All semi-automatic carbon dioxide welding machines are equipped with voltage and current adjustment knobs. However, the voltage adjustment of tap type carbon dioxide welding machines is a toggle switch.
In case of an integrated welding machine (where the wire feeder is installed inside the host), the current adjustment knob is installed on the host panel.
In the case of a split type welding machine (where the wire feeder is independent and connected to the host via cables), the current adjustment knob is installed on the wire feeder.
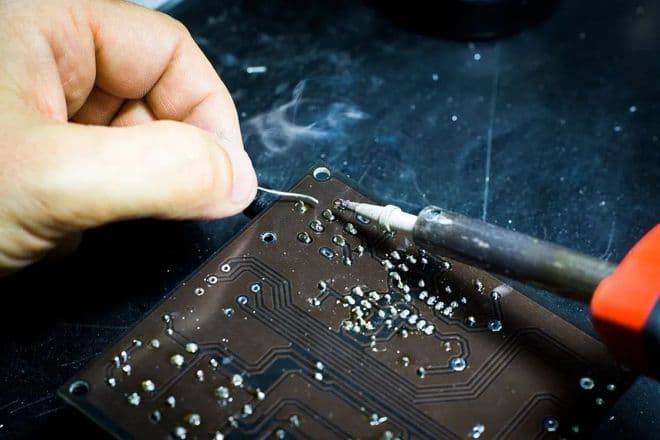
There are two methods to adjust the voltage of carbon dioxide welding machines:
- For thyristor rectifiers and inverter welding machines, a potentiometer is used.
- For tap type welding machines, voltage adjustment is done using the transfer switch.
The first requirement to ensure stability during the CO2 welding process is that the welding wire feeding speed must be equal to the melting speed.
The energy required to melt the welding wire is supplied by the welding machine. The higher the power output of the welding machine, the faster the welding wire melts.
In the case of a thyristor rectifier welding machine, the output power is adjusted by controlling the conduction angle of the thyristor. For an inverter welding machine, the output power is adjusted by controlling the pulse width. For a tap welder, the output voltage is adjusted.
According to conventional wisdom, power is the product of voltage and current. Therefore, adjusting the output power of the welding machine is equivalent to adjusting the welding current.
The welding current in carbon dioxide welding is adjusted by controlling the wire feed speed. This can be explained from two perspectives:
- The current is generated in a closed circuit (circuit).
- Current is a function of time.
In an open circuit, no matter how high the voltage, the current is always zero. In this case, the voltage at the terminals of the circuit is the electromotive force (EMF) of the power supply, which can be measured using a voltmeter at points A and B. This is known as the no-load voltage of the welding machine. .
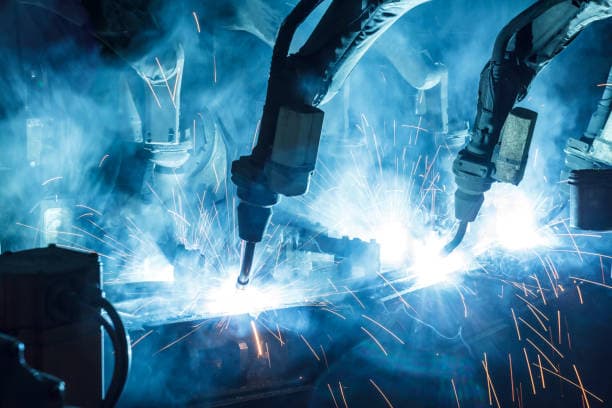
If a loop cannot be formed in the circuit, there will be no current flow and no voltage generated at both ends of the resistance R. Resistance R represents the sum of the internal resistance of the power supply and the voltage drop loss of the power cable. transmission in the welding arc source system. The internal resistance of the power supply is caused by the leakage reactance of the transformer, the adjustment of the conduction angle of the rectifier components, and the pulse width of the switching device.
However, if two points A and B are short-circuited or a resistance RH is indirectly connected at these points, current will be generated in the circuit. RH refers to the voltage drop generated when the welding current short-circuits the workpiece through the arc and droplet, also known as load resistance.
From the analysis above, it is evident that the lower the values of R and RH, the greater the current in the circuit and vice versa. The electromotive force E of the power supply has the opposite effect.
