
1. Operating procedures
- Follow safety standards for machine tool workers and use necessary protective equipment.
- Check the front support frame, rear retaining frame, and ram for foreign objects and remove them if present to avoid possible safety hazards.
- Check the alignment and stability of the upper and lower molds, and verify that each positioning device meets the processing requirements.
- Before beginning, thoroughly clean the upper and lower production models and remove any foreign objects, such as iron ballast, from the notch to avoid damaging the models and affecting accuracy.
- Before starting, carefully inspect the engine, switch, wires, and ground for any problems, and verify that the equipment's operating parts and buttons are in the correct position.
- If the upper ram and positioning axes are not at the origin, perform the procedure to return them to the origin.
- After starting the machine, let it idle for 1-2 minutes and move the ram through a full stroke 2-3 times. If any abnormal sound or fault occurs, stop the machine immediately, solve the problem and only continue operation after everything is normal.
- Select the correct die based on the board thickness. Generally, the opening size should be 6 to 10 times the thickness of the board, and for boards less than 2 mm, it should be 6 to 8 times.
- Have one person in charge of supervising the operation to ensure close cooperation with the feeding and pressing personnel and to ensure that all personnel are in a safe position before sending the bend signal.
- When processing narrow broken plates, reduce the system pressure to avoid cracks in the notch of the production model.
- Before bending, adjust the gap between the upper and lower production models so that they are equal.
- During bending, the person responsible for the operation must not place their hands in the production mold room and narrow, long or small materials must not be supported with their hands. Fold only one piece of material at a time and do not fold multiple pieces simultaneously.
- Check the oil level in the tank and refill with hydraulic oil of the same model if necessary. Start the machine and check the hydraulic piping or oil pump for problems.
- If an abnormality occurs, stop the machine immediately, investigate the cause and resolve it immediately. Do not operate the machine while injured, as this will worsen the problem.
- The person responsible for the operation must undergo specialized training and the company must assign a designated operator to the machine to ensure proper protection and maintenance.
- Compact the sheet material during bending to prevent warping and possible damage.
- Cut off the power when pressing the die and only do this after stopping the operation.
- When changing the opening of the variable lower die, do not allow any material to contact the lower die.
- Do not stand behind the machine tool while it is in operation.
- Do not bend the boards at just one end.
- If a mold problem is discovered during operation, stop and correct it. Do not make corrections manually during operation to avoid injury.
- Do not bend thick iron plates, hardened steel plates, high-quality alloy steels, square steels or plates that exceed the performance of the plate bending machine to avoid damage to the machine.
- Regularly check the alignment of the upper and lower molds and the pressure gauge indication.
- Before shutting down, place wooden blocks on the lower die below the oil cylinders on both sides and lower the upper ram onto the wooden block or lower the upper die to the bottom of the lower die opening.
- After work, turn off the oil pump and power supply.
- It is prohibited to bend thick iron plates, hardened steel plates, high-quality alloy steels, square steels or plates that exceed the performance of the plate bending machine.
- Ensure the safety of all personnel by always following proper operating procedures and guidelines.
2. Precautions
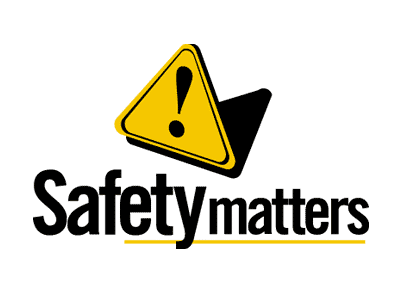
Precautions before operation:
- Before starting the machine, inspect the oil circuit, oil cup and oil level according to the lubrication table to ensure that the oil is of good quality and the oil circuit is clean.
- Check that all parts are in good condition, that the upper and lower dies are in the correct position, and that the oil pump motor is operating normally.
- After turning on the oil pump, let it run under air pressure for 3 to 5 minutes and confirm that the equipment is working properly.
Precautions for operation:
- During operation, the part to be pressed must be positioned in the center of the upper and lower dies and parallel to them, and placed securely. No adjustments or repairs to the dies should be made during operation.
- When pressing long or large parts, two or more people must be involved to prevent the part from falling or deforming during pressure release. Clamping the ends of the part being pressed is not allowed.
- When changing or pressing the part, it must be positioned in the center of the dies without any inclination. The upper die must be approached slowly to prevent the workpiece from jumping.
- Always check whether the strokes of the two oil cylinders are consistent during operation and make adjustments or report for repair if necessary. If the oil cylinder piston wobbles or the oil pump makes a loud noise, the air in the oil circuit must be removed.
- Regularly monitor the oil tank to ensure the oil level is adequate. If the oil level is too high, inspect the oil return piping and adjust the oil return valve. It is strictly prohibited to overfill the oil tank. The working oil temperature must not exceed 45°C.
- If the control valve, safety valve or safety protection device fails, operation must not continue.
- The operator must secure the adjusting valve and pressure gauge after making any adjustments, and other people must not move or adjust them.
- If the working pressure is too high, the valve must be checked and adjusted, and operation can only be resumed when the problem has been resolved.
- The upper die must not exceed its maximum stroke.
- No hands should be placed between the upper and lower dies during operation.
- Regularly check the machine's travel to ensure key security.
- Turn off the oil pump when adjusting dies or performing maintenance to ensure safety.
Shutdown precautions:
- Before turning off the machine, the dies must be closed. Follow these steps to shut down: first turn off the running oil pump, then turn off the control power supply, and finally turn off the main power supply.
- After completing work, clean the machine and surrounding work area and store the workpiece in the designated location.
3. Maintenance

1. Hydraulic oil circuit
The. Inspect the oil level in the oil tank once a week. If the level is below the oil window, add hydraulic oil.
B. The recommended hydraulic oil for this machine is ISO HM46 or Mobil DTE25.
w. The oil in a new machine should be changed after 2,000 hours of use and should be changed again after 4,000 to 6,000 hours of use. Each time the oil is changed, the oil tank must be cleaned.
d. The oil temperature in the system must be between 35°C and 60°C and must not exceed 70°C. If the temperature is too high, it can cause deterioration and damage to the oil quality and components.
2. Filter
The. Every time you change your oil, the filter should be replaced or thoroughly cleaned.
B. If the machine tool gives an alarm or other indication of dirty oil, the filter must be replaced.
w. Inspect and clean the oil tank air filter every three months, and it is recommended to replace it once a year.
3. Hydraulic components
The. Clean hydraulic components (base plate, valve, motor, pump, oil pipe, etc.) every month to avoid contamination. Do not use soap or other cleaning agents.
B. After the machine has been in use for a month, inspect the bend of each oil pipe to see if there are any deformities. If any are found, replace the tube. After two months of use, tighten all accessory connections. Carry out this maintenance with the machine turned off and without pressure in the system.