Nowadays, many factories extensively use laser plasma cutting machines due to their high cutting efficiency and superior cutting quality, winning the approval of countless companies and customers.
However, during plasma cutting, harmful substances are produced, causing air and noise pollution.
Dust generated by plasma cutting must be collected and filtered through purification equipment in accordance with environmental protection requirements.
In this article, I will guide you in understanding the dangers of plasma cutting dust and its purification solutions.
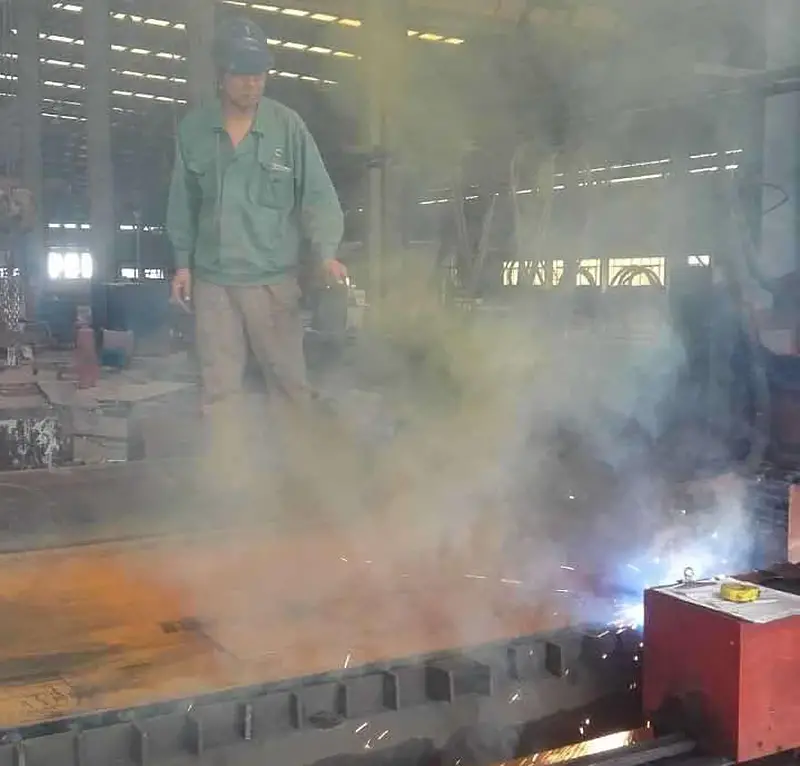
What is the dust produced by plasma cutting machines?
Plasma cutting machines, known for their high cutting efficiency and wide cutting range, have a disadvantage – they generate significant amounts of dust during operation.
This dust, similar to welding fumes, is mainly made up of harmful gases and tiny dust particles, including CO, C2, H2, Nx and hydrocarbons.
Specific hazards of metal dust
Here is a detailed description of the specific hazards posed by metal dust produced during cutting:
- Ozone is a colorless, harmful gas with a distinct irritating smell. Strongly stimulates the respiratory tract and lungs. Short-term inhalation of low concentration ozone (0.4mg/m3) can cause symptoms such as coughing, dry throat, chest tightness, loss of appetite and fatigue. Long-term inhalation can cause bronchitis, emphysema and pulmonary fibrosis.
- Carbon monoxide is a colorless, odorless, non-irritating gas that easily binds to hemoglobin in the human body. Thus, when a large amount of hemoglobin binds to carbon monoxide, it can potentially lead to tissue necrosis due to oxygen deprivation.
- Plasma light radiation is intense, mainly composed of ultraviolet radiation, visible light radiation and infrared radiation. Particularly, the ultraviolet intensity, such as wavelengths of 260-290μm, is 2.2 times that of argon arc welding. In addition to light radiation, there are other hazards such as toxic gases from dust, high-intensity and high-frequency noise, and high-frequency oscillations that can cause harm to the human body.
