Fasteners are a common component that everyone should be familiar with.
In this article, we will introduce fasteners from four perspectives: fastener classification, thread identification and inspection, material requirements, heat treatment requirements, and mechanical performance requirements for bolts, bolts, and studs, as well as the types and structure of steel frame bolts. .
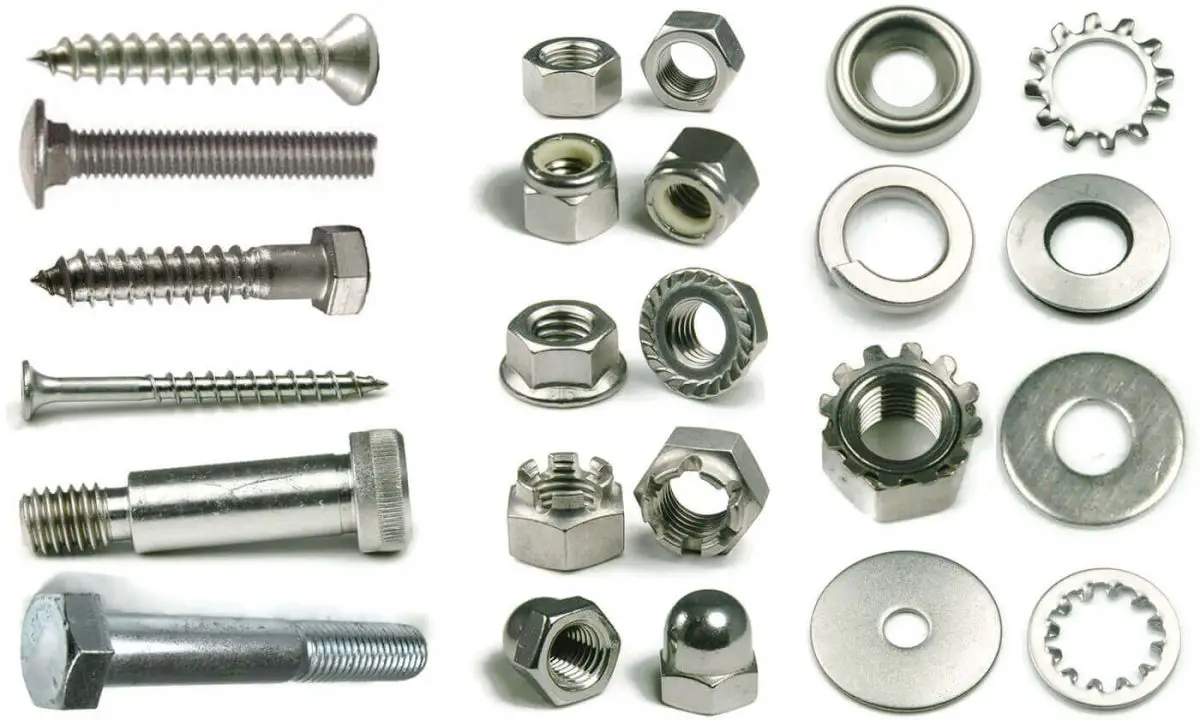
I. Classification of Fasteners
What are fasteners?
Fasteners are mechanical components used to securely join two or more parts or components into a single unit. They are also commonly called standard parts in the market.
Types of fasteners:
Fasteners generally include the following twelve types of parts: bolts, studs, screws, nuts, self-tapping screws, wood screws, washers, retaining rings, pins, rivets, complete sets and connecting pairs, as well as welding nails .
(1) Screws:
Screws are a type of fastener made up of a head and a screw (cylinder with external thread) that requires a nut to fix two pieces with through holes. This type of connection is known as a screw connection and is removable as the two parts can be separated if the nut is unscrewed from the screw.
As shown below:
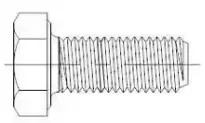
Fig. 2-1-1 Complete threading of the external hexagonal screw
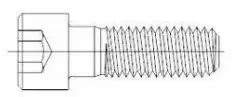
Fig. 2-1-2 half tooth of internal hexagonal screw with cylindrical head
(2) Stallion:
A pin is a fastener that has external threads on both ends and has no head. When connecting, one end is screwed into a part with an internal threaded hole, while the other end passes through a part with a through hole and is secured by a nut. This results in a tightly connected whole.
This type of connection is called a pin connection and, like the screw connection, is a removable connection. Pins are mainly used when one of the connected parts is thick, requires a compact structure, or frequent disassembly makes the bolted connection unsuitable.
As shown below:
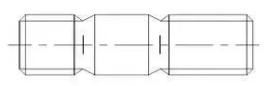
Fig. 2-2-3 double head pin
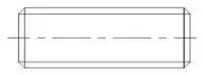
Fig. 2-2-4 full thread pin
(3) Screw:
A screw is a fastener consisting of a head and a screw. It can be divided into three categories based on its purpose: steel structure screw, fastening screw and special purpose screw.
Machine screws are mainly used to attach a part with a fixed threaded hole to a part with a through hole without the need for a nut (this type of connection is known as a bolted connection and is also a removable connection). Machine screws can also be used with nuts to fasten two parts with through holes.
Set screws are mainly used to fix the relative position between two parts.
Special purpose screws, such as eyebolts, are used to lift components.
As shown below:
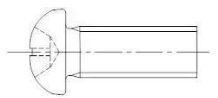
Fig. 2-3-5 pan head screw
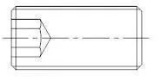
Fig. 2-3-6 Internal hexagon fixing screw
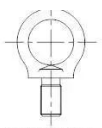
Fig. 2-3-7 eyelet
(4) Walnut:
A nut is a component that has an internal threaded hole and is typically in the shape of a flat hexagonal column, a flat square column, or a flat cylindrical shape.
Nuts are used to fasten and connect two parts into a single unit with bolts, pins, or steel framing bolts.
