inferior, el producto más cercano al extremo de la abrazadera se cortará en último lugar, lo que significa que la tensión de la placa no se libera antes, lo que hace que el proceso sea más estable y reduce la probabilidad de que se produzcan ondulaciones en el corte. como se muestra en la Figura 7.
Al programar el proceso de corte, asegúrese de seleccionar el punto de entrada y la dirección de corte para que el producto finalmente se corte cerca del final de la abrazadera.
Cuanto más corta sea la distancia recorrida durante el proceso de corte, más ondulaciones se pueden evitar hasta cierto punto. Por supuesto, al seleccionar el punto de entrada en la parte inferior del producto, considere si la dirección de corte es en el sentido de las agujas del reloj o en el sentido contrario a las agujas del reloj.
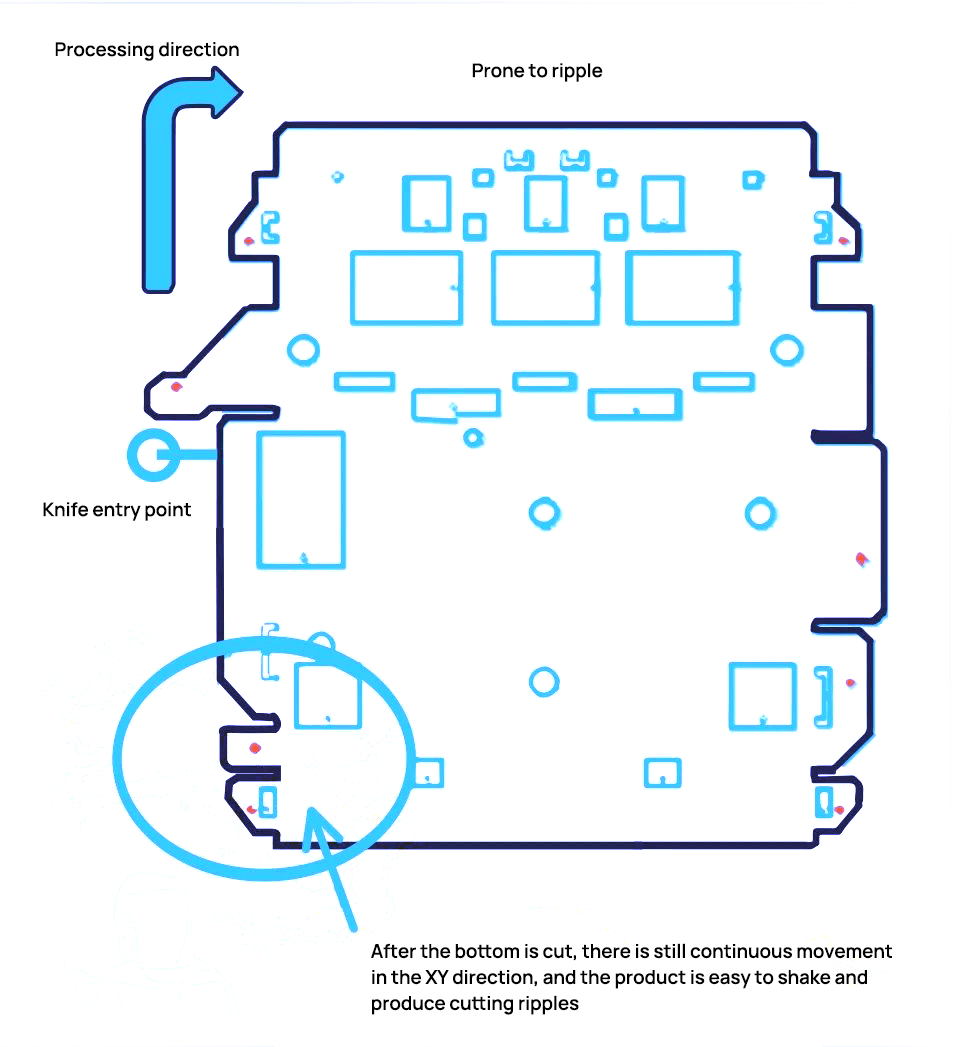
Fig. 6 La posición del punto de corte es mala.