- Nitrogen oxides are a toxic gas with an irritating odor, mainly composed of nitrogen dioxide. It is a reddish-brown gas with a characteristic smell. Once inhaled, it enters the lung alveoli through the upper respiratory tract and gradually interacts with water, causing severe irritation and corrosion to lung tissue, leading to pulmonary edema.
Workers involved in cutting have noticed that when using plasma cutting machines to cut 3 to 6 mm carbon steel plates, a lot of yellow smoke is generated. This yellow smoke poses a significant threat to human health and can easily cause pneumoconiosis if inhaled for long periods.
Given these hazards associated with plasma cutting dust, it is crucial to implement effective dust purification when carrying out plasma cutting work to reduce the incidence of occupational illnesses.
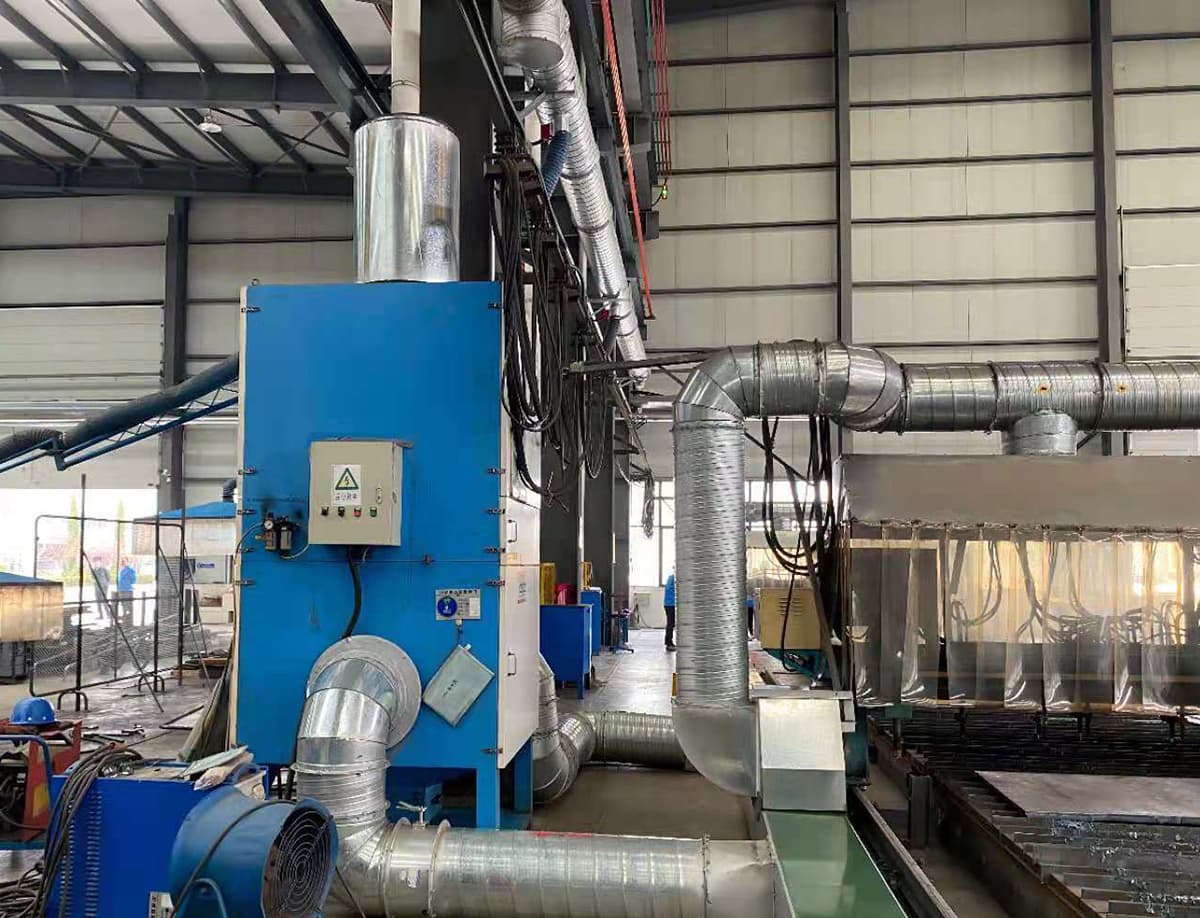
How harmful is the dust produced by plasma cutting machines?