As shown below:
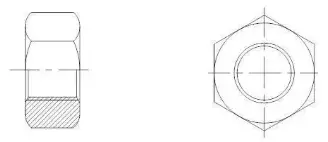
Fig. 2-4-8 hex nut
(5) Self-tapping screw:
A self-tapping screw is similar to a screw, but has a special thread designed specifically for self-tapping screws.
It is used to fix and connect two thin metal components into a single unit. Small holes need to be pre-drilled in the components. Because the screw has a high level of hardness, it can be screwed directly into the component hole to form corresponding internal threads on the component.
This type of connection is also removable.
As shown below:
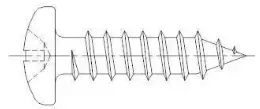
Fig. 2-5-9 self-tapping screw
(6) Wood Screws:
A wood screw is similar to a screw but has a special thread designed specifically for use in wood. It can be screwed directly into a wooden component or part to firmly connect a metallic (or non-metallic) part with a through hole to the wooden component.
This type of connection is also removable.
As shown below:
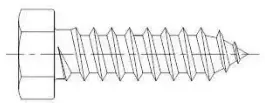
Fig. 2-7-10 hexagonal head wood screw
(7) Washer:
A washer is a type of fastener with a flat circular shape.
It is placed between the supporting surface of bolts, screws or nuts and the surface of connected parts to increase the contact surface area, reduce pressure per unit area, and protect the surface of connected parts from damage. Another type of spring washer can also prevent the nut from loosening.
As shown below:
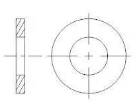
Fig. 2-7-11 flat washer
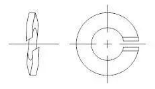
Spring washer 2-7-12
(8) Retaining ring:
A retaining ring is installed on the shaft groove or hole groove of steel structures and equipment to prevent the movement of parts on the shaft or hole from left to right.
As shown below:
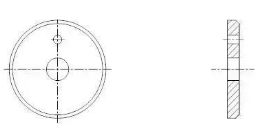
Fig. 2-8-13 retaining ring
(9) Pin:
Pins are primarily used to position parts, and some can also be used to connect, secure, transmit power, or lock other fasteners.
As shown below:
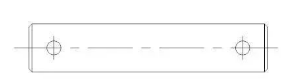
Figure 2-9-14 pin
(10) Rivets:
Rivets are fasteners comprised of a nail head and shank and are used to securely connect two parts or components with through holes into a single unit. This type of connection is known as a rivet connection and is also known as riveting.
Rivets form a non-removable connection as the rivets must be destroyed to separate the two connected parts.
As shown below:
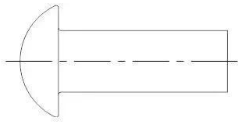
Fig. 2-10-15 Half round head rivet
(11) Mounting and connection pair:
An assembly refers to a fastener supplied as a combination, such as a machine screw (or screw, self-tapping screw) and a flat washer (or lock washer, spring washer).
A connecting pair refers to a fastener consisting of a special bolt, nut and washer, such as a high-strength large hexagonal screw connecting pair for steel structures.
As shown below:
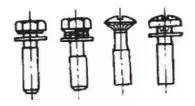
Fig. 2-11-16 machine screw assembly
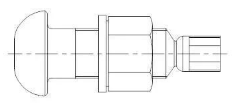
Fig. 2-11-17 Torsional shear bolt connection of steel structure
(12) Grip:
A tack is a single fastener consisting of a polished shank and a nail head (or no nail head) that is fixedly connected to a part or component by welding, to connect it to other parts.
As shown below:
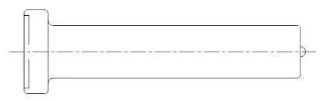
Fig. 2-12-18 welding nail
II. Thread Identification and Inspection
1. Purpose and characteristics of the thread:
Threads are commonly found in a variety of applications, including aircraft, cars, water pipes, and everyday gas use.
In most cases, wires serve as fastening connections and facilitate the transfer of force and movement.
Although there are several types of special-purpose threads, their number is limited.
The durability and simplicity of threads, combined with their reliable performance, easy disassembly and convenient manufacturing, make them a crucial component in all types of electromechanical products.
For a thread to work effectively, it must possess two essential qualities:
- The ability to easily rotate;
- Adequate strength.
2. Thread classification
The. Threads can be categorized into four types based on their structural characteristics and uses:
- Common thread (fastening line): It has a triangular tooth shape and is used for connecting or fixing parts. Common threads can be further divided into coarse and fine threads based on their pitch. Fine threads have greater connection strength.
- Transmission wire: Its tooth shape includes trapezoidal, rectangular, saw-shaped and triangular shapes.
- Sealing thread: Used to seal connections, mainly pipe threads, tapered threads and tapered pipe threads.
- Special purpose thread: Used for specific purposes.
B. Threads can also be divided based on region (country) into metric threads, British threads, and American threads.
British and American threads are collectively called British threads and have a tooth profile angle of 60° and 55°. They use inch sizes for diameter, pitch and other relevant parameters.
In our country, the tooth profile angle is standardized at 60° and the diameter and pitch series are measured in millimeters. This type of thread is called a common thread.
3. Common Topic Profile
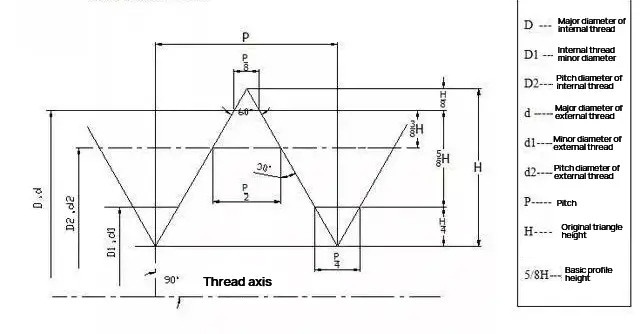
4. Basic Topic Terms
A thread is a continuous formation along a specified cylindrical or conical surface.
- External thread: A thread formed on the outer surface of a cylinder or cone.
- Internal thread: A thread formed on the inner surface of a cylinder or cone.
- Major Diameter: The diameter of an imaginary cylinder or cone that is tangent to the top of an external thread or the bottom of an internal thread.
