1. Fiber optic sensors
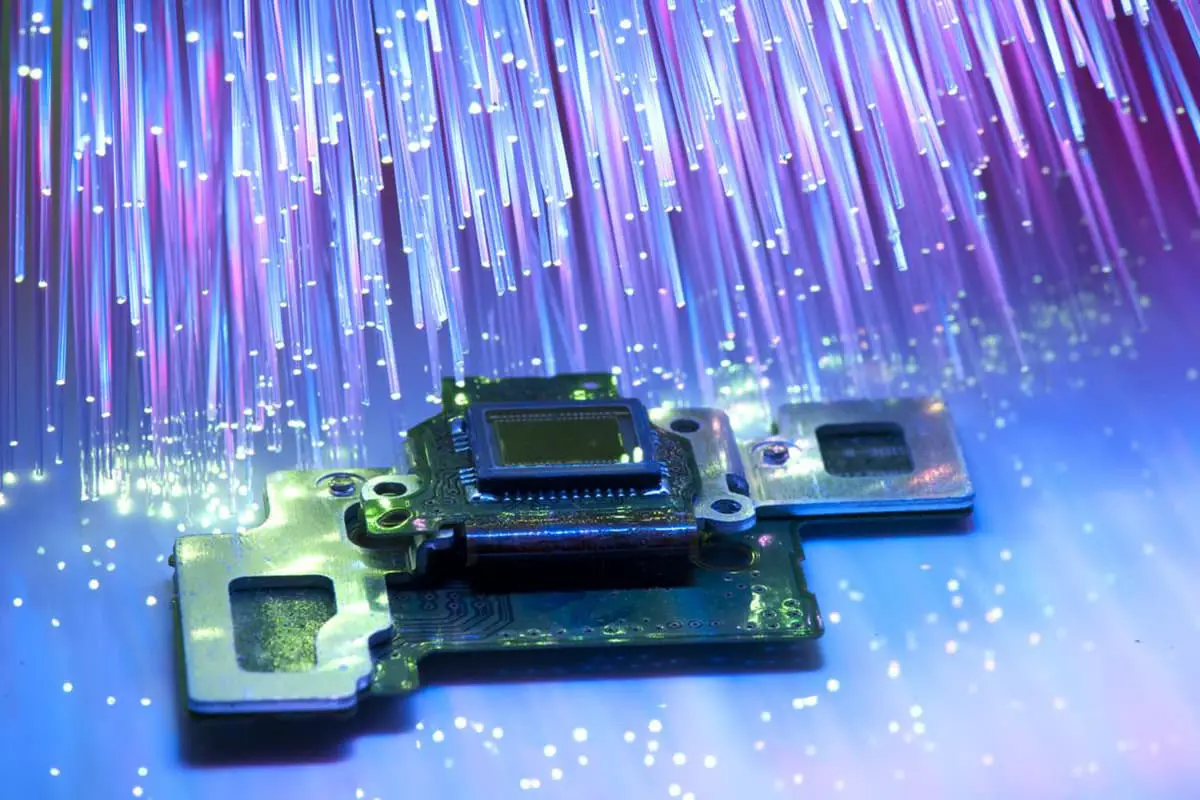
Fiber optic sensors are devices that transform the state of an object being measured into a detectable optical signal.
The working principle of a fiber optic sensor is to direct light from a source through an optical fiber to a modulator.
Inside the modulator, light interacts with the external parameters being measured, causing changes in optical properties such as intensity, wavelength, frequency, phase and polarization state.
This results in a modulated optical signal, which is then transmitted through the optical fiber to photonic devices and, after demodulation, produces the measured parameter. Throughout the process, the light beam is channeled in and out of the modulator through optical fiber.
The main function of optical fiber is to transmit the light beam and, secondly, to function as a light modulator.
Compared to traditional sensors, fiber optic sensors have several unique advantages. They use light as a carrier of sensitive information and optical fiber as a means of transmitting this information.