Harms the Operator's Health
The dust produced by plasma cutting machines contains many inhalable substances (such as manganese oxide and potassium and sodium oxides). Once these substances enter the human body, they can cause significant harm.
Workers who spend a lot of time working in dusty conditions from CNC plasma cutting machines have a significantly higher proportion of respiratory illnesses, such as chronic bronchitis, than others.
Furthermore, these inhalable substances can accumulate in the body's bones and blood, leading to a decrease in their function and can even cause cancer.
Impacts business benefits
Environmental protection has become an international and national trend. Dust pollution can result in fines for companies.
Furthermore, failure to promptly manage dust pollution can affect the accuracy of production machines, thereby impacting production efficiency.
Given these two main reasons, the dust risks from plasma cutting machines are significant and require timely purification treatment. So how should dust from plasma cutting machines be managed?
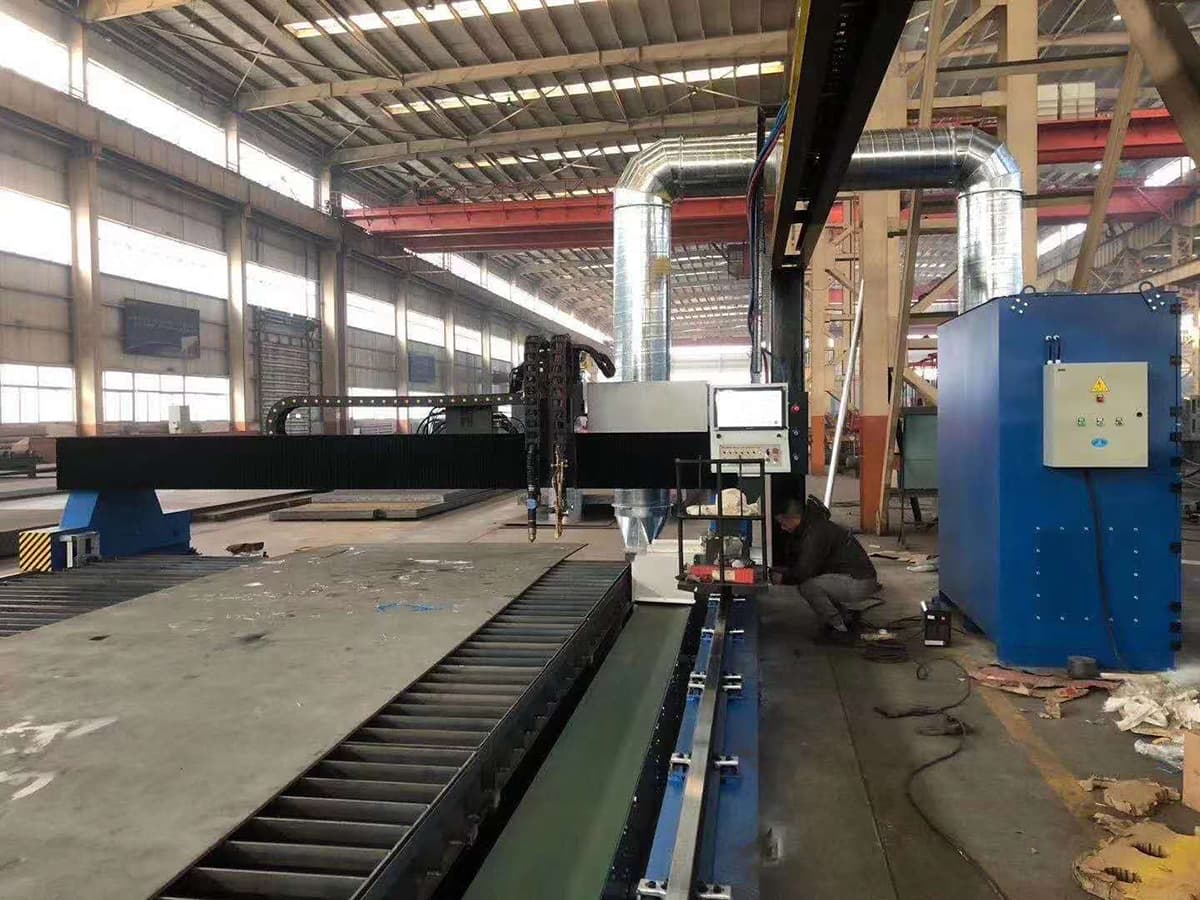
Dust purification solutions for plasma cutting equipment
Currently, there are two main methods for managing plasma cutting dust:
- Wet dust removal method
This method involves installing a water bed under the cutting deck, allowing the part to be submerged in water. Cutting is carried out underwater, so the oxides produced during cutting are collected by the water, thus purifying the working environment. This method only requires a water holding container as a one-time investment.