- Small diameter: The diameter of an imaginary cylinder or cone that is tangent to the bottom of an external thread or the top of an internal thread.
- Mean diameter: The diameter of an imaginary cylinder or cone that passes through the groove of the tooth shape where the width of the protuberance is equal. This imaginary cylinder or cone is referred to as a pitch diameter cylinder or pitch diameter cone.
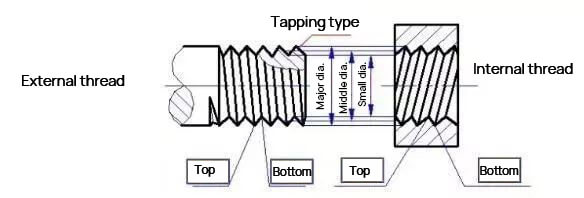
- Right-hand thread: A thread that is screwed in by turning clockwise.
- Left-hand thread: A thread that is screwed in by turning counterclockwise.
- Profile Angle: The angle between two adjacent sides of the tooth in the thread profile.
- Pitch: The distance along the axis between two corresponding points on the pitch line of two adjacent teeth.
5. Wire marking
Metric thread marking:
Generally, a complete metric thread designation should cover the following three aspects:
A represents the thread type code, indicating the characteristics of the thread;
B refers to the thread size, which generally includes the diameter and pitch. For multithreaded threads, you must also include the lead and number of threads;
C refers to the thread accuracy, which is determined by the tolerance zone of each diameter (including the position and size of the tolerance zone) and the screwing length.
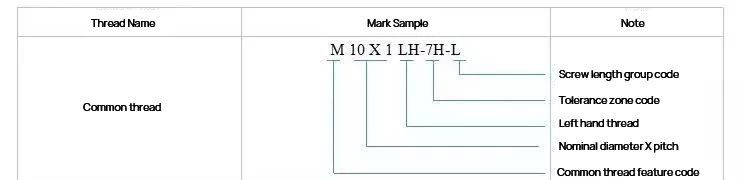
Inch thread marking:
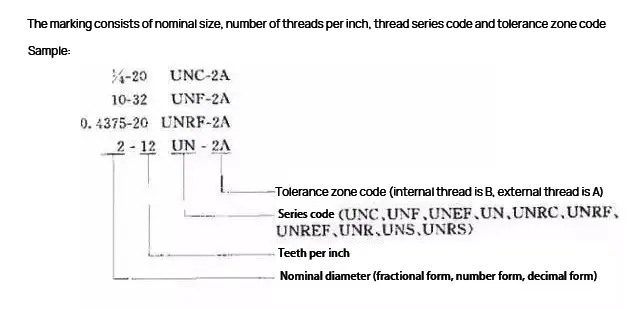
6. Thread measurement
For general standard threads, thread ring gauges or plug gauges are used for measurement.
Because there are numerous thread parameters, it is impractical to measure each one individually. Typically, thread gauges (thread ring gauges and thread plug gauges) are used to make a comprehensive thread assessment.
This inspection method, known as simulated assembly acceptance, is not only convenient and reliable, but also meets the accuracy requirements for typical threads.
As a result, it has become the most widely used acceptance method in actual production.
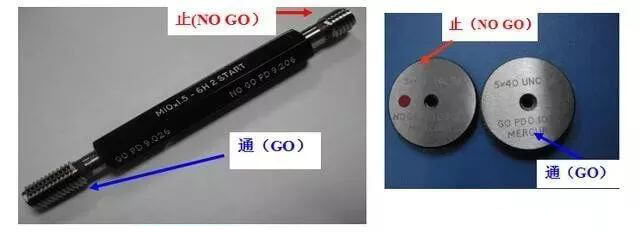
7. Thread measurement (pitch diameter)
In threaded connections, pitch diameter is the only factor that determines thread fit, making it crucial to correctly evaluate pitch diameter qualifications.
To ensure the basic service performance of the thread, the standard must specify the pitch diameter qualification judgment principle: “The actual pitch diameter of the thread cannot exceed the pitch diameter of the maximum solid profile of the tooth. The single pitch diameter of any part of the actual thread shall not exceed the pitch diameter of the minimum solid profile.”
Currently, there are two convenient methods for measuring single pitch diameter: using a thread pitch diameter micrometer or using the three-needle method (which is adopted by our company).
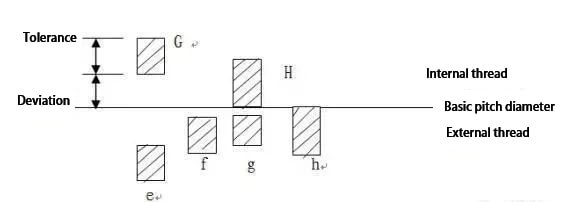
8. Thread adjustment degree:
Thread fit refers to the degree of tightness or looseness between the screw threads.
Fit class, on the other hand, refers to the specified combination of tolerance and runout for internal and external threads.
(1) For unified inch threads:
External threads have three classes: Class 1A, Class 2A, and Class 3A.
Internal threads also have three classes: Class 1B, Class 2B and Class 3B, all with loose fit.
The higher the class number, the tighter the fit.
On English threads, only Class 1A and Class 2A have specified offsets. Class 3A has zero deviation and Class 1A and Class 2A have equal deviation.
The higher the class number, the lower the tolerance, as shown in the figure.
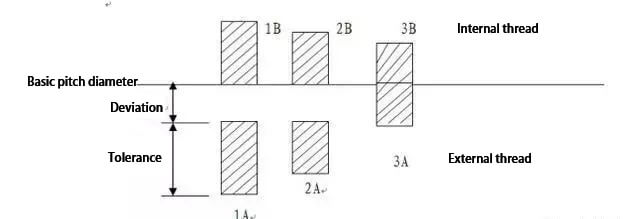
- Class 1A and Class 1B have very low tolerance and are suitable for internal and external thread tolerance adjustments.
- Class 2A and Class 2B are the most widely used thread tolerance grades specified for British series mechanical fasteners.
- Class 3A and Class 3B have the tightest fit and are suitable for fasteners with tight tolerances, especially for safety-critical projects.