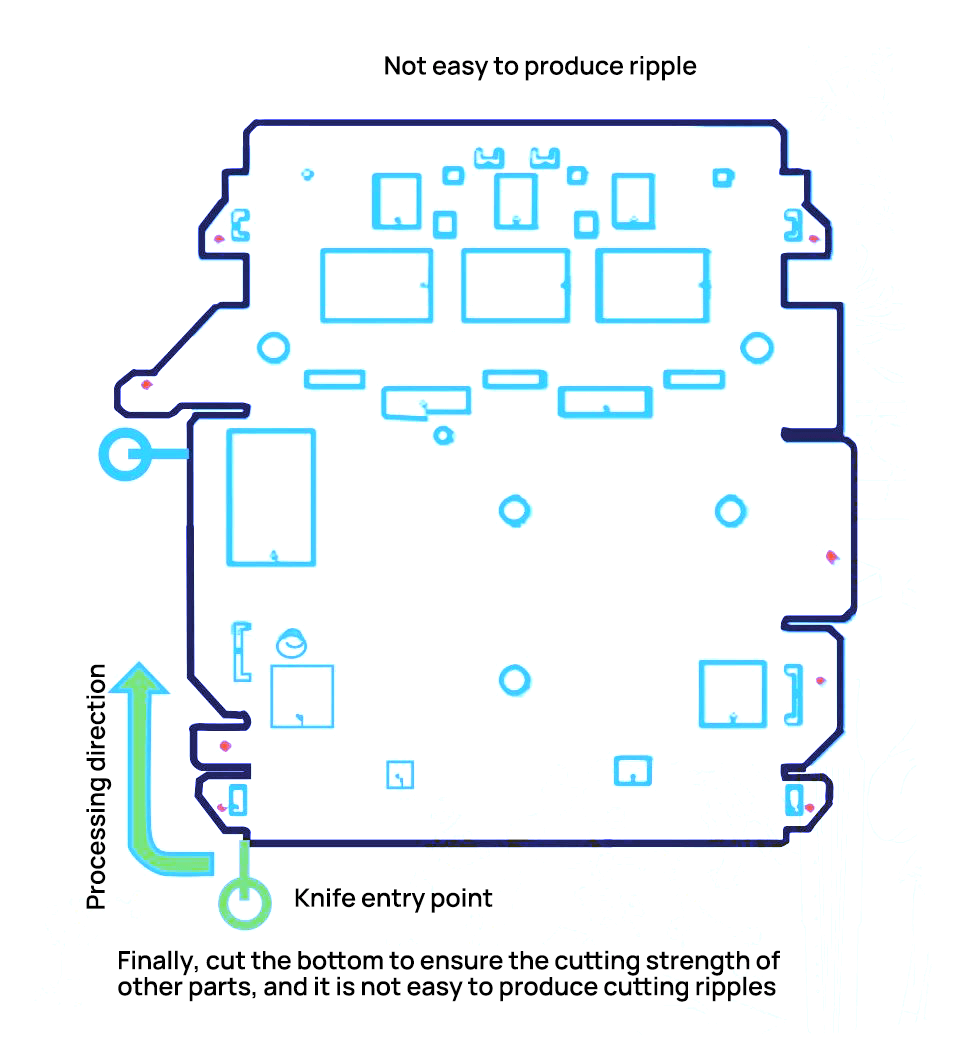
Fig. 7 la posición del punto de corte es buena
Posición de fijación de la abrazadera
La función de las abrazaderas es mantener la placa en su lugar y permitir que se mueva en las direcciones X e Y según el programa de procesamiento. Garantizan la estabilidad del tablero durante la operación de procesamiento. Por lo tanto, es fundamental distribuir uniformemente las posiciones de las abrazaderas, lo que evitará la vibración inestable de las placas provocada por la desviación de las abrazaderas hacia un lado y la generación de ondulaciones cortantes.
La Figura 8 muestra una comparación de las posiciones de las abrazaderas.
Aunque la posición de las abrazaderas puede afectar la ondulación del corte, este factor se puede evitar durante el proceso de operación.

Fig. 8 Posición de fijación de la abrazadera
Secuencia de eliminación del producto
Durante el proceso de producción, el manipulador TK a veces se utiliza para ayudar a sacar los productos cortados, lo que puede ahorrar recursos humanos y materiales y lograr equipos de producción totalmente automatizados. Sin embargo, cuando se utiliza el manipulador TK para retirar productos, es fundamental prestar atención a controlar la secuencia de retirada del producto para evitar debilitar la resistencia y agitación de los materiales que podrían provocar ondulaciones en el corte.
Tomar productos primero de ambos extremos del tablero y luego del centro puede provocar la liberación de tensión en ambos extremos del tablero, lo que resulta en una resistencia insuficiente del tablero. Cuando el programa de procesamiento llega a la mitad de la placa, la placa puede temblar debido a una resistencia insuficiente, lo que provoca ondulaciones de corte en los productos y resulta en altas tasas de defectos del producto y pérdidas de procesamiento, como se muestra en la Figura 9.
