TIG welding and A-TIG welding
Tungsten argon arc welding (TIG) is widely used in modern welding methods due to its high welding joint quality, good formability, excellent welding performance and flexible application scenarios, and can be portable and used in environments complexes.
However, its limitations are also very obvious.
Regardless of carbon steel, stainless steel or titanium materials, ordinary TIG welding is only applicable to thin plates, which is determined by its welding principle: during TIG welding, due to the temperature coefficient and surface tension, the direction of the welding pool flux is also export-oriented, as shown in Figure 1.
Therefore, when the welding power is increased, the width of the welding pool increases more, but the depth increases less.
At the same time, the bearing capacity of the tungsten electrode is limited, the arc heat is relatively dispersed during the welding process, and the arc power is limited.
Therefore, in general, the TIG welding speed is low and the weld penetration depth is shallow. Generally, only thin plates below 3mm can be welded;
Generally, the plate or tube with a thickness of more than 3mm needs to be chamfered first, and backing welding + overlay welding is adopted, which is time-consuming, complicated and expensive.
Its disadvantages can be summarized as follows: the penetration depth of single-layer welding is shallow, the multi-layer welding process is complex, and the cost is high.
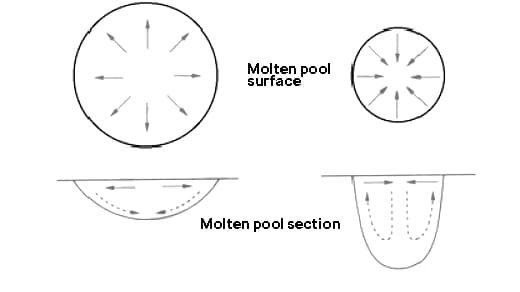
Fig. 1 TIG welding pool flow direction
With the development of welding technology, in order to overcome the penetration limitation of TIG welding, active argon arc welding (A-TIG) emerged.
The A-TIG welding method was first proposed by the Ukrainian Barton Welding Research Institute (PWI) in the 1960s, but it was only in the late 1990s that extensive research was carried out in research institutes in European and American countries. (like EWI and TWI).
Among them, the active flow developed by EWI has been widely used. However, the application in this field has not been popularized in China.
Comparison of welding methods and effects
In terms of welding method, the only difference between A-TIG welding and conventional TIG welding is that an active agent coating process is added.
That is, before welding, the welding active agent is evenly coated on the weld surface, as shown in Fig. 2, which is the coating effect of the welding active agent prepared by the small team.
However, for welding thick plates, the chamfering process is omitted, which greatly improves the efficiency and production cost.
Under the same welding specification, compared with TIG, the weld penetration can be greatly improved (up to 300%), as shown in Fig. 3 (a) below is the traditional TIG welding pool, (b) is the A-TIG under the same welding parameters.
Currently, the A-TIG welding method has been used to weld stainless steel, carbon steel, nickel-based alloy and titanium alloy.
Compared with conventional TIG, A-TIG can significantly improve productivity, reduce production costs and reduce welding deformation.
It has a wide application perspective.
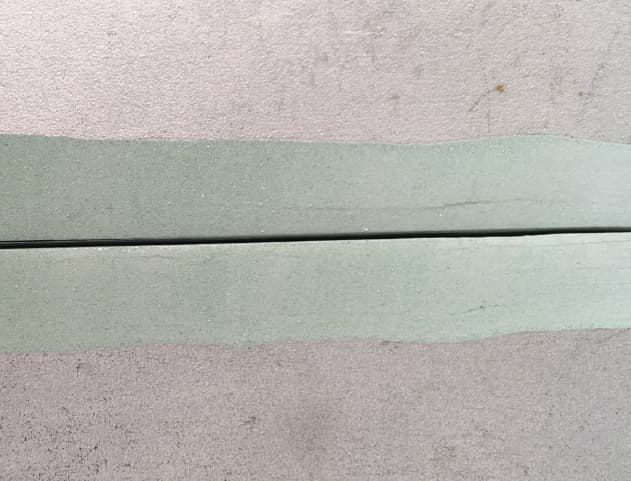
Fig. 2 Effect of active coating agent on welds
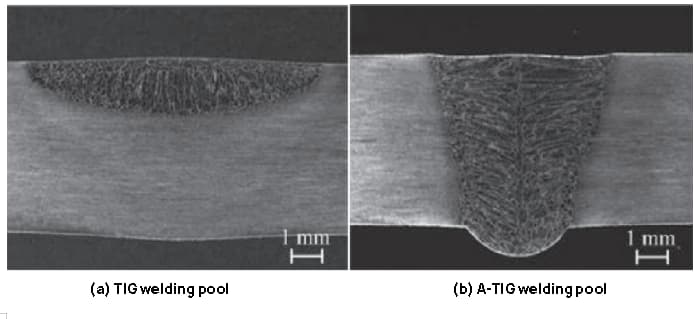
Fig. 3 Comparison of welding penetration
Principle of increasing penetration of A-TIG welding
The penetration enhancement mechanism of A-TIG welding includes the viewpoint of “arc contraction”, “surface tension”, “anode point contraction” and “plasma contraction”.
Ukrainian scholars tend towards the “arc contraction” view, while American scholars believe that the “surface tension” view is the main reason for the increased depth of penetration.
Currently, there is no unified view on the mechanism for increasing weld penetration in the world.
“Arch contraction” point of view
Although arc contraction is obvious, there is still no consensus mechanism to explain the effect of active flux elements on welding penetration in A-TIG welding.
