1. Introduction
Remote laser welding (RLW) technology, a non-contact robotic laser welding process, has seen significant advances in recent years. This has led to greater production efficiency and greater processing flexibility in the laser welding process.
The concept of RLW was first introduced in 1996 by John Macken.
One of the main features of RLW is the perfect combination of a high-power, high-beam-quality laser source with a long focal length (up to 1600 mm) and a galvanometer scanning device.
Compared to traditional laser welding, RLW offers faster speed, shorter cycles and greater flexibility.
RLW technology research has been applied to various types of lasers for a long time. The high-power fiber laser with a wavelength of 1080 nm is capable of transmitting the laser beam through the fiber and improving the focusing accuracy and processing flexibility.
On the other hand, the CO2 laser with a long wavelength of 10.6 μm cannot transmit the beam through the optical fiber.
Due to its ideal wavelength and excellent beam quality, the high-power fiber laser is the preferred choice for RLW applications, outperforming traditional CO2 lasers and Nd:YAG lasers.
The working principle of RLW is to reflect and direct the laser beam through the galvanometer sweep, allowing high-speed transmission to the surface of the part.
2D scanning is the most commonly used in the RLW field. It consists of a galvanometer system with two light-scanning mirrors that can be electrically rotated. The system can support an output power of 5 kW, making it more cost-effective than 3D scanning.
However, RLW also faces several challenges, such as the need for pre-processing, welding quality and stability requirements, the supply of shielding gas, and the proper fixing and positioning of the galvanized sheet.
Compared to traditional laser welding, RLW requires a greater number of process parameters, which can be broadly categorized into three groups: beam quality, processing parameters and material properties.
2. Remote laser welding process
2.1. Process principle
The idea behind Remote Laser Welding (RLW) is not entirely new. Its main principle involves reflecting and positioning the focused laser beam at a specific distance above the workpiece using a scanner. The typical focal length for RLW ranges between 1000 and 1600 mm.
In 1996, John Macken performed the first RLW experiment using a laser with a focal length of 1600 mm. This experiment was a milestone in the development of the RLW process, as it achieved welding with a small hole pattern.
The scanner helps to correctly project the laser beam onto a large part, with an area of 1 mx 1 m or even larger, and the welding speed can reach 30 m/min.
There are two general working modes for the RLW process: the RLW system with an integrated scanner and the robot-based RLW system.
The RLW system with integrated scanner uses a scanning unit, typically a 2D scanner, to focus and position the laser beam (see Figure 1 (a)).
The robot-based RLW system uses a long-focus laser optical mirror and a six-axis robot for operation. The robot is responsible for positioning the laser beam on the surface of the part (see Figure 1 (b)).
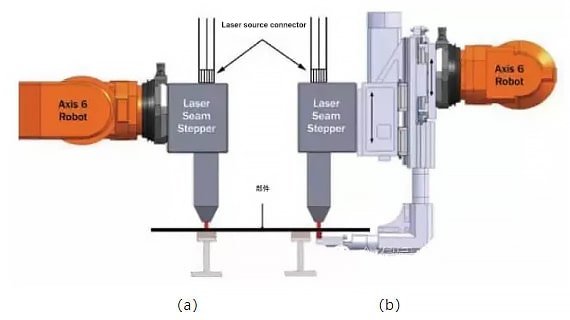
Figure 4. RLW unit with 5 kW fiber laser
2.3. Typical characteristics of RLW
Compared to the traditional laser welding process, the RLW system with integrated scanner has several advantages, such as:
- High flexibility, short processing cycle, fast production speed, good welding results, uniform and stable performance, high automation, reduced material requirements and low maintenance needs, leading to lower production costs.
- Low heat input helps minimize thermal deformation.
- The system has a compact design and takes up little space.
2.3.1. Efficient production
The RLW system with integrated scanner is more efficient due to its fast welding speed and short processing cycle.
Under normal conditions, the welding speed can be increased from 6 m/min to 30 m/min, depending on the configured laser output power.
Eliminating scanner downtime can further reduce the processing cycle by 80%.
The uninterrupted movement and rapid positioning of the scanning head allows the RLW system to move between welds in just 50 ms, while robot positioning typically takes 2 to 3 seconds.
As a result, the processing cycle of the RLW system with an integrated scanner is 6 to 10 times faster than resistance spot or arc welding.
2.3.2. Highly flexible
The long-distance operation between the scanning head and the workpiece in the RLW system provides great flexibility during welding, which is not possible with traditional laser welding equipment.
As shown in Figure 5, welding can only be completed with long-distance operation.
Another benefit of long-distance operation is that it prevents metal fumes or spatter from affecting optical components.
