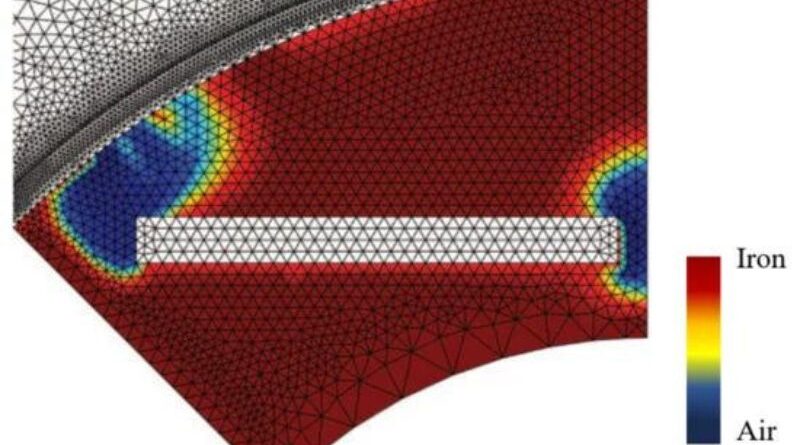
magnetic properties
The magnetic properties of magnetic materials depend on the direction of the material's crystals and determine the dimensions or instrumentation of machines for a given power, the required excitation, operating efficiency, etc.
-
Be less reluctant or extremely absorbent or have a high relative permeability value µ R .
-
High permeation induction (to reduce the volume and weight of iron parts).
-
High electrical resistance, therefore lower eddy voltage and therefore lower eddy current loss.
-
Conical hysteresis loop or lower coercivity, therefore lower hysteresis loss and high operating efficiency.
-
A high temperature.
-
It must have a great energy product value. It is expressed in joules/m 3 .
Permanent magnets
Permanent magnets have revolutionized the efficiency of electrical machines. Their ability to maintain their magnetic properties without an external field makes them the first choice for countless applications, from motors and generators to magnetic bearings. We delve deeper into the science behind permanent magnets, including rare earth magnets, and explore recent advances in magnet manufacturing that have significantly improved their performance.
Magnetic Materials: The Building Blocks of Electrical Machines
At the heart of every electrical machine is a magnetic core responsible for controlling the flow of electrical current and producing mechanical work. We investigate the properties of various magnetic materials such as iron, steel and magnetic alloys and understand their unique properties ideal for specific applications. From ferromagnetic to paramagnetic materials, each type has different magnetic properties that engineers carefully consider when designing electrical machines.
Conductive materials for electrical machines
Factors to Consider When Designing Electrical Machines
When designing electrical machines, several factors must be carefully considered to create an efficient, reliable and cost-effective device that meets specific application requirements. These factors cover several aspects, including performance, materials, environmental impact and safety. The most important factors to consider during the design process include:
Soft magnetic material
Silicon steel
Special league
-
Nickel-based alloy with high nickel content (iron + molybdenum + copper or chromium) used in magnetic amplifiers, power transformers, etc.
-
Nickel-based alloy with low nickel content (iron + silicon + chromium or manganese) used in induction coils, coils, transformers, etc.
-
Terminator (iron + nickel + cobalt).
-
Mumetal (copper + iron)
-
Pemendur (iron + cobalt + vanadium) is used for oscilloscopes, microphones, etc.
Amorphous alloys
Superconductors: a magnetic wonder
Superconductors have the extraordinary ability to conduct electricity without resistance at low temperatures. We explore how these materials have the potential to revolutionize electrical machines, achieving unprecedented efficiency and power density. Although the practical application of superconductors is still in its infancy, we discuss the current state of research and development and provide insights into their prospects in electrical machines.
Material selection for optimal performance
Selecting the right magnetic material for a specific application is a complex process that requires a balance between several factors, including cost, efficiency and environmental impact. We address the considerations engineers must make when selecting magnetic materials, taking into account the intended application, operating conditions and sustainability requirements.
Switching in DC machines
Switching is fundamental to the operation of DC machines, including DC motors and generators. The key mechanism allows the conversion of electrical energy into mechanical energy in motors, driving movement, mechanical work and, conversely, the conversion of mechanical energy into electrical energy in generators. Commutation ensures that current in the armature winding flows unidirectionally, which is essential for maintaining the desired direction of rotation in motors and producing a stable output voltage in generators.
The commutation process involves the interaction between the commutator and the brushes, with the contact pads maintaining electrical contact with the commutator segments while the rotor or armature rotates. This continuous contact allows current to be transferred from one armature coil to another, ensuring constant rotor rotation in motors or stable voltage output in generators. Proper switching is critical to the smooth and efficient operation of DC machines, and challenges such as sparking, arcing and brush wear must be carefully managed to maintain optimal performance and reliability. Advances in switching technology, such as electronic commutation in brushless DC motors, have further improved efficiency and reduced maintenance requirements, making DC machines a versatile choice for a variety of industrial, automotive and consumer applications.