((wysiwyg_imageupload:1976:))This project report is contributed by S. Sridevi of ARULMIGU MEENAKSHI AMMAN COLLEGE OF ENGINEERING, VADAMAVANDAL.
1. INDUSTRIAL PROFILE
1.1 COMPREHENSIVE COACH FACTORY
The integral bus factory is a production unit of the Indian Railways set up under the First Five Year Plan. ICF is initiated with the transfer of bus construction technologies from m/s SWISS CARS AND ELEVATORS, Manufacturing Corporation, Switzerland.
The Prime Minister of India inaugurated the Shri production unit. Pandit Jawaharlal Nehru on October 2, 1955.
The CIF has evolved into more than 300 projects consisting of
· sleeper trainers
· Air-conditioned bus
· Self-propelled buses
· Mainline and Diesel Electric Multiple Units (EMU, DMU, MEMU)
· Metro bus
· Diesel Electric Tower Cars (DETC)
· Accident Relief Medical Vans (ARMV)
· Inspection Cars (RA)
· Fuel Test Cars
· Track Recording Cars
· The last buses are for the Deccan Odyssey (an Indian Railways luxury train)
· coaches for MRVC (world class coaches)
· ICF's range of business encompasses design, development and manufacturing of various types of coaches for Indian railways and for export.
1.2 SALIENT CHARACTERISTICS OF CIF COACHES:
· All steel welded body
· Anti-telescopic structure
· Good riding quality
· Lightweight
· High speed
· Adopting corrosion prevention method
· Safe and economical design
· Improved amenities
· Fine proof measure
1.2 CIF DEPARTMENTS:
· Mechanic
· Electric
· Engineering
· Guys
· Security
· Accounts
· Stores
· Doctor
CHAPTER 2- INTRODUCTION
The main objective of our project is to guarantee safety on the road and avoid “separation” to a greater extent. Most, if not all railways, implement safety systems, mainly to prevent trains from colliding with each other.
At the implementation level, considering the first, our safety system is based on the principle that trains cannot collide if they are not authorized to occupy the same section of track at the same time. Therefore, railway lines are divided into blocks where a detection system detects the current condition of a train and outputs signals at the block entrance accordingly.
Considering the latter, although separation is a momentary phenomenon; It mainly occurs in ductile materials, where ductile materials take a long time to lose their tensile strength and finally break.
Implementation of the topic must also be possible under working conditions. To achieve this, a detailed study of certain traction systems in real time and the various parties involved is necessary. Therefore, before we get into our topic, let us give a brief insight into the control elements involved in our topic for efficient practical implementation.
2.1 STUDY OF ESSENTIAL REAL-TIME COMPONENTS
2.1.1 Traction Motors :-
The project consists of two circuit diagrams, among them one contains a circuit to control the motor motor, i.e.… Traction motor. Therefore, the classifications of various traction drives and their types are given below.
Only three types of traction motors are manufactured at ICF.
They are
· DC to AC EMU Series Traction Motor
· DC series traction motor for DEMU
· AC/DC series traction motor for world-class buses. (MRVC Units)
Among the above three types, only the first two are commonly used in Indian railways.
CLASSIFICATION OF DC TO AC EMU SERIES TRACTION MOTOR:
· 535V, 340A, 167KW (continuous rating).
· 535V, 350A, 187KW (1 hour rating).
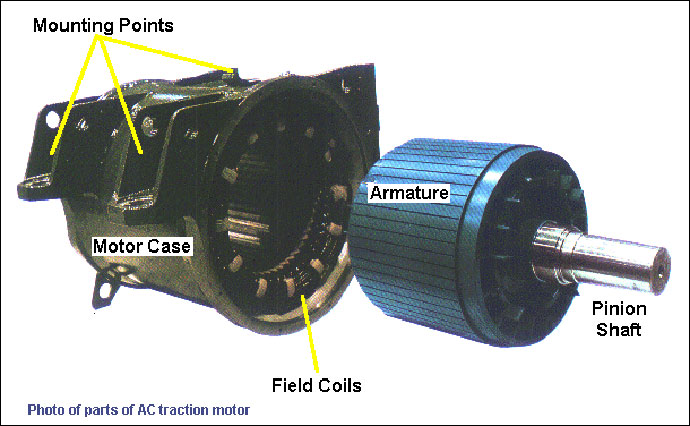
Fig 2.1.1AC traction motor
CLASSIFICATION OF DC SERIES TRACTION MOTOR FOR DEMU:
· 1160 rpm, 557V, 415A, 208KW (continuous rating)
· 1115 rpm, 557 V, 457 A, 208 KW (1 hour rating)
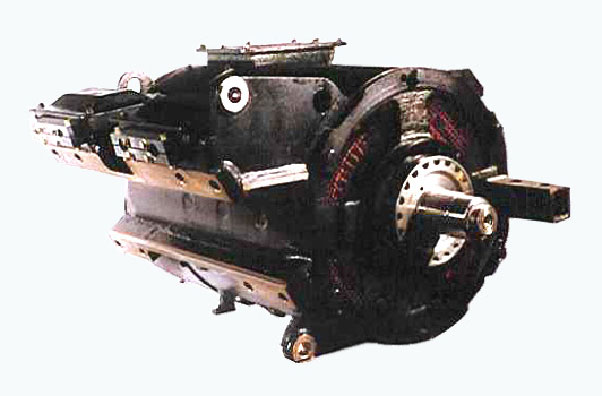
Fig 2.1.2 DC series traction motor for DEMU
AC/DC MULTIPLE UNIT RATINGS FOR WCC
Three-phase squirrel cage asynchronous induction motor controlled by VVVF, 6 poles, 250KW, 162A, 1029V, 1259rpm, 0.81pf, 64Hz.
