TIG and MIG welding are two common arc welding processes in sheet metal processing. Both produce the highest quality welded connections and connect different materials efficiently. However, they have unique processes, advantages and disadvantages, which means they have different areas of application.
The choice between the two sheet metal welding processes should only be made after a thorough comparison between MIG and TIG welding. Therefore, this article will make a comprehensive comparison between MIG and TIG, showing the differences between the processes, their advantages and disadvantages, and their applications so that you can choose the right method.
What are the differences between MIG and TIG welding?
To choose the best of the two methods, you need to know the differences. Knowing the differences between MIG and TIG welding, you can easily make a comparison between TIG and MIG using the parameters highlighted below.
1. Power source
An important parameter when comparing MIG and TIG is the energy source used by both welding processes.
TIG welding uses alternating or direct current sources depending on the type of metal and the type of arc desired. The AC power source used in TIG welding is best suited for aluminum due to its cleaning effect (i.e. it removes oxide from the metal surface). On the other hand, the direct current source is suitable for generating strong arcs.
MIG welding uses only a DC power source.
2. Material compatibility and thickness
Material compatibility is not a valid comparison parameter for MIG and TIG welding when it comes to power source, as there is little difference between the two processes.
Both welding processes are compatible with the same materials, such as aluminum, carbon steel and stainless steel. However, you can consider the thickness of the material to choose between the two methods.
TIG welding is best suited for working with thick metals because it offers better process control and there is less risk of destroying the part.
3. Type of electrode used
MIG welding uses consumable electrodes, while TIG welding uses non-consumable electrodes.
Electrodes are used to generate electrical arcs, as filler material or for electrical conduction. Due to the difference between the two processes in terms of electrode usage, this is an important parameter when comparing MIG and TIG welding.
Two types of electrodes are used in arc welding: consumable electrodes and non-consumable electrodes. Both electrodes generate arcs. However, consumable electrodes are used as filler material during welding.
Examples of consumable electrodes include carbon steel and nickel steel, while non-consumable electrodes include copper-clad carbon, graphite, and tungsten.
4. Type of shielding gases
Shielding gases are responsible for protecting the weld pool and the part against atmospheric contaminants during welding. MIG welding uses CO2 (most common), helium, argon and oxygen as shielding gases.
In TIG welding, however, argon is used as a shielding gas. In some cases, a combination of helium/argon (for welding high nickel materials), argon/nitrogen (stainless steel), and argon/hydrogen (stainless steel) may be used.
5. Welding torch cooling system
A welding torch produces a lot of heat and needs to be cooled with the right coolant. Two common refrigerants used in welding are water and gas.
On the one hand, air cooling is lightweight and cheap, but less effective at very high temperatures. On the other hand, water cooling utilizes water better than air.
Because TIG welding generates more heat than MIG welding, water-cooled welding torches are used. However, you can also use air-cooled welding torches for both processes.
6. Quality of welded parts
The quality of the welding surface is another crucial factor that makes the comparison between MIG and TIG clear. TIG welding is of better quality because it produces a clean, beautiful surface finish along the weld line. Therefore, it is the best product method that requires high aesthetic appearance.
7. Productivity
MIG welding is faster than TIG welding because TIG welding requires a higher level of detail and uses filler metals.
8. Costs
TIG welding is more expensive due to the cost of the components and the higher quality and detail of the weld. It also requires more time, which increases the energy required and the cost of electricity.
Different components for TIG and MIG welding
The main difference between MIG and TIG welding is in their components. The different components of both processes are listed below.
1. TIG welding components
Here are the main components of TIG welding that you should know:
1.1 Performance
The power source can be alternating or direct current. An AC power supply is suitable for working with aluminum due to its inherent cleaning properties. A DC source produces a stronger arc, but is only suitable for working with a clean surface for the gas shield to work.
1.2 Flashlight
TIG torches are available in various designs. Common models have an on/off button and a control on the handle. Some use a foot pedal to control these commands. Due to the high heat generated during the process, they are mainly water cooled.
1.3 Pedal
This is responsible for controlling the amount of electricity that enters the burner. As you press the pedal, the amount of current entering the torch increases and the arc becomes hotter. This speeds up the welding process. However, be careful with the extra heat and speed.
1.4 Electrode and gas protection
The tip of the electrode is responsible for the shape of the arc, while the gas (usually argon) emitted by the nozzle protects the arc and the weld pool. The nozzle requires a gas lens for gas flow. They come in different sizes, which determines the gas coverage.
1.5 Filling material
The size of the welding wire should depend on the thickness of the part. Furthermore, the material must match the workpiece.
1.6 Support straps
They are made of copper or aluminum and are attached to the back of the welding. Here they distribute heat to cool the welding area. You can also use water-cooled support rods (where cold water is circulated through the rod).
2. MIG welding component
MIG welding uses different equipment to achieve the same goals. Below are the important components used in the procedure.
2.1 Power source
MIG welding requires a DC power source due to the high heat of the process. This is why many MIG welding enthusiasts also talk about a constant voltage power supply.
2.2 Wire
The wire feeding system must be smooth for better welding quality. There are two main types of MIG welding wires: cored wire and solid MIG wire. Cored wire is a metal that contains a flux compound that forms a gas that protects the arc and the weld pool. This type of wire does not require shielding gas. In contrast, MIG solid wire does not contain flux and requires a shielding gas.
2.3 Electrode
The electrodes used in MIG welding are consumables, that is, they are used in the welding process. They come in different shapes and sizes. The most common sizes are 0.023, 0.030, 0.035 and 0.045. Of these four sizes, 0.035 is the most common.
2.4 Flashlight
This component protects the arc and transmits current to the wire. They can be water or air cooled. When choosing a MIG welding torch, consider weight, ease of use, suction, neck configuration, and cord length.
