Con el crecimiento de la economía, el uso de láminas de acero inoxidable se ha generalizado cada vez más. Ahora se utilizan comúnmente en la industria de la construcción, fabricación de maquinaria, producción de contenedores, construcción naval, construcción de puentes y otros campos.
Actualmente, el corte por láser es el método principal para cortar láminas gruesas de acero inoxidable. La tecnología de corte por láser de placas gruesas de acero inoxidable es cada vez más avanzada y reemplaza gradualmente las técnicas de corte tradicionales.
Para obtener un resultado de corte de alta calidad, es fundamental dominar las técnicas del proceso.
En términos de espesor, las placas medianas se refieren a placas de acero con un espesor de 10,0 a 25,0 mm, las placas con un espesor de 25,0 a 60,0 mm se denominan placas gruesas y las placas con un espesor superior a 60,0 mm se denominan placas extragruesas. .
Para cortar acero inoxidable grueso de alta calidad, es esencial que los fabricantes de productos de acero inoxidable tengan un conocimiento profundo del proceso de corte por láser.
Criterio para corte por láser de chapa gruesa
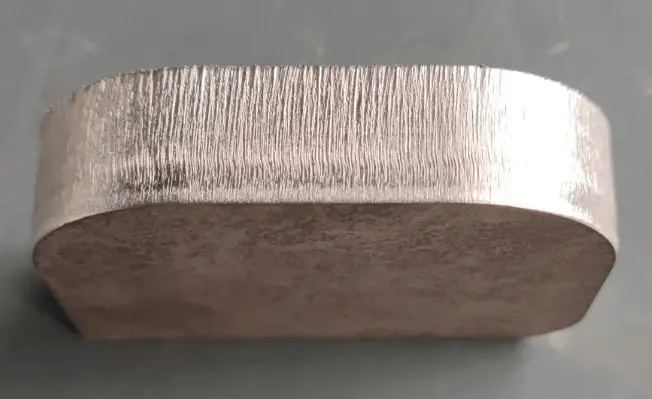
1. Rugosidad
El proceso de corte por láser da como resultado líneas verticales en la sección de corte. La rugosidad de la superficie de corte depende de la profundidad del grano. Un grano menos profundo da como resultado una sección de corte más suave, mientras que un grano más profundo produce una superficie de corte más gruesa. Además, una veta más superficial da como resultado un corte de mayor calidad.
2. Perpendicularidad
Para láminas gruesas, la perpendicularidad del filo es extremadamente importante. Si el rayo láser está demasiado lejos del foco, se volverá divergente, lo que puede dar como resultado anchos desiguales en la parte superior e inferior de la rendija.
Si el filo se desvía significativamente de una línea vertical, la pieza de trabajo no cumplirá con los estándares y puede ser difícil de usar. Cuanto más cerca esté el filo de una línea vertical, mayor será la calidad del corte.
3. Ancho de corte
El ancho del corte determina el diámetro interior del perfil. Durante el proceso de corte real, es necesario ajustar los parámetros y compensar el material que se corta para garantizar que la pieza cumpla con las especificaciones de tamaño deseadas.
4. grano
Al cortar placas gruesas a alta velocidad, el metal fundido se expulsa por la parte posterior del rayo láser en lugar de ser expulsado por la muesca debajo del rayo láser vertical. Esto da como resultado un patrón curvo en el filo.
Para resolver este problema, es necesario disminuir la velocidad de avance al final del proceso de corte, lo que puede eliminar efectivamente la formación de este patrón curvo.
5. Rebabas
La rebaba es un factor crucial para determinar la calidad del corte por láser. La eliminación de rebabas requiere un esfuerzo adicional, lo que resulta en un aumento de tiempo y costos de mano de obra. Como resultado, la presencia o ausencia de rebabas es el criterio principal para determinar si un corte por láser se considera de calidad aceptable.
6. Área afectada por el calor
El área afectada por el calor se refiere a la profundidad de la región donde la estructura interna ha sufrido cambios. Durante el corte por láser, el metal cerca de la muesca se calienta, lo que puede provocar cambios en la estructura del metal. Por ejemplo, algunos metales pueden volverse más duros.
7. Deformación
El calentamiento rápido durante el proceso de corte puede causar deformación, lo cual es particularmente crítico en el mecanizado de precisión. Para evitarlo, es necesario controlar la potencia del láser y utilizar pulsos láser cortos, lo que reduce el calentamiento de los componentes y evita la deformación.
