El láser se crea mezclando helio de alta pureza, CO2 de alta pureza y nitrógeno en la unidad de mezcla de gas. El generador láser genera el láser y se agrega un gas de corte como N2 u O2 para procesar el objeto. La energía del láser está altamente concentrada y puede derretir y gasificar instantáneamente el material.
Este método resuelve eficazmente las dificultades del procesamiento de materiales duros, quebradizos y refractarios, ofreciendo alta velocidad, precisión y mínima deformación. Es ideal para procesar piezas de precisión y microcomponentes.
Varios factores pueden afectar la calidad del corte por láser, incluida la velocidad de corte, la posición de enfoque, la presión del gas auxiliar, la potencia de salida del láser y otros parámetros del proceso. Otros factores como la trayectoria de la luz externa, las características de la pieza (reflectividad y condición de la superficie del material), el soplete de corte, la boquilla y la placa también pueden afectar la calidad del corte.
Estos factores son particularmente importantes en el procesamiento de láminas de acero inoxidable, lo que genera problemas como grandes nódulos y rebabas en la parte posterior de la pieza, mala redondez cuando el diámetro del orificio es de 1 a 1,5 veces el espesor de la placa y líneas rectas que no son directamente a las esquinas. Estos problemas continúan desafiando a la industria de la chapa en el procesamiento láser.
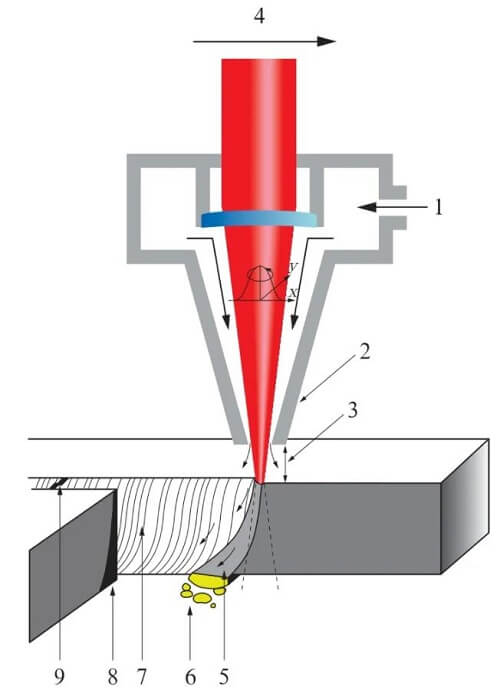
Figura 1 Principio de fusión del corte por láser
- Gas auxiliar
- Boquilla
- Altura de la boquilla
- Velocidad cortante
- Derretido
- Escoria
- Aspereza de corte
- Zona afectada por el calor
- Ancho de hendidura
Problema de acumulación de tumores
Hemos realizado repetidas pruebas y hemos descubierto que el soporte de corte equipado con la máquina de corte por láser no es adecuado para procesar chapa.
Las principales razones son:
(1) Si el ángulo R es grande, habrá un área de contacto grande entre la parte superior del soporte y la placa procesada, lo que generará una mayor probabilidad de reflexión por salpicadura si el rayo láser solo se corta en la parte superior del soporte. Por otro lado, si el ángulo R es pequeño, la probabilidad de reflexión por salpicadura será baja al procesar láminas delgadas.
(2) Si la distancia es pequeña y la pendiente es baja, el espacio disponible para que el rayo láser penetre más será limitado. Cuanto más pequeño es el espacio de reflexión, mayor es la fuerza de reflexión, lo que hace que el tumor cortante se adhiera más firmemente al lado opuesto de la placa.
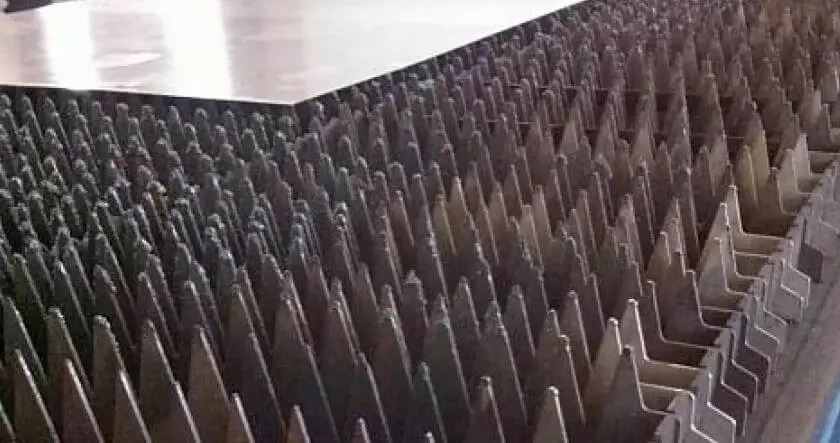
Fig. 2 Soporte mejorado
En base a las consideraciones anteriores, hemos mejorado el soporte de corte equipado con la máquina:
(1) Reduzca el ángulo R y aumente la distancia desde la parte superior del soporte hasta la superficie de la base, así como aumente la pendiente. Esto reduce significativamente las salpicaduras y los tumores en la parte posterior de la pieza de trabajo, lo que permite que el tumor se caiga fácilmente con un toque suave de una herramienta.
(2) Durante el proceso de corte, se descubrió que la aplicación de aceite a la superficie de la placa reduce la adhesión de las salpicaduras de corte. El aceite forma una película protectora en la superficie del plato, dificultando que la salpicadura se adhiera al plato.