As mentioned previously, R is the inherent resistance of the welding circuit. For tap welders, the primary and secondary systems of the main transformer are made into a closely coupled structure to obtain a small leakage reactance to meet the requirements of the flat characteristics of carbon dioxide welding. In this type of welding machine, R can be considered unchanged, but the no-load voltage E of the power supply can be changed by changing the tap through the commutator.
In welding machines controlled by thyristors and inverter welding machines with IGBT as a switch, the transformer does not have an adjustable tap and E in the circuit can be considered constant. R in the circuit can be adjusted by changing the conduction angle of the thyristor and the IGBT activation judgment ratio.
Although the effects of R and E on the current in the circuit are easy to understand and pay attention to, the role of RH often does not receive enough attention. This is the second problem we want to talk about – current is a diploma that has time as a reference.
The output power of the welding machine can be achieved not only by adjusting the power supply voltage, but also depends on the load condition.
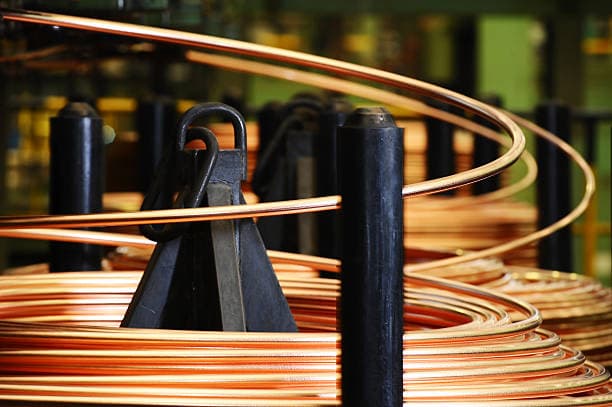
When welding with carbon dioxide, the welding wire is deposited on the workpiece (weld) in two ways:
- Short circuit transition
- Fine fall transition.
The short-circuit transition frequency is generally around 100 times/second, and the fine-drop transition frequency is higher.
The welding wire serves as the electrode (referred to as point A), while the workpiece is the other electrode (point B).
When the arc is lit, the welding arc is part of the RH, and the transfer of droplets from the welding wire is another part of the RH.
For short-circuit transition, the wire feed speed influences the frequency of the short-circuit transition. The faster the wire feed speed, the higher the short circuit transition frequency, which increases the opportunities to provide a path for this circuit in a unit of time. As a result, the equivalent resistance RH becomes smaller and the current also increases.
Furthermore, carbon dioxide welding uses a thin welding wire with a high current density, combined with a flat and characteristic power source. Arc self-regulation plays an essential role in the welding process.
During the welding wire feeding process, the flat characteristic power source increases the melting speed of the welding wire, allowing the welding current to be adjusted by locally modifying the wire feeding speed.
In summary, the welding current in carbon dioxide welding is the result of the collective influence of E, R and RH.

However, in this system, E and R have a relatively wide range of adaptation, while RH is more sensitive to changes in the system.
To maintain the stability of the welding process and reduce spatter, it is necessary to frequently adjust the wire feed speed so that the melting speed of the welding wire matches the wire feed speed.
This process results in changes in the welding current, which is why we usually refer to adjusting the wire feed speed as welding current adjustment.
If we think that the wire feed speed is the only way to adjust the welding current, we may blindly increase the wire feed speed to increase the welding current, which can cause “wire lift” – a phenomenon where the welding gun is pushed back and the welding process becomes discontinuous.
In contrast, reducing the wire feed speed just to decrease the current can cause a discontinuous welding process with large spatter, resulting in a weak welding gun and highly stacked but unpenetrated weld beads.
To obtain optimal welding results, experienced welders coordinate voltage and current (wire feed speed) adjustments while observing the state of the weld and listening to the sound of the wire transition.
Beginners can consult the CO 2 formula of the welding arc characteristic curve to be adjusted, where UH=15+0.04I (UH represents the arc voltage; I represents the welding current).
For example, when the welding current is 200A, the arc voltage should be around 23V. These two data can be read from the voltmeter and ammeter of the power supply.
It is worth noting that due to the voltage drop of the welding cable and the contact resistance of each connection point in the welding circuit, the voltmeter reading may be higher than the actual voltage.
When using a certain diameter of welding wire, there is more than one stable working point in the welding process. For example, when using φ1.2mm welding wire in short circuit transition state, the current can be adjusted from 90A to 150A and the voltage range is between 19V and 23V. In the particle transition state, the current can range from 160A to 400A, and the voltage can be adjusted to operate between 25V and 38V.