2.1.2 Description of the Need for Control:
The project deals with the complication of braking and controlling DC motor in performing operations like forward movement, reverse movement, speed control and stopping during integrity check and separation. To perform these operations efficiently, a brief description about the controller section is given below.
2.1.3 Master Controller :
Here the master-slave control technique is used between DC MEUs where bi-directional communication is possible but the command passes only from the master to the slave control motor. Commands for drive and direction selection are issued from the engine controllers. It consists of the following components
1. Direction selection switch
· Forward (F)
· Neutral(N)/Deceleration
· Reverse(R)
2. Traction/brake controller
It is used to distribute the torque request from the inverter traction/brake controller to the train.
3. Dead man's switch
It is built into the traction/brake controller. To activate the dead man via the lever, the driver must rotate it approximately 5 degrees when the mode selector is in the forward or reverse position, then only one driver can activate the train.
2.1 .4 Control Drive/Brake Reference:
The train is stopped two or three times during the parts grinding process. Therefore, adequate knowledge about the braking system, its types and use of multiple braking methods in traction drives is required for real-time implementation. They are provided in detail as below. To understand train drive/brake control it is necessary to know that there are five different operations performed in five different working conditions or modes.
· Emergency braking
· Normal braking
· Automatic braking
· Coastal
· Driving
EMERGENCY BRAKING:
The brake pipe is unloaded and fully pneumatic is applied. The operating mode is reached when the driver places the traction/brake controller in the 'EB' position, releases the dead man, places the mode selector in the neutral position, or places the brake controller in the emergency or brake position.
NORMAL BRAKING:
EP/ED brakes are used to brake the train. The braking of the train is controlled by the BECU (Brake Electronic Control Unit). There are two types of brake cylinder pressure sensor one is provided for BECU and TCU. The brake pipe remains charged and the automatic brake is not applied. To achieve this mode, the traction/brake controller must be in the braking position.
AUTOMATIC BRAKING:
Automatic braking is used when deceleration using EP and ED brakes is not sufficient. They are used if one or more vehicles in the train are not capable of braking using the EP and ED brakes.
COAST:
Here no drive or braking force is applied. To achieve this mode, the traction/brake controller must be in the coast position.
2.1.5 Brake Equipment:
These equipment are mainly used for braking operations . For all four braking methods mentioned above, two valves, three brakes and a compressor are used. They are listed below.
1. Driver brake valve
2. Emergency brake valve
3. Electro-pneumatic brake
4. Pneumatic brake
5. Parking brake
6. Compressor
415 VAC, 50 Hz, 6.7 KW, 12.7 A
Working pressure: 10bar
Weight: 180
2.1.6 Driver's Cabin Equipment:
To control the traction motor or the prototype, a real replication of the driver's cabin is required. The second circuit diagram mentioned in the project is the actual miniature of the driver's cabin.
· Master Controller
· Direction selection switch
· Brake controller, dead man switch
· LED indication panel
· Ecab for control and auxiliary MCBs
· Train ON-OFF driver control switch.
2.1.7 NEED TO STUDY COUPLER:
To take the necessary actions during 'Separation' or 'Decoupling', detailed information on the type, nature of the material used and the construction of the individual couplings and couplers required. Detailed information about couplings used in Indian Railways is given below.
2.1.7 COUPLER
A coupling (or coupler) is a mechanism for connecting rolling stock on a train. The coupler design is standard and is almost as important as the railway gauge, since flexibility and convenience are maximized if all rolling stock is coupled to it.
So that two railway vehicles can be connected together in a train they are fitted with couplers. Given that there are a large number of railway vehicles, which may need to be coupled at one time or another in their lives, it seems sensible to ensure that the couplings are compatible and in a standard position at each end of each vehicle.
The integral bus factory manufactures only four types of couplers for coaches and locomotives in India. They are
1) IRS Couplers
2) CBC – Central Buffer Coupler
3) ABC-Auto Buffer Coupler
4) Schaku Coupler
Among the four, only three types are currently used. Automatic buffer couplers are not manufactured nowadays due to their various difficulties. Let's take a detailed look at other types.
BAR COUPLER:
The simplest type of coupler is a link and pin. Each vehicle has a bar fixed to the center of the head that has a loop with a central hole attached to it. Each coupler has a bell-shaped mouth around the end of the bar to help guide the bar with the hole into place. The loops are aligned and a pin is placed in them.
