1. Welding of quenched and tempered low carbon and low alloy steels
1. Welding characteristics of quenched and tempered low-carbon and low-alloy steels
Quenched and tempered low-carbon and low-alloy steels generally have high yield strength (450-980MPa), good ductility, toughness and resistance to wear and corrosion. Depending on the intended application, different alloy compositions and heat treatment processes can be employed to obtain low-carbon, low-alloy quenched and tempered steels with different comprehensive properties.
Low carbon quenched and tempered steels typically have a wC (carbon equivalent) content of no more than 0.21%, which gives them better weldability compared to medium carbon quenched and tempered steels.
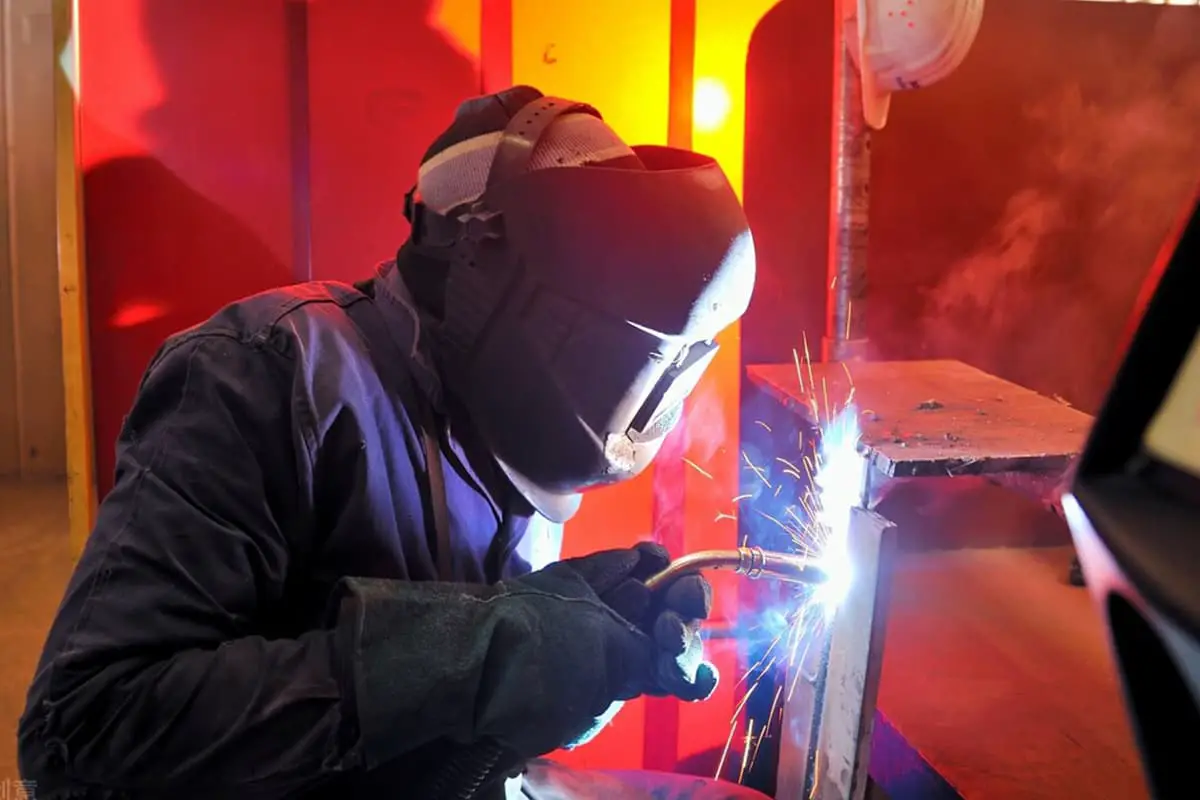
Welding sequence | |
1 | Check groove dimensions and surface quality |
two | Clean the groove and surrounding area of oil and other dirt |
3 | Perform spot welding using the first outer layer welding process, with a length of 30-50mm |
4 | Weld inner layers 1-4 |
5 | Grind the root pass by carbon arc gouging from the outside, followed by grinding with a grinding wheel |
6 | Weld the outer layers 5-7 |
7 | Clean up slag and spatter after welding |
8 | Perform visual inspection |
9 | Perform non-destructive testing |
Welding Specification Parameters
Passes | Welding method | Welding Material Grade | Welding material specification | Current types and polarity | Welding Current (Ampere) | Arc Voltage (Volt) | Welding speed (mm/per pass) | Comments |
1 | SMAW | J507 | Φ4.0 | DCEP | 150~180 | 22~24 | 150~200 | |
2~7 | SMAW | J507 | Φ5.0 | DCEP | 180~210 | 22~24 | 160~220 |
3) For the same equipment mentioned above, the welding seam between the big head and the inner head is a corner joint. The material is 16MnR with a thickness of 82.5 mm and 38 mm. It requires a K-shaped groove and falls into the category of welding medium thickness plates.
