Summary:
Connecting aluminum and steel can produce lightweight automotive parts. However, cracking of intermetallic compounds caused by welding these dissimilar metals can significantly impact joint performance.
This post introduces the main welding methods for laser welding of aluminum and steel and explains the status of research in recent years.
Galvanized steel is a steel substrate coated with layers of zinc of different thicknesses. The zinc plating process is categorized into electroplating and hot galvanizing.
The zinc layer not only provides physical shielding but also offers electrochemical protection to the steel substrate.
Due to its excellent corrosion resistance, galvanized steel is widely used in various sectors such as transportation, electrical power, construction, heating installations, instruments and furniture.
In particular, the application of ordinary galvanized steel, high-strength galvanized steel and ultra-high-strength galvanized steel in the automobile industry improves the corrosion resistance and extends the service life of the body and other parts.
However, the presence of a zinc layer makes fusion welding of galvanized steel plates challenging. This is because the melting point of zinc is 420 ℃, its boiling point is 908 ℃, while the melting point of base steel is 1300 ℃ and its boiling point is 2861 ℃.
During the melting and welding process, zinc tends to evaporate and oxidize extensively, leading to defects such as pores, incomplete fusion and cracking.
Aluminum and its alloys are known for their lightweight properties (with a density of 2.7g/cm3), high specific strength, excellent electrical and thermal conductivity, corrosion resistance and the ability to retain good mechanical properties even at low temperatures.
In today's world, energy, security and environmental protection have become crucial issues. With growing concerns about environmental pollution and the energy crisis, achieving lightweight vehicles has become a global focus.
Consequently, extensive research has been conducted on aluminum/magnesium, aluminum/titanium, titanium/aluminum, and aluminum/steel composite structures throughout the world.
Aluminum/steel composite structures take full advantage of the advantages of both materials to reduce weight and pollution, and have found wide applications in the automotive, aviation and shipbuilding industries.
The application of aluminum-steel connections in the automobile door panel is illustrated in the figure below.
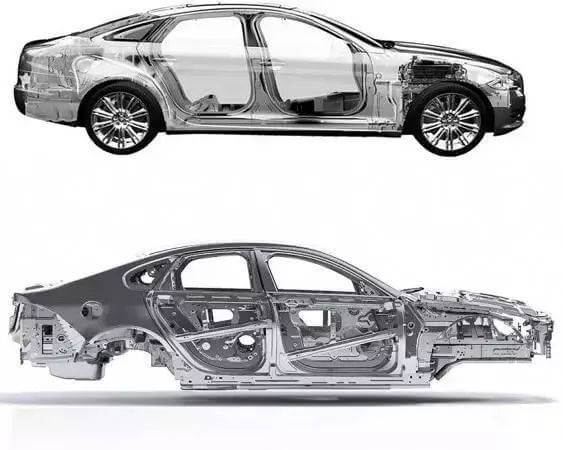
Hybrid laser arc welding technology, as shown in the experimental schematic diagram in Fig. 2, is a new and efficient welding method developed in the 1970s.
The high energy density of the laser allows deeper penetration, but the gap bridging is poor and the assembly accuracy must be high.
The arc heating range is wide, which allows you to get a wider weld, but the arc bridge to the gap is good.
By utilizing their respective characteristics, hybrid laser arc welding technology can achieve wide butt weld and large penetration.
The plasma produced by the laser can stabilize the arc, making the hybrid welding process adaptable and efficient.
Honggang Donga et al. invented a method for connecting dissimilar metals using large composite laser and arc heat sources.
The patent focuses on laser arc heat source hybrid welding with a small spot, which cannot be applied to the connection between steel and aluminum, steel and copper and other dissimilar metals.
In this method, the laser has an obvious stabilizing effect on the arc, which is used to melt the filler metal and low-melting base metal.
The large spot laser can precisely control heat input.
Tensile property tests on 5A02 aluminum alloy and galvanized steel joints obtained by this method show that the failure position of the sample occurs in the zone affected by welding heat on one side of the aluminum alloy base metal, and not in the zone brazing connection. The joint strength can reach 153.1 MPa. Qin and others adopt laser MIG composite welding of galvanized steel/aluminum alloy and AlSi5 welding wire.