- External threads specified fit deviations for Class 1A and Class 2A, but not for Class 3A.
The tolerance for Class 1A is 50% greater than that of Class 2A and 75% greater than that of Class 3A. For internal threads, Class 2B tolerance is 30% greater than Class 2A.
The tolerance for Class 1B is 50% greater than that of Class 2B and 75% greater than that of Class 3B.
(2) The common thread grades for external metric threads are 4H, 6E, 6G and 6H, while the common thread grades for internal threads are 6G, 6H and 7H.
The precision grade of Japanese standard threads is divided into three grades: I, II and III, with grade II being the most commonly used.
In metric threads, the basic deviation of H and h is zero, while the basic deviation of G is positive, and the basic deviation of e, f and g is negative, as shown in the figure.
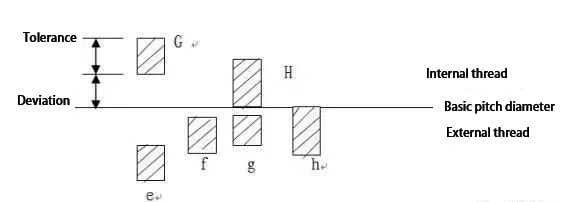
- H is the most commonly used tolerance zone position for internal threads and is generally not used for surface coating or very thin phosphating layers. The use of the basic deviation from the G position is rare and is mainly used for thicker coatings.
- The G tolerance zone is often used for coating with 6-9um thin coating. For example, when product drawings require 6H screws, the threads must be coated with 6G tolerance zone.
- The best thread adjustment combinations are H/G, H/H or G/H. For refined fasteners such as screws and nuts, it is recommended to use 6H/6G.
Average precision degree of common thread
Walnut: 6H
Screw: 6g
Medium precision class of thick coated threads
Nut: 6G
Screw: 6e
High precision grade
Walnut: 4H
Screw: 4h, 6h
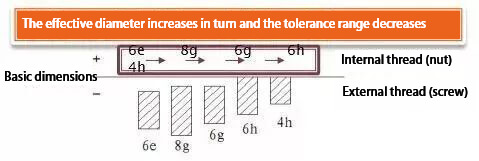
M6-P1. 0 | External diameter | Effective diameter |
6e | 5.76-5.94 | 5.178-5.29 |
8g | 5,694-5,974 | 5,144-5,324 |
6g | 5,794-5,974 | 5,212-5,324 |
6am | 5.82-6.00 | 5,238-5,350 |
4h | 5.868-6.00 | 5,275-5,350 |
9. Common Special Topic
1). Self-tapping wire: It is a kind of wide wire with a large lead.
GB/T5280 JIS B1007
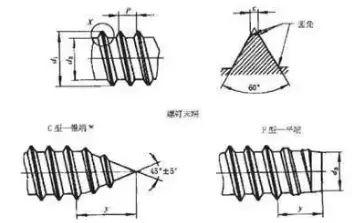
Specifications | Tooth step |
ST 1.5 | 0.5 |
ST 1.9 | 0.6 |
ST 2.2 | 0.8 |
ST 2.6 | 0.9 |
ST 2.9 | 11 |
ST 3.3 | 1.3 |
ST 3.5 | 1.3 |
ST 3.9 | 1.3 |
ST 4.2 | 14 |
ST 4.8 | 1.6 |
ST 5.5 | 1.8 |
ST 6.3 | 1.8 |
ST 8 | 2.1 |
ST 9.5 | 2.1 |
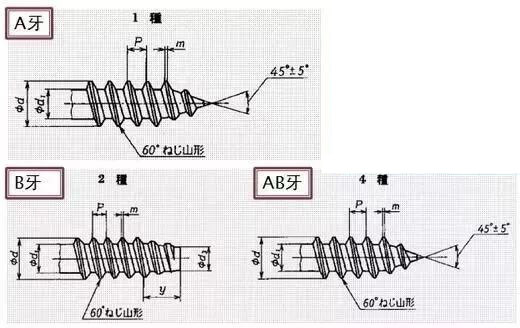
Specifications | two | 2.5 | 3 | 35 | 4 | 45 | 5 | 6 | 8 |
Number of teeth | AB Teeth | 40 | 28 | 24 | 20 | 18 | 16 | 14 | 12 |
A tooth | 24 | 18 | 16 | 14 | 12 | 10 | 9 |
Specifications | Number of teeth | |
AB Teeth | A tooth | |
two | 40 | |
2.5 | 28 | |
3 | 24 | 24 |
35 | 20 | 18 |
4 | 18 | 16 |
45 | 16 | 14 |
5 | 12 | |
6 | 14 | 10 |
8 | 12 | 9 |
2) Self-tapping locking thread (triangular thread)
GB6559
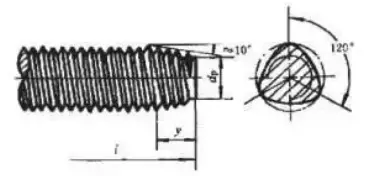
3. ) Nail thread for wall panel (quick thread)
GB/T14210
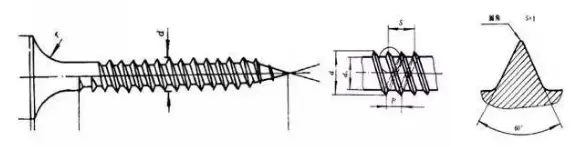
4) Wooden wire:
See Fig. 1-1-32 for thread profile and wood screw size (CB/T922-1986)
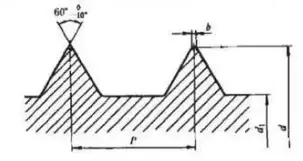
Fig. 1-1-32 thread profile for wood screw
III. Material requirements, heat treatment requirements and mechanical performance requirements of screws, screws and pins
Material requirements for screws, screws and pins
Performance level | Materials and heat treatment | Chemical composition /% | Quenching temperature ℃ min | ||||
W | Pmax | Smax. | Bmax | ||||
min | max. | ||||||
4.6 | Carbon steel or carbon steel with added elements | – | 0.55 | 0.05 | 0.06 | anything | – |
4.8 | |||||||
5.6 | 0.13 | 0.55 | 0.05 | 0.06 | – | ||
5.8 | – | 0.55 | 0.05 | 0.06 | |||
6.8 | 0.15 | 0.55 | 0.05 | 0.06 | |||
8.8 | Carbon alloy copper (e.g. copper, manganese or chromium) with added elements is quenched and tempered | 0.15 | 0.40 | 0.025 | 0.025 | 0.003 | 425 |
Medium carbon steel, quenched and tempered | 0.25 | 0.55 | 0.025 | 0.025 | |||
Alloy Steel Rate and Tempering | 0.20 | 0.55 | 0.025 | 0.025 |
Performance level | Materials and heat treatment | Chemical composition/% | Quenching temperature ℃ min | ||||
W | Pmax | Smax. | Bmax | ||||
min | max. | ||||||
9.8 | Carbon alloy steels with added elements (such as boron, manganese or chromium) are ignited and tempered | 0.15 | 0.40 | 0.025 | 0.025 | 0.003 | 425 |
