Manufacturers and product designers across industries use a few important tools to connect and align various components and structures. Rivets are one of the most important tools that allow this component to be assembled. However, these types of rivets often have different design requirements, materials, applications and properties.
This article is a complete guide to the types of rivets, how they work and their various applications. We also compare riveting and welding to help you decide which method is best for your project.
What is a rivet?
A rivet is a mechanical fastener that holds sheet metal together during various manufacturing operations. It usually consists of a head and an end on opposite sides. The head is generally smooth and larger than the cylindrical body/stem, similar to a metal pen. Furthermore, they are parts machined from different materials such as brass, copper, steel and aluminum.
Additionally, rivets are different types of fasteners than regular screws and nuts. They require other installation techniques that allow parts to be permanently assembled or connected.
How does Rivet work?
Rivets are a fundamental tool for the construction of various machines and structures. The general operating principle of a rivet is that drills drill holes in the parts while you insert the rivets into the hole and deform the end. This process is relatively simple and practical.
The preformed head of a rivet is a “shop head,” while a new head, called a “shop head,” is created after the rivet is inserted into the components to be joined. The end of the rivet turns into a shop head when you deform it with a hammer. This process is called disturbance or buckling. As this happens, the end expands and holds the rivet firmly in place.
A step-by-step guide to the riveting process
To get a firmly installed rivet, here are some steps to follow:
Step 1 : You need to determine the appropriate rivet for your parts. To do this successfully, you must consider factors such as the ideal rivet material, the ideal rivet type, and the ideal rivet size.
Step 2 : The next step is to determine where to place the rivet on your parts. This helps ensure efficient connection of materials or components.
Step 3 : You need to drill a hole that is exactly 1.5mm larger than the diameter of the rivet you want to mount.
Step 4 : Insert the rivet into the hole you made in the materials you want to join.
Step 5 : When installing the rivet, the tail/shaft will come out at the opposite end of the piece where you will deform it.
Step 6 : Tapping the tail flattens the material, causing the tail to expand to about half its actual size. Most importantly, make sure the bottom of the rivet is identical to the workpieces to complete the rivet connection.
Materials used to make rivets
You can use different materials to make different types of rivets for your products. Stainless steel, aluminum, brass and copper are the main materials that help meet various product standards. However, as there is an extensive list of materials suitable for making rivets, it is important to use the correct material, with the desired mechanical properties and compatible with the parts to be joined.
Aluminum Rivets
Aluminum is a standard variety of metal used in the manufacture of rivets and fasteners. It is widely used due to its lightness and softness properties. In general, aluminum alloys offer excellent wear resistance. Most importantly, aluminum's malleability makes it easier to produce complex parts.
Stainless Steel Rivets
They are extremely robust and resistant to wear. Stainless steel rivets are commonly used in the aircraft, locomotive and power generation industries. Manufacturers often use these stainless steel rivets because of their corrosion resistance.
Steel Rivets
Steel rivets can be easily fitted or secured into your applications. The low carbon properties of certain steels make them suitable for a variety of riveting applications. Low carbon steel rivets are more flexible and adaptable than rigid high carbon steel rivets. As a result, high-carbon steel rivets require additional material and their formability decreases.
copper rivets
Copper rivets have excellent thermal and electrical conductivity. Copper is flexible in both application and appearance. It is a remarkable conductor of electricity. Therefore, copper rivets are more suitable for electrical appliances.
Brass Rivets
Brass is a flexible, low-friction material, providing excellent strength and impressive stain resistance. Furthermore, due to its properties, brass cannot produce sparks. Most importantly, these characteristics make brass rivets the most popular type in gas appliances.
7 Types of Rivets Used in Manufacturing
In general, there are different types of rivets, each specifically designed for a wide range of applications, strengths, and materials. Below are the seven most commonly used rivets in sheet metal fabrication projects.
1. Solid rivets
These are the most commonly used rivets, commonly called round rivets. They are easy to use, reliable and represent the oldest form of fastening materials. Depending on the smoothness and different size of the rivet, you can deform the end slightly using a crimping tool or hammer.