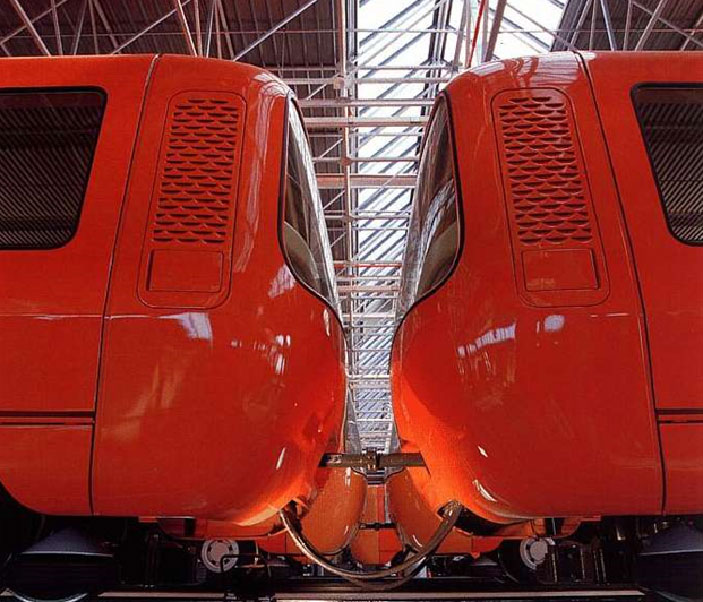
Fig.2.1.7(a) Bar coupler
The common type of coupler is the bar coupler. This is also known as a semi-permanent coupler. Cannot be disconnected unless the train is in a workshop and access under the train is available. It is typically used in EMUs, which are maintained in fixed formations of two, three or four cars. The bar couplers are located inside the unit, while the outer ends of the unit have some type of easily disconnected coupler. Bar couplers are simple, consisting of just a bar with a hole at the inner ends through which the car body is connected by a screw. Others consist of two halves, which are screwed together.
IRS OR 3-LINK COUPLING:
This type of coupling is exactly what it says – a set of three links, which hang from hooks on each vehicle. One development of this is the “Instanter” coupler, which has a forged intermediate link in a triangular shape to allow adjustment of the distance between vehicles. This allows the side dampers used with the coupler to be adjacent to each other and provide some degree of slack damping.
The coupler required a person to get down into the lane between the two vehicles and lift the coupling chain over the hook of the other vehicle. Sometimes a “coupling post” was used to quickly uncouple freight cars.
This is a development of the same coupling where the intermediate link is replaced by a screw. The screw is used to tighten the coupling between the two vehicles to provide damping by compressing the side shock absorbers. The following photos show typical threaded couplings.
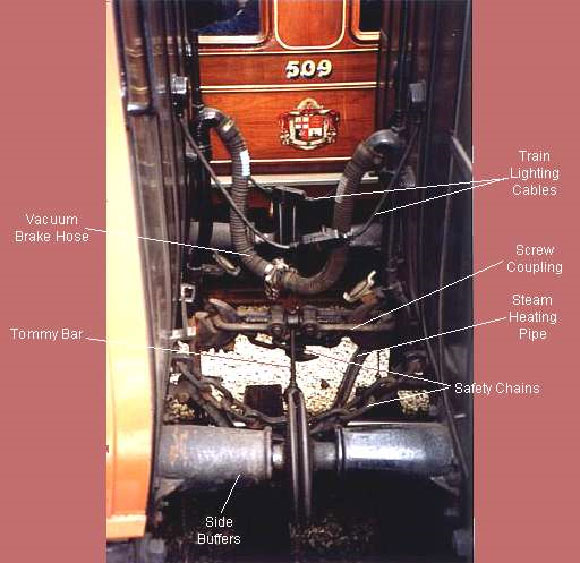
The photo above shows a coupled screw coupler also showing typical passenger vehicle coupling accessories In addition to the mechanical couplings required to connect the vehicles; trains needed connections for brakes, lighting and heating. In this photo the arrangements for coupling two passenger cars in a steam-hauled train are shown. This specific type of bus is equipped with safety chains, which are installed in case the main coupling breaks. All work connecting the two vehicles is carried out manually. They involve hard and sometimes dangerous work.
CBC – CENTRAL BUFFER COUPLER:
It is also known as a buckeye or hinged coupler or alliance coupler.
