Cogeneration or Combined Heat and Power (CHP) is the combined generation of heat and power. It is not a single technology, but an integrated energy system. Cogeneration first involves producing energy from a specific fuel source, such as natural gas, biomass, coal or oil. During fuel combustion, cogeneration captures excess heat that would otherwise have been wasted.
The captured heat can be used to boil water, create steam, heat buildings, etc. For example, in the oil sands, steam is needed to produce bitumen. By using cogeneration, energy companies can simultaneously produce steam for production and electricity on site. By minimizing waste, cogeneration plants generally convert 75-80% of the fuel source into usable energy, compared to conventional systems that only cover around 45%/
When the captured heat is used to produce electricity, the process is called a combined cycle.
Cogeneration was practiced in some of the first electrical generation installations. Before central stations distributed energy, industries that generated their own energy used exhaust steam for process heating. Large office and apartment buildings, hotels, and stores often generated their own power and used waste steam for building heating. Due to the high cost of upfront energy, these cogeneration operations continued for many years after utility electricity became available.
Types of Cogeneration :
There are two broad categories of cogeneration:
1. The coverage cycle:
In this type, the primary heat at the higher temperature end of the Rankine cycle is used to generate high-pressure, high-temperature steam and electricity in the usual way.
The process steam at low pressure and temperature is then removed from the turbines according to the process requirements. There are two ways to use steam.
They are the following:
(a) Using steam in the turbine exhaust – The steam turbine in this case is called a back pressure turbine. The condenser is removed and the turbine exhaust is conveyed to the process plant. Because the condenser is absent, the turbine's exhaust pressure is higher (hence the name backpressure turbine) and its efficiency is lower.
(b) Extracting steam from the turbine in an intermediate state; as well as for heating feed water. A turbine of this type is known as an extraction turbine or a passing turbine. As a condenser is used, the cycle efficiency is greater; and the extracted steam has much higher pressure and temperature.
The main advantage of this cycle is its ability to use a wide range of fuels, including wood, coal, oil, coke, waste, etc. and is therefore used where low quality waste and by-product fuels are readily available.
This type, however, is rarely used due to its high initial cost and low power/heat ratio; especially at high process steam pressures.
2. Background cycle:
Here, the first primary heat at high temperature is used directly to meet the process requirements. Low quality waste heat (low temperature and availability) from the process plant is used to generate electricity. The cycle efficiency is obviously low, –10% for low temperature applications and up to 20% for high temperature applications. Since waste heat is free, cycle economics can be favorable.
The main applications of bottom cycles are in the chemical and material processing industries, such as cement, limestone and steel.
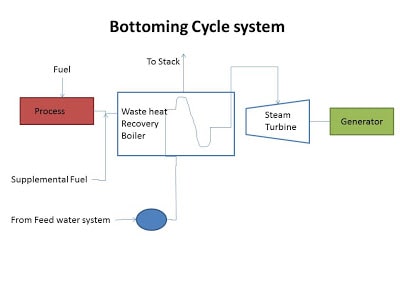
Because the temperature of waste heat is low, hydrocarbon fluids are often used as the working medium.
Types of coverage cycle :
Because the bottoming cycle has very low combined efficiency, it is of little thermodynamic or economic interest, and therefore only the topping cycle can provide real savings in primary energy. Furthermore, most process applications require a low quality steam (low temperature and availability) that can be conveniently produced in a topping cycle.
Some of the arrangements for cogeneration in the coverage cycle are as follows:
(a) Steam turbine plant with back pressure turbine.
(b) Steam turbine power plant with condensing turbine steam extraction.
(c) Gas turbine power plant with heat recovery boiler – using gas turbine exhaust to generate steam.
(d) Combined steam gas turbine power plant – The steam turbine is of the back pressure type (a) or extraction-condensation type (b) above.
Backpressure steam turbine plant (a) is best suited only when electricity demand is low compared to heat demand. The combined cycle plant (d) above is best suited only when electrical demand is high, roughly comparable to heat demand or higher. The gas turbine cycle (c) falls in the middle. Only the extraction condensation plant (b) above is suitable over a wide range of ratios.
Cogeneration with a gas turbine plant :
Gas turbines are used alone in a wide range of services.
Some of them are:
1. As a propulsion unit for all types of aircraft.
2. To drive mechanical equipment such as pumps and compressors in industrial plants.
3. As a power unit for railways and racing cars.
4. To drive electrical generators in electrical power plants – To produce energy for peak loads.
There is also growing interest in the use of gas turbines for cogeneration and combined cycle plants. The working temperatures of the gas turbine are quite high (maximum temperature around 1200 – 1300°C) and the hot exhaust gases leaving the turbine at around 500°C still contain a large amount of stored thermal energy.
This thermal energy can be used for various purposes, such as:
1. Drying and direct heating – In the food industry.
2. Fluid heating in process industries – to heat air, oil, water which is a working medium in a process plant.
3. Steam production using a waste recovery boiler – The steam produced can be used for process application or for generating electricity using steam turbines. This is known as “cogeneration” for the former and “combined cycle” for the latter.
A simple gas turbine cycle composed of an Air Compressor (AC), Combustion Chamber (CC) and Gas Turbine (GT) is used. The turbine exhaust gases pass through a heat recovery boiler (HRB) to generate process steam which is then taken to the process plant. Supplemental fuel burners are provided to burn additional fuel to increase the process steam mass flow rate for a short period if necessary.