Welding robots mainly consist of the robot body, control cabinet (including hardware and software) and automated welding equipment.
For example, automated welding equipment for arc welding and spot welding includes welding power source (with its control system), wire feeder (for arc welding), welding torch (collet), among others.
When technicians operate welding robots, shouldn't some safety precautions be taken?
For example, it is essential to choose the correct and reasonable location for the welding robot setup.
Welding robots contain many high-precision components, especially their control cabinets. Despite excellent dust protection, an unsuitable installation environment can still reduce the robot's lifespan.
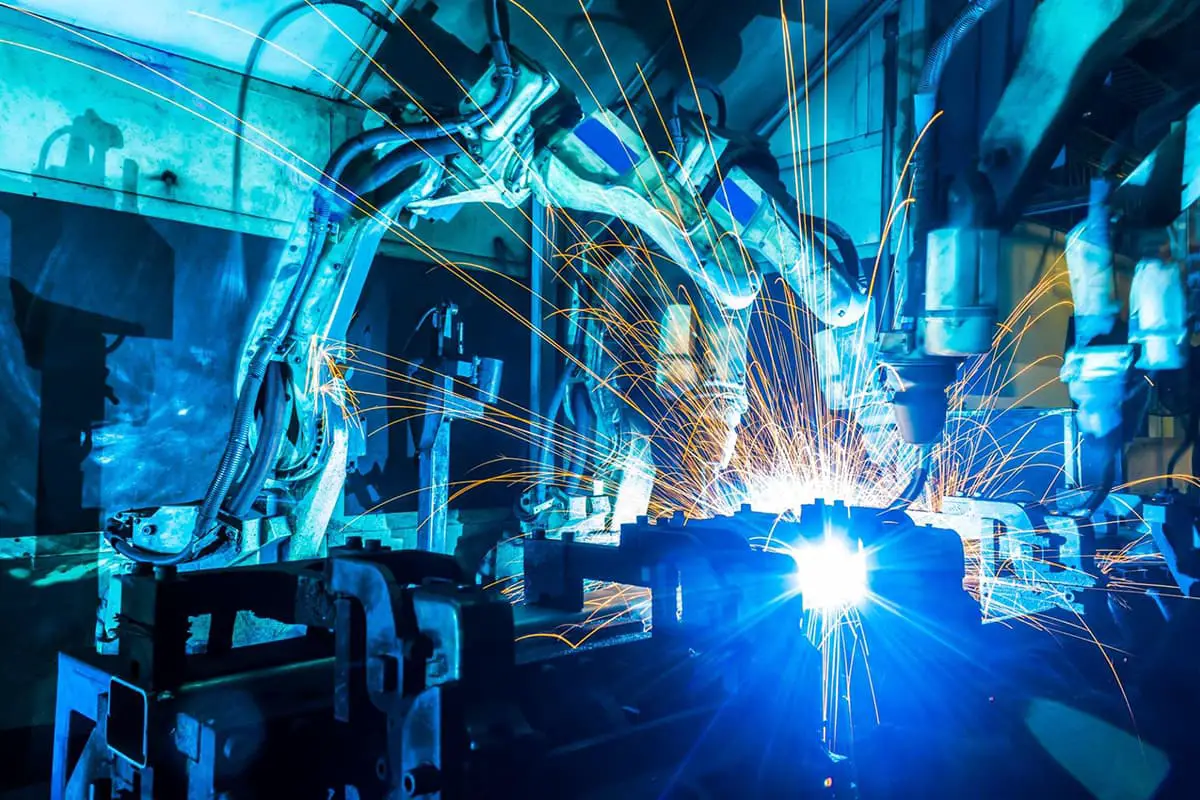
I. Precautions for operating welding robots
1. Before calling, confirm the following:
a) The robot's safety barrier is not damaged.
b) Technicians are properly dressed in work attire as required.
c) Protective equipment (safety helmets, safety shoes, etc.) is available in the production workshop.
d) The welding robot, control box and control cables are not damaged.
e) Automatic welding machines (such as Fronius or Lincoln welders) and welding cables are not damaged.
f) Safety devices (emergency stop, safety lock, wiring, etc.) are not damaged.
2. Before teaching the welding robot, confirm that there are no noises or abnormal conditions:
a) Manually operate the welding robot to confirm that there is no noise or abnormal conditions.
b) Press the emergency stop button while the servo power is on to confirm that the robot servo power can be cut off correctly.
c) Release the lever on the back of the teaching box while the servo power is on to confirm that the robot servo power can be correctly cut off.
3. During the welding robot teaching operation, confirm the following:
a) Ensure that the operator can immediately exit the robot's range of motion during teaching operations.
b) When operating the welding robot, face the robot as much as possible (do not take your eyes off the robot).
c) Try to avoid being within the range of motion of the robot when it is not operating.
d) When not operating the welding robot, press the emergency stop button to stop its operation.
e) When safety measures, such as robot safety barriers, are in place, an assistant must be present to monitor. Avoid operating the welding robot when the monitor is not present.
II. Precautions for automatic operation of welding robots
1. Before automatic operation, confirm the following:
I. There are no personnel inside the robot's security fence;
ii. The correct program number to be regenerated is set;
iii. The welding robot is in the normal moving position;
4. The teaching box is in the appropriate position;
v. There are no tools or other objects within the welding robot's range of motion;
saw. The movement speed of the welding robot (including overtaking) is appropriate;
viii. The welding robot can stop urgently when safety devices (such as emergency stop) are triggered;
viii. The state is ready to press the emergency stop button at any time;
Ix. If welding is required, a protective welding mask is prepared before welding.
2. During automatic operation, observe the following:
I. If there is any abnormality or feeling of insecurity, immediately press the emergency stop button;
ii. Do not stay within the robot's safety fence or within the welding robot's working range;
iii. Do not put your hand or tools into openings in the robot's safety fence.
3. After automatic operation, confirm the following:
I. After automatic operation, press the emergency stop button to stop the welding robot;
ii. Before entering the robot safety fence, change the operation mode to manual mode (teaching mode). Furthermore, the welding robot must stop working when the emergency stop button is pressed;
iii. If there is welding, do not directly touch the welding part.
III. Wrap it up
In conclusion, the welding robot is a key equipment involved in welding production operations. Technical personnel must undergo systematic professional training before they can work in it.