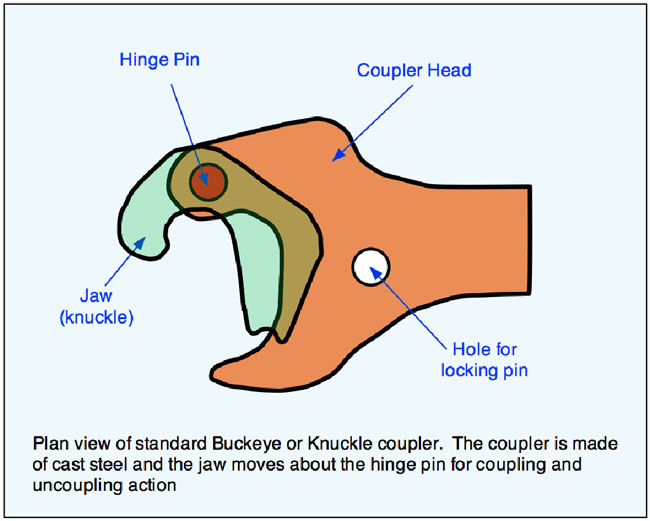
By far the most common coupler seen around the world is known as the “Knuckle”, “Buckeye” or “Janney” coupler, diagram at left. This is an automatic mechanical coupler design originating from the USA and commonly used in other countries for freight and passenger vehicles. The term “Buckeye” comes from the nickname of the US state of Ohio “the Buckeye State”, which originally marketed the coupler. The link and pin coupler required the crew to stand between the cars to couple and uncouple, and as a result there were many injuries and even deaths.
The coupler is made of cast steel and consists of four main parts. The head itself, the jaw or joint, the hinge pin, around which the joint rotates during the coupling or uncoupling process, and a locking pin. The locking pin is lifted to release the joint. This is done by lifting a steel block inside the coupler head which releases the joint and allows it to rotate. The simplified diagram below shows the steps when two couplers are being coupled.
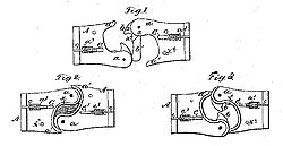
To couple two vehicles, the joints must be open. When the two vehicles are joined, the joints of the two couplers close and are locked from behind by a vertical pin that sets a steel block in place behind a raised casting in the joint. To decouple, one of the pins must be pulled upwards to release the block that locks the joint. This is done by operating a lever or chain on the side of the vehicle. 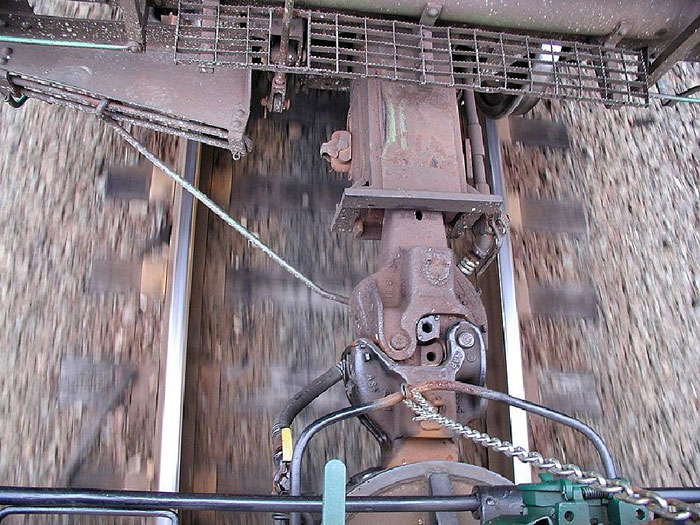
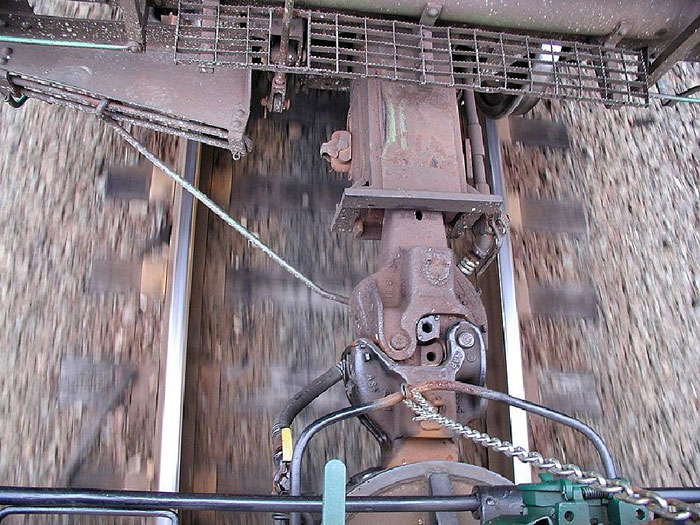
Fig 2.1.7 (d) Standard Type E CBC couplers performing their role in freight trains
SCHAKU COUPLER OR SCHARFENBERG AUTOMATIC COUPLER:
More and more railways are using Scharfenberg automatic couplers. A fully automatic coupler connects vehicles mechanically, electrically and pneumatically, typically by pushing the two vehicles together and then pressing a button or pedal in the cab to complete the operation. Decoupling is done by another button or pedal to disconnect the electrical contact and the pneumatic connection and disengage the coupler mechanically.
Fully automatic couplers are complex and need a lot of care and maintenance attention. They need to be used frequently to keep them in good working order. There are several different designs in use.