The preheating temperature of the welding area and its surroundings must be 100°C. The interlayer temperature during the welding process must be maintained between 100-250°C. After welding, it needs to be heated to 620℃ and held for 2 hours for stress-relieving annealing treatment. See Table 5-16 for specific welding process details.
Table 5-16: Welding Process Card for K-Slot Corner Joint
Welding Process Card for Joints | Number | ||
Joint Diagram ![]() |
Base material | 16MnR | 16MnR |
Base material thickness | 82.5mm | 38mm | |
Welding position | Flat welding | ||
Welding technique | Straight welding, multiple pass welding | ||
Preheating temperature | 100°C | ||
Interim temperature | ≤100~250℃ |
Welding sequence | |
1 | Check groove dimensions and surface quality |
two | Clean the groove and surrounding area of oil and other dirt |
3 | Perform spot welding using the first outer layer welding process, with a length of 30-50mm |
4 | Weld the inner layers 1-6 |
5 | Grind the root pass by carbon arc gouging from the outside, followed by grinding with a grinding wheel |
6 | Weld outer layers 7-16 |
7 | Clean up slag and spatter after welding |
8 | Perform visual inspection |
9 | Perform non-destructive testing |
10 | Perform post-welding heat treatment |
Welding Specification Parameters
Passes | Welding method | Welding Material Grade | Welding material specification | Types of current and polarity | Welding Current (Ampere) | Arc Voltage (Volt) | Welding speed (mm/per pass) | Comments |
1 | SMAW | J507 | 1.0 | DCEP | 150~180 | 22~24 | 150~200 | |
2~16 | SMAW | J507 | 5.0 | DCEP | 180~210 | 22~24 | 160~220 |
4) A chemical machinery factory is producing a liquid chlorine storage tank. The main material is 16MnDR with a thickness of 22mm. The welding seam serves to close the cylindrical body, using a butt joint with an asymmetrical X-shaped groove.
The welding process involves a combination of shielded metal arc welding (SMAW) and submerged arc welding (SAW). After welding, heat treatment at 620°C for 1 hour is required to eliminate stress. See Table 5-17 for specific welding process details.
Table 5-17: Welding Process Card for Asymmetrical X-shaped Groove Butt Joint
Welding Process Card for Joints | Number | ||
Joint Diagram |
Base material | 16MnDR | 16MnDR |
Base material thickness | 22mm | 22mm | |
Welding position | Flat welding | ||
Welding technique | Straight welding pass | ||
Preheating temperature | Room temperature | ||
Interim temperature | ≤150℃ | ||
Post-weld heat treatment | 620°C, 1h |
Welding sequence
1 | Check groove dimensions and surface quality, groove surface 100% magnetic particle test (MT) |
two | Clean the groove and surrounding area of oil and other dirt |
3 | Perform spot welding using the first outer layer welding process, with a length of 30-50mm |
4 | Weld inner layers 1-4 |
5 | Grind the root pass by carbon arc gouging from the outside, followed by grinding with a grinding wheel |
6 | Weld the outer layers 5-6 |
7 | Clean up slag and spatter after welding |
8 | Perform visual inspection |
9 | Perform non-destructive testing |
10 | Perform post-welding heat treatment |
Welding Specification Parameters
Passes | Welding method | Welding Material Grade | Welding material specification | Current types and polarity | Welding Current (Ampere) | Arc Voltage (Volt) | Welding speed (mm/per pass) | Comments |
1 | SMAW | J507GR | 4.0 | DCEP | 140~170 | 22~24 | 150~200 | |
2~4 | SMAW | J507GR | 5.0 | DCEP | 170~200 | 22~24 | 200~250 | |
5~6 | MOUNTAIN RANGE | H10MN2 SJ101 |
4.0 | DCEP | 600~650 | 32~36 | 24 ~ 28 m/h |
5) As mentioned before, for the welding seam between the nozzle upper flange and the liquid chlorine storage tank tube, a butt joint with one-sided welding and two-sided forming is required.
Tungsten inert gas (TIG) welding is used for back sealing, and shielded metal arc welding (SMAW) is used for filling and capping. The groove is a V-shaped groove without a blunt edge. After welding, stress relief treatment is carried out. See Table 5-18 for welding process details.