However, it can lead to secondary pollution (water pollution) and metal oxides are likely to clump underwater, making cleaning a challenge. For users in colder regions, the water on the cutting deck can freeze during the winter, causing problems.
Furthermore, this method is not suitable for purifying dust from metals such as aluminum and magnesium, which produce explosive dust during cutting.
- Dry dust removal method
Dry dust removal involves adding a dust capture device to the CNC cutting platform. The captured dust is transported directly to a dust filter and purification device. After treatment, the purified air is then discharged.
Dust produced during plasma cutting is mainly formed below the cut of the part, making exhaust-type negative pressure cutting decks the most common dust capture device. Due to its simple structure, reliable operation and effective dust removal, the dry dust removal method is widely used.
The dust collector for a plasma cutting machine is designed and manufactured based on the machine's specifications, focusing on economic efficiency, easy maintenance, economical operation and minimum subsequent costs, while ensuring effective dust removal.
Depending on the width of the cutting work platform, it can be divided into a single-side pneumatic door style workbench and a double-side pneumatic door style workbench.
Plasma Cutting Machine Dust Collector Workflow
The objective is to collect the dust produced during plasma cutting. The collection method can be side suction, bottom suction or top suction, with the dust directly sucked into the pipeline by the fan. A dust removal device is added to the end of the pipeline, and the collected dust is directly purified by the dust removal equipment before being discharged inside or outside the workshop. Within the designed air volume, the purified powder can meet environmental emission requirements.
The dust removal system of blow-suction type plasma cutting machine
The blow and suction type plasma cutting machine dust removal system involves placing a square suction duct on one side of the cutting platform, which has a suction port that can move with the cutting machine.
Related Reading: CNC Plasma Cutting Dust Removal: Explained
On the other side of the cutting deck is a ventilation port with a small axial flow fan. The suction port and blower port are fixed on the cutting machine and kept consistent with the cutting head.
The lower part of the cutting platform is equipped with an exhaust duct with vertical plates, which ensures that suction occurs at the place where dust is generated within a limited width during cutting. When the dust removal system of the plasma cutting machine operates, the sealing strip can closely adhere to the top of the square suction duct under the effect of the negative pressure of the pipeline to play a sealing role.
The suction port has two rollers where the sealing strip is lifted, allowing smoke to enter through the suction duct of the suction port, and then be sucked into the dust removal equipment for filtration and purification.