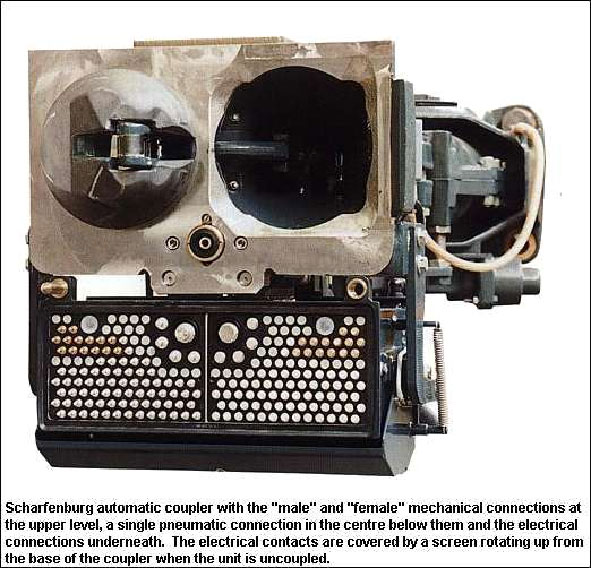
Figure 2.1.7(e) Automatic
COUPLING MECHANISM
It consists of two mechanical projections. One is conical, the other is funnel. The conical and funnel shape of the profile of the front face of the coupler guarantees a wide collection range both horizontally and vertically and allows automatic coupling in curves, even with vertical mismatch and very low speed.
Minimum force is only required for successful coupling. The coupler faces and locking system form a rigid connection both vertically and horizontally. The parallelogram arrangement of the coupler locks provides uniform distribution of the tensile load. This coupler lock design ensures minimal wear and maximum coupler longevity. The rigid, backlash-free connection allows for jerk-free acceleration and braking and offers optimum driving comfort. It also prevents cars from overtaking in the event of an accident.
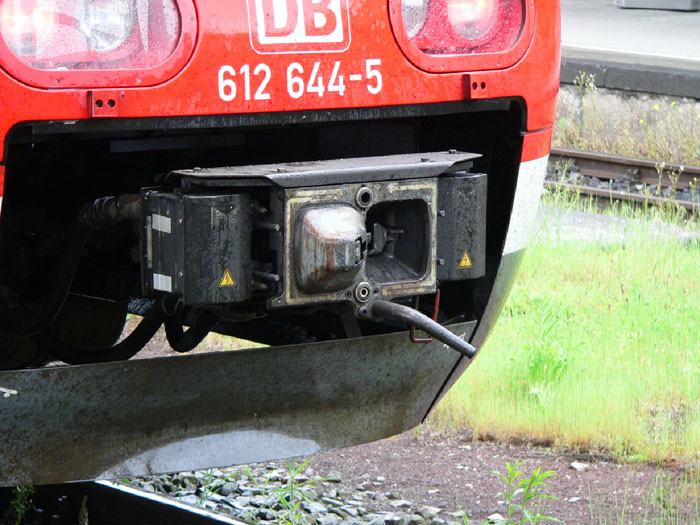
Fig 2.1.7(f) Schaku in the train carriage
2.2 EXISTING SYSTEMS:
The project was primarily conceived as a solution to overcome the defaults in existing methods for verifying integrity. The current tracking-based detection method has many difficulties. The working principle and difficulties were discussed in detail.
2.2.1 Track-based detection method:
Detecting a train on a segment is done by measuring the current flowing from one rail through the train's axles to the other rail, meaning the train effectively short-circuits the rails, or by counting the number of axles entering and leaving the segment. To prevent a train from entering a busy segment, the system provides means to control the movement of the train. It is capable of stopping or slowing down a train when it is about to pass a red signal.
Control information is transmitted to the train by antennas on the tracks or by signals sent across the tracks. The current situation has many disadvantages. The most obvious is that there is no standardization across India. Trains crossing borders must be equipped with all applicable systems.
2.2.2 Patterns in trajectory-based detection:
Train safety is based on infrastructure and, due to the amount of equipment on the track, maintenance is labor intensive and expensive. Under normal conditions, only one train is allowed on a segment because the length of a segment is fixed and varies between one and several kilometers and the distance between trains is often much greater than necessary, resulting in poor track usage.
Tracks could be used much more efficiently if the distance between trains was flexible and based on the length, weight and speed of the trains.
Sometimes a car is accidentally uncoupled from the train. The train must be checked to see if all cars are still present. In the old system, this was done on the track system by counting axles. For passenger trains this is not very difficult to accomplish, as there are many mechanical and electrical connections between the cars.
Unlike passenger trains, freight train cars are connected only mechanically with chains and hooks and compressed air lines for the brakes.
2.2.3 Solution:
The only solution to eliminate the standards mentioned above is the use of train-based wireless sensor networks instead of track-based networks. sensor systems.
2.3 REQUIREMENTS:
An integrity security system must meet a series of requirements for the system to function effectively.
2.3.1 Functional Requirements
· Coupling and decoupling with an integrity system should not take longer or involve more actions than without an integrity system.
· The integrity system should require as little human intervention as possible, reducing the risk of human error.