Medium carbon steel, quenched and tempered | 0.25 | 0.55 | 0.025 | 0.025 | |||
Quenched and tempered alloy steel | 0.20 | 0.55 | 0.025 | 0.025 | |||
10.9 | Carbon alloy steel with added elements (such as boron, manganese or chromium), quenched and tempered | 0.20 | 0.55 | 0.025 | 0.025 | 0.003 | 425 (340 cancelled) |
Medium carbon steel, quenched and tempered | 0.25 | 0.55 | 0.025 | 0.025 | |||
Quenched and tempered alloy steel | 0.20 | 0.55 | 0.025 | 0.025 | |||
12.9 | Alloy steel, ignition rate and tempering | 0:30 | 0.50 | 0.025 | 0.025 | 0.003 | 425 |
12.9 | Carbon alloy steels with added elements (such as boron, manganese, chromium or molybdenum) are quenched and tempered | 0.28 | 0.50 | 0.025 | 0.025 | 0.003 | 380 |
Mechanical and physical properties of screws, nuts and pins
Subitem | Mechanical and physical properties | 4.6 | 4.8 | 5.6 | 5.8 | 6.8 | 8.8 | 9.8 | 10.9 | 12.9/12.9 | ||
d≤M6 | d≥M16 | |||||||||||
1 | Nominal tensile strength rmpA | nominal | 400 | 500 | 600 | 800 | 900 | 1000 | 1200 | |||
min | 400 | 420 | 500 | 520 | 600 | 800 | 830 | 900 | 1040 | 1220 | ||
two | Lower yield point rmpA | nominal | 240 | 300 | ||||||||
min | 240 | 300 | ||||||||||
3 | The stress of 0.2% non-proportional elongation is specified for the machined test part.RP0.2 Mpa | nominal | 640 | 640 | 720 | 900 | 1080 | |||||
min | 640 | 660 | 720 | 940 | 1100 | |||||||
4 | The specified non-proportional stretching stress of the fastener is 0.0048d.RXY Mpa | nominal | 320 | 400 | 480 | |||||||
min | 340 | 420 | 480 | |||||||||
5 | Guaranteed voltage MPa | 225 | 310 | 280 | 380 | 440 | 580 | 600 | 650 | 830 | 970 | |
Certified Stress Rate | 0.94 | 0.91 | 0.93 | 0.90 | 0.92 | 0.91 | 0.91 | 0.90 | 0.88 | 0.88 |
Subitem | Mechanical and physical properties | 4.6 | 4.8 | 5.6 | 5.8 | 6.8 | 8.8 | 9.8 | 10.9 | 12.9/12.9 | ||||
d≤M6 | d≥M16 | |||||||||||||
6 | Elongation after fracture of the machined specimen A f % | 22 | 20 | 12 | 12 | 10 | 9 | 8 | ||||||
7 | Reduction in the area of the machined specimen Z% min | 52 | 48 | 48 | 44 | |||||||||
8 | Elongation after fracture of the fixator A 1 % min | one | 0.24 | one | 0.22 | 0.2 | ||||||||
9 | Head firmness | New crack terminal | ||||||||||||
10 | Vickers hardness HVF ≥ 98N | min | 120 | 130 | 155 | 160 | 190 | 250 | 255 | 290 | 320 | 385 | ||
220 | 250 | 320 | 335 | 360 | 380 | 435 | ||||||||
11 | Brinell hardness HRB F=30D 2 | min | 114 | 124 | 147 | 152 | 181 | 238 | 242 | 276 | 304 | 366 | ||
max. | 209 | 238 | 304 | 318 | 342 | 361 | 414 | |||||||
12 | RockwellHRB hardness | min | 67 | 71 | 79 | 82 | 89 | |||||||
max. | 95.0 | 99.5 | ||||||||||||
Rockwell hardness | min | 22 | 23 | 28 | 32 | 39 |
4. Types and structure of steel structure screws
1. Overview of steel structure bolted connection
Bolted connection for steel structures is a method of connecting two or more parts or components of steel structures into a single unit using bolts. This type of connection is the simplest method for pre-assembling components and installing structures.
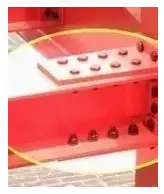
Complete screw connection of beam and column joints
The bolted connection was first used in the installation of metal structures. However, in the late 1930s it was gradually replaced by rivet connections and was only used as a temporary fastening method during component assembly.
The high-strength screw connection method emerged in the 1950s. These screws are made of medium-carbon steel or medium-carbon alloy steel and have a strength 2 to 3 times that of ordinary screws.
The high-strength screw connection has the advantages of being convenient to construct, safe and reliable. It has been used in the manufacture and installation of metal structures in metallurgical factories since the 1960s.
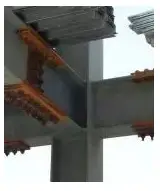
Complete connection of beam splice bolts
2. Screw Specification
Common bolt specifications used in steel structures include M12, M16, M20, M24 and M30. The letter “M” represents the screw symbol and the number is the nominal diameter.