Para evitar este problema, es imprescindible retirar los productos sucesivamente por el lado opuesto a las pinzas. Esto asegura que la concentración de tensión de la placa en la posición de procesamiento esté bien distribuida y que el movimiento sea estable, evitando la aparición de ondulaciones de corte, como se muestra en la Figura 10.
Por lo tanto, durante el procesamiento y la programación, es importante garantizar que los productos se retiren secuencialmente desde el extremo más alejado de la pinza para mantener la resistencia de la placa y evitar sacudidas durante el movimiento, evitando así la generación de ondas de corte.
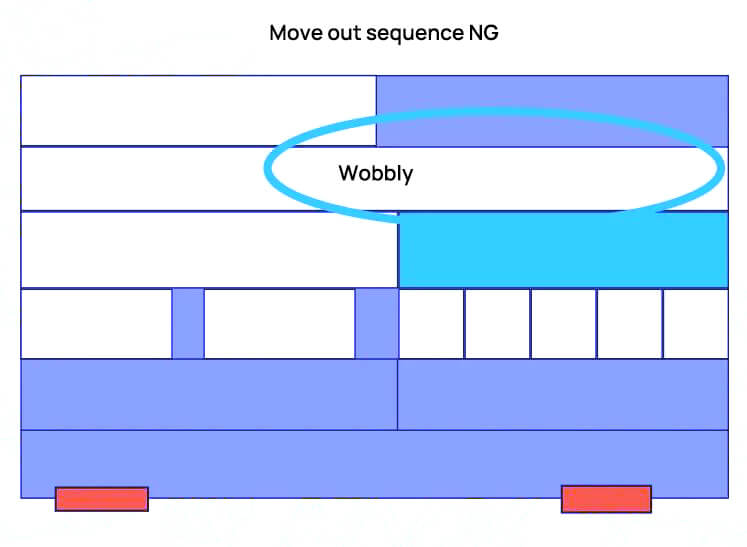
Fig. 9 mala secuencia de eliminación del producto
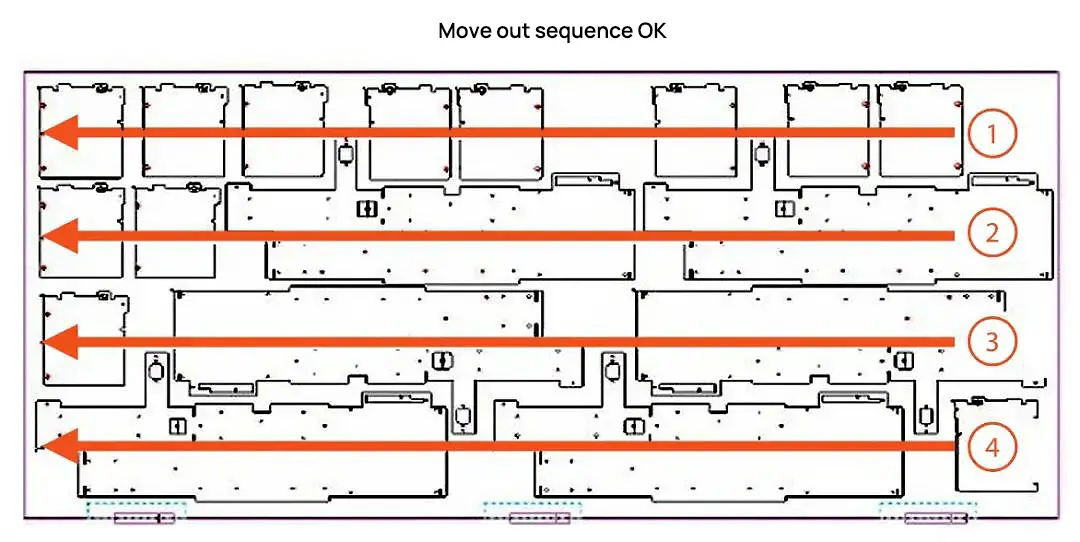
Fig. 10 buena secuencia de retirada del producto
Conclusión
Los factores que influyen en la investigación anterior se basan en un análisis de las ondas cortantes en esta etapa.
La generación de ondas de corte no está influenciada por un solo factor, sino por los efectos combinados de varios factores, incluidos el tamaño, el peso, la velocidad de procesamiento y otros.
Para evitar la generación de ondulaciones de corte, es necesaria una consideración exhaustiva de todos los factores durante el proceso de programación para minimizar la posibilidad de que se produzcan ondulaciones de corte.