· The driver must receive a clear status of the train's integrity.
2.3.2 Hardware Requirements:
Wireless is preferable to wired. Connecting and disconnecting wires is time-consuming and error-prone in the railway environment.
· The integrity system should not require radical changes in the design of cargo transport. It should be a simple add-on installed once on existing cars.
· There should be no operational degradation. The system may not wear out over time.
The hardware must be suitable for the harsh railway environment. It must be robust and shockproof.
2.3.3 List of hardware components used:-
The list of components used for the project template is provided below.
. LV-Masonry®-EZ1-High Performance Ultrasonic Sensor .
. A pair of RF transmitter and receiver.
. RLP434A SAW-based RF receiver (433.92 MHz).
. TLP434A RF Transmitter (433.92 MHz)
. HT12E encoder and HT12D decoder where the encoder is used along with the transmitter and the decoder is used along with the receiver.
. Two AT89S52 microcontrollers.
. Two PMDC engines.
· One of the motors is for controlling the prototype, which is the motor for the model train and the other motor is for controlling the hook.
For effective health detection, we are using USS in WSN for its notable features.
2.3.4 ULTRASONIC SENSOR CHARACTERISTICS
- The ultrasonic sensor we are using is very sensitive, even a small distance if 1mm deviation can be easily identified. Signal transmission is also very fast.
- Because of this, it is easy to take corrective action now at risk.
- Whenever the effective distance changes, vibrations first develop. If these vibrations exceed a certain range, the sensor will detect this too.
- Then the engine speed is adjusted to reduce the stress on the coupling.
- Therefore, it is possible to detect and rectify it before the moment of decoupling.
2.4 CASE STUDIES:
2.4.1 Murulla rail accident
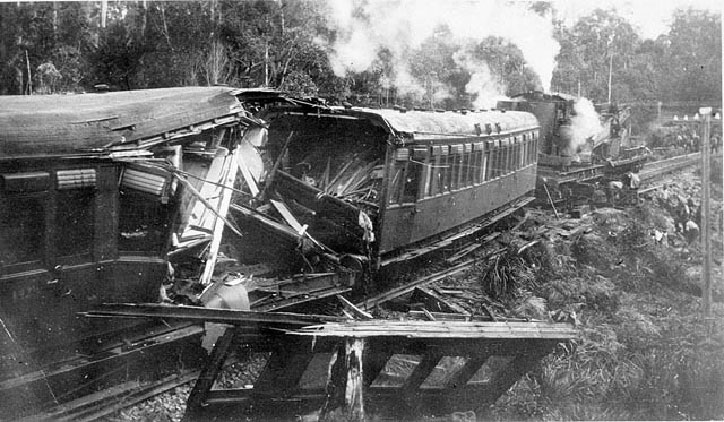
Fig 2.4.1 Image of the damaged car
The Murulla rail accident involved the collision of the Sydney-bound Northwest Mail Train with runaway freight wagons near Murrurundi, New South Wales, in the Upper Hunter Valley, on 13 September 1999. Almost 26 people lost their lives.
A goods train was split up and attempts by the train crew to reunite the parties resulted in 12 vehicles fleeing down a steep incline and colliding with the oncoming mail train.
This was the worst accident on the New South Wales rail network until the Granville rail disaster in 2005.
The signal box at Murulla controlled a circular line for trains to pass on a single railway track; there were no other connections at the site. Electric Train Staff operated between Wingen and Murulla and Electric Tablet operated between Murulla and Blandford.
Train No. 62, southbound goods train, comprised a standard goods locomotive carrying 34 carriages and a brake van was to pass through Murulla on the main line. Another goods train, No. 95, operating in the opposite direction, had entered the circular line and was waiting for No. 62 to pass. No. 62 was 951 feet (290 m) long and had a load of 746 tons (758 t). All vehicles were equipped with Westinghouse air brakes.
The train slowed down at the Murulla signal box for the exchange of single line tokens and when train personnel for the next section were received, the driver of No. 62 accelerated. The collision resulted in the train splitting, with the twelve rear vehicles becoming separated from the main train. This was later attributed to the failure of a traction hook. The driver noticed the train split and both parts of the train were stopped safely.
It was found that both parts of the train were within the clearance points of the circular line, therefore, train no. 95 was allowed to leave.
The detached portion of No. 62 consisted of 12 vehicles and was 331 feet long and weighed 264 tons. Hand brakes were applied to these vehicles. It appears that the train personnel in possession of the locomotive crew were returned to the instrument in the signal box at this time, and all vehicles were within the limits of the initial signals.
After a series of attempts to fit a rear rope, the brake van was deflected backwards, violating the clearance point for the circular line. The two opposing vehicles in the separation were finally coupled together with a single steel cable connection, but the air brake hoses could not be connected. The signalman then requested that the train be brought forward so that it would be clear of the clearance point to allow the southbound No. 8 mail train to pass the loop.