Bolts are divided into 10 grades based on their performance: 3.6, 4.6, 4.8, 5.6, 5.8, 6.8, 8.8, 9.8, 10.9 and 12 ,9. Screws with grades greater than 8.8 are manufactured from low carbon alloy steel or medium carbon steel and undergo heat treatment (quenching and tempering). These are called high strength screws. Screws with grades lower than 8.8 (excluding 8.8) are called common screws.
The table below shows the performance grade and mechanical properties of screws.
mechanical property | Performance level | |||||||||||||||||||
3.6 | 4.6 | 4.8 | 5.6 | 5.8 | 6.8 | 88 | 9.8 | 10.9 | 12.9 | |||||||||||
≤M16 | ≥M16 | |||||||||||||||||||
Tensile strength, MPa | Nominal value | 300 | 400 | 500 | 600 | 800 | 800 | 900 | 1000 | 1200 | ||||||||||
Small value | 330 | 400 | 420 | 500 | 520 | 830 | ||||||||||||||
Rockwell hardness | HRB | CDH | ||||||||||||||||||
minimum value | 52 | 67 | 70 | 80 | 83 | 89 | 22 | 25 | 28 | 34 | 39 | |||||||||
Maximum | 95 | 99 | 32 | 35 | 37 | 41 | 44 | |||||||||||||
Yield point, MPa | Nominal value | 180 | 240 | 320 | 300 | 400 | 480 | |||||||||||||
minimum value | 190 | 340 | 420 | |||||||||||||||||
yield strength, MPa | Nominal value | 640 | 640 | 720 | 900 | 1080 | ||||||||||||||
Minimal stress | 660 | 940 | 1000 | |||||||||||||||||
Stress guaranteeSp.Mpa | 180 | 230 | 310 | 280 | 380 | 440 | 580 | 600 | 660 | 830 | 970 |
The screw's performance grade is composed of two parts of numbers, which respectively represent the screw's nominal tensile strength and the material's flow rate.
For example, the meaning of bolts with a performance grade of 4.6 is: the number in the first part (4 in 4.6) is 1/100 of the nominal tensile strength (n/mm 2 ) of the bolt material, or that is, fu ≥ 400N/mm 2 ;
The number in the second part (6 in 4.6) is 10 times the flow rate of the screw material, i.e. fy/fu = 0.6;
The product of two numbers (4) × 6 = “24”) is 1/10 of the nominal yield strength (or yield strength) (n / mm 2 ) of the screw material, which means fy ≥ 240n/mm 2 .
According to their level of manufacturing precision, common screws used in steel structures can be categorized into three grades: A, B and C.
Grade B screws are considered refined and typically used in mechanical products, while grade C screws are considered rough.
Unless otherwise specified, common bolts used in steel framing are typically thick Grade C bolts with a performance grade of 4.6 or 4.8.
The design value of resistance for bolted connections must be taken from Table 3.4.1-4 of code GB50017-2003 for the design of steel structures.
Table 3.4.1-4 Bolted connection resistance design value (n/mm 2 )
Bolt Performance Grade, Anchor Grade and Steel Component | Common screw | Radium suppository | High strength screw for pressure bearing connection | ||||||||
Grade C screw | Grade A and B screws | ||||||||||
Traction | Shear strength | Pressure bearing | traction | Shear strength | Pressure bearing | traction | traction | Shear strength | Pressure bearing | ||
Common screw | Level 4.6 and 4.8 | 170 | 140 | ||||||||
Level 5.6 | 210 | 190 | |||||||||
Note 8.8 | 400 | 320 | |||||||||
Bolt Anchor | Q235 Steel | one | 140 | ||||||||
Q345 steel | 180 | ||||||||||
High Strength Butterfly Screw Pressure Bearing Connection | Note 8.8 | 400 | 250 | ||||||||
Level 10.9 | 500 | 310 | |||||||||
component | Q235 Steel | one | 305 | 405 | 470 | ||||||
Q345 steel | 385 | 510 | 590 | ||||||||
Q390 steel | 400 | 530 | 615 | ||||||||
Q420 Steel | 425 | 560 | 615 |
Table 3.4.1-5 Design value of rivet connection resistance (n/mm 2 )
Willow nail steel grade and component steel grade | Remove the nail | Shear strength | Pressure bearing | |||
Type I hole | Class II hole | Type I hole | Class II hole | |||
rivet | BL2 or BL3 | 120 | 185 | 155 | ||
component | Q235 Steel | 450 | 365 | |||
Q345 steel | 565 | 460 |
3. Classification of screws
Screws are known by various names such as screws, nails, standard parts, fasteners, etc.
In a general sense, screws can encompass a variety of fasteners, including common screws, high-strength screws, anchor bolts, expansion screws, chemical anchors, bolts, pins, and more.
When considering screws more specifically, they can be divided into two categories: common screws and high-strength screws.
(1) Common screw connection
Ordinary screws can be divided into rough and refined screws based on manufacturing accuracy.
In addition, common screws can also be classified into various types, such as hex head screws, stud screws, countersunk head screws and others.
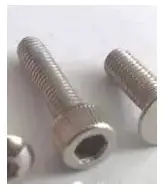
The image above shows countersunk head screws
rough screw
Class C screws are typically rough screws made from carbon structural steel.
To ensure smooth penetration of screws into screw holes, the hole diameter must be 1.0 to 2.0 mm larger than the nominal diameter (d) of the screws, resulting in a Class II hole.
Bolt hole spacing should be arranged to facilitate tightening with a wrench.
When raw bolts are used to connect the components of pillars, beams and roof trusses, a connection structure with support plates must be adopted.
In this scenario, the bolt is under tension and its shear force is supported by the support plate (as illustrated in the attached diagram).
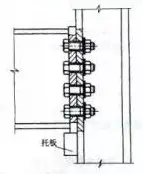
The low degree of resistance of the materials used in raw screws restricts their use in structural connections. However, raw bolts are still commonly used in connecting secondary beams to work platforms, wall beams, roof beams, brackets, and hinged supports with low shear force.