Requisitos tecnológicos para el corte por láser de chapas gruesas de acero inoxidable.
1. Selección de boquilla
Diámetro de la boquilla
El diámetro de la boquilla determina la forma del flujo de gas, el tamaño del área de difusión de gas y el caudal de gas en la entalla, lo que influye en la estabilidad de la extracción y el corte de la pieza fundida. Un mayor flujo de aire hacia la muesca da como resultado velocidades más rápidas y una mayor capacidad para eliminar la pieza fundida, siempre que la pieza esté colocada correctamente dentro del flujo de aire.
Para acero inoxidable más grueso, se recomienda utilizar una boquilla más grande. Para aumentar la presión y garantizar un resultado de corte normal, se puede aumentar el ajuste de la válvula proporcional, lo que da como resultado un mayor flujo.
Especificaciones de la boquilla
La especificación de la boquilla se refiere principalmente a la apertura final. Por ejemplo, la boquilla de corte fabricada por Precitec tiene una abertura que varía de 1,5 mm a 5,0 mm. La selección de apertura se basa principalmente en el poder de corte. A mayor potencia, más calor se genera y mayor es la cantidad de gas necesaria.
Cuando se cortan tablas de menos de 3 mm, generalmente se utiliza una boquilla con una abertura de 2,0 mm. Para cortar tablas de entre 3 mm y 10 mm, se selecciona una boquilla de 3,0 mm. Cuando se cortan tablas de más de 10 mm de espesor, se requieren boquillas con aberturas de 3,5 mm o más.
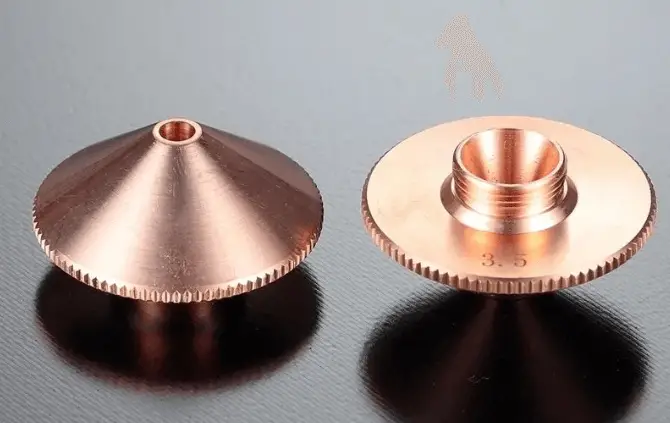
Boquilla monocapa con apertura △3,5
¿Boquilla de una sola capa o boquilla de doble capa?
Normalmente, las boquillas de doble capa se utilizan para el corte oxidativo (donde se utiliza oxígeno como gas auxiliar) y las boquillas de una sola capa para el corte por fusión (donde se utiliza nitrógeno como gas auxiliar). Sin embargo, algunos láseres tienen instrucciones específicas sobre el uso de boquillas de una o dos capas. En estos casos, es importante seguir las instrucciones proporcionadas por el láser.
dos . Selección de gas auxiliar y pureza del gas.
En el corte por láser de acero inoxidable se utiliza a menudo una variedad de gases auxiliares, incluidos oxígeno, nitrógeno y aire. Los diferentes gases tienen distintos efectos en el proceso de corte. El oxígeno da como resultado secciones negras, el aire produce secciones de color amarillo claro, mientras que el nitrógeno ayuda a prevenir la oxidación y mantener el color original del acero inoxidable. Como resultado, el nitrógeno es el gas auxiliar preferido para cortar acero inoxidable.
Pureza recomendada de oxígeno y nitrógeno:
Oxígeno | Nitrógeno | |
Beneficios | Alta velocidad de corte, capaz de cortar láminas gruesas | Evita la oxidación del filo, por lo que no es necesario volver a trabajar la pieza. |
Pureza recomendada | ≥99,999% | ≥99,995% |
Los datos de prueba del flujo de nitrógeno, el diámetro de la boquilla y la presión del gas se muestran en la siguiente figura.