The guard in No. 62 released the handbrake at the rear, leaving it unlocked and the driver advanced towards the engine. As he started the train, the rear rope broke and the rear began rolling down the ramp toward Bland Ford, colliding with the oncoming mail train just beyond the distant signal. The collision resulted in the deaths of 26 people.
2.5 BLOCK DIAGRAM-I (GENERAL BLOCK DIAGRAM) 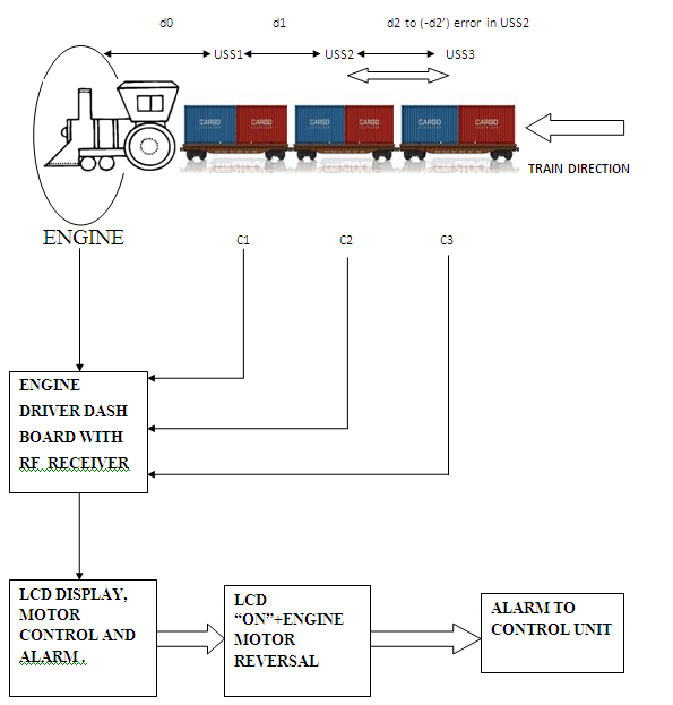
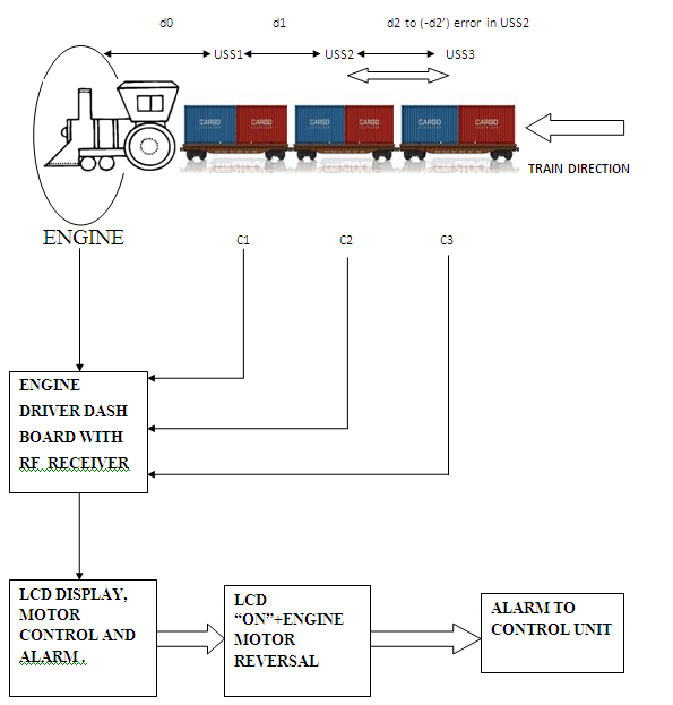
Fig 2.5 General Block Diagram
2.5.1 BLOCK DIAGRAM – I
EXPLANATION:
Ultrasonic sensors are placed in every car. Each USS is connected to a transmitter and the pairing receiver is placed on the engine driver's dashboard.
Each USS is placed at the end of the car at a predefined distance. All transmitters are connected to a single receiver on the engine.
The receiver is connected to a microcontroller circuit with LCD alarm and motor control screen.
(a)LCD display to indicate the location of the car.
(b) The alarm is also present for indication purposes.
(c) Motor control mainly serves to perform four operations sequentially during separation.
TO STOP
TO REVERSE
TO STOP
NEXT/START AGAIN.
Whenever the effective distance between the sensor changes, the USS detects and sends an RF signal to the motor driver through the microcontroller circuit in the car.
Then the microcontroller on the engine driver's panel sends an “alert” signal to the driver to control the engine speed.
All types of couplers used in trains are ductile in nature. Therefore, prevention before separation or decoupling is possible by adjusting the train engine speed.
Therefore, separation is avoided up to this point using the methods. Instead of all these measures, separation happens, the USS itself detects the couplings and sends signals to activate the second circuit at the end of the car which takes necessary measures to eliminate the problems due to separation.
