With the development and progress of the manufacturing industry, nuts as fasteners are widely used in mechanical engineering, aerospace, automobile, railway and other areas. Most traditional walnut manufacturing processes use machining, but this processing method has several problems, such as: B. low precision, high cost and low production efficiency. With the continuous progress of science and technology, nut forging technology has emerged and its advantages such as high precision, high strength, high productivity, etc. are widely recognized.
1. The background of forged nut technology
Nut forging technology is a combination of forging and molding technology, a new nut manufacturing process that achieves mold shape and internal opening accuracy in a single molding process to meet tolerance requirements. Drop forging is the process of forming a metallic material by deforming it under tension at a constant temperature. Molding is the process of plastic deformation and shrinkage of metallic materials under conditions of high temperature and high pressure through molding to form the desired shape. Therefore, nut forging technology will effectively integrate the metal forging and molding process, so that nut manufacturing cost, production efficiency and product quality are greatly improved.
2. The advantages of forged nut technology
- 1) High precision: By using drop forging technology, the tolerance requirements in shaping and opening the internal cavity in a molding process can be met accurately. This avoids processing errors caused by multiple processing, ensures product accuracy and reduces production costs.
- 2) High strength: The combination of forging and molding can achieve high cold plasticity and improve the strength and durability of walnut products to ensure product quality and performance.
- 3) Saving raw materials: In the traditional machining process, parts generally use more metal material due to burr, taper and other problems. Nut forging technology can effectively avoid this situation while reducing material waste, thereby saving raw materials.
- 4) High production efficiency: Forged nut technology's high degree of automation and higher production efficiency can effectively reduce labor costs and ensure defect-free functionality and quality.
3. The manufacturing process of forged nuts
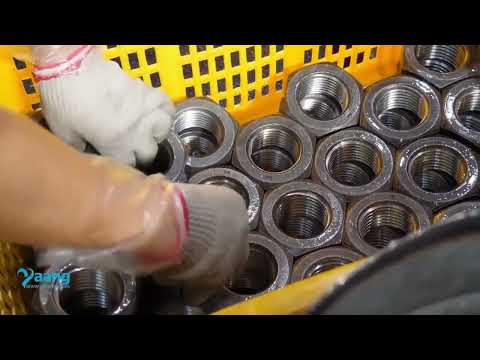
Drop forging involves heating metallic material until it becomes plastic and then forming it into the desired shape under pressure. Below are the general steps of the forged nut manufacturing process:
- Raw material preparation: Selection of suitable metal material, generally carbon steel, stainless steel or alloy steel. Raw materials must comply with relevant standards and specifications.
- Raw material heating: The raw material is heated to the suitable forging temperature. This temperature depends on the type of metal and the required mechanical properties.
- Billet Forging: The heated metal billet is placed in a forging die and pressurized by forging machines to shape the billet into the desired nut shape. Forging can be divided into two phases: rough forging and finishing forging to ensure that the required size and shape are achieved.
- Cooling: After forging, the nut must be cooled at a suitable rate to stabilize the crystalline structure of the metal and ensure the required mechanical properties.
- Cutting and Shaping: After cooling, the nut may have some irregularities or oversized shapes that need to go through the cutting and shaping steps to meet exact dimensional and finishing requirements.
- Heat treatment: To improve the hardness and strength of walnut, heat treatment such as quenching and tempering is generally carried out.
- Inspection and Quality Control: Various tests are carried out on the nuts produced to ensure that they meet specifications. This may include visual inspections, dimensional measurements, hardness testing, etc.
- Surface treatment: Depending on requirements, the surface of the nut may be coated or subjected to other special treatments to improve its corrosion resistance or appearance.
- Packaging and delivery: After all manufacturing and testing steps are completed, the nuts are packaged and ready for delivery to the customer.
Please note that different types and specifications of nuts may require different manufacturing processes. The steps above are for general guidance only.
4. Application of forged nuts
The patented forged nut technology is widely used in the market. Below are some introductions, mainly from the following aspects:
1) Automotive industry
Forged nuts are mainly used in the automotive industry, especially for high-end vehicles such as Mercedes-Benz, BMW, etc. Forged wheel nuts can improve the fit between the wheel hub and the wheel, reduce vibration and noise, and thus further improve the performance of the entire vehicle.
2) Aerospace
Forged nut technology is also widely used in the aerospace industry, such as aircraft fuselage connection bolts, accessory bolts, engine connection bolts, etc. Due to the high hardness and strength of products made from forged nuts, they have better fatigue resistance and durability and can meet the extreme requirements, meet the performance of nuts that bring high strength, high load and high-speed flights.
3) Power plant industry
Forged nuts are generally used to connect various mechanical power equipment such as seats, heads, bases and other fixed parts such as steam turbines, engines and other power equipment. Nuts are often forged.
4) Heavy engineering
Many fixed parts such as high-speed locomotives, train wheel connecting bolts, large machinery and equipment connecting bolts, bridge connecting bolts, tower crane positioning bolts and others use forged nuts to meet the requirements of nuts for fatigue resistance, high strength, durability and other requirements.
5. The development trend of forged nut technology
Although significant results have already been achieved, forged nut technology still faces some challenges and requirements. On the one hand, with the continuous development of society and technology, modern industry's demands for higher quality, more accurate and more stable dried fruit products are increasing day by day. Suppose you want to master the technology of forged nuts with greater precision and greater strength. In this case, it is necessary to constantly optimize the technological process and constantly improve capabilities and production levels. On the other hand, the technical transformation and market promotion of forged nut technology still needs to be strengthened and improved, including how to improve the technical content of patented technology and market competitiveness, improve the production process, and continuously reduce production costs. production.
The technology for forged nuts in the area of machining and shaping is promising, but the potential for future development is still enormous. As a potential field in manufacturing industry, forged walnut technology will assume greater economic and social responsibility in the future and play an important role in realizing industrial modernization, innovation and development, and improving national technology.
In short, nut forging technology has a wide range of applications in various industries, and the product is widely recognized in the market. Through continuous improvement and application of technology, the nut forging manufacturing process is developed and the product performance and application areas are further expanded.