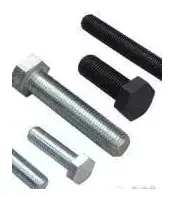
The figure above shows common screws.
Raw bolts are also often used in pre-assembly of steel structures in workshops, in pre-fixing riveted components before riveting, in assembly before connecting high-strength bolts, and in temporary fixation before welding of nodes .
When using rough screws as permanent fastener screws, they must be tightened after proper alignment and measures must be taken to prevent loosening.
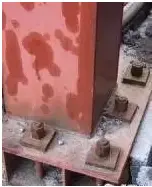
The figure above illustrates the double nut locking method for the column base screw.
Refined screw
Class A and B screws are considered refined screws and typically require Class I holes. The hole diameter should be 0.3 to 0.5 mm larger than the nominal diameter (d) of the screw.
Refined screw connections are used in some structural connections that are frequently disassembled and reassembled.
Refined screws are mainly used in mechanical products and are not commonly used in steel structure construction.
(2) High strength screw connection
Bolts made from high-strength steel or requiring high preload are called high-strength bolts.
These screws generate tension and transmit external forces through friction.
In contrast, a traditional bolt connection transmits shear force through the shear strength of the bolt and the bearing pressure of the hole wall.
When tightening the nut, the tension is minimal and can be disregarded.
In addition to the material's high strength, a high-strength screw also applies significant tension, resulting in extrusion pressure between the connecting components, providing strong friction perpendicular to the direction of the screw.
Furthermore, factors such as tension, anti-slip coefficient and type of steel directly impact the load capacity of a high-strength screw.
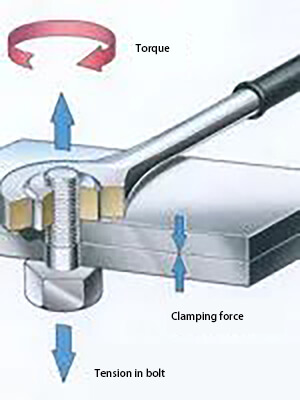
Working principle of high strength screw
High strength bolts are mainly classified into two categories based on their stress conditions: friction type and pressure type.
In terms of construction process, high-strength bolts are divided into two types: high-strength torsional shear bolts and high-strength large hexagonal bolts.
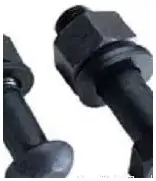
Torsional Shear Type High Strength Bolt and High Strength Large Hexagon Bolt
The friction-type high-strength screw connection transfers external force through the friction generated on the contact surface of the steel plate after the connecting plate layer is firmly adhered by the screw clamping pressure. The surface of the component is sandblasted to create a red rust surface, which provides a high coefficient of friction and reduces the number of connecting screws required. The hole diameter for a high strength friction type bolt should be 1.5 to 2.0 mm larger than the nominal diameter (d) of the bolt.
In contrast, the pressure-supported high-strength bolt connection transfers stress through the combination of friction between components, shear force from the bolt's central axis, and component bearing pressure. The hole diameter for this type of screw should be 1.0 to 1.5 mm larger than the nominal diameter (d) of the screw. Holes are drilled using a CNC drill and a drilling jig.
In essence, friction-type and pressure-type high-strength screws are the same screw, with the difference being the consideration of slip in the design. The friction surface of the friction-type high-strength screw cannot slide, and the screw cannot bear shear. If the friction surface slips, it is considered to have reached the design failure state, which is a relatively established and reliable technology. On the other hand, the friction surface of the high-strength bolt of the pressure bearing can slip and the bolt also undergoes shear, with the ultimate failure being similar to that of an ordinary bolt (screw shear failure or steel plate compression failure ).
The large high-strength hexagonal bolt is composed of a high-strength bolt, nut and two washers, forming a high-strength bolt connection pair. During construction, the structure is temporarily fixed with rough screws, and then high-strength screws are installed one by one from the middle of the screw group, starting with initial tightening, followed by retightening, and finally final tightening .
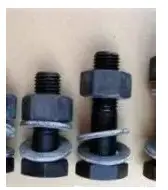
The figure shown above shows large pairs of high strength hex head screw connections of varying lengths.
When installing the high strength hexagonal head large screw connecting pair, a washer must be placed on both sides of the screw. The initial tightening torque value should be 50% of the final tightening torque value, while the retightening torque value should be equal to the final tightening torque value.
The formula for calculating the final value of the tightening torque is:
TC = k * Pc * d
Where
- Tc is the value of the final tightening torque, in n m;
- k is the torque coefficient;
- Pc is the construction requirement, in kN;
- d is the thread diameter of the high-strength screw, in mm.
A torque wrench must be used to tighten and must be calibrated before each use.
The torsional shear type high strength screw connection pair is composed of a high strength screw, a nut and a washer.
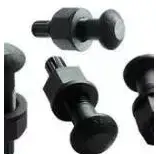
High strength torsional shear type screw
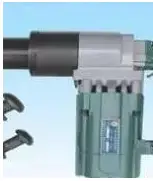
Electric Torsion Shear Wrench
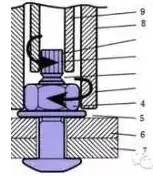
Installation principle of high strength torsional shear bolt
When installing the torsional shear type high strength bolt connection pair, only one washer should be placed on one side of the nut.
The formula for calculating the value of the initial tightening torque is:
Tc = 0.065 * Pc * d
Where
- Tc is the value of the initial tightening torque, in n · m;
- Pc is the construction claim, in kn;
- d is the thread diameter of the high-strength screw, in mm.
Finally, a specialized wrench should be used to unscrew the plum blossom head until it breaks.
Quality inspection should focus on supervision and inspection of the construction process.
(3) Anchor bolt
An anchor bolt, also known as an anchor bolt or anchor wire, is used to connect the base of a steel frame column to a concrete foundation. Q235 and Q345 round steels are commonly used for this purpose.
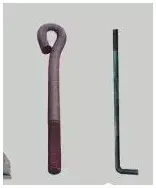
There are different types of anchors and if the diameter is greater than 24 mm, an anchor plate must be used.