Además, la película de aceite es más eficaz para guiar el rayo láser, especialmente al mecanizar placas con superficies extremadamente lisas, como el acero inoxidable tipo espejo. Esto se debe a que la película de aceite absorbe más fácilmente el rayo láser en comparación con una superficie de placa lisa, lo que hace que el rayo sea más fácil de penetrar y posicionar.
Por lo tanto, comenzamos a cubrir uniformemente la parte delantera y trasera del tablero con aceite para laminación de metales, que tiene un alto punto de inflamación. Esto ha llevado a una reducción significativa de las salpicaduras y la acumulación de tumores en la parte procesada, especialmente en la espalda, que es mucho mejor que antes.
(3) Después de repetidos ajustes a la posición de enfoque en los parámetros de corte, los técnicos descubrieron que la mejor posición de enfoque del láser para cortar la hoja es un poco menos de la mitad del espesor de la hoja.
Sin embargo, con la deformación de la placa o una presión excesiva del aire de corte, la calidad del corte se vuelve inestable cuando la placa delgada vibra ligeramente o se ve afectada localmente por la alta presión del gas.
Pero cuando el enfoque se ajusta a aproximadamente 2/3 del espesor de la placa (corrigiendo la desviación del enfoque causada por la deformación o vibración), se previene efectivamente la formación de rebabas finas bajo las mismas condiciones de presión de aire y placa.
Como resultado, la calidad de corte de la pieza mejoró enormemente.
Problema de redondez de agujeros pequeños
Cuando se utiliza una máquina de corte por láser, puede resultar complicado producir agujeros de alta calidad de aproximadamente 1 a 1,5 veces el grosor del tablero, especialmente para agujeros redondos.
El proceso de corte por láser implica perforación, inserción y corte, lo que requiere cambiar parámetros intermedios. Esto produce un retraso durante la transición, lo que provoca que los orificios redondos del producto terminado se distorsionen.
Para superar este problema, optimizamos el tiempo de perforación e inserción para alinearnos mejor con el proceso de corte. Esto elimina el cambio notable en los parámetros y da como resultado un resultado de mayor calidad.
Problema de rectitud de esquinas
En el procesamiento láser, varios parámetros importantes (como el factor de aceleración, la aceleración, el factor de desaceleración, la desaceleración y el tiempo de residencia en las esquinas) desempeñan un papel crucial en el procesamiento de piezas de láminas delgadas, que están fuera del rango de ajuste convencional.
Durante el proceso de mecanizado de piezas de chapa fina con formas complejas, a menudo se producen esquinas. El rayo láser debe disminuir su velocidad en cada esquina y luego acelerarse nuevamente. Estos parámetros determinan el tiempo de pausa del rayo láser en cada punto.
(1) Si el valor de aceleración es demasiado alto y el valor de desaceleración es demasiado bajo, es posible que el rayo láser no penetre bien el tablero en las esquinas, lo que resulta en una baja permeabilidad y una mayor tasa de desechos.
(2) Si el valor de aceleración es demasiado bajo y el valor de desaceleración es demasiado alto, el rayo láser penetrará el tablero en las esquinas, pero el valor de aceleración bajo hace que el rayo láser permanezca en el punto de conmutación de aceleración y desacelere durante un largo tiempo. tiempo, lo que hace que la placa se derrita y se vaporice continuamente bajo la influencia del rayo láser continuo, lo que genera una línea no recta en las esquinas. (Aquí no se consideran otros factores convencionales que afectan la calidad del corte, como la potencia del láser, la presión del gas y la sujeción de la pieza de trabajo).
(3) Al procesar piezas de láminas delgadas, se recomienda reducir la potencia de corte tanto como sea posible sin comprometer la calidad del corte, de modo que no haya diferencias de color obvias ni quemaduras en la superficie de la pieza de trabajo.
(4) Se debe minimizar la presión del gas de corte, lo que puede reducir en gran medida los microtemblores locales de la placa bajo una fuerte presión de aire.
Según el análisis anterior, ¿qué valores se deben establecer para una aceleración y desaceleración adecuadas? ¿Existe una relación proporcional entre ambos que deba seguirse?
Para determinar los valores ideales, los técnicos ajustan continuamente la aceleración y desaceleración, marcan cada pieza cortada y registran los parámetros de ajuste. Mediante comparaciones repetidas de muestras y un examen cuidadoso de los cambios de parámetros, se descubre que al cortar acero inoxidable en el rango de 0,5 a 1,5 mm, el valor de aceleración apropiado está entre 0,7 y 1,4 g, y el valor de desaceleración está entre 0,3 y 0,3 a 1,4. gramo. 0,6 g. Existe una regla general que dice que el valor de la aceleración es aproximadamente el doble del valor de la desaceleración.
Esta regla también se aplica a láminas laminadas en frío de espesor similar, pero para láminas de aluminio de espesor similar los valores deben ajustarse en consecuencia.
Conclusión
Al abordar con éxito los factores que afectan la calidad del corte, la calidad de los productos de láminas de acero inoxidable que procesamos ha mejorado significativamente en términos de reducción de tumores de corte y mejora de la sutileza del corte.
Como trabajadores técnicos modernos, es importante comprometerse con el aprendizaje, tener el coraje de explorar nuevas soluciones y adherirse al principio de "excelencia en la producción". Este enfoque garantiza la producción de productos de alta calidad y el éxito en una intensa competencia económica.