Wire EDM is an electrothermal production process that uses electrical discharges to remove material from a workpiece. It is an improvement on the traditional EDM method, compatible with almost all conductive materials and can create complex designs and shapes.
For this reason, it is used by many parts manufacturers in different sectors, as it is highly recommended in many CNC workshops. This article discusses wire EDM, compatible materials, and their application in many industries.
What is wire EDM?
Wire EDM is a non-contact subtractive manufacturing process that uses a thin wire electrically charged with a dielectric fluid to cut a metal part into various shapes.
The process creates small chips and precise cutting lines by melting or vaporizing the material rather than cutting it. This facilitates the machining of parts that are not suitable for conventional machining techniques. However, the parts must be electrically conductive.
How does wire EDM work?
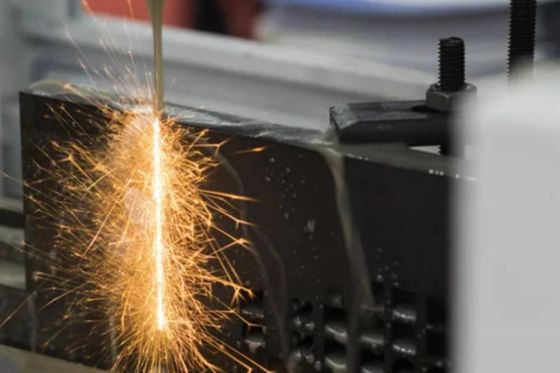
The wire EDM process has a simple mechanism.
When machining a part using this method, the part is immersed in a dielectric fluid, clamped with a machine vise, and a wire is passed through it to create sparks when an electrical current passes through it.
In other words, the wire carries one side of the charge and the workpiece, which must be made of conductive material, carries the other side of the charge. As the two approach, a hot electrical charge leaps through the opening and melts small pieces of metal.
Electric spark is the cutting tool to cut the material into the desired shape. Additionally, wire EDM uses deionized water to control the process and remove small particles that are removed.
Components of a wire EDM machine
The machine consists of several parts that work together to give the material the desired shape. The machine components are listed below.

1. CNC Tools
CNC tools control the entire wire EDM process. Control of the entire process includes control over the wire routing order and the ability to automatically control the cutting process.
Note: The complexity of the CNC tool determines the error rate and processing time.
2. Power supply
The power supply is the component that supplies pulses (from 100V to 300V) to the wire electrode and the workpiece. Additionally, it controls the frequency and intensity of electrical charges that flow through the wire electrode and interact with the workpiece.
To provide the quality and type of load required in wire EDM, it is necessary to use a sophisticated power supply.
3. Wire
The wire serves as an electrode to generate the electrical discharge. The shape and thickness of the part directly affect the wire diameter. Typically you can use wires with diameters of 0.05 to 0.25 mm. The main types of yarn used are
-Brass wires
Brass is the most commonly used wire material for electrical discharge machining due to its excellent conductivity. It is an alloy of copper and zinc. The higher the zinc content, the faster the wire cuts. However, there must be a balance because when the zinc content is above 40%, the corrosion rate of brass wire decreases.
-Galvanized wires
As the name suggests, this is achieved by applying a layer of pure zinc or zinc oxide to the surface of the wire. Manufacturers use galvanized wire because it improves processing speed.
-Diffusion annealed wires
The diffusion annealing process allows the production of wires with a higher zinc content (more than 40% zinc). The wires are coated with layers of pure zinc. These yarns are ideal for mass production and can handle many materials.
-How to choose the right yarn
- To choose the right EDM wire material for your project, consider the following
- tensile strength
- Breaking strength
- conductivity
- Evaporation temperature
- toughness
4. Dielectric medium
The wire EDM process must be carried out in a tank filled with dielectric fluid. This liquid prevents small particles from the workpiece from sticking to the wire electrode. The most commonly used medium is deionized water, which cools the process and gives the piece a good surface finish.
5. Electrodes
The machine's electrodes are the wire (cathode) and the workpiece (anode). The servo motor controls the wire electrode and ensures that it never comes into contact with the workpiece during wire EDM.
Materials that a wire EDM machine can cut
Wire EDM machines can create complex shapes and patterns on a workpiece. Additionally, they can work on most materials that can conduct electricity, even the hardest and most delicate ones.
Common shapes and materials you can cut with the machine include:
aluminum
Aluminum has excellent thermal and electrical conductivity. However, aluminum is naturally soft and can be difficult to cut using this process as it can result in rubber deposits after processing.
titanium
Wire EDM is ideal for titanium because the process resists the stickiness of this alloy and grinds long chips. However, they require deionized water as a dielectric medium to keep heat generation under control during processing.
steel
Steel is a very strong metal. Therefore, many manufacturers prefer to use a wire EDM machine instead of a CNC machine. However, the material generates a lot of heat, so the necessary care must be taken.
Brass
Brass is easy to cut with a machine because it has high tensile strength. However, as it is a soft metal, the cutting speed must be low.
graphite
Graphite can be difficult to cut with traditional cutting tools. However, EDM wire is suitable because the wire is sharp and prevents particles from being torn off.
Differences between wire EDM and conventional EDM
Wire EDM is an improvement over conventional EDM. The functionality is similar. However, there are significant differences. Below are some differences between the two editing methods.
