Copper busbar welding is not common in our company's power construction due to its high requirements and difficulty. However, copper busbars, with their superior conductivity, were chosen for the electrical busbars of the coal plant.
After carrying out welding experiments and product welding applications, the welding subsidiary has essentially mastered the copper busbar welding technology, laying the foundation for future copper busbar welding in our company and raising our welding technology to a new level.
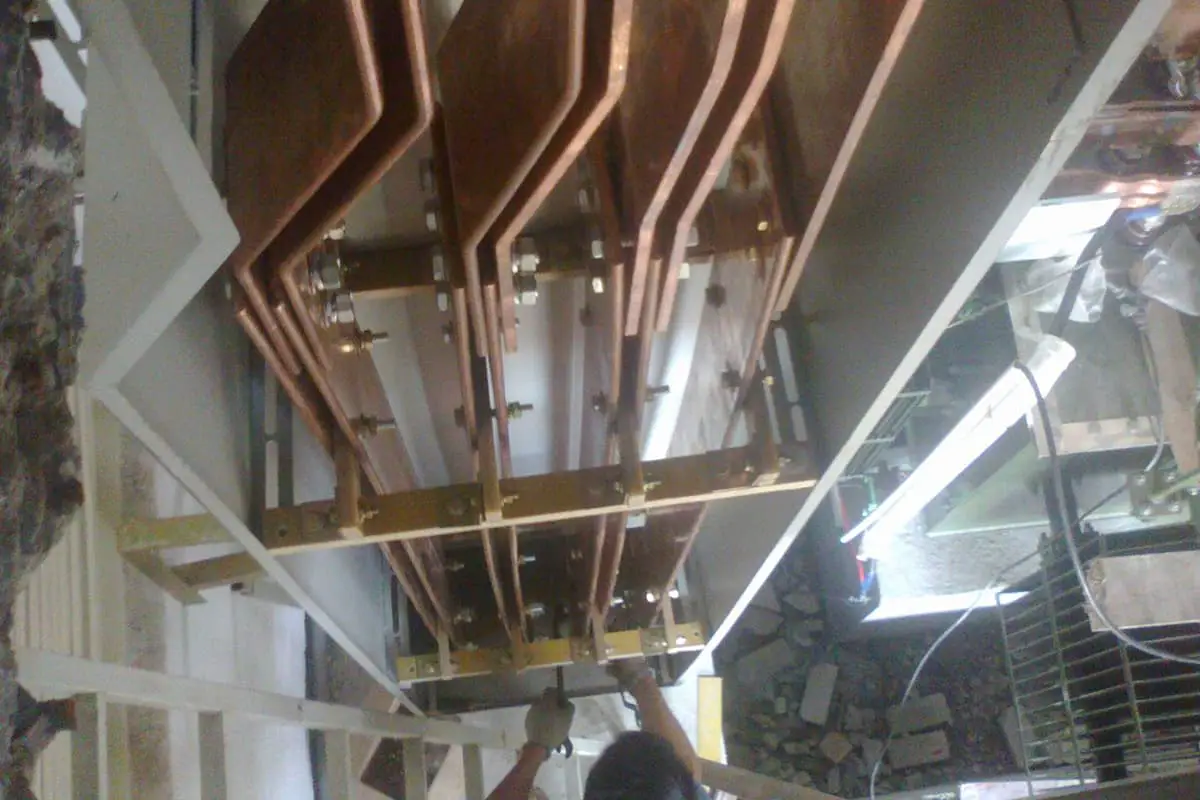
1 . Features and process of welding copper busbars
Connecting copper busbars in power plants mainly involves two methods: screw fixing and welding. Copper has excellent electrical conductivity, thermal conductivity, heat resistance and formability. Industrial pure copper is not less than 99.5% ωcu.
two . Features of copper welding
2.1 High Thermal Conductivity
The thermal conductivity of pure copper at room temperature is 8 times that of carbon steel. To heat a piece of pure copper to its melting temperature, a large amount of heat is required.
Therefore, a concentrated heat source is required during welding; otherwise, the heat will dissipate quickly. Preheating must be carried out on the workpiece when welding pure copper.
2.2 High sensitivity to thermal cracking
Various copper-based materials always contain a certain amount of impurities that form a low-melting eutectic. The presence of a low-melting eutectic film on the solidified part or in the heat-affected zone can cause cracking under welding stress.
2.3 High pore tendency
Pores in copper solder metal are mainly caused by hydrogen. When pure copper contains a certain amount of oxygen or when CO gas is dissolved in pure copper, pores can also be caused by water vapor and the reaction of CO with O to generate CO2 gas.
Generally, the pores are distributed in the center of the weld and close to the fusion line.
2.4 Deterioration trend in joint performance
During welding, copper inevitably undergoes oxidation and wear to a certain extent, resulting in various welding defects. This could potentially lead to a decrease in the strength, plasticity, corrosion resistance and electrical conductivity of the welded joint.
In the copper fusion welding process, the grain size in the weld and heat-affected zone increases significantly, affecting the mechanical properties of the joint to a certain extent.
To improve joint performance, it is not only crucial to minimize thermal effects, but also to control the impurity content of the weld and modify the weld metal through alloying.