Additionally, long-distance operations require fewer accessories, effectively reducing equipment costs in applications involving heavy or large products.
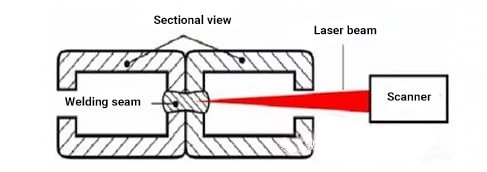
Figure 5. RLW is used to weld parts with poor accessibility
2.3.3. Cost advantage
RLW has already demonstrated its cost-effectiveness in BIW production. Numerous research results show that the RLW system can reduce production costs in several ways, such as:
- Reduction of unit production costs through mass production.
- Improve efficiency and reduce equipment costs by reducing the number of laser welding guns.
- Reducing material consumption costs by shortening the overlapping width of welds.
- Extending the useful life of equipment and reducing maintenance costs.
However, RLW also has its disadvantages, such as the need for shielding gas, high-quality beams, fixtures, and weld tracking.
RLW's biggest challenge is providing shielding gas to the part. The auxiliary gas must cover the entire processing area, rather than moving synchronously with the weld. This requires a large number of nozzles to inject shielding gas at a high flow rate simultaneously to prevent oxidation and contamination. As a result, a large amount of shielding gas is required, which increases the cost of the process.
2.4. Application of RLW
Currently, laser resistance welding (RLW) is mainly used for mass production of flat panel assemblies, which generally involves a substantial amount of welding.
The automotive industry is a key application area for RLW.
To date, approximately 70 RLW systems have been implemented in various production processes, including manufacturing automobile seats (such as seats, frames, rails and panels), body-in-white components (such as luggage compartments, rear panels, doors/ suspension parts, sidewalls and heat exchangers) and internal structures (such as reinforcing ribs and upper rear window shelves/protectors).
3. RLW process parameters
Researchers have carried out various tests and studies on various process parameters such as welding speed, focus position, beam tilt, shielding gas, joint design and base metal properties in order to improve the beam characteristics of RLW. These characteristics include laser power, beam quality, wavelength, spot diameter, focal length, mode, and polarization.
The researchers studied RLW equipped with fiber lasers using four different types of steel as base materials, including carbon steel, galvanized steel, galvanized alloy steel and stainless steel.
The main process parameters are presented in Table 2 below.
Table 2. List of fiber laser RLW process parameters
Basic Materials | Output power | Focal length | Spot diameter. | Welding speed | Focus position | Time |
---|---|---|---|---|---|---|
(Thickness mm) | K.W. | mm | μm | m/min | mm | (ref.) |
Mild steel S355 (1.5mm) | (mm) 8 | 470 | 640 | 2-14 | 0 | 2008(6) |
S235 Mild Steel | (mm) 8 | 1053 | 300-800 | 2-22 | -80-80 | 2007(15) |
Galvanized steel JAC270EN (1.5mm) | 4 | 1250 | 360 | 5 | 0 | 2009(35) |
Galvanized Alloy Steel GA60 (1mm) | 4 | 1500 | / | 4 | 0 | 2009(8) |
Stainless steel 1.4301 (20mm) | (SM) 3 | 500 | 109 | 4-10 | 0 | 2009(36) |
Furthermore, the researchers also extensively examined various process parameters, including output power, welding speed, shielding gas supply, beam tilt, and focus position.
3.1. Laser power
In the laser processing process, increasing laser power results in a corresponding increase in welding speed.
According to the data, when welding carbon steel with remote laser welding, if the output power of the fiber laser is increased from 4 kW to 8 kW while the spot diameter remains constant, the welding speed will increase significantly. However, with the increase in laser power, problems such as spatter and sagging in the welds may arise, which can negatively impact the quality of the weld.
Figure 7 shows the relationship between laser power and welding speed and penetration depth when welding S355 carbon steel using remote laser welding.
As the graph indicates, an increase in laser power leads to an increase in welding speed and penetration depth.
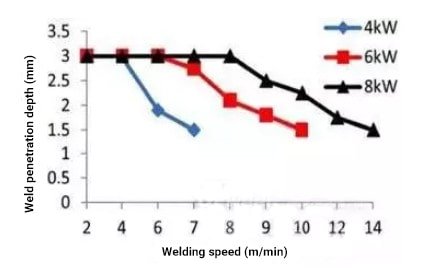
Figure 7. The influence of output power on RLW (with exhaust device, without shielding gas, spot diameter 640 mm, focal length 470 mm, mild steel S335)
3.2. Welding speed
Welding speed is a critical factor in the resistance laser welding (RLW) process.
