35CrMo steel, a common material used in our company's parts, is generally quenched and tempered through oil quenching or water quenching with oil quenching. However, since the production line's multifunctional furnace has been put into use, it has been unable to complete the water quenching oil cooling process.
As a result, oil-quenched parts, particularly those with rolled bars without surface processing, have low hardness and do not meet drawing requirements. This requires secondary quenching, which negatively impacts part performance, increases production costs and results in unnecessary losses.
An analysis revealed that the low hardness is mainly due to insufficient cooling speed. Based on relevant data and production experience from other heat treatment plants, cooling 35CrMo steel bars with brine can increase the cooling rate.
As our company has not previously used water quenching in the production of 35CrMo steel bars, we need to test the water quenching and oil quenching methods and compare their mechanical properties before deciding to implement water quenching for 35CrMo steel bars.
1. Determination of the test plan
(1) Test materials
The test material is a 35CrMo steel bar produced by our company (φ 60 mm), see Table 1 for chemical composition.
Table 1 Chemical Composition of 35CrMo Steel Bar (Mass Analysis) (%)
Project | W | Yes | Mn | Cr | Mo | s | P | Ass | No |
National standard | 0.32~0.40 | 0.17~0.37 | 0.40~0.70 | 0.80~1.10 | 0.15~0.25 | ≤0.035 | ≤0.035 | ≤0.30 | ≤0.30 |
Test Materials | 0.36 | 0.26 | 0.56 | 0.99 | 0.17 | 0.03 | 0.02 | 0.1 | 0.1 |
(2) Testing instruments and equipment
The production line for multipurpose furnace testing equipment is shown in Figure 1. The electronic universal testing machine is controlled using Rockwell hardness tester and CMT8202 microcomputer.
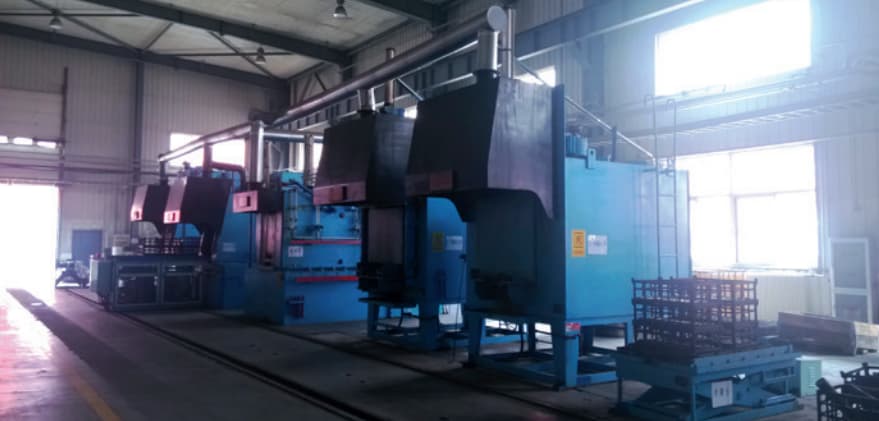
Fig. 1 Multifunctional oven production line
(3) Test method
The test consists of two parts: a comparison of the hardened layer depth between two quenching methods.
Samples from both quenching methods undergo a tensile test and the results of their tensile strength and elongation are compared.
2. Testing process and results analysis
2.1 Hardening depth
Take the φ60mm bar as a test sample and conduct quenching in oil and water.
(1) Oil quenching process
Quenching 860℃, keeping for 45min, oil cooling to 150℃;
Season at 200℃, keep for 180 minutes and cool in air to room temperature.
(2) Water quenching process
Temper at 860°C, hold for 45 minutes and then cool with water to 150°C.
Heat to 200°C, hold for 180 minutes and cool in air to room temperature.
No tempering cracks are observed on the surface of the treated sample.
Measure the hardness of the machined surface every 2.5mm from surface to center, as shown in Figure 2.
The hardness results are presented in Table 2.
Table 2 shows that the hardness after water quenching is high and the hardened layer is deep.
