1. What is fiber cement board?
Fiber cement board is a new type of building material formed from natural fiber and cement through pulping, molding, cutting, pressing and curing processes.
It has light weight, high strength, water resistance, fire resistance, deterioration resistance, large size, good workability and higher construction efficiency.
It is widely used in residential and industrial buildings. It can be applied to interior walls, exterior wall panels, ceiling panels, curtain wall coverings, composite wall panels, insulation materials, sound-absorbing barriers and roof installations.
2. Uses of fiber cement board
Fiber cement board is a composite material made from sand, cement and plant fibers. It comes in several visual variations, including cross grain, wood grain, wall guard, and oval surface designs.
Available in block form, the board can be used in attic floors, wall cladding, soffit/eaves panels or as a base layer under bathroom tiles. It can not only serve as an external wall cladding, but also as a fire panel.
3. Fiber cement board price
What factors determine the price of fiber cement sheets?
By adding fibers to high-quality cement substrates, the cracking resistance and brittleness of the material can be improved, increasing its deformation capacity.
The type, length, cross-sectional dimensions and bonding characteristics of the fiber with the cement substrate will influence the macro performance of the fiber cement board material.
Fiber cement boards can be formed through various methods such as conventional casting, papermaking, mold pressing, extrusion and more. The training method usually has some impact on your performance.
Different raw materials and production processes determine the price of fiber cement boards, along with the inherent properties of the boards themselves.
Factors affecting the price of fiber cement board raw materials include:
- Component composition: fiber type, cement grade, pulp
- Production process: type of production equipment, whether the production equipment is complete (hydraulic press and its tonnage).
- Post-production care: National regulations require a mandatory seven-day curing period in a designated curing chamber.
4. Fiber cement board production process
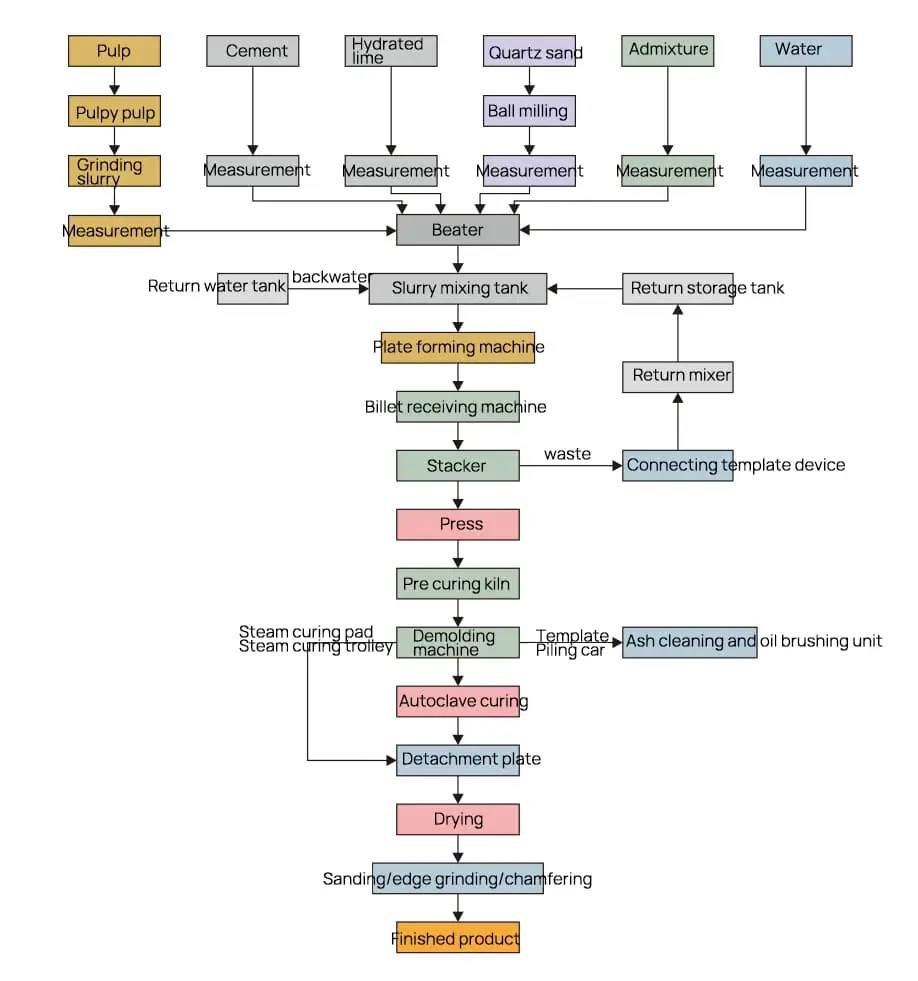
The widely used cement brick pallets are molded from GMT fiberglass materials. This composite material pallet is a replacement for bamboo glue boards, wooden boards, rubber boards and plywood and features wear resistance, impact resistance, vibration resistance, waterproofing, corrosion resistance and anti-aging properties. GMT fiberglass brick pallet molding equipment is specifically the Four Column Hydraulic Press.
