Compared to movement on the ground, flying is more difficult and complex because it involves movement within the Earth's atmosphere. Regardless of the type of aircraft, whether commercial, defense or space aviation, the durability and effectiveness of the various parts of the aircraft must be considered.
Manufacturing complex aircraft part geometries with high precision requires specialized knowledge and skill. In other words, human error cannot occur in the manufacturing of parts for the aerospace industry.
What is CNC machining in the aerospace industry?
Aerospace CNC machining uses computer-based tools and components to produce and maintain aircraft and aerospace parts. It is a computer-aided manufacturing process that moves cutting tools using pre-programmed codes and software.
Although many industries use CNC to manufacture parts and products, the aerospace industry is one of the most sensitive where there is no room for error. Furthermore, manufacturers with CNC machines achieve the same results regardless of the quantity produced, whether a single part or thousands of parts.
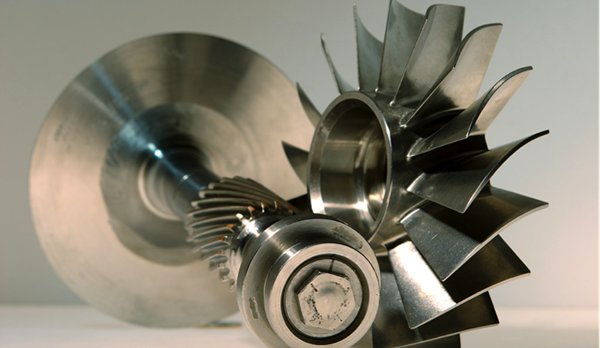
What materials are used in aerospace machining?
Machining parts in the aerospace industry is an adaptable process. However, not all metals and plastics are ideal for manufacturing aerospace parts. Below are the materials used in machined parts in the aerospace industry.
Aluminum and aluminum alloys
Aluminum is one of the most used metals for machining aerospace parts, mainly due to its high tensile strength and light weight. Aluminum is also very malleable, which makes it easier to process on CNC machines.
The most popular aluminum alloy for CNC machining in the aerospace industry is 7075 aluminum, the main alloy component of which is zinc. Offers good resistance to fatigue. The material was used to manufacture various wing, fuselage and support structure components.
Aircraft aluminum alloys 4047 (cladding/filling), 6951 (fins) and 6063 (frame) are also machinable. Therefore, 6000 series alloys are generally considered easier to machine than others.
Titanium and titanium alloys
Aerospace is the sector where titanium alloys are most used worldwide. The metal tolerates high temperatures well, is resistant to corrosion and has a good strength/weight ratio. The use of titanium in the aerospace industry has become common.
Commercial and military aircraft, such as the Airbus A380 and Boeing B787, as well as helicopters such as the F-22, F/A-18 and UH-60 Black Hawk, require significant quantities of this material for their various parts. The aircraft structure and titanium engine components include discs, rotor blades, shafts and casings.
CNC machining titanium can be more difficult because it is harder than aluminum, which often leads to tool wear and heat buildup, which can warp the material. Therefore, aerospace titanium machining must be done at a lower machine speed and higher chip load.
Technical plastics
Due to their incredibly light weight, excellent impact and vibration resistance, sealing properties and chemical resistance, plastics can be a valuable alternative to metals. Furthermore, they provide better electrical insulation compared to metals and are ideal for CNC prototyping. PEEK, polycarbonate and Ultem are high-performance polymers used in the aerospace industry.
Aerospace engineering plastics can be CNC machined into aircraft parts such as cabin interiors, trays, wear pads, armrests, backlit instrument panels, valve components, casings, hoses and insulation.
Not all engineering plastics are ideal for aerospace CNC machining, as aircraft polymers must meet certain toxicity, smoke and flame standards. So it is a crucial factor.
Benefits of CNC Machining for Aerospace Parts
CNC machining is perfect for producing aircraft parts due to its numerous advantages. Benefits include:
Create lightweight components
Weight is a crucial factor for flying parts of technology. CNC machining can be used to create thin-walled structures and components from strong yet lightweight materials to meet this need. This makes them ideal for use in the aerospace industry to produce parts and components.
Minimal defects in parts
Parts manufactured using traditional/conventional manufacturing methods are subject to errors due to dimensional errors caused by the human factor. However, this is hardly the case with precision CNC machining, as this manufacturing process ensures that aerospace parts meet strict size, tolerance and performance standards, ensuring high performance and preventing part failures.
High accuracy and precision
Precision is the hallmark of CNC machining as it produces parts with high precision and consistency. CNC machines are accurate to a few micrometers, with a small margin of error. The use of CNC machining in the aerospace industry ensures the production of parts that precisely fit aircraft parts, thus avoiding general part failures and resulting loss of property.
Consistency and efficiency
CNC machining increases manufacturing efficiency in the aerospace industry. This process is automated, which increases production speed and reduces time while ensuring that the parts produced are accurate and consistent. Thanks to this precision and consistency, there is minimal waste and the parts produced rarely need to be reworked due to dimensional inaccuracies.
CNC machining processes for aviation
The aerospace industry has a high demand for parts with extreme precision, which is why precision machining is necessary in the aerospace industry. The reason for this is that most parts have complex designs and geometries. There are different types of CNC machines, but for high precision, two main CNC machines are used in the aerospace industry.