It is now believed that the most likely mechanism will be related to the influence of halogens and oxides at the arc root and plasma region (also related to voltage), rather than the influence of molten pool movement.
As shown in Figure 4 below, the number of electrons in the peripheral area of the arc decreases and electrons are the main charge carrier.
This forces the arc to contract and reach a new equilibrium state, which has greater current density in the arc column region and in the anode region.
It is believed that this reaction occurs mainly in the peripheral region of the arc at lower temperatures, which leads to a reduction in the diameter of the arc column and the anode area.
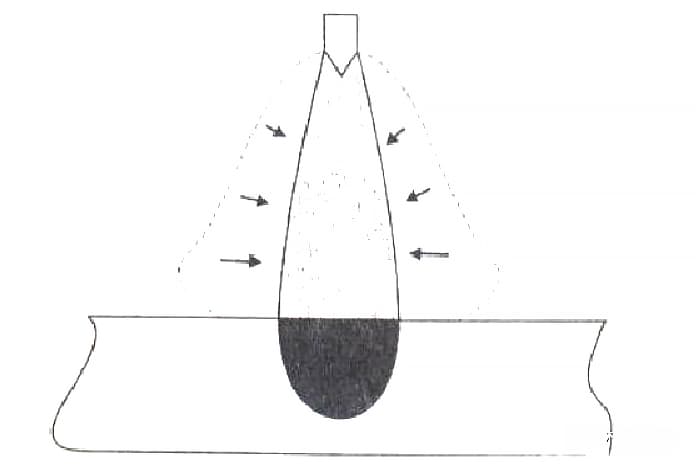
Fig. 4 Schematic diagram of arc contraction
“Surface tension” point of view
The “surface tension” point of view holds that the flow state of the metal in the molten pool plays a decisive role in the depth of penetration formed.
In traditional TIG welding, the surface tension of the molten metal in the molten state forms a surface tension flow from the center of the molten pool to the periphery of the molten pool due to the temperature coefficient, and the resulting penetration depth is relatively shallow;
When the active agent is present in the molten pool metal, the surface tension gradient of the liquid metal in the molten pool changes, so that the molten pool metal forms a flow direction from the periphery of the molten pool to the center of the molten pool. , and the heating efficiency of the lower molten pool is improved, thus forming a greater molten depth.
As shown in Fig. 5 below.
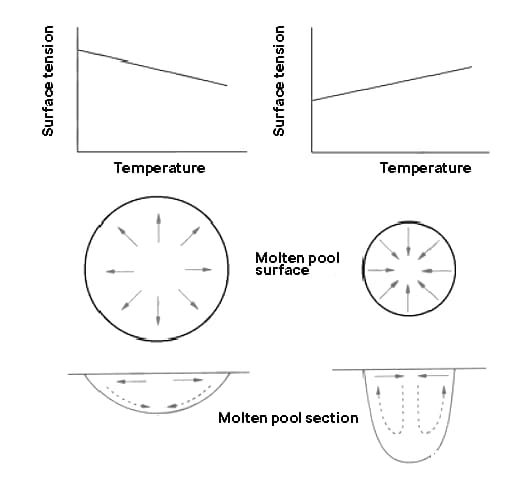
Fig. 5 Effect of surface tension on molten pool flow
“Anodic point” viewpoint
According to the “anodic stain” point of view, after adding sulfide, chloride and oxide to the molten pool, the anodic stain of the molten pool will shrink obviously, as shown in Fig. 6, and a large penetration depth will be generated .
For this phenomenon, research shows that: after the addition of the active agent, the metallic vapor generated by the molten pool is suppressed.
Because metallic particles are more likely to be ionized, when the metallic vapor is reduced, only a small band of anode points can be formed and the arc conducting channel is constricted.
While the electromagnetic convection inside the molten pool is activated, the plasma convection on the surface of the molten pool is weakened, so as to form a greater penetration depth.
This explanation is more convincing for active agents of the non-metallic compound type, but not for metallic compounds.
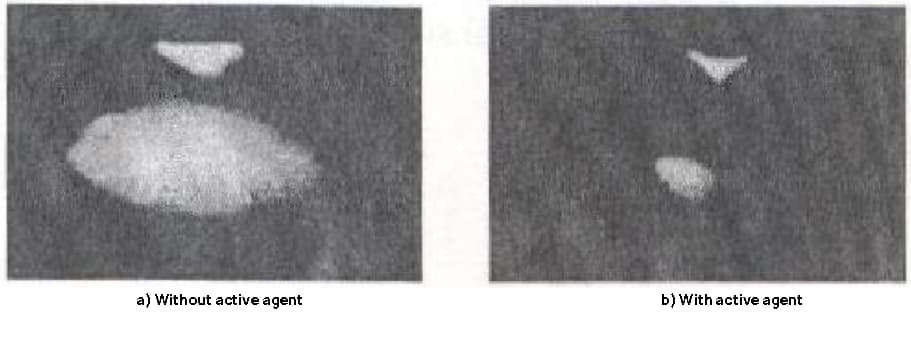
Fig. 6 Shrinkage of the arc anode area in the presence of active elements
Summary
In recent years, a large number of welding researchers at home and abroad have used various auxiliary methods to study the application of A-TIG in welding medium and thick plates.
It was found that different effects of active agents can be obtained through the proportion of different components in the active agents, which have different effects on increasing weld penetration and weld quality.
For specific materials, they can be developed and applied in industrial production by adjusting the proportion of active elements or adding other active trace elements to form active agents.
It is also hoped that this technology can be more widely used.