Solid rivets have a basic construction consisting of a solid shaft and a head, generally made of copper, steel or aluminum. This makes these rivets very stable and durable. Typical applications of solid rivets include the production of various thin structural parts in aircraft, electronics, marine, machinery, construction and other industries.
2. Blind rivets
A blind rivet is a tubular rivet with a head and a mandrel in the middle. You need to insert the blind rivets into an already drilled hole in the parts to be connected. Then use rivet pliers or a special tool to force the mandrel through the rivet. The compressive force between the tool and the mandrel head expands the tube diameter and locks the sheets.
Unlike solid rivets, you can only attach blind rivets to one side of the part. Blind rivets are ideal for cases where it is nearly impossible to see or access the back/blind end of a connection. Typical applications for blind rivets include shipbuilding, electronics, household applications and aerospace.
3. Insert rivets
Set rivets have a mandrel in the middle, just like blind rivets. However, drive rivets require the use of a special tool to pull the mandrel through the rivet. Only a hammer and possibly a support block are needed to insert the mandrel into the rivet body and clamp the parts.
These rivets are perfect for any application where the holes do not penetrate the entire block, plate or plate. For example, you can use impact rivets to hold panels in place or to fit nameplates into binding holes.
4. Self-piercing rivets
These rivets do not require drilling into the material before use. Self-drilling rivets can drill holes in materials using its taper bit or taper drill bit. They pierce the top layer of material and leave the bottom layer half perforated. A stamping punch causes the end of the rivet to expand and lock into the base plate, creating a flat button.
Most importantly, self-drilling rivets are preferred for heavy-duty applications and can join dissimilar materials that are almost impossible to weld, such as steel and aluminum.
5. Split rivets
Split or yoke rivets are similar to self-drilling fasteners. They are the first choice for joining soft materials such as wood, plastic and leather. Therefore, they are not ideal for critical applications but are suitable for home repair work.
Split rivets usually have a sawn or slotted body and are suitable for repairs. Therefore, the sawn bodies or split rivets of these rivets have sharp points that allow holes to be made in the materials.
6. Tubular rivets
Tubular rivets are generic tubular rivets with a head, shank and partially hollow tube. They come in a variety of configurations and usually have a head on one end and a hollow side. The hollow side passes through each piece to be connected. Manufacturers connect the field head to the hollow side using cold forming technology.
However, it is important to use low-strength, highly ductile metals for your rivets as they require extensive cold working. Therefore, tubular rivets are popular in commercial applications and electrical equipment.
7. Flush rivets
Flush rivets are also called countersunk rivets. They are best used on exterior surfaces to ensure an attractive appearance and avoid air resistance. They consist of countersunk heads and holes, making them suitable for finished metal surfaces that require minimal visibility. Due to their flush appearance, they are functional tools for aerodynamic applications.
Other Important Types of Rivets
Here are other types of rivets that manufacturers use to join different materials and components together.
Types of rivets | Characteristics | Forms |
Threaded rivet | With an internal threaded mandrel and a flattened external one on both sides that allows you to hold and rotate the tool. | Automotive, aerospace and industrial applications. |
Snap Head Rivet | Provides a solid connection with a head length of approximately 0.7 inches and a shaft diameter of 1.6 inches. | Ideal for use in the construction and manufacturing industries with high maximum strength requirements. |
Friction rivets | These are multi-part rivets consisting of a shank and a sleeve. | Aircraft construction, automotive industry, railway and traffic technology. |
Mushroom head rivets | With mushroom-shaped heads and a lower profile than normal rivets, they are used to lock parts together. | Facilitates the joining of materials of different thicknesses. |
Flat head rivets | It features a unique shape that consists of a cylindrical head that tilts from top to bottom. | Heavy structural construction due to exceptional grip and strength. |
Rivet Types Applications
Rivets are used in various industries to ensure firm fastening or connection of two or more wood or metal materials. Rivets allow the connection of parts that are typically more massive than screws of similar diameter. Below are some application areas of rivets:
Construction/Joints
Rivets are popular in construction because of their high efficiency. These are reliable fasteners that allow you to easily connect different parts of a structure or machine. You can use a rivet joint to join any wood and metal materials. These rivets allow you to connect various wooden furniture such as cabinets, cupboards and shelves.