This gives them characteristics of both fiber optics and optical measurements, such as excellent electrical isolation, strong resistance to electromagnetic interference, non-invasiveness, high sensitivity, long-distance monitoring capability, corrosion resistance, explosion-proof properties, and flexible light. paths that are easily connected to computers.
Sensors are evolving to be more sensitive, accurate, adaptable, compact and intelligent. They can operate in places inaccessible to humans, such as high temperature areas or dangerous zones such as radiation areas, serving as extensions of our senses.
Furthermore, they can exceed human physiological limits, capturing external information that goes beyond our sensory perceptions.
2. Photoelectric sensors
Photoelectric sensors are devices that convert optical signals into electrical signals. Its operation is based on the photoelectric effect.
The photoelectric effect refers to the phenomenon in which electrons in certain materials absorb the energy of photons and produce a corresponding electrical effect.
The photoelectric effect is categorized into three types: external photoelectric effect, internal photoelectric effect and photovoltaic effect.
Photonic devices include phototubes, photomultiplier tubes, photoresistors, photodiodes, phototransistors, and solar cells, among others. The performance and characteristic curves of these devices were analyzed.
Photoelectric sensors use photonic devices as conversion components. They can detect non-electrical physical quantities that directly cause changes in light quantities, such as light intensity, illumination, radiometric temperature measurement and gas composition analysis.
They can also detect other non-electrical quantities that can be converted into changes in light quantities, such as part diameter, surface roughness, deformation, displacement, vibration, speed, acceleration, as well as the shape of objects and the identification of their functioning. status.
Photoelectric sensors are non-contact, fast-response and reliable, making them widely used in industrial automation and robotics.
The continuous emergence of new photonic devices, especially the advent of CCD image sensors, has opened a new chapter for the further application of photoelectric sensors.
3. What are the differences between fiber optic sensors and photoelectric sensors?
Both fiber optic sensors and photoelectric sensors serve as two typical sensors widely used in production measurements.
The distinctions between them will be analyzed in terms of principles and applications.
(i) Principles:
(1) Photoelectric sensors:
These sensors use photoelectric components as detection elements. They first convert the measured changes into changes in the optical signals and then use the photoelectric components to further transform the optical signals into electrical ones.
Photoelectric sensors generally consist of a light source, an optical path, and photoelectric components.
(2) Fiber optic sensors:
These sensors transmit light from a source through optical fibers to a modulator.
The parameters to be measured interact with the light entering the modulation region, leading to changes in optical properties such as intensity, wavelength, frequency, phase and polarization state.
This is known as modulated signal light. After being transmitted through optical fibers to a light detector and demodulated, the measured parameters are obtained.
(ii) Applications:
(1) Applications of photoelectric sensors:
Dust Turbidity Monitoring:
One of the vital tasks for environmental protection is to prevent industrial dust pollution. To mitigate industrial dust pollution, it is necessary to first determine the amount of dust emitted, and it is necessary to monitor smoke and dust sources for automatic display and exceed alarm limits.
Flue gas turbidity is detected by the change in light transmission within the chimney. If the turbidity increases, the light emitted by the light source is absorbed and refracted further by the dust particles, reducing the light reaching the detector.
Consequently, the intensity of the light detector output signal may reflect changes in the turbidity of the stack.
Use of Photocells in Photodetection and Automatic Control:
When used for photodetection, the basic principle of a photocell is similar to that of a photodiode.
However, their fundamental structures and manufacturing processes are not entirely identical.
Photocells do not require external voltage during operation; they have high photoelectric conversion efficiency, wide spectral range, good frequency characteristics and low noise.
Thus, they are widely used in photoelectric reading, optoelectronic coupling, optical grating ranging, laser collimation, film sound reproduction, UV light monitors, and flame protection devices for gas turbines.
(2) Applications of fiber optic sensors:
Fiber optic sensors are employed to measure various physical quantities, such as insulator contamination, magnetism, sound, pressure, temperature, acceleration, gyroscopes, displacement, liquid level, torque, photoacoustic effects, current and strain.