Precision CNC milling
This is a multi-axis machining process that uses a milling machine to produce parts. The machine used for this production moves along the traditional linear X, Y and Z axes, as well as the A and B rotation axes, allowing the creation of complex shapes and geometries.
While it is possible to use a 3- or 4-axis CNC milling machine when machining aerospace parts, it is better to use a 5-axis CNC milling machine as they can be machined in a single operation. Can work in up to 5 directions of the piece. This helps manufacturers reduce errors and lead times. Furthermore, the cutting tools on 5-axis CNC machines rotate at high speed, which ensures the accuracy and precision of the parts.
CNC milling allows for the precise manufacturing of aerospace parts such as landing gear, electrical components, and transmissions.
Precision CNC turning
This process, also known as subtractive machining, involves removing material to create the desired shape. In the precision turning process, the material bars are held in a wedge shape and rotated. This process continues until the material reaches the desired shape.
CNC precision turning is a detailed and complex process for producing cylindrical aerospace parts. It is also important to note that this process is highly precise, as the computer controls the speed and position of the tool and material used.
CNC precision turning produces aerospace parts such as screws, nuts, threads, end pins, fasteners and shafts.
Typical Surface Finishes for CNC Aircraft Parts
Although several surface treatments are available for CNC machined parts in the aerospace industry, not all are ideal for use on aircraft components. The industry uses four types when it comes to choosing between different surface treatments.
Anodizing
In this type of surface treatment, the aerospace part is immersed in an electrolytic solution, creating a uniform layer of oxide on the surface of the part. Two types of anodizing are used on aerospace parts: Type II and Type III.
Type II anodizing forms a decorative layer on the surface of the part. This layer is often thin, making the surface and aerospace part susceptible to corrosion and abrasion when exposed to it. Type III anodizing, on the other hand, creates a more protective hard layer on the surface of the part.
Anodizing aluminum as a surface finish protects aerospace parts from corrosion and improves their durability.
Passivation
Passivation is a common post-processing method used in aerospace CNC machining to improve the functionality and surface quality of products. The surface of the part may show microroughness or surface contamination after the machining process, which can negatively affect the performance of the part over time. However, with passivation, these problems are no longer problems, as the process improves the corrosion resistance of aerospace parts and reduces the need for maintenance.
polishing
Polishing is one of the ideal surface treatments for use on aerospace parts. It's a simple process that uses the idea of sanding to smooth any surface. The process generally begins with the roughest surface of the aerospace part and progresses until a smooth, attractive surface finish is left.
Additionally, polishing can increase the durability of an aerospace material. This is done by reducing the likelihood of chips or cracks. The downside is that polishing aerospace parts takes a lot of time and can be expensive.
Powder coating
The most common surface treatment for aerospace metal parts is powder coating. It is very popular due to its variety of functions and durability. Powder coated aerospace parts are scratch resistant and will not fade over time.
Additionally, this surface finish is available in a wide range of colors to provide aerospace parts manufacturers with greater flexibility and improved aesthetics.
Tips for machining aerospace parts
CNC machining aerospace parts is a difficult task. However, here are some tips to keep in mind during the process or before visiting an aerospace CNC shop.
Run a simulation
Before starting actual production of aerospace parts, use CNC machining simulation software to ensure everything is perfect from start to finish. Simulation software allows you to visualize the performance of your aerospace parts before starting production.
Use the right machine and cutting tools
There are various CNC machines and cutting tools, but not all of them are suitable for machining aerospace parts. That's why it's best to use the right tools and machines for the job. To increase the size of your equipment, it is often recommended to use large, high-speed milling machines designed specifically for this task.
Divide production into specialized parts
Looking at a product as a unit can seem daunting, so it's best to split production lines. Divide the production system into specialized parts depending on product quality and components. Choosing the right equipment for the job will help simplify aerospace parts production.
Choose the right design
The design phase is one of the most important steps in product development. A properly adapted design can save the time required for part preparation, increasing productivity, efficiency and reliability.
CNC machining applications in the aerospace industry
There are many uses for CNC machining in the aerospace industry. Below are the most common ones.
Electrical Connectors : CNC machining supports the production of the aircraft's electrical system, which consists of vital components. The production of the aircraft's electrical system often depends on its weight and space limitations.
Valve components : These small components are widely used in the aerospace industry and CNC machined valves ensure parts precision and effective and safe operation.
Oxygen-producing components : CNC machining helps produce oxygen-producing safety systems that are robust, temperature-resistant, and lightweight.
Waves : In aviation, waves play a fundamental role in transmitting energy. CNC machining makes it easy to produce robust parts from heat-resistant materials.
Other aerospace CNC machining applications include cabin parts, wing ribs, fuselage components, actuators, motion controls, engine casings, landing gear components, discs and filter housings.
Choose WayKen for your aerospace CNC machining projects
We know that each project and its application is different. Therefore, we offer each customer unique yet practical solutions, including precision machining services and custom surface finishing. So what are you waiting for? Contact us today and let us start manufacturing your high-quality aerospace machined part.
Common questions
Are there any special surface quality requirements in CNC machining of aerospace components?
Yes, to some extent, incredibly tight tolerances can be achieved with CNC machining, allowing for various surface qualities often required in the aerospace industry.
Is precision important in CNC machining of aerospace parts?
A fundamental aspect of manufacturing aerospace parts is precision machining. This industry has very high production standards and stricter safety regulations for CNC machining of aircraft parts.