The main stages of argon arc welding cannot be ignored:

1. Impressive bow
There are three arc methods for argon arc welding: scratch arc, lifting arc and high frequency arc.
Scratch and attack bow
Arc scratching and etching refers to the scratching and etching between the tungsten electrode and the workpiece.
At the same time, the short-circuit current will heat the tungsten electrode and the arc can be ignited by lifting the welding gun.
This arc striking method has the advantages of simple control and convenient operation. Its disadvantage is that it is easy to set tungsten and pollute the workpiece.
Striking arch lift
Raise the arc start, that is, short-circuit the tungsten electrode and the workpiece first during the arc start, and the short-circuit current will be controlled to be very small.
Heat the tungsten electrode. When the tungsten electrode is withdrawn from the workpiece, the current is switched to the arc impact current in a very short time to ignite the arc.
The utility model has the advantages of avoiding high-frequency interference and reducing the tungsten pollution of the workpiece.
High Frequency Arc
High-frequency arc ignition uses high-frequency and high-voltage generator to generate high voltage between the tungsten electrode and the workpiece, burst air discharge and arc ignition.
Most of the arc striking methods we use are breaking type i.e. holding the welding torch perpendicular to the work piece, keeping the tungsten electrode at a distance of 3-5min from the work piece, connecting the power supply and discharging into the rupture gap under the action of high voltage, high frequency or high voltage pulse, ionizing the shielding gas to form ion flow and ignite the arc.
This method ensures that the extreme part of the tungsten is intact, the burning loss is small and the arc quality is good, so it is widely used.
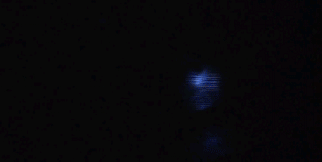
2. Molten Puddle Control
Ultimately, controlling the shape and size of the molten pool is controlling the welding temperature: temperature has a great impact on welding quality, and various welding defects are caused by inappropriate temperature.
Thermal crack, undercut, crater crack, depression, element burning loss, collision, etc. are all caused by too high a temperature;
Cold cracks, air holes, slag inclusion, incomplete penetration and incomplete fusion are all caused by insufficient welding temperature.
3. Arc operation
There are certain requirements and rules for arc operation: the angle included between the torch axis and the welded surface is called torch tilt, which directly affects the heat input, shielding effect and operation field of view.
Generally, the shielding effect is better when the torch tilt is 70°-85°and 90°.
However, the protective air flow ejected from the welding torch deviates backwards with the increase of the welding torch moving speed, which may cause the molten pool to not be fully protected, so that the welding speed welding cannot be too fast.
GTAW generally adopts the left-hand welding method.

