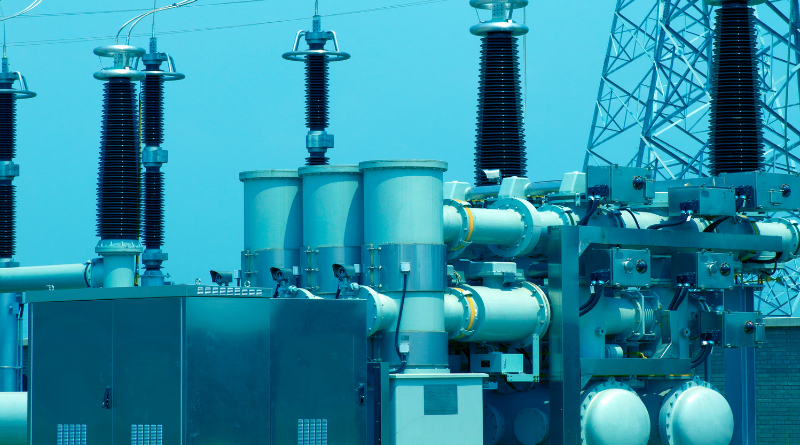
Transformer cooling is crucial to the reliable operation of power transformers. Transformers are used to increase or decrease voltage in electrical power systems and can generate significant amounts of heat during their operation. Excessive heat can lead to deterioration of insulating materials, reduced transformer efficiency, and even catastrophic failure. To avoid these problems, various cooling methods are used to dissipate heat and keep the transformer temperature within safe limits.
Because there are no rotating parts to create a draft, transformers are more difficult to cool than rotating machines. For small powers up to, for example, 20 kW, the external surface is sufficient to dissipate the heat generated by radiation losses. In other words, simple tanks large enough to accommodate the transformer are not sufficient for the heat generated inside due to the various losses. However, as the size of the transformer increases, a normal single tank may not be able to dissipate its losses. In this case, cooling tubes are provided that increase the heat dissipation area.
Cooling Methods for Transformers
- Dry type : Transformers that use air as coolant are called dry type transformers.
- Oil-immersed type : Transformers that use oil as a coolant are called oil-filled transformers.
The letter symbols used to denote these methods depend on the following.
- Medium cooling is used.
- Type of circulation used.
Average
Traffic
Signs indicate transformer cooling methods
- The medium comes into contact with the windings.
- The circulation of the refrigerant in contact with the windings
Dry type transformers
Natural Air – ON
Air explosion – AB
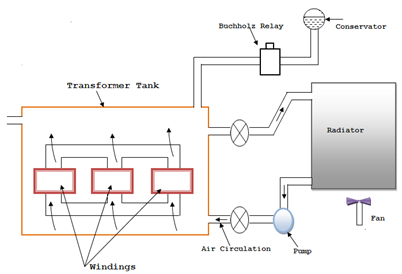
Oil Transformers
Oil-cooled transformer – ON
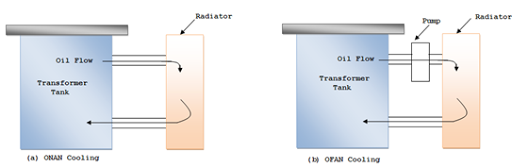
Oil and Air Cooled Transformer – ONAF
Transformer with forced water and oil cooling – ONWF
Oil-cooled transformers – OF
Oil-cooled transformer with natural air cooling – OFAN
Oil-cooled and air-cooled transformer – OFAF
OFWF oil and water cooled transformer
Air cooling
Air-cooled transformers use natural convection or forced air circulation to dissipate heat. They are generally smaller and suitable for lower power applications. Air cooling is economical and requires less maintenance than oil cooling.
Liquid-cooled refrigeration
In liquid-filled cooling processes, a dielectric liquid other than oil is used as a coolant, for example synthetic esters or silicone liquids. These fluids have better thermal properties than traditional transformer oils and are more environmentally friendly. Liquid-filled transformers are often used in sensitive or environmentally regulated areas.
Oil and air cooling
Forced cooling methods are used for high power transformers. Pumps or fans are used to allow oil or air to circulate in a controlled manner and thus improve cooling performance. Forced cooling is essential for transformers operating at higher loads to prevent overheating.
Conclusion
In summary, adequate transformer cooling is essential to maintaining the reliability and longevity of transformers in electrical power systems. Depending on the size, power and operating conditions of the transformer, different cooling methods are chosen to prevent overheating and ensure safe and efficient operation.
Common questions
Why is cooling necessary for transformers?
Cooling is necessary to maintain a safe operating temperature for transformers. Transformers generate heat due to electrical losses in their windings and core. Failure to dissipate heat effectively can result in insulation degradation and transformer failure.
How to choose the cooling method for a transformer?
The cooling method of a transformer is generally selected based on factors such as power rating, operating conditions, and environmental considerations. Larger transformers often use oil cooling, while smaller transformers may use air or liquid cooling.
What are the advantages of liquid cooling?
Liquid cooling provides better heat dissipation and fire protection than traditional oil cooling. It is also more environmentally friendly and therefore suitable for sensitive areas.