Experimental results show that the brazing interface produces 2 to 4 μm and the phase groups are FeAl2, Fe3Al5 and Fe4Al13. The maximum tensile strength of the joint is 247.3 MPa.
Wangshujun et al. also used laser MIG hybrid welding technology and experimented with three different welds: AlSi5, AlSi12 and AlMg5 to study the effects of intermetallic compounds, weld microstructure and formation after the addition of Si and Mg.
The results show that increasing the Si content can refine the grains in the melting zone and increase the microhardness of the melting zone. The microhardness of Al-Si solder in the fusion zone is higher than that of Al-Mg solder.
The average thickness of the intermetallic compound layer for AlSi12, AlSi5 and AlMg5 welds is 0.90 μm, 1.49 μm and 2.64 μm, respectively.
It was concluded that the presence of Si in welds inhibits the diffusion of Fe and reduces the formation of intermetallic compounds.
XRD analysis of the middle layer reveals that the layers of intermetallic compounds corresponding to AlSi5 and AlSi12 consist of the phases Fe2Al5, Fe4Al13 and Al0.5Fe3Si0.5, while those corresponding to AlMg5 consist of the phases FeAl2, Fe2Al5 and Fe4Al13.
The joint strength of AlMg5, AlSi5 and AlSi12 welds is 178.9 MPa, 172.43 MPa and 144 MPa, respectively.
It was concluded that an increase in Si content is detrimental to joint strength, while the addition of Mg increases joint strength. However, it has not been explained how Si and Mg affect joint strength.
Tommy et al. conducted a study on the interaction between laser and plasma arc during hybrid laser arc welding and developed a hybrid coaxial laser arc welding head.
l laser brazing
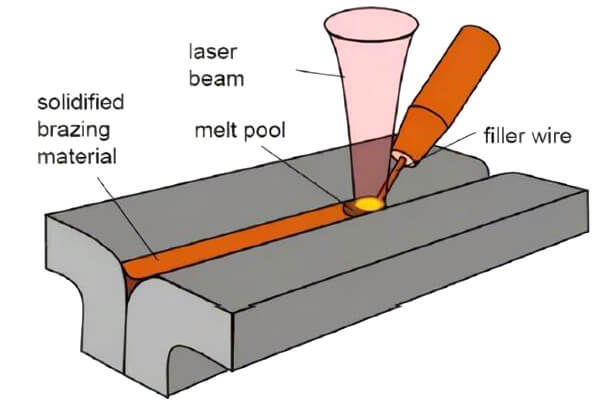
Brazing involves the use of solder with a lower melting point than the base metal. By heating to a temperature higher than the melting point of the solder and lower than the melting point of the base metal, the solder melts while the base metal remains solid.
The liquid solder then wets the base metal and, under the capillary action of the brazing gap, automatically fills any gaps in the base metal and diffuses with it to create a strong joint.
Fusion brazing combines the characteristics of brazing and fusion welding, making it ideal for connecting dissimilar materials with large differences in physical properties.
When steel and aluminum are brazed, the steel remains solid while the aluminum and solder melt. The resulting brazing connection is formed on the steel/weld side, while fusion welding occurs on the solder/aluminum side.
The basic principle of fusion brazing for steel and aluminum is to combine molten aluminum and solder with solid steel through an interface reaction.
In this method, solder may or may not be added for soldering purposes.
Peyre et al. conducted a study on joining galvanized steel and aluminum alloy using solderless laser fusion brazing.
Their findings indicate that an interface layer 2 to 20 μm thick forms along the steel-aluminum interface.
The layer mainly consists of the Fe2Al5 phase, with a hardness of up to 1200HV. This leads to cracks in the joint, causing a significant reduction in the mechanical properties of the joint.
Evaporation of zinc produces pores, but a 10 μm thick zinc coating promotes wetting and spreading of aluminum on the steel.
Tensile tests indicate that coating flow on the surface of galvanized steel can inhibit zinc evaporation. Non-galvanized steel, however, has low mechanical resistance.
