Metal and polymer connections are ideal lightweight structures for automobiles. The process of effectively connecting composite materials such as carbon fiber reinforced polymer (CFRP) or glass fiber reinforced polymer (GFRP) and metallic components has received much attention with the emergence of lightweight automotive structures (see Figure 1).
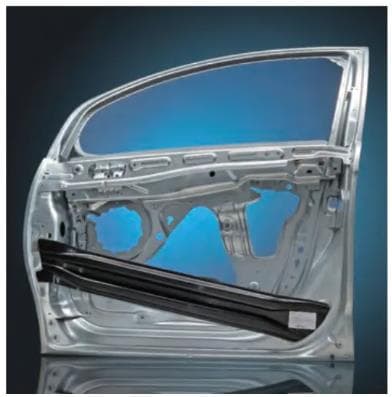
The bond between different materials is crucial for functional and safety aspects in the automotive industry.
The requirements of the automotive industry are clear: the gluing process must be fast, reliable and automated.
Table 1 lists the three most common methods for connecting composite materials and metal components in industrial processes, among which laser welding may be the latest method, but it still needs more research and improvement. These issues not only involve efficiency, but also involve the strength and aging of the connecting parts. This article will discuss these questions in detail.
Table 1: Connection methods for composite materials
Mechanical Fixation | Adhesive bonding | laser welding |
Benefits:
– Fast and cheap process – Mature technology |
Benefits:
– Various stickers for different applications – Suitable for connecting composite materials |
Benefits:
– Fast and reliable process – High joint strength – No additional materials required |
Disadvantages:
– Holes can compromise the strength of fibers and composite materials – Additional weight of fasteners |
Disadvantages:
– Requires extensive surface preparation – Long processing time – Requires additional materials |
Disadvantages:
– Specialized equipment required – Limited to thermoplastic materials |
Basics of laser welding technology
The hidden laser welding process for connecting composite materials and metal parts mainly consists of two steps. In the first step, the metal part is treated with a laser to form a microstructure on its surface.
This process can be achieved using a continuous wave single-mode fiber laser with a nominal power of about 1 kW. The laser scans the surface of the metal part to form a regular groove with a cutting edge geometry (see Figure 2).
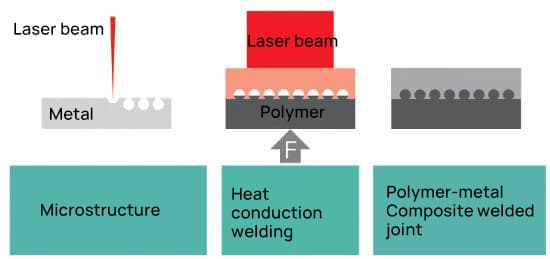
Due to the high intensity of the laser beam, the metal partially melts and vaporizes during the ablation process. The evaporative pressure pulverizes the material, and part of the splashed material solidifies at the edge of the groove, forming a certain degree of sharp edge structure in the groove.
To make the polymer bond more closely to the metal surface, the density of the surface microstructure can be increased, for example, by scanning the grooves with the laser beam at a 90° angle (see Figure 3).
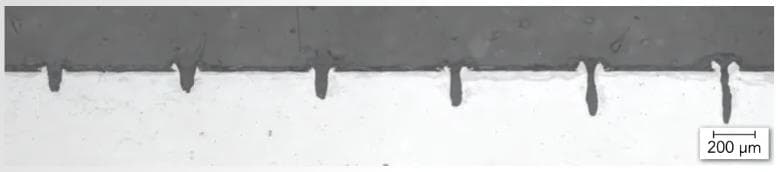
There is another process that can achieve this superficial structuring. This process can be carried out using ultrashort pulse (USP) lasers to create a sponge-like surface structure with tapered protrusions.
This surface structure can be obtained from various materials, such as steel, aluminum, silicon and titanium. The adhesion of the polymer to this surface is better than that of the microstructure produced by fiber laser processing. The only problem is that the processing speed of USP lasers is slower.
Since USP lasers reach mid-kilowatt level power (as expected in another Fraunhofer project), they may be a better choice for microstructuring metal surfaces used for bonding composite materials.