Auto Industry
Rivets are used in a variety of ways in the automotive industry. Manufacturers in this sector use these fasteners to assemble chassis components, body panels and various other parts. They are mainly used to fix materials with different properties, such as steel and aluminum. Additionally, rivets have excellent vibration and fatigue resistance, providing impressive advantages in high-strength applications.
jewelry industry
Experienced and aspiring jewelry makers use rivets as a cold joining method in their various operations. Jewelers use rivets to efficiently create cold joints using basic metal forming skills, specialized instructional videos, and some standard tools. Many manufacturers have switched to rivets because they allow them to connect metal parts without necessarily having to use welding technology.
aerospace industry
Manufacturers in this industry often use solid, durable and reliable materials when processing various projects. Therefore, riveting is an essential technique in aircraft construction as it facilitates solid alignment and shaping of solid parts. Additionally, rivets join aluminum alloys together because they are not compatible with welding technology.
sports
Manufacturers often use rivets in the sporting goods industry. They use rivets to connect components such as skateboards, bicycle frames and ski bindings. Rivets are ideal for these applications due to their high strength and durability.
Riveting or welding: which one to choose?
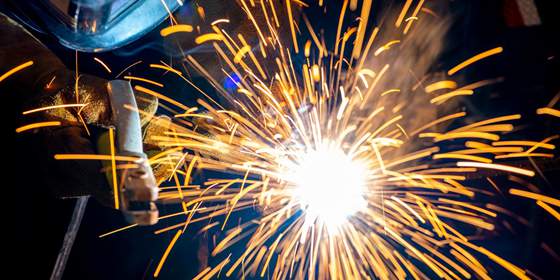
Riveting and welding are ideal joining techniques, with advantages and disadvantages. Both are suitable for a wide range of products. However, it is important to understand the differences between the two methods to determine compatible products for each technique. The table below shows a comparison of their differences.
factors | Rivets | Welding |
materials | Riveting is the best choice for connecting different materials. | Not suitable for joining materials with different properties. |
Cost | Riveting is more expensive due to operating, labor and material costs. | Welding is an economical option. |
Forms | Typical areas of application of this method include the production of consumer goods, the aircraft industry, shipbuilding and bridge construction. | Manufacturers in the defense, aerospace and electrical industries prefer welding. |
Strength | Riveting is not a suitable method for manufacturing products that require rigid structures. | Welded materials have durable and robust connections, making the process ideal for producing rigid structures. |
speed | Riveting involves several processes such as drilling holes, joining and flattening the rivets, which may take longer. | Welding is an automated technique for joining various metal parts with excellent production efficiency. |
Security | Riveting is a safer method. | Although welding is an automated process, the use of heat can pose a certain level of danger. |
Concluding
Rivets are the ideal alternative to screws, nuts, bolts and welded connections. They are more reliable and long-lasting fasteners than many other fasteners.
There are different shapes of rivets with different configurations and purposes. This may be due to the dynamic nature of mechanical engineering and structures. However, it is advisable to choose the ideal material for your rivets when choosing the type of rivet that best suits your projects.
Common questions
What type of rivet is most common?
The most commonly used type of rivet is the solid rivet. Solid rivets are adaptable, easy to install and are often used in applications with high safety and reliability requirements.
What is the normal diameter of a rivet?
The normal diameter of a rivet is 1/8 inch (3.175 mm).
Which rivet material is best for metal?
Stainless steel rivets are ideal for metal parts due to their strength and resistance to wear and corrosion. They are commonly used in rail transport, aviation and the automotive industry.
What is the most used material to make rivets?
Aluminum is the most commonly used material for fasteners like rivets. It is known for its softness and lightness. Additionally, it offers excellent corrosion resistance, making it an ideal choice for many applications.