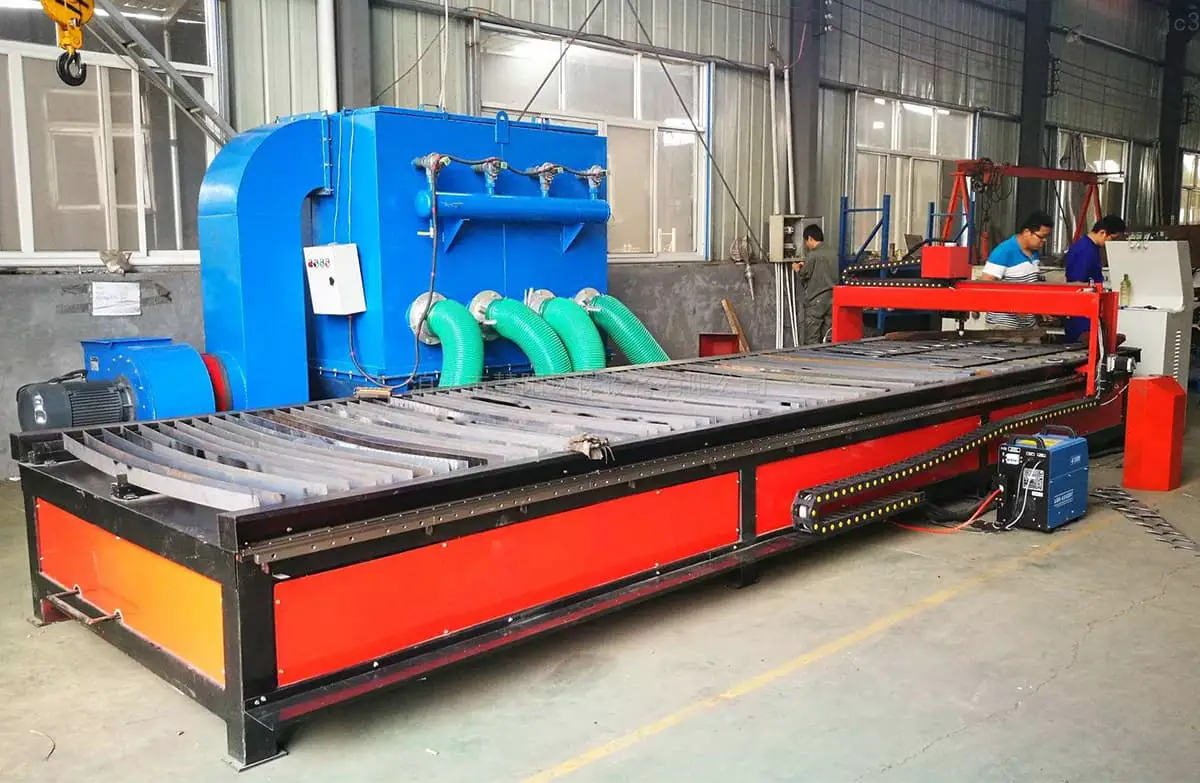
What are the dangers of plasma cutting?
Plasma cutting can pose several dangers:
- Exposure to arc light during the cutting process can result in eye injuries;
- A substantial amount of harmful gases are generated during the cutting process. Once inhaled, they can have harmful effects on health;
- Sparks thrown during the cutting process can cause burns to the skin;
- The process often generates high-frequency noises, which can damage your ears over time;
- Another significant point is that the high frequencies and electromagnetic radiation generated by the high-frequency oscillator during plasma cutting can cause bodily harm. Long-term exposure can cause serious harm to workers in the field.
Damage caused by plasma cutting can be divided into two categories:
- Short-term direct damage: The arc of plasma light can seriously stimulate the eyes, causing eye damage, mainly due to the infrared and ultraviolet radiation emitted by the metal.
- Long-term indirect damage: The radiation generated by the plasma arc can affect cell division in the long term, leading to various health problems. Inhalation of smoke or gases generated during the process, and the metal oxides and metal vapors that enter the lungs, can stimulate the respiratory tract and potentially cause pathological changes over time.
Safety Considerations for Plasma Cutting Machines
The harmful factors in plasma arc cutting mainly include harmful gases, metal dust, noise, arc light radiation (infrared) and high-frequency electromagnetic fields. The main risk is electric shock.
Therefore, it is essential to prioritize safety and security during plasma arc cutting.
1. Electric shock prevention
The no-load voltage of the plasma arc cutting power supply is relatively high, especially during manual operation, posing a risk of electric shock. Therefore, the power supply must be properly grounded during use, and the cutting torch and areas touched by hands must be reliably isolated.