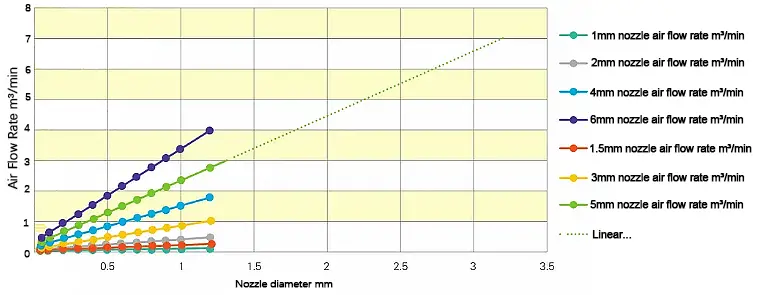
El eje vertical representa los valores de prueba del flujo de gas, mientras que el eje horizontal representa la configuración de ajuste. Se muestran diferentes cambios de presión de gas y diferentes colores representan las condiciones de prueba de diferentes diámetros de boquilla.
El gráfico muestra que el caudal está determinado por la presión del gas ajustada y el diámetro de la boquilla, con una correlación lineal positiva.
3 . Posición de enfoque
Para garantizar el efecto de corte y proteger la boquilla de daños, es necesario realizar una prueba coaxial antes de cortar. Esta prueba garantiza que la boquilla esté alineada con el haz de salida del láser.
Método de prueba de posición de enfoque
Para realizar la prueba coaxial, adhiera un trozo de cinta transparente al extremo de la salida de la boquilla. Ajuste la potencia de salida del láser para perforar y observe si hay un orificio central en el papel de la cinta y su posición. Ajuste el tornillo de ajuste en el mango de la cavidad del espejo hasta que el orificio perforado con láser en la cinta de papel se alinee con el centro de la boquilla.
El enfoque afecta el espesor, el material y la calidad que se puede cortar. Diferentes materiales y espesores requieren diferentes ajustes de enfoque. Antes de cortar, mida el enfoque cero real y utilícelo como base para probar y analizar los parámetros del proceso de corte.
En el corte de acero inoxidable, el desenfoque negativo es la dirección preferida para la selección del proceso.
Ubicación del enfoque | Material de corte y características de la sección. |
Distancia focal cero: el enfoque del láser está en la superficie de la pieza de corte |
Este método es adecuado para cortar acero al carbono fino con un espesor inferior a 1 mm. La atención se centra en la superficie de la pieza de trabajo, lo que da como resultado una superficie superior lisa y una superficie inferior rugosa. |
Distancia focal negativa : el enfoque del láser está debajo de la superficie de la parte de corte |
Este es el método de corte de acero inoxidable. El foco se coloca debajo de la superficie de la placa, lo que da como resultado una superficie lisa más amplia, una hendidura más ancha en comparación con una hendidura de longitud focal cero, un mayor flujo de gas durante el corte y un tiempo de perforación más largo que con una focal cero. longitud. |
Distancia focal positiva : el foco del láser está por encima de la superficie de la pieza de corte. |
Al cortar acero al carbono, se utiliza oxígeno como gas auxiliar. Esto da como resultado una superficie ennegrecida y una sección de corte desigual. |
4 . Influencia del ajuste de la frecuencia del láser y la relación de pulso en la calidad del corte
Influencia del cambio de frecuencia en el corte de láminas gruesas de acero inoxidable:
A medida que la frecuencia disminuye de 500 a 100 Hz, la calidad de la sección de corte mejora y las capas se vuelven más finas. Sin embargo, si la frecuencia se establece en 100 Hz, no será posible el recorte y se reflejará la luz azul. Para determinar el mejor rango de frecuencia, es necesario experimentar con cambios de frecuencia.
Para lograr resultados de corte óptimos, es importante garantizar una combinación perfecta entre el tiempo de pulso y la energía de un solo pulso.
Influencia del cambio del ciclo de trabajo por impulsos en el corte de láminas gruesas de acero inoxidable:
El valor crítico para el ciclo de trabajo del pulso es del 45%. Si el ciclo de trabajo se reduce aún más, aparecerá una marca socavada en la superficie inferior. Por otro lado, si el ciclo de trabajo aumenta al 60%, la sección cortada se vuelve rugosa, con capas ligeras y una superficie de corte amarilla.
El ciclo de trabajo del pulso representa la proporción de tiempo que se irradia el haz en cada pulso. La frecuencia es el número de veces que se produce la potencia máxima en un pulso, mientras que el ciclo de trabajo se refiere a la relación entre la potencia máxima y la potencia baja en un pulso.