Welding Process Card for Joints | Number | |||
Joint Diagram ![]() |
Base material | 16MnD | 16MnD | |
Base material thickness | 6mm | 6mm | ||
Welding position | Flat welding | |||
Welding technique | Straight welding pass | |||
Preheating temperature | Room temperature | |||
Interim temperature | ≤150℃ | |||
Post-weld heat treatment | 620°C, 1h | |||
Tungsten electrode diameter (mm) | Φ2.5 | Shielding gas | Air | |
Nozzle diameter (mm) | Φ16 | Gas flow rate (L/min) | 10 |
Welding sequence | |
1 | Check groove dimensions and surface quality, groove surface 100% magnetic particle test (MT) |
two | Clean the groove and surrounding area of oil and other dirt |
3 | Perform spot welding using the first outer layer welding process, with a length of 5 to 10 mm |
4 | Weld the inner layers 1-3 |
5 | Perform visual inspection |
6 | Perform non-destructive testing |
7 | Perform post-welding heat treatment |
Welding Specification Parameters
Passes | Welding method | Welding Material Grade | Welding material specification | Types of current and polarity | Welding Current (Ampere) | Arc Voltage (Volt) | Welding speed (mm/per pass) | Comments |
1 | GTAW | H10MnSi | 2.5 | DCEN | 80~120 | 10~12 | 50~80 | |
2~3 | SMAW | J507GR | 4.0 | DCEP | 140~170 | 22~24 | 140~180 |
2. Typical example of welding low-carbon low-alloy quenched and tempered steel
A certain company is manufacturing the movable legs of an automotive crane, with material HQ80C. Uses an argon shielding gas mixture and H08MnNi2MoA welding wire. See Table 5-19 for welding process details.
Welding Process Card for Joints | Number | ||
Joint Diagram |
Base material | HQ80C | HQ80C |
Base material thickness | 16mm | 12mm | |
Welding position | Flat welding | ||
Welding technique | Straight welding pass | ||
Preheating temperature | 100~125℃ | ||
Interim temperature | 100~125℃ | ||
Shielding gas flow rate (L/min) | Air+CO 2 (20%) | ||
Shielding gas flow rate (L/min) | 10~15 |
Welding sequence | |
1 | Check groove dimensions and surface quality |
two | Before assembly, carry out a blasting treatment to remove oxide scale, oil and other dirt from the surface of the steel plate, groove and surrounding area |
3 | Perform spot welding using the first layer welding process for positioning, with a length of 30-50mm |
4 | Weld the 4 inner corner welds, cleaning the root outside until the inner corner weld is exposed, then weld the outer corner welds |
5 | After welding, grind the welds and clean up slag and spatter |
6 | Perform visual inspection |
Welding Specification Parameters
Passes | Welding method | Welding Material Grade | Welding material specification | Current types and polarity | Welding Current (Ampere) | Arc Voltage (Volt) | Welding speed (mm/per pass) |
1 | MAW | H08MnNi2MoA | l.2 | DCEN | 120~150 | 18~22 | |
2~4 | MAW | H08MnNi2MoA | 1.2 | DCEN | 140~170 | 22-24 |
3. Typical example of welding of quenched and tempered medium carbon steel
Repair of a broken shaft in a rolling mill, welding the shaft core to the intermediate shaft. The material is 37SiMn2MoV (similar to 42CrMo) and is welded by the shielded metal arc welding (SMAW) process. The welding electrode used is J607Ni. See the welding process details in the table.
Welding Process Card for Joints | Number | ||
Joint Diagram ![]() |
Base material: 37SiMn2MoV (similar to 42CrMo) | 37SiMn2MoV | 37SiMn2MoV |
Welding position: Shaft core to intermediate shaft | Flat welding | ||
Welding Technique: Shielded Metal Arc Welding (SMAW) | Flat welding | ||
Preheating temperature: According to welding procedure specifications | Straight welding pass, multiple passes with multilayer pressure welding | ||
Interlayer temperature: According to the specifications of the welding procedure | 300℃, within a range of 300mm from the welding area | ||
Post-weld heat treatment: According to welding procedure specifications | 300-400℃ |
Welding sequence | |
1 | Check groove dimensions and surface quality, penetration test 100% of groove surface (PT) |
two | Clean the groove and surrounding area of oil and other dirt |
3 | Insert the shaft core into the intermediate shaft and then place it into a well-type heating furnace for preheating |
4 | When welding, ensure that the thickness of each layer of deposited metal is less than 2 mm |
5 | Perform visual inspection |
6 | Carry out hydrogen removal treatment at 350°C~400°C for 2 hours. After sufficient insulation time, wrap the area within 300 mm of the weld with insulating blanket |
7 | After cooling, perform liquid penetrant testing on the weld and surrounding base material with no surface defects. After passing inspection, process the end of the central shaft, assemble and tighten after cooling. Apply uniform preheat to the area within 300mm of the weld, increasing the temperature to 300℃. Welding requirements remain the same as mentioned above |
8 | Perform the hydrogen removal treatment, following the same procedure as above |
9 | Take a stress relief treatment |
10 | Take PT and UT tests |
Welding Specification Parameters
Passes | Welding method | Welding Material Grade | Welding material specification | Current types and polarity | Welding Current (Ampere) | Arc Voltage (Volt) | Welding speed (mm/per pass) | Comments |
1 | SMAW | J607Ni | Φ4.0 | DCEP | 140~170 | 22~25 | 160~200 | |
2~3 | SMAW | J607Ni | Φ5.0 | DCEP | 170~200 | 22~25 | 180~220 |