2.6 BLOCK DIAGRAM –II
2.6 ENGINE DASH BAORD CIRCUIT:
Fig 2.6.1 Motor driver panel block diagram
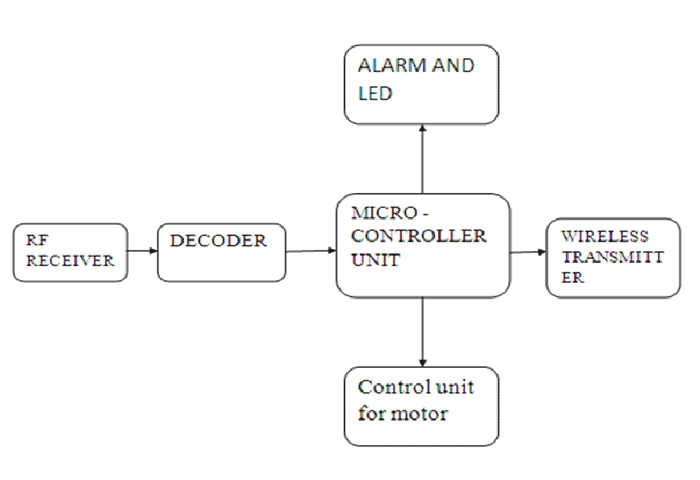
2.6.1 BLOCK DIAGRAM II-EXPLONATION
Whenever the cars are uncoupled, the USS sensors and RF transmitter transmit an uncoupled signal to the RF receiver that is on the engine driver's panel. The RF receiver decodes the signal and transmits it to the microcontroller. The microcontroller provides control signal to the motor unit to reverse the motor, also to alarm and LED display.
The current status of a particular train is reported to the control station in a remote area through wireless transmitters.
CIRCUIT DIAGRAM I
MICROCONTROLLER CIRCUIT AT THE END OF THE CAR
2.7 CIRCUIT AT THE END OF THE CAR: Check Circuit D
2.7.1 Circuit diagram I consists of the following sections:
1. Ultrasonic sensor with serial port transmitter and receiver
two. Microcontroller
3. Power supply
4. Encoder and transmitter section
5. Hook Motor Control Relay
The ultrasonic sensor detects the distance between the two cars. Whenever it detects decoupling through the transmitter and receiver from the serial port to the microcontroller, the microcontroller has a coded program to perform two operations simultaneously. They are
· The transmitter sends the signal at the rate of 433.49 MHz to the receiver on the engine side.
· The signal is given to the hook motor to raise it.
· Another signal to stop and reverse the motor motor through the encoder is also given.
· After transmitting the signal to the main locomotive to stop the train, the microcontroller has a pre-written program, which sends a command to the relay to “ON” the hook control motor to lift it.
· The hook control motor has a pull rope wrapped around it at one end and the other end tied to the hook.
· After lifting the hook through the control motor, the encoder-transmitter assembly sends a signal to move the train backwards.
· Meanwhile, the ultrasonic sensor detects the distance between two cars.
· Whenever the train reaches a specified distance, the sensor detects it and sends signals to the microcontroller.
· There it sends a signal through the transmitter to stop the train.
· After the “STOP” operation, a command from the microcontroller is sent to turn off the motor for re-engagement of the drop hook operation.
· Then a signal from the transmitter will be sent to the main locomotive for forward movement of the train.
· If the hook is not attached correctly, all the above operations will be repeated again until the re-attachment process is perfect.
CIRCUIT DIAGRAM II
MICROCONTROLLER CIRCUIT ON DRIVER’S PANEL
2.8 CIRCUIT IN THE DRIVER'S CABIN: The circuit was explained in Tab 2 of the Circuit Diagram.
2.8.1 EXPLANATION OF CIRCUIT DIAGRAM -II
Circuit diagram II consists of the following sections
1. Receiver, decoder section
two. Microcontroller
3. LCD screen
4. Engine Control Section
5. Power supply
Receiver, Decoder Section:
The receiver signals at a frequency of 433.92 MHz and rejects signals at other frequencies. The received frequency is reduced to 38 KHz in the receiver section itself. Then the signal passes to the microcontroller.
· The microcontroller has a pre-written program to stop the engine during decoupling detection in cars.
· Simultaneously, the number of cars and the distance between two cars are displayed in the LCD section.
· After receiving the signal from the transmitter by lifting the hook at the end of the car, the direction of the motor is reversed by operating relays S1, S2 to the no-change condition.
· The engine is reversed until it reaches a defined position (specified distance) between the cars.
· The reversing movement is stopped when receiving the signal from the ultrasonic sensor to stop it.
· Then the motor starts to advance through relays S3, S4 upon receiving the signal confirming the coupling of the hook at the ends of the cars.
3.CONCLUSION:
3.1 RESOURCES AND FUTURE PLANS
. Existing solutions for checking train health are almost with exceptions based on track systems, while our solution relies exclusively on train-based WSN.
. The use of ultrasonic sensors made our model cheap, fast and simple.
. For long transport trains instead of microcontroller, PLC7200 pin or any other embedded IC can be used.
. Using the same sensor networks, derailment detection and control can be done.
Project source code
Circuit diagrams
Train integrity based on WSN13 | ![]() |
Train integrity based on WSN14 | ![]() |