1. Introducción al cabezal de corte
Actualmente, los cabezales de corte utilizados en el mercado de máquinas de corte por láser de fibra son principalmente las series LightCutter (Figura 1) y ProCutter (Figura 2) de PRECITEC, una empresa alemana.

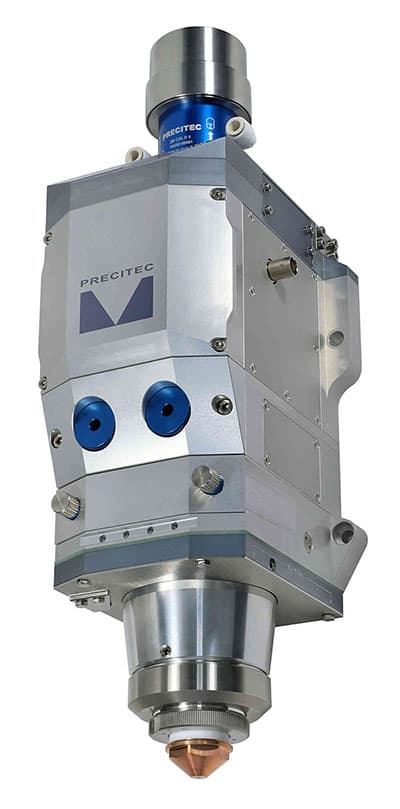
Estas dos series de cabezales de corte son adecuadas para potencias láser en los siguientes rangos: LightCutter≤2500W, ProCutter≤6000W.
2. Análisis del proceso de contaminación del cabezal de corte
Como se muestra en la Figura 3, los componentes ópticos dentro del cabezal de corte constan de 2 espejos colimadores, 3 espejos de enfoque y 4 espejos protectores. La contaminación de estas lentes afecta directamente al proceso de corte de la máquina herramienta.
Según las pruebas de procesos a largo plazo y el análisis exhaustivo del uso de los clientes, los principales factores que causan la contaminación del cabezal de corte son los siguientes:
①Método de instalación inadecuado del cabezal de fibra óptica.
②Efecto de sellado deficiente del cabezal de corte.
③Método inadecuado para reemplazar los espejos protectores.
④Tiempo de control de procesamiento irrazonable.
⑤Datos no científicos del proceso de corte.
⑥Uso de piezas vulnerables de baja calidad para el cabezal de corte (espejos protectores, anillos de sellado, etc.).
⑦Operación y uso inadecuado por parte del cliente final.
⑧Método incorrecto de mantenimiento y reparación del cabezal de corte.

- 1. Conector de fibra óptica
- 2. Módulo de colimación que contiene dos espejos de colimación.
- 3. Módulo de enfoque que contiene dos espejos de enfoque.
- 4. Caja protectora con ventana
- 5. Sensores
- 6. Contratuerca de cerámica
- 7. Anillo de cerámica
- 8. Boquilla
- 9. Conector de cable coaxial (conector de cable del transceptor)
Lectura relacionada: Puntos negros en lentes de soldadura y corte por láser: exploración de causas y soluciones
3. Investigación sobre la prevención de la contaminación con cabezales cortantes.
Aunque es un desafío lograr cabezales de corte absolutamente libres de contaminación, existen métodos que pueden emplearse para prolongar el tiempo entre los episodios de contaminación y reducir su gravedad. Esto puede ayudar a aumentar la vida útil del cabezal de corte y reducir los costos de mantenimiento y reparación.
Para abordar los factores enumerados anteriormente que contribuyen a reducir la contaminación de la cabeza, se pueden tomar las medidas respectivas de la siguiente manera:
3.1 Mejora del método de instalación del cabezal de fibra óptica
Se pueden realizar mejoras en el método de instalación asegurándose de que el cabezal de fibra óptica se inserte horizontalmente en el cabezal de corte y se bloquee de forma segura.
Es importante mantener un ambiente limpio durante el proceso de instalación, y si existe un número importante de partículas en suspensión (polvo) en los alrededores, se recomienda realizar esta tarea antes de las 6:00 am, es decir, antes de la hora de instalación. comienza la instalación. el turno de trabajo.
3.2 Mejora de la eficacia de sellado del cabezal de corte
Dado el nivel actual de fabricación mecánica, incluso con la tecnología alemana más avanzada, no es posible lograr un sellado absoluto para los cabezales de corte láser. Durante el uso posterior, es inevitable que entre polvo y contamine las lentes.