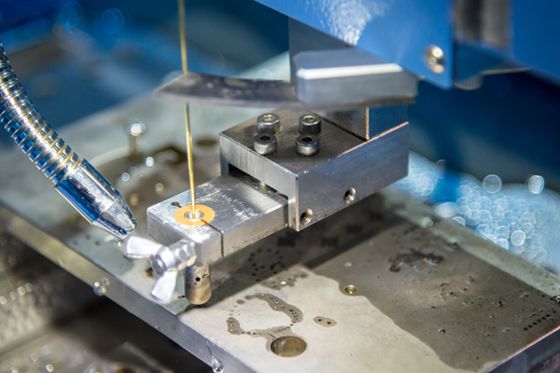
electrode
As mentioned above, the electrode used in wire EDM is a thin heated wire. In contrast, conventional EDM uses highly conductive metals, such as graphite or copper electrodes, to generate electrical charges. Electrodes come in different shapes and sizes, which affects their smoothness. For example, a round electrode creates the smoothest surface. Then follow a square, a triangle and a rhombus. When the electrode is inserted into the workpiece, it forms a shape and leaves a “negative” impression of its shape.
Processing speed
The electrodes of traditional EDM machines must have different shapes. Therefore, manufacturers need to create and shape them before the machining process, which takes time. In contrast, the wire EDM machine is ready to use as soon as the wire is in position. This makes them suitable for applications that need to be completed quickly.
precision
Wire EDM uses wire as an electrode. This means that the accuracy is greater than with conventional erosion. For example, the wire electrode allows cuts approximately 0.004 inches thick. Their precision makes them better suited for machining parts with complex shapes and designs, unlike conventional EDM, which is better for more rigid cuts.
Forms
Wire EDM is versatile and can cut ferrous and non-ferrous metals, which is why it is used in many industries. Furthermore, size and shape are not restrictions on use, as both long and extremely small parts can be processed. However, traditional wire EDM can process harder and thicker materials because the thickness of the wire electrode in a wire EDM machine affects its use.
Advantages and disadvantages of wire EDM
Advantages of Wire EDM
- Allows precise and accurate cuts, eliminating the need for additional processing and finishing of the part.
- The process is suited to creating complex designs and shapes that would be difficult to produce using traditional CNC machining.
- It is suitable for machining small parts and cutting highly detailed objects that would be too delicate for other machining options.
- Wire EDM is ideal for brittle materials that cannot withstand the stress of machining.
- In just one processing step, the machine cuts the material without burrs or distortions.
- The editing process cuts continuously and without interruptions. Even if the thread breaks during cutting, the process will continue immediately.
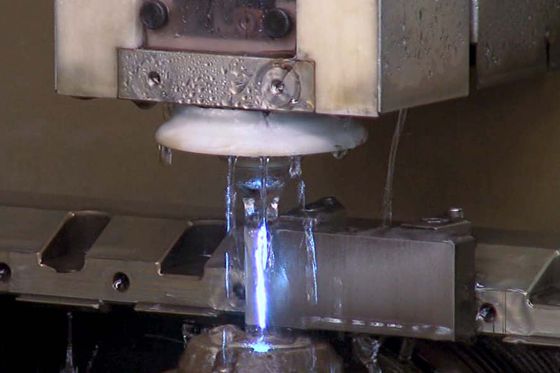
Disadvantages of wire EDM
- It is only compatible with materials that conduct electricity.
- On the cutting surface of some materials, such as aluminum, an oxide layer can form. This may require additional post-processing, increasing costs.
- The initial investment and maintenance costs are high.
Wire EDM Applications
Many industries use wire EDM machines from prototyping to full production. Some industries are listed below.
Auto Industry
Parts in the automotive industry have complex shapes and sizes and are often hard. Therefore, the industry prefers to use wire EDM machines because the process does not rely on mechanical forces and the wire electrode does not need to be stronger than the workpiece. The process is used to create holes and cavities to customize automotive parts such as bumpers, dashboards, car doors and more.
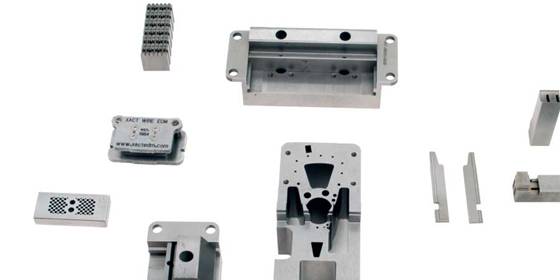
Medical industry
Wire EDM machines produce complex parts with high precision for use in all medical fields, including optometry and dentistry. Additionally, metals that work well with wire EDM machines are often used to manufacture medical devices.
Because the diameter of the wire determines the size of the cut, the wire EDM machine adds small features to parts such as dental implants and syringe components without compromising their structural integrity.
aerospace industry
Wire EDM produces parts with tight tolerances and is the preferred machining method for aerospace parts manufacturers. In addition to waterjet cutting, this process is mainly used for parts that cannot withstand the high temperatures and stresses of conventional cutting tools.
Parts in the aerospace industry must have excellent surface finish and be precise and precise. Manufacturers have used the wire EDM process for years to produce engines, turbine blades, chassis parts and more.
Concluding
Wire EDM is a versatile and precise machining process that can be used to create complex shapes and geometries. It is commonly used in the aerospace and medical industries where parts must meet tight tolerances. Wire EDM can also be used to create prototypes or individual parts. We hope that with this article you now have a better understanding of wire EDM.
Upload your CAD file today and receive an instant quote. We will be happy to work with you to find the right solution.
Common questions
What other types of EDM are there?
In addition to wire EDM, there is also drilling and sinker EDM. The difference is in the electrode used. The electrodes in hole EDM are tubular and create smaller, deeper holes. Die sink EDM, on the other hand, uses an electrically conductive metal to form a “positive” of the desired shape.
What is the difference between wire EDM and laser cutting?
Laser cutting uses a high-powered thermal beam to cut materials, while wire EDM uses electrical erosion of a wire.
Why is deionized water used in wire EDM?
Due to its low carbon content, deionized water is used as a dielectric medium in wire EDM. It serves as a coolant to regulate the dielectric temperature.