2.5 Protection against gases
MIG welding uses CO2 or argon as shielding gases. They are responsible for protecting the arc and weld pool from atmospheric contaminants.
TIG welding: principle, advantages and disadvantages and applications
If you are new to the process, you can better understand the comparison between TIG and MIG welding by thoroughly familiarizing yourself with the process. Below you will find an overview of the principles of both processes, their advantages and disadvantages and their areas of application.
TIG welding principle
TIG welding is an arc welding process that uses a tungsten electrode to create an arc that produces the heat needed to weld the material.
The heat generated melts a filler material that is placed into the joint space or weld pool by the operator. During welding, argon or another combination such as argon/nitrogen and argon/hydrogen protects the arc from contamination.
TIG welding is the best method for welding metals with a thickness of about 10 mm and the highest welding quality. However, it is slower because the filler has to be fed manually. The electrode is non-consumable and creates deep penetration.
Advantages of TIG welding
- With high precision and accuracy
- Provides high quality welded joints that improve aesthetics
- It's environmentally friendly
- Provides the operator with better control
- Maintenance and operating costs are lower because non-consumable electrodes are used
Disadvantages of TIG welding
- It is an expensive process due to the fillers required.
- It's a slow process
- Requires a clean welding surface
TIG welding applications
For welding thin metals
In TIG welding, operational control is better, which makes it extremely precise and accurate. Therefore, it is the best method for welding thin metals.
For welding aluminum
Aluminum and other metals such as copper and titanium are thin sheets. They also require an aesthetic surface without losing functionality. TIG welding's precision and better solder joints make it the most suitable arc welding method for such metals.
Suitable for short production runs
Due to its precision, TIG welding is the best method for short production runs. However, for large print runs, it becomes more complex and expensive.
For the production of products that require aesthetics
TIG welding provides a high-quality weld joint, making it the best and most aesthetically pleasing welding method. Therefore, it is applicable in art, construction, etc. where aesthetics is a selling point.
MIG welding: principle, advantages and disadvantages and applications
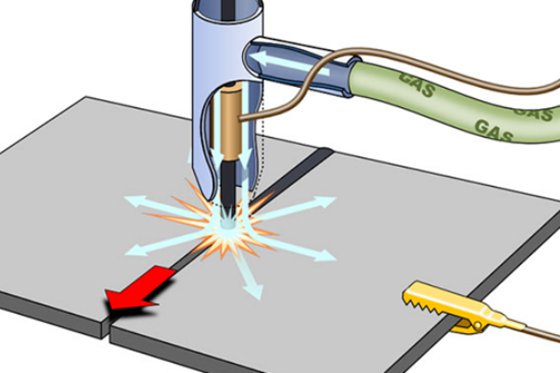
MIG welding principle
MIG welding is an arc welding process that uses a consumable electrode to create an arc that generates heat to weld material. During the welding process, CO2 protects the arc against contamination.
Unlike TIG welding, MIG welding does not require filler material because the electrode is consumable. Furthermore, due to these consumable electrodes, the process is semi-automatic (sometimes even automatic).
Advantages of MIG welding
-The welding process is fast and cheap
-With accuracy
-It is semi-automatic or automatic
-Produces a clean weld line
Disadvantages of MIG welding
-May be unreliable due to unstable arc
-Not environmentally friendly due to the production of smoke and fumes
-Not suitable for thin materials as it may burn
MIG Welding Applications
For welding thick metal parts
MIG welding uses a consumable electrode that acts as a filler material and solidifies the weld. This makes thick metals easier to weld.
Can be used when welding parts with small defects
MIG welding does not involve a start-stop mechanism like TIG welding. The continuous nature of welding reduces the likelihood of welding defects, making it the perfect method for welding products with few defects.
Welding for longer production cycles
MIG welding is production efficient and easy to use. Therefore, it is a better method for long production runs.
MIG vs. MIG Welding TIG welding: which is better?
According to sheet metal fabrication experts, MIG welding is better than TIG welding. Below are some reasons why MIG welding is better:
MIG is more diverse
MIG welding is more versatile due to the use of consumable electrodes. The process facilitates the connection of two metal parts without tension.
MIG has better speed
MIG welding is an automatic or semi-automatic process. Therefore, it is faster than TIG welding. Furthermore, MIG welding is a continuous process that, like TIG welding, omits details.
MIG is easier to use
TIG welding requires the operator to have extensive technical knowledge before committing to the process. MIG welding does not require much technical knowledge, which makes it easier to use.
Concluding
MIG and TIG welding processes are common arc welding processes with a wide range of material compatibility. Both methods are unique and have different advantages, disadvantages and areas of application. To make the best choice for your project, you can perform a comparison to determine the most suitable method for your project.
Common questions
What is the main difference between MIG and TIG welding?
The main difference between TIG and MIG lies in their application and principle. MIG, unlike TIG welding, is more suitable for thick metals, while TIG welding is ideal for thin metals due to operational control. Furthermore, MIG welding uses a consumable electrode that acts as a filler material, while TIG welding uses a separate filler material. You can read more about the differences between MIG and TIG welding above.
Is MIG or TIG better for welding aluminum?
Both processes are suitable for welding aluminum. However, most sheet metal manufacturers would choose TIG welding because aluminum is a lightweight material that requires better operational control. Additionally, aluminum is used for its aesthetic appeal, and the high quality of TIG welding makes it a better option.
Should I choose riveting over welding?
Riveting and welding are joining methods with their advantages and disadvantages. For example, riveting is a temporary method while welding is permanent. Additionally, welding is less aesthetically pleasing than riveting. It would be best to weigh these pros and cons before choosing either procedure.