To control the formation of Fe-Al intermetallic compounds and improve joint performance, some researchers have used solder during laser brazing to change the chemical composition of the joint.
Serra et al. used 4047 solder (Al-12Si) in the aluminum/steel laser fusion brazing connection, resulting in a continuous joint without significant macro defects and a thin layer of Fe Al-Si intermetallic compound at the steel/weld interface.
The effect of Si on the growth of Fe-Al intermetallic compounds was investigated using Al-12Si solder. The proposed mechanism suggests that Si reduces the melting temperature of aluminum, influences the viscosity and surface tension of molten aluminum, and subsequently affects the weld wetting angle and width.
In addition, some scholars have added Mg, Cu and other elements to the solder to explore the effect of solder alloy on the microstructure and properties of the solder.
Dharmendra et al. conducted a fusion brazing test on a lap joint made of DP600 galvanized steel and AA6016 aluminum alloy using continuous pulse Nd:YAG laser.
They used Zn-Al welding wire containing 85% Zn and 15% Al in the test and varied the laser power, welding speed, and wire feed speed.
The researchers found that the thickness of the reaction layer was between 3 and 23μm.
When the heat input was between 60 and 110J/mm, the tensile strength of the joint reached 220MPa, with the fracture position located far from the weld and close to the aluminum alloy side.
At welding speeds of 0.5 and 0.8m/min, the corresponding thicknesses of the intermetallic compounds were 8 and 12μm, respectively.
Tensile tests showed that the joint presented greater mechanical resistance when the thickness of the intermetallic compound was between 8 and 12μm.
If the thickness was less than 8μm, the mechanical resistance increased as the intermetallic layer increased, while if it was greater than 12μm, the mechanical resistance decreased.
It was explained that when the composite layer is thin, cracking initiates along the brittle intermetallic composite layer, resulting in very low fracture resistance.
On the other hand, when the composite layer is thick, the mechanical resistance is also low due to the fragility of the layer in relation to other areas.
Laukant et al. conducted a laser fusion brazing test using ZnAl2 solder on aluminum/steel. The results showed that intermetallic compound layers of about 5μm FeAl were produced, and the shear force of the joint reached up to 9 KN.
Similarly, Rajashekhara Shabadi et al. conducted a laser fusion brazing test using ZnAl30 solder on AA6016 and low-carbon galvanized steel. The intermetallic compound formed in the test results is mainly Fe2Al5Znx, which may also contain ZnFeAl3, with a thickness of about 10μm.
Recently, some scholars have conducted laser fusion brazing experiments on high-strength aluminized steel and aluminum alloy.
For example, Windmann et al. performed a laser fusion brazing test using AlSi3Mn solder and discovered the formation of the Al8Fe2Si phase at the AlSi3Mn/Mn22B5 interface.
Furthermore, the thickness of the intermetallic compound created at the Mn22B5/AlSi3Mn interface is 2 to 7μm, and the shear strength of the joint is 21 to 74MPa.
By preheating the steel surface before welding, the joint strength can be increased to 210 to 230MPa.
Recent research has shown that both Al-Si solder and Zn-Al solder inevitably create intermetallic compounds.
However, the growth sequence of FeAl-Si intermetallic compounds and the identification of the Zn-Al weld reaction phase require further investigation.
Laser fusion welding is a promising technology for connecting steel and aluminum.
Conclusion
Hybrid laser arc welding is mainly used to weld thicker plates due to its high welding efficiency.
Laser fusion brazing has great potential for application in the production of light automobiles.
The laser fusion brazing process has been used to connect thin and dissimilar metals made of aluminum and steel using Al-Si and Zn-Al solders.
However, there are still several challenges in laser welding of galvanized steel/aluminum alloys for automobile manufacturing. For example, the low absorptivity of the material to laser energy results in the generation of plasma, which can impact the stability of the welding process.
Furthermore, the process of connecting aluminum and steel can produce brittle Fe-Al intermetallic compounds. Furthermore, the metallurgical compatibility of the molten weld with the aluminum alloy base metal and its wettability with the base metal steel need to be considered.
Finally, it is crucial to control and prevent welding defects such as pores, cracks, incomplete fusion and slag inclusion.