La causa principal de este problema es el aumento de la temperatura del cabezal de corte durante el proceso de corte (se puede lograr un corte normal cuando la temperatura del cabezal de corte es <55°C).
Esto conduce a un aumento de la presión interna, lo que provoca que algunos gases se liberen desde el cabezal de corte al entorno circundante.
Cuando el cabezal de corte deja de funcionar (después del turno de trabajo), la temperatura interna desciende a la temperatura ambiente, lo que hace que la presión interna sea inferior a la presión ambiental.
Los gases ambientales contaminados con polvo serán aspirados hacia el cabezal de corte hasta que las presiones interna y externa alcancen el equilibrio, contaminando así el cabezal de corte.
Para resolver este problema, el enfoque es mantener una presión positiva (mayor que la presión ambiental) dentro del cabezal de corte para aislar la entrada de gases polvorientos del medio ambiente.
Se pueden emplear los siguientes métodos para mejorar:
①Suministre continuamente gas limpio, seco y sin aceite al cabezal de corte. (Se recomienda nitrógeno, con una presión de 0,15 bar ≤ P < 0,3 bar).
②Instale un sistema de respiración para mantener siempre una presión positiva dentro del cabezal de corte.
3.3 Reemplazo adecuado de la lente protectora
Al reemplazar la lente protectora, debe hacerlo rápidamente. Mientras retira la caja de la ventana de la lente protectora (Figura 3), selle inmediatamente la ventana al cabezal de corte con cinta (sellando la abertura de instalación de la caja de la ventana de la lente protectora).
Además, asegúrese de que ningún objeto sucio entre en contacto con las lentes protectoras y que los operadores eviten hablar (para evitar salpicar saliva en las lentes protectoras).
3.4 Diseño racional de la sincronización del control de la máquina herramienta
La velocidad de propagación de la luz es más rápida que la velocidad de transmisión del gas. Al cortar o perforar, puede haber un retraso en el gas de corte, lo que hace que el láser comience a procesar antes de que el gas de corte alcance la presión o el caudal requerido, lo que provoca la contaminación de la lente protectora.
Se pueden implementar los siguientes métodos de mejora:
1. Modifique el tiempo de emisión del láser y liberación de gas (corte de gas) indicando la liberación de gas, esperando un período determinado (espera de gas), emitiendo láser y luego procesando.
2. Mantenga una cierta presión de aire (gas protector) durante todo el proceso de procesamiento.
La secuencia de procesamiento debe ser la siguiente: ordenar la liberación del gas de protección, preprocesar la placa (leer los datos de procesamiento y definir el origen), ordenar la liberación del gas de punción, ordenar la liberación del láser de punción, ordenar el corte liberación de gas, instruir la liberación del láser de corte (contorno de corte), completar el corte del contorno, posicionar rápidamente para el siguiente contorno, instruir la liberación del gas de punción, instruir la liberación del láser de punzonado, instruir la liberación del gas de corte, instruir la liberación del corte por láser (corte de contorno), completar el corte de contorno, repetir el ciclo, finalizar el proceso de corte, apagar el gas de protección y finalizar el programa.
3.5 Datos del proceso de corte racional
El uso de datos racionales del proceso de corte ayuda a prevenir la contaminación en el cabezal de corte debido a cortes anormales.
3.6 Uso de consumibles calificados
El uso de consumibles calificados, como lentes protectoras y anillos de sellado, contribuye al sellado del cabezal de corte.
3.7 Procedimientos operativos correctos
Siga las instrucciones proporcionadas por el proveedor del equipo para operar y utilizar correctamente la máquina herramienta.
3.8 Métodos de mantenimiento adecuados
Asegúrese de que el cabezal de afeitado esté limpio y seco y límpielo a diario.
4. Conclusión
Al implementar los métodos de prevención de la contaminación antes mencionados, se mejora significativamente la contaminación de las lentes ópticas dentro del cabezal de corte de fibra.
La aplicación práctica ha demostrado que con un mantenimiento regular y una cuidadosa atención a los detalles, se pueden evitar fallas frecuentes en las piezas de corte, extendiendo así la vida útil de las lentes y aumentando la eficiencia de producción del equipo.