3 . Copper Bus Welding Process
3.1 Welding Method Selection
The most common welding methods for copper are gas welding and manual tungsten inert gas (TIG) welding.
However, to improve welding quality, manual TIG welding is preferred. This welding method is superior due to its concentrated heat, easy-to-control melt pool and, mainly, its effectiveness in welding materials with a thickness (δ) of less than 12 mm.
TIG welding provides stable arc, excellent protection and flexible operation, making it particularly suitable for medium thickness welding.
3.2 Selection of Welding Materials
Copper welding materials refer to welding wires and fluxes. Filler Welding Wire: When performing manual TIG welding, it is necessary to manually add filler welding wire. The brand, welding wire composition and welding processability, joint mechanical properties and corrosion resistance are closely related.
When choosing filler welding wire, the first considerations should be the base metal brand, plate thickness, product structure and construction conditions.
Therefore, when welding copper busbars, a filler welding wire with a composition similar to the base metal is selected. The technical parameters of copper welding wire are shown in Table 1.
Table 1: Technical Parameters of Copper Welding Wire
Note | GB Standard Model | Primary chemical composition | Mass Fraction (%) |
Fusion point | Primary use |
HS201 (Scu-2) |
HSCu | Sn-1.1 | Si-0.4 | 1050 | Pure copper and tungsten arc welding (Use of Flow 301) |
HS201(Scu-2) | Mn-0.4 | Copper (remained) |
Technical parameters of copper welding wire
Welding: During argon arc welding, the surface of the molten metal tends to oxidize to form cuprous oxide (Cu2O). Its presence often leads to defects such as weld porosity, cracks and slag inclusions. The technical parameters of the weld are shown in Table 2.
4. Pre-Welding Preparation
Pre-welding preparation mainly refers to cleaning the workpiece and welding materials, and designing and processing the groove before welding.
It is crucial to clean the surface of the welding wire and both sides of the copper plate groove within 30mm to remove grease, moisture, oxides and other impurities. Groove processing is carried out using a pneumatic chisel or beveling machine.
The types of groove processing for copper welding are shown in Table 3.
Table 2: Technical Parameters for Welding Flux
Note | Primary components (by mass fraction) % | Melting point(℃) | Scope of application | |||||
Na2B407 | H3B03 | In F | NaCl | KCI | Other | |||
CJ301 | 16.5-18.5 | 76-79 | – | – | – | AIP04 4-5.5 |
650 | Copper gas welding |
Table 3: Types of welding groove processing for copper
Material name | Plate Thickness (mm) | Diagram | Bezel type | Joint type | Joint Structure Dimensions | ||
The | B (mm) |
P (mm) |
|||||
Pure Copper | ≤3 |
|
I-shape | Butt joint | – | 1-2 | |
≥4 |
|
V format | Butt joint | 30°-35° | B | 1-2 | |
≤12 |
|
Unique V shape | T-Joint | 50°~60° | 2-3 | 1-2 |
Note: 'b' can be set according to the on-site joint gap and process requirements.
Table 4: Welding Process Parameters for Copper
Plate Thickness (mm) |
Tungsten electrode diameter (mm) |
Welding wire diameter (mm) |
Welding current (A) |
Chlorine gas flow (L/min) |
Preheating temperature (°C) |
1-4 | 2.0 | 2.0 | 140-220 | 15-16 | 200-300 |
5-12 | 2.5 | 2.0 | 240-260 | 16-18 | 600-650 |
5. Key points for welding copper busbars
5.1 The copper bus soldering location must maintain an ambient temperature above 5°C;
5.2 The shielding gas used is argon;
5.3 The copper busbar welding wire should be HS201 pure copper wire. CJ301 flux is added and then mixed with anhydrous ethanol (alcohol) until a pasty consistency is obtained, which is then spread on the beveled welding surface before welding;
5.4 The welding wire is heated and coated with CJ301 before welding;
5.5 To select the welding process parameters, manual tungsten arc welding uses direct current positive electrode (DCEP); the pure copper welding process parameters are shown in Table 4;
5.6 The welding machine should work well, with flexible current adjustment and convenient operation;
5.7 The preheating method of copper busbar is electric or flame heating;
5.8 For preheating temperature selection, parts with a thickness δ of less than 4 mm can be preheated appropriately, while those with a thickness δ of more than 4 mm should be preheated at a temperature of 600-650 ℃;
5.9 Welding under restrictive conditions should be avoided as much as possible. Strict temperature control between passes is necessary during the welding process, using small oscillation welding and low line energy;
5.10 The welding seam must be spot welded, with a length of no less than 10mm. The number of welding points must be evenly distributed and not less than three;
5.11 For welding parts with a thickness δ greater than 4mm, a multilayer and multipass welding process must be used;
5.12 Black spots caused by high temperatures during welding must be cleaned immediately. Cleaning between passes must be carried out with a stainless steel brush;
5.13 The quality of the welding points must be checked before welding. Welding can only continue after confirming that there are no defects;
5.14 Intermediate inspection steps must be reinforced. For example, after spot welding, between welding layers and after the entire welding is completed, inspections must be carried out strictly in accordance with the requirements of the welding process to ensure welding quality.