In the second stage of connecting composite materials with metal parts, the polymer is heated until it melts.
Then, the polymer is pressed into the microstructure of the surface of the metal part and, after cooling, a good bond is achieved between the polymer and the metal part.
There are different methods for heating the polymer: one method involves heating the polymer (as in traditional injection molding) and then pressing it into the groove, while another method involves heating the metal part and pressing it onto the cold polymer.
Heat conduction causes the polymer to melt and flow into the microstructure on the surface of the metal part. Both methods can form a polymer-metal composite connection.
The first step of laser microstructuring is a quick, non-contact process. The actual connection process can be easily integrated into existing production processes such as injection molding or stamping. Therefore, the laser welding method is generally a fast and economical process, suitable for mass production.
Mechanical Stress Test
In practical applications, metal-polymer connected composite parts may be subjected to multiaxial, in-phase or out-of-phase loads. For all applications, several questions arise: how much pressure can this joint withstand? Where will it break? What does this mean for the connection process?
Experts at Fraunhofer ILT in Germany carried out a series of pressure tests using different materials to answer these questions (see Figure 4). In one case, they made a test specimen composed of a 1.5 mm thick stainless steel plate and a 3 mm thick glass fiber reinforced polypropylene (PP) strip for tensile and shear testing, and an unreinforced PP for tensile testing.
The metal surface was processed with a single-mode fiber laser with a nominal power of 1 kW and a focused diameter of about 40 μm to form a reproducible cutting edge groove structure. The polymer part was heated with a 3 kW semiconductor laser (power of about 300-700 W), with a spot size of 7.5×25 mm 2 . The two pieces were fixed together with a clamping pressure of 3 bar, and the connection area of the tensile-shear specimen (steel + PP) was 150 mm 2 while that of the tensile specimen (steel + PP) was 100 mm 2 .
Five specimens of each type were destructively tested. The connection strength of the microstructure with a groove spacing of 400 μm was tested under a tensile and shear load of 13.1 MPa, and the connection strength with a groove spacing of 300 μm was measured under a tensile and shear load of 15.5 MPa. In the tensile load test, the specimens withstood loads of 5.1 MPa (spacing between grooves of 400 μm) and 9.1 MPa (spacing between grooves of 300 μm), respectively.
Of course, dense microstructures have better adhesion, but it should be noted that dense microstructures will increase the processing time.
The researchers performed similar tests on magnesium alloy plates. All test results showed that laser welding technology can establish a strong and reliable connection between metal and polymer parts.
Aging test
Another question in automobile production is whether such connections can meet the requirements of climate change and corrosion.
To answer this question, researchers performed several tests. They performed standard climate change tests on composite connection samples according to VW PV 1200, with temperature ranging from 80-40°C.
A test cycle lasted 12 hours, repeated for 2, 10 and 30 cycles. Destructive tensile and shear strength tests were performed on the samples before and after climate change testing.
All test results showed that the samples could withstand pressure values between 8-15 MPa. An interesting phenomenon occurred outside the gluing area during the test.
After repeating the test for 30 cycles, parts outside the bonding area failed the strength test. In other words, the bonding area was even stronger than that of the original polypropylene material.
This phenomenon was even more pronounced in the corrosion test. The salt spray test was carried out for 7 days according to VDA62I-415. The test included salt spray and high humidity conditions. Before testing, all specimens could withstand forces of about 8 MPa and 15 MPa.
After the corrosion test, all PP/T40 materials broke outside the bonding area, while the GFRP materials broke inside the bonding area, but with greater strength than before corrosion. The steel specimens showed rust, mainly in the microstructure area.
There was obvious corrosion penetration into the bond area, but this did not significantly affect the bond strength. The microstructure area outside the aluminum plate bonding area also showed signs of corrosion, but not within the bonding area. A straightforward conclusion is that any open areas of microstructure in the metal should be avoided.
Tests have shown that laser connection technology can establish highly reliable connections between metal plates and plastics.
Standard weather and corrosion tests did not affect bond strength. After a period of aging, the plastic itself, not the bonding area, broke down. Open areas of microstructure in the metal should be avoided.