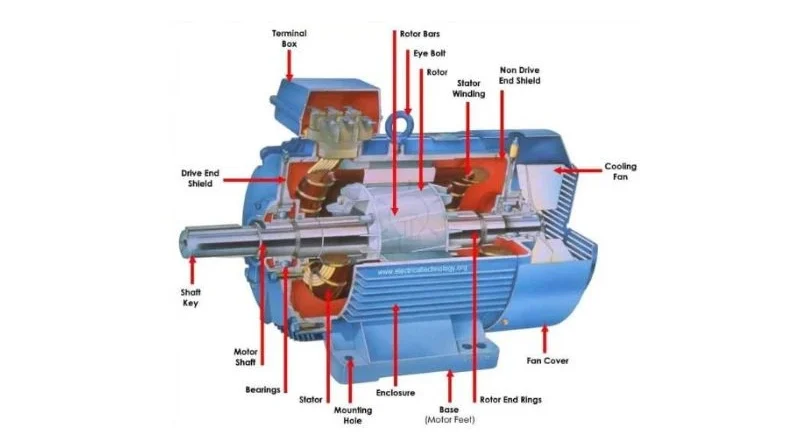
When it comes to industrial applications and powering heavy machinery, the three-phase induction motor is the cornerstone of modern technology. This remarkable machine is a workhorse in many industries, from manufacturing to agriculture. In this article, we will look at the design of a three-phase induction motor and discover the intricate details that make it a marvel of electrical engineering.
Understanding Three-Phase Induction Motors
Before we delve into the design details, let's first take a look at the basics of a three-phase induction motor.
What is a three phase induction motor?
A three-phase induction motor, often called an induction motor, is a type of electric motor that converts electrical energy into mechanical energy. It works on the principle of electromagnetic induction, in which a rotating magnetic field is generated in the motor to induce the rotation of a rotor. These engines are widely used due to their simplicity, reliability and efficiency.
Key Features of Three-Phase Induction Motors
Three-phase induction motors have several important characteristics:
- Stator: The stator is the stationary part of the motor and consists of laminated iron cores and windings. It creates a rotating magnetic field using three-phase alternating current (AC).
- Rotor: The rotor is the rotating part of the engine. It consists of a squirrel cage rotor or a wound rotor. The rotor interacts with the rotating magnetic field, resulting in mechanical rotation.
- Camp: Induction motors are equipped with bearings that support the rotor and reduce friction during rotation.
Now that we have a basic understanding, let's look at the complex structure of a three-phase induction motor.
Structure of a three-phase induction motor
A three-phase induction motor is made up of several main components that work seamlessly together to produce mechanical movement. Let's analyze its construction step by step.
stator
It contains a steel frame surrounding a hollow cylindrical core made of thin silicon steel fins to reduce hysteresis and eddy current losses. There are evenly spaced air slots on the inner edge of the louvers. The insulation is connected to create a symmetrical three-phase star or delta circuit. The three-phase stator coil is wound on a certain number of poles depending on the required speed. If the number of rods is greater, the engine speed will be lower and vice versa. As soon as the stator winding is fed with a three-phase power supply, a rotating magnetic field with constant strength is created. This rotating magnetic field creates currents in the rotor due to electromagnetic induction.
The stator is the heart of the induction motor. It consists of the following elements:
- Stator Core: The stator core is typically made of laminated steel sheets and provides a low reluctance path for the magnetic flux generated by the stator windings.
- Stator windings: These windings are carefully arranged in grooves in the stator core. When three-phase alternating current is used, it creates a rotating magnetic field that surrounds the rotor.
rotor
Squirrel rotor type
It contains an I-shaped laminated cylindrical core with parallel grooves at the outer edge. An aluminum or copper rod is fixed at each point. All of these rods are connected at one end with metal rings called end rings. This arrangement guarantees a permanently shorted winding that lasts forever. No power is supplied to the rotor but current is induced in the stator due to the action of the transformer.
Therefore, the induction motor using squirrel cage rotor is called squirrel cage induction motor. Its simple and robust construction allows it to operate in the most adverse conditions. On the other hand, it has the disadvantage of low starting torque. This is due to the permanently short-circuited rotor bars. To obtain high starting torque, it is not possible to add a resistor externally.
Wound rotor type
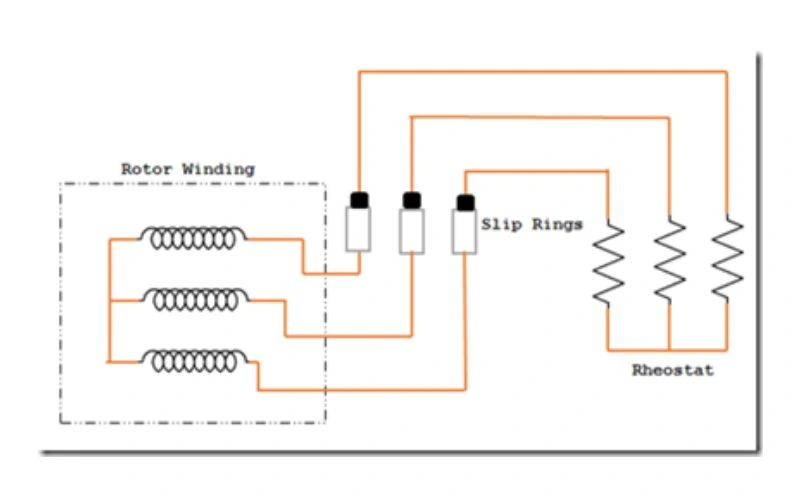
During the starting phase, external resistors are activated to achieve a high starting torque. When the motor reaches its rated speed, the wound rotor works in a similar way to the squirrel cage rotor, short-circuiting all three brushes.
camping
Bearings support the weight of the rotor and allow it to rotate smoothly. The choice of bearings depends on factors such as motor size and application.
Housing and refrigeration
Engine components are housed in a robust housing to protect them from environmental influences and ensure structural integrity. Proper cooling, often achieved through fans or other cooling mechanisms, is essential to maintaining engine performance and preventing overheating.
Terminal box
A terminal box is provided to connect the motor to the power supply and control devices. It contains terminals for the motor cables and may contain protective functions such as overload relays and thermal sensors.
Why is it important to understand construction?
Understanding the construction of a three-phase induction motor is crucial for several reasons:
- Maintenance: Knowledge of engine design facilitates proper maintenance and troubleshooting and helps you diagnose and correct problems efficiently.
- Optimization: By understanding the components of the motor, one can optimize its performance for specific applications, such as adjusting rotor resistance for better control.
- Safety: Knowledge of engine design is critical to the safety of personnel working with or near the engine.
Conclusion
In short, designing a three-phase induction motor is a fascinating mix of engineering principles and practical design. Understanding their components and how they work is essential for anyone who works with these engines, whether for maintenance, optimization or safety reasons. Being the cornerstone of modern industry, the three-phase induction motor continues to drive progress and innovation across multiple sectors.
Common questions
Can a three phase motor run on a single phase power supply?
No, a three-phase induction motor is designed to operate from a three-phase power supply. Attempting to operate it with a single-phase power supply will result in reduced performance and possible damage to the motor.
What advantages does a squirrel cage rotor offer over a wound rotor?
A squirrel cage rotor is simpler to design and maintain, making it more reliable and less expensive for most applications. It has fewer moving parts, less maintenance and high starting torque.
How can I determine the motor size and power for a specific application?
Motor size and power depend on application requirements. You must consider factors such as load type, operating conditions, and torque requirements. For accurate selection, it is recommended to consult a professional or refer to motor sizing guidelines.