4. Torch holding method
Hold the torch handle with the thumb and forefinger of your right hand, and the other three fingers touch the workpiece for guidance.
1. Handle
Lightly press the welding nozzle onto the weld and shake the arm a lot to weld.
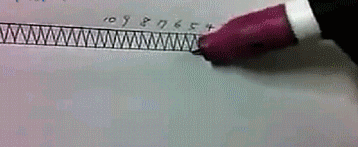
Advantage:
Because the welding nozzle is pressed into the weld and the welding handle is very stable in the process of operation, the weld has good protection, good quality, beautiful appearance and high product qualification rate.
In particular, overhead welding is very convenient. When welding stainless steel you can get a very nice looking color.
Disadvantages:
It's difficult to learn. As the arm oscillates a lot, it is impossible to weld around obstacles.
2. Mop:
The welding nozzle rests smoothly or not on the weld, the little or ring finger of the right hand also rests on the workpiece or not, the arm swing is small, and welding is performed by dragging the welding handle.
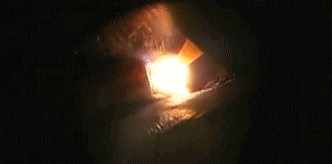
The advantage:
Easy to learn and adaptable.
Disadvantages:
The forming and quality are not good, especially overhead welding is not easy to weld, so it is difficult to obtain the ideal color and forming when welding stainless steel.
5. Welding wire fixing method
Hold the welding wire with the middle finger of your left hand at the top and the ring finger at the bottom.
Pinch the welding wire with your thumb and forefinger and move it into the molten pool. Then loosen your thumb and forefinger and move forward and tighten the welding wire.
This way, the entire welding wire can be transported without stopping.
The welding wire feeding angle and feeding mode are related to the proficiency, which directly affects the weld geometry.
The welding wire should be fed at a low angle, generally 10° – 15°, generally no more than 20°.
This helps to cover the fusion end with shielding gas and prevent collision with the tungsten electrode, so as to shorten the distance from the welding wire to the drop-shaped weld pool.
The wire feeding action should be light and not agitate the gas protective layer to prevent air from entering.
When the welding wire enters the molten pool, it must avoid short circuit in contact with the tungsten electrode to prevent the tungsten electrode from burning and falling into the molten pool, resulting in the inclusion of tungsten in the weld.
The end of the welding wire must not extend into the arc column, i.e. between the weld pool and the tungsten electrode.
Otherwise, under the action of the high temperature of the arc column, the welding wire will melt violently and drip into the weld pool, causing splashing and banging sounds, thus damaging the stable combustion of the arc, resulting in internal pollution of the weld pool and poor appearance of the weld, grayish black and not very shiny.
The melting of the welding wire in the weld pool can be divided into five stages:
A) The welding torch is perpendicular to the workpiece and ignites the arc to form a weld pool. When the molten pool is heated by the arc to become white and bright and flowing, it is necessary to prepare the welding wire feed.
B) The torch moves back slightly and tilts 10° – 15°.
C) Pry the inner edge of the weld pool and feed the end of the welding wire into about 1/3 of the weld pool.
Contact and dissolve the welding wire by the heat of the weld pool. Do not stir the molten pool as in gas welding (BC at the same time).
D) Pull the welding wire back, but its end does not leave the protection zone and remains separated from the front edge of the weld pool, ready to add the welding wire again.
E) The welding torch advances to the front of the weld pool to form a new weld pool.
(Repeat CDE until welding is completed)
6. Wire Feed
Yarn feeding can be divided into external yarn filling methods, internal yarn filling and yarn following methods,
1. External Yarn Filling:
Can be used for support and filling. A large current is used.
The head of the welding wire is in front of the groove.
The welding wire is compressed with the left hand and continuously sent to the molten pool for welding.
Groove clearance should be little or no clearance.
Advantage:
Because the current is large and the gap is small, the production efficiency is high and the operating skills are easy to master.
Disadvantages:
When it is used for reinforcement, as the operator cannot see the blunt edge melting and back reinforcement, it is easy to produce incomplete fusion and cannot obtain the ideal back formation.
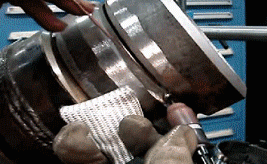
2. Inner filling wire
The inner filler wire can only be used for backing welding.
Use your left thumb, index finger or middle finger to cooperate with the wire feeding action, and clamp the welding wire with your little finger and ring finger to control the direction.
The welding wire is close to the blunt edge on the inner side of the groove and melted together with the blunt edge for welding.
The gap of the groove must be greater than the diameter of the welding wire. If it is a plate, the welding wire can be bent into an arc.
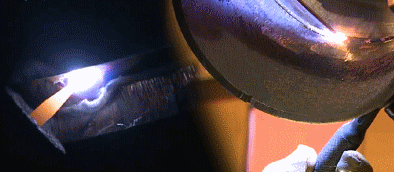
Advantage:
Because the welding wire is on the reverse side of the groove, the blunt edge and melting of the welding wire can be seen clearly, and the reinforcement on the reverse side can also be seen by the residual light of the eyes, so the welding melting is good;
Back bracing and lack of fusion can be well controlled.
Disadvantages:
The operation is difficult and the welder needs to have more qualified operational skills;
Because the gap is large, the welding amount increases accordingly, the gap is large, the current is low, and the working efficiency is slower than that of the outer filling of the wire.
7. Bow stop
Arc stopping consists of stopping midway for some reason and then continuing to weld.
The correct arc stopping method is to use the arc stopping method after casting to accelerate the arc running speed (reducing the weld pool area), so that there can be no arc crater and shrinkage cavity, the which creates conditions for the next arc to strike and continuous welding.
The accelerated arc length is about 20 mm.
During back arc welding, after the molten pool forms, press 1-2 dimples, add no or less welding wire at the starting point of the joint, and then return to normal welding.
To avoid pores and ensure weld quality, the welding speed at the starting point or joint should be slowed down appropriately.
8. Bow stop

Arc quenching, also known as arc quenching, is a necessary method for welding termination. Bow stopping is very important and should receive close attention.
If the arc is not stopped correctly, it is easy to cause cracks, shrinkage cavities and other defects
Common arc stopping methods include:
A) The welding current attenuation method uses the attenuation device to gradually reduce the welding current, so as to gradually reduce the molten pool, so that the base metal cannot melt, so as to achieve the purpose of not there is a contraction cavity at the arc stop.
Common GTAW welding machines are equipped with an attenuation device.
B) Method of increasing welding speed At the end of welding, the advancing speed of the welding torch is gradually accelerated and the feeding amount of welding wire is gradually reduced until the base metal does not melt.
The basic point is to gradually reduce the heat input and overlap the weld by 20-30mm.
This method is best suited for circumferential seams without craters and shrinkage cavities.
C) When the multiple arc extinguishing method is terminated, the welding speed decreases, the caster angle of the welding torch increases, and the arc is lengthened to make it hot.
It is mainly concentrated in the welding wire, and the feeding amount of the welding wire is increased, the arc well is filled, and the welding is increased.
After the arc is extinguished, the arc is ignited immediately, repeated two or three times, so that the welding wire can continue to be supplied to the weld pool during solidification, so as to gradually cool the arc stop.
However, after multiple arc extinguishing, the arc closing position is generally high, and the weld rise in the arc closing position needs to be leveled.
D) Arc extinguishing plate is commonly used in flat plate joints by arc extinguishing plate method.
The arc extinguishing plate must be removed and leveled after welding.
Practical test:
The current attenuation method is the best way to stop the arc with attenuation device, and the welding speed increasing method is the best way to stop the arc without attenuation device, which can avoid cratering and arc shrinkage .
The welding torch cannot be removed immediately after the arc has extinguished.
It should remain at the arc stopping location for 2 to 5 minutes, and the arc stopping part under high temperature should be protected from oxidation with delayed gas.