Welding speed is mainly determined by power density, required penetration depth, laser mode, focus position and number of scans.
Welding speed influences the appearance of the weld pool, the shape of the weld joint and the depth of penetration.
Figure 8 illustrates the relationship between welding speed and welding depth when remote laser welding is performed on 1.4301 stainless steel with different laser powers.
As shown in Figure 8, higher welding speeds result in shallower welding depths, and higher laser power results in deeper welding depths.
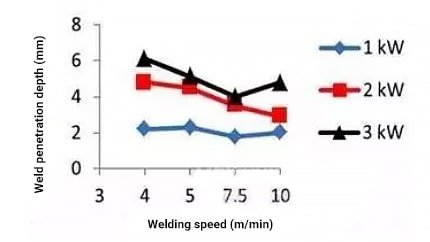
Figure 8. Influence of welding speed on RLW welding depth
(Stainless steel 1.4301, 3 types of output power, focal length 500mm)
3.3. Shielding gas
The use of shielding gas during remote laser welding offers several benefits, including preventing oxidation of the welding area, reducing metal vapor, removing metal particles from the beam path, stabilizing the welding process, and preventing the formation of plasma.
When performing RLW on steel, the most commonly used shielding gases are argon, helium, nitrogen and compressed air.
The typical flow rate of RLW shielding gas is about 15 to 20 liters per minute, which varies depending on the length of the welding area.
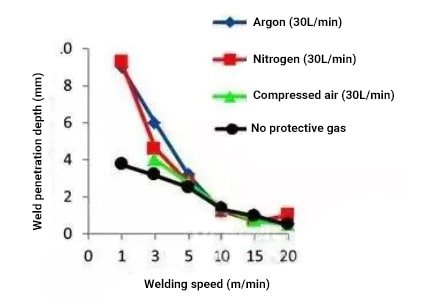
Figure 9. Influence of shielding gas on RLW welding depth and speed
(Steel plate, 8 kW output power)
When performing remote high-power fiber laser welding, the impact of shielding gas on welding depth and speed can be seen in Figure 8.
Regardless of whether shielding gas is used, as welding speed increases, penetration depth will continue to decrease.
However, at welding speeds less than 5 meters per minute, the use of shielding gas becomes a significant factor affecting the welding process. This probably occurs because the large amount of metallic vapor generated in the small holes obstructs the welding process.
When the welding speed increased to 14 meters per minute, the effect of shielding gas on RLW welding depth began to become more pronounced.
3.4. Beam tilt
Due to the long working distance, the acceptable range of inclination angles for laser resistance welding (RLW) is extensive.
The size and shape of the spot produced by the laser beam on the surface of the part will vary with changes in the tilt angle.
As power density and absorption change, the beam angle will impact penetration depth and interface width.
When the inclination angle exceeds 60°, it significantly affects the penetration depth. On the other hand, little difference in the welding process is observed when the inclination angle is between 20° and 30°.
According to the data, when the inclination angle is between 0° and 20°, it has no impact on the welding quality.
3.5. Focus position
The position of the focus influences the depth of penetration, the shape of the welded joint and the quality of the cut.
The focal position of the laser beam varies with the thickness of the base material.
To achieve the best penetration effect, the focal position is typically placed about 1 millimeter above the surface of the workpiece.
Figure 10 illustrates the relationship between focal position and penetration depth when a laser disc is used for remote laser welding of steel.
As shown in Figure 10, when the focal position is at 0 millimeters on the part surface, the penetration depth is deeper.
As the distance of the focused laser beam increases, the penetration depth decreases.
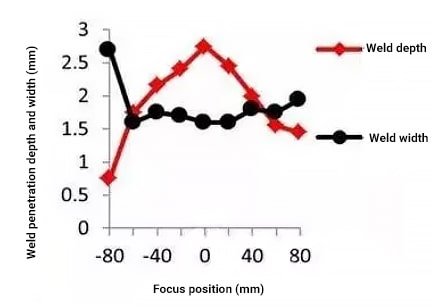
Figure 10. The effect of focus position on the depth and width of RLW welding
4 . Conclusion
The purpose of this article is to investigate the process of remote laser welding using fiber lasers.
The remote fiber laser welding process has great potential for a wide range of applications.
Due to its high productivity, excellent flexibility and low overall cost, the process has been adopted in the automobile industry.
For the fiber laser welding remote unit, the scanner is the most critical component.
However, to obtain good welding results, users must also consider a series of process parameters, such as beam quality, laser power, welding speed, shielding gas supply, focus position and others, during welding. laser remote.