A lower voltage can be used to ignite the non-transferred arc before connecting the higher voltage transferred arc circuit. If the key is placed on the handle, an insulating rubber cover must be applied to cover the exposed key to prevent direct hand contact with the key. Whenever possible, automated operation is encouraged.
2. Arc light radiation prevention
The intensity of arc light radiation is high, mainly consisting of infrared radiation and visible light radiation. The light radiation from plasma arcs is stronger than other arcs, especially ultraviolet light, which can seriously damage the skin. During manual cutting, operators must wear suitable masks and gloves and also protect their necks.
In addition to wearing sunglasses with your mask, it is best to include lenses that absorb ultraviolet light. During automatic operation, a protective screen can be installed between the operator and the operating area. Plasma arc cutting can be carried out underwater, using water to absorb light radiation.
3. Dust and smoke prevention
The plasma arc cutting process accompanies large amounts of vaporized metal vapor, ozone, nitrogen compounds, etc. Combined with the large airflow during cutting, dust in the workplace can be raised massively, causing serious impacts on the operator's respiratory tract and lungs.
Therefore, the workspace must be equipped with good ventilation equipment and dust prevention measures. When cutting, an exhaust device can be installed below the grid worktable or underwater cutting can be used to reduce dust.
4. Noise prevention
High-intensity and high-frequency noise is generated during plasma arc cutting, especially when using high-power plasma arc cutting, the noise is even louder. This can significantly affect the operator's auditory and nervous system. The noise level mainly depends on the cutting current; the greater the current, the stronger the noise.
When noise energy is concentrated in the 2000 to 8000 Hz range, operators are required to wear ear protection. If possible, try to use automatic cut-off, with the operator working in a soundproof room.
Underwater cutting can also be used, using water to absorb noise. Placing the workpiece underwater for cutting can significantly reduce noise. Test results show that when cutting is carried out underwater, noise is reduced by 22-24dB compared to dry cutting.
Additionally, using a cutting torch with a water curtain (with a water flow rate of 70-80L/min) can reduce noise by about 20dB. When the cutting current is below 100A, the noise is relatively low and the impact on the surrounding environment is not significant.
5. High frequency electromagnetic field protection
Plasma arc cutting requires a high frequency oscillator to ignite the arc. However, high frequency may cause some harm to the human body.
Preventive measures mainly include:
- Select an arc ignition frequency between 20-60Hz, shield the high-frequency oscillator with a shield, ensuring a good grounding connection to the part;
- Cut off power to the high-frequency oscillator immediately after ignition of the main electric arc;
- Minimizing time when using high frequency sparks to check the center of the electrode pair.
Plasma Arc Cutting Protection Tips
- Avoid looking directly at the cutting arc during the plasma cutting process, wear professional protective glasses to prevent the arc light from burning your eyes.
- Large amounts of toxic gases are produced during the plasma arc cutting process; a multi-layer filtered dust mask must be worn.
- Towels, gloves, foot protectors and other protective equipment must be used during the plasma arc cutting process to avoid splashing sparks that burn the skin.
Safety Precautions
The following safety precautions must be observed when using a plasma cutting machine:
Grounding is required: The plasma cutting machine must be grounded to ensure safety.
Electric shock prevention: Measures must be taken to prevent electrical shock from all components and gas pipes of the mower to protect users.
Oxygen safety: Care must be taken when using oxygen to avoid leaks and accidents.
Avoiding gas poisoning: Improper use of gas indoors can cause poisoning. Choose a well-ventilated space and change the air regularly when using gases.
Keep a safe distance: Keep a safe distance during operation to avoid accidents during cutting.
Wear protective equipment: When operating a plasma cutter, wear safety equipment such as protective mask, insulating gloves, fire- and explosion-resistant work clothes, and shoes to ensure personal safety.
Avoid cutting dust: Plasma cutting machines generate a lot of dust, so protective glasses and masks should be worn to protect the eyes and respiratory system.
Follow standard procedures: Follow the standard operating procedures of the plasma cutter, strictly follow the instruction manual to avoid operational errors and accidents.