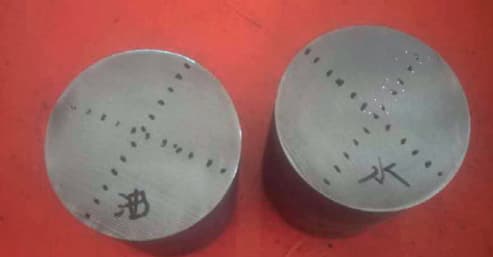
Fig. 2 Hardness test of the hardened layer
Table 2 Hardness of the Hardened Layer
Distance to surface/mm | 0 | 2.5 | 5 | 7.5 | 10 | 12.5 | 15 | 17.5 | 20 | 22.5 | 25 | 30 |
Water quenching hardness HRC | 53 | 52 | 50 | 46 | 40 | 37.5 | 35 | 33 | 32 | 30 | 28 | 25.5 |
HRC Oil Quench Hardness | 33 | 32 | 31 | 30.5 | 30 | 28 | 27.5 | 26 | 24 | 23 | 23 | 22.5 |
2.2 Comparison of mechanical properties
35CrMo steel bars can be subjected to oil and water quenching, and the hardness can be adjusted to reach 28-30HRC by adjusting the tempering temperature.
(1) Oil quenching process
Quenching 860℃, keeping for 45min, oil cooling to 150℃;
Season at 520℃, keep for 90 minutes and cool in air to room temperature. The process curve is shown in Fig.
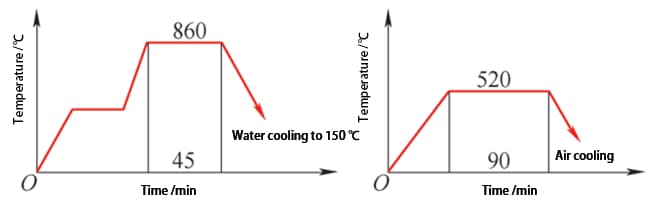
Fig. 3 Oil quenching process curve
(2) Water quenching process
Quenching 860℃, holding for 45min, water cooling to 150℃;
Season at 580℃, keep for 90 minutes and cool to room temperature. The process curve is shown in Fig.
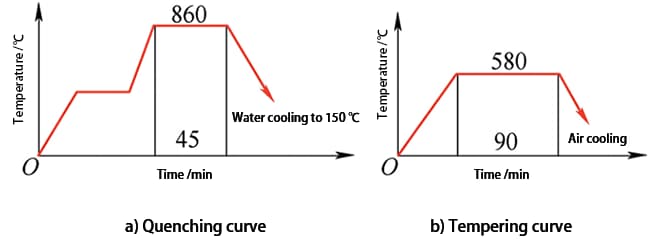
Fig. 4 Water quenching process curve
The test bar is processed into a tensile specimen for tensile testing, and the results are shown in Table 3.
It can be seen from Table 3 that the strength after water quenching is relatively high and the toughness is relatively low, with little overall difference.
Table 3 Mechanical Properties
Quenching Cooling Medium | Tensile strength/MPa | Stretching (%) |
brine | 880 | 14 |
oil | 814 | 19 |
2.3 Analysis of results
Based on the test results, it can be deduced that although the tensile strength has improved significantly, the elongation has decreased with the same surface hardness. This is due to the rapid cooling speed of water quenching, which results in a deeply hardened layer and high hardness.
This solution addresses the problem of insufficient hardness in 35CrMo steel bars after oil quenching.
3. Benefits analysis
Changing some 35CrMo steel parts to a water quenching process can not only meet production requirements and reduce the rework rate, but also save costs. Electricity savings equal the electricity cost for rework plus the electricity cost saved by the existing process. The calculation is as follows: Electricity savings = (209 × 1.5 + 78 × 3) × 120 (approximately 120 heats of 35CrMo steel production per year) × 10% × 1.2 + 91 (washer power) × 0.5 × 120 × 1.2 yuan = 14,436 yuan.
Labor cost saved = (time saved + rework time) × number of operators × annual production furnace × man-hour unit price=(0.5+4.5×10%)×2×120×8.571 yuan = 1954yuan.
Material cost saved = (quenching oil loss per furnace + cleaning fluid loss) × annual production heats = (50 + 20) × 120 yuan = 8,400 yuan.
The annual total is about 24,790 yuan.
4. Conclusion
35CrMo steel bars can be quenched with water instead of oil.
The hardness not only meets the requirements, but also has little impact on the comprehensive mechanical properties.
Related reading: Chart of mechanical properties of metals
In addition to these benefits, the rework rate has significantly decreased, leading to improved labor efficiency and reduced production costs. Furthermore, the use of a lower quenching temperature and the elimination of oil fumes generated in the quenching process from cooling the material's oil result in greater economic benefits, as well as energy savings and reduced emissions.