During installation, the anchor bolt group must be fixed by the steel structure and installed together with the connecting reinforcement cage before pouring the concrete. The screw head must be exposed to the concrete surface for a specific length.
As soon as the concrete reaches a certain level of strength, the base of the steel column must be installed and secondary grouting must be carried out at the bottom of the column.
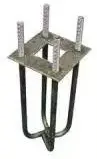
Group of fixed anchor bolts with steel structure
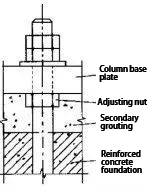
Anchor bolt schematic diagram
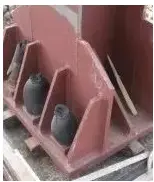
The image shows the base of a steel frame column before secondary grouting, with a rubber sleeve being used to protect the top of the thread anchor.
(4) Chemical anchor bolt
Chemical anchor is a new type of fastening material that consists of a chemical agent and a metal rod. It is used to install connectors from other structures into existing concrete structures.
It can be used to install post-embedded parts in various metal structure constructions, such as curtain walls and marble dry suspension. Furthermore, it can be used to install equipment, install guardrails on highways and bridges, reinforce and transform buildings, among other applications.
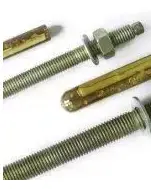
Bolt and chemical anchor bolt agent
The chemical anchor is a new type of anchor that follows the expansion anchor. It is a composite component that attaches and fixes to the perforated concrete substrate using a special chemical adhesive and screw, thus achieving anchorage of the fixed parts.
The chemical anchor bolt has a large load-bearing capacity and can replace the built-in anchor bar. It is often used to solve the problem of forgetting to install the embedded parts of a steel structure at the construction site after concreting the concrete. Chemical anchor can be used to correct this situation.
The chemical anchor construction steps are as follows:
- According to engineering design requirements, drill holes at designated positions in the base material (such as concrete). Hole diameter, depth and screw diameter should be determined by professional technicians or field testing.
- Drill the holes using a hammer drill or hydraulic drill.
- Clean the holes from dust using a special air cylinder, brush or compressed air machine. This should be repeated at least three times to ensure there is no dust or water in the hole.
- Make sure the screw surface is clean, dry and free from oil or masonry.
- Check the packaging of the glass tube anchor for any abnormalities such as damage or solidification of the agent. Insert the round head of the package into the anchor hole with the head facing outward and push it to the bottom of the hole.
- Using an electric drill and a special installation device, insert the screw into the bottom of the hole by turning it sharply. Impact methods must not be used.
- Once the screw reaches the bottom of the hole or the position marked on the screw, stop turning immediately, remove the installation accessory, and avoid disturbing the gel until it is completely cured. Excessive rotation can lead to glue loss and affect anchoring strength.
(The rotation time should not exceed 30 seconds, the rotation speed should be between 300 to 750 rpm, the screw propulsion speed should be about 2 cm/s and impact methods are not allowed).
(5) Expansion screw
The function of an expansion screw is similar to that of a chemical anchor and is used for anchoring applications with less stress.
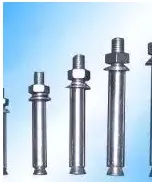
Expansion screws of different specifications
Expansion bolts should not be used on cracked parts or crack-prone parts in concrete structures.
When designing main load-bearing structures, important pipelines, high-speed operations, impact loads and large vibrations, expansion bolts should be selected based on the calculated tensile force and shear force.
4. Bolt arrangement and construction requirements
The arrangement of screws can be divided into two categories: parallel and staggered.
Parallel arrangement – this arrangement is simple, organized and compact. The size of the connection plate used is small, but results in significant weakening of the component section.
Staggered arrangement – this arrangement is not as compact, but the size of the connection plate used is larger, resulting in less weakening of the bar section.
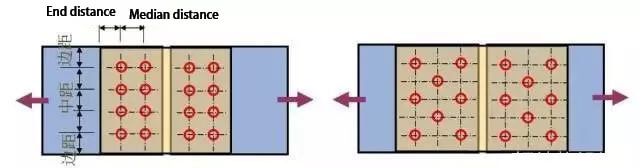
Stress Requirements
Vertical tension direction: To avoid stress concentration on the bolts and excessive weakening of the section, as well as to reduce the load capacity, the edge distance and the end distance of the bolts should not be too small.
Direction of force action: To prevent the plate from breaking or breaking, the final distance should not be too small.
For Compression Members: To avoid warping of the connecting plates, the intermediate distance should not be too large.
Building Requirements:
- The distance from the edge and the average distance of the screws should not be too large to avoid loose fittings between the plates, moisture ingress and corrosion of the steel.
- To make it easier to tighten the nut with a wrench, the screw pitch should not be less than 3 times the screw diameter.
In accordance with these requirements, the allowable bolt spacing and relevant design values are specified in the code GB50017-2017 for the design of steel structures.
Table 8.3.4 maximum and minimum distances allowed for screws or rivets
name | Position and direction | Maximum distance allowed (whichever is smaller) | Minimum distance allowed | ||||
Center spacing | Outer line (vertical or along the direction of the inner force) | 8d or 12t | 34d | ||||
Middle row | Vertical direction of internal force | 16d or 24t | |||||
Along the direction of the internal force | Member under pressure | 12d or 18t | |||||
Limb tension | 16d or 24d。 | ||||||
Along the diagonal direction | |||||||
Distance from component center to edge | Along the direction of the internal force | 4d or 8t | 2d | ||||
Vertical direction of internal force | Cutting edge or manual gas tip | 1.5d | |||||
Rolling edge, automatic gas cutting or saw edge | High strength screw | ||||||
Other screws or nails | 1.2d |
Observation:
1.d 0 is the diameter of the screw or nail hole and t is the thickness of the external sheet.
2. The maximum distance between the edge of the steel plate and the screw or rivet connected to the rigid member (such as angle iron, channel steel, etc.) can be adopted according to the value of the middle line.