The Four Column Hydraulic Press works by leveraging a hydraulic control system to enhance the hydraulic regulating valve. The electrical control system, through the pump, hydraulic cylinder and various hydraulic valves, performs energy conversion, regulation and delivery to complete the entire molding process.
This machine is characterized by its compact structure, agile and reliable operation, fast speed, low power consumption, low noise and the ability to adjust pressure and stroke within a specified range. The operation is simple.
By changing molds, one machine can produce different models of brick pallets and carry out the cement brick pressing process. Common specifications for composite brick pallets are as follows:
1400*1400*30mm, 1350*1150*30mm, 1350*880*28mm, 1250*900*25mm, 1180*880*25mm, 1350*700*30mm, 980*860*22mm, 850*850*20mm, 980* 680*20mm, 1100*560*25mm
The cement brick pallet molding process in a Four Column Hydraulic Press includes:
Grinding and mixing: fiber, felt and plastic are mixed in a weighted proportion. The mixture is then added to a crusher for grinding and mixing.
- Heating and melting: The crushed mixture is added to a heater for melting at a temperature between 600°C-850°C, with a heating time of 6min-10min.
- Compression molding: The heated and melted fiber material is stacked and placed into the mold of Four Column Hydraulic Press. The molding process is completed by applying pressure between 5000MPA-6000MPA.
- Forming: The initially compressed fiber material is placed in a laminating machine to be shaped into fiber plates using the hydraulic press.
Features of molded cement brick pallets:
Using a mixture of crushed fiberglass (hereinafter referred to as “fiber”), felt and plastic, which is then heated to a high temperature and melted, stacked and inserted into a hydraulic composite material molding press for high-pressure compression molding.
After that, it is put into a laminating machine for shaping. The final fiber boards, in addition to having the characteristics of conventional fiber boards such as lightness, sound absorption, thermal insulation, environmental friendliness and flame retardancy, have an aesthetic and smooth exterior due to the inclusion of felt and plastic. The plates are also more resistant to wear and pressure, making them less likely to break during use.
Precautions for operating the Four Column Hydraulic Press:
- Proper grounding of the machine is essential and a separate ground is preferred.
- Adjustments to the mold are not permitted while the machine is in operation.
- Hydraulic oil should be N46 anti-wear hydraulic oil or N46 low-spill hydraulic oil, filtered through an 80-100 mesh sieve before use.
- After 200 hours of operation, the cleanliness of the oil must be checked. There should be no strange smell and when a drop of oil is dripped onto white filter paper, there should be no black spots in the central area of the oil trace, otherwise oil replacement will be necessary.
- The press must not be overloaded.
- If there is an unexpected leak in the system, sufficient hydraulic oil should be added after troubleshooting.
- The cleanliness of the pumping station and oil tank of the four-column hydraulic press for 500 ton composite molding should be checked regularly. It is strictly prohibited for water, dust and foreign objects to enter the oil tank.
- When changing functions, all air from the system must be expelled before operation.
- If there are any abnormalities during testing or operation, the machine must be stopped immediately for inspection.
- Holding pressure for 10 minutes allows a pressure drop of 2.5Mpa.
The four-column hydraulic press is also suitable for molding SMC, EMC, GMT, LFT-D and other thermosetting and thermoplastic composite materials. Molded products are efficient, precise, reliable, energy-saving, environmentally friendly and economical.