1. Definition and classification of one-sided welding and double-sided forming
1.1 Definition of single-side welding and double-side forming
Single-sided welding and double-sided forming are essential methods and skills for welders involved in welding pressure vessels, important silos and boilers. It is also used in the manufacture and installation of important welded steel structures that require full penetration but cannot be processed and re-welded on the back of the components.
During this welding, no other auxiliary measures are necessary. However, when welding positioning is required at the groove root, different clearances should be reserved according to different welding methods.
When welding is performed on the front side of the groove, uniform, regular and qualified welds can be obtained on both the front and back sides of the groove. This unconventional welding operation is known as “one-sided welding and two-sided forming”.
1.2 Classification of one-sided welding and two-sided forming
1.2.1 Intermittent arc welding method
To begin the welding process, place the test panel with the slightly gapped end on the left side. Position it for arcing and use a long arc to preheat the welding components for a set period of time. Then press the arc and swing the electrode sideways between the two blunt edges for welding.
As the molten metal from the blunt edge connects with the molten metal from the electrode, listen for the “porphyrin” sound, which indicates a successful bond. The arc light will then be extinguished.
During each continuous arc, the center of the welding electrode must be aligned 2/3 of the way across the welding puddle. This ensures that both sides of the blunt edge are melted at the same time. As soon as the “porphyrin” sound is heard, quickly extinguish the arc, allowing the newly formed weld pool to cover about 2/3 of the previously formed weld pool.
1.2.2 Continuous arc welding method
Continuous arc welding is a technology that involves continuously burning the arc during welding without extinguishing the arc light. It uses a small gap in the groove and a small welding current at the beginning, maintaining continuous short arc welding.
The basic elements of this technology involve striking the arc with the electrode and applying minimal pressure. Then, at the starting point of welding, the sawtooth-shaped electrode moving method with small pitch is used to swing the electrode sideways to preheat the welding components.
The welding rod should be sent into the root as far as possible to drive the electrode breaking action. When a “porphyrin” sound is heard, the welding will form a dissolved hole. The arc must be immediately transferred to any position on the groove surface and then a certain electrode angle must be used between the groove surfaces.
The operation involves small, uninterrupted actions that last about 2 seconds. When the arc melts the groove root on both sides by about 1.5 mm, the welding rod should be raised by 1-2 mm. The electrode should be rotated in a zigzag pattern with a small step so that the arc is in front of the fusion hole while welding is carried out forward.
During welding, it is crucial to ensure that the center of the welding rod is aligned with the front edge of the weld pool and the base metal junction, so that each new weld pool overlaps the previously generated weld pool. During arc extinction, the electrode must be slowly brought to the right or left side, behind the weld pool, and raised to extinguish the arc.
When welding joints, the arc should be lit at a distance of 10-15mm from the crater at the beginning, and the electrode should be moved halfway across the crater at normal speed. The electrode should then be pressed down and when a “porphyrin” sound is heard, a slight oscillation should be made for 1-2 seconds. After that, the electrode should be raised by 1-2 mm so that it can be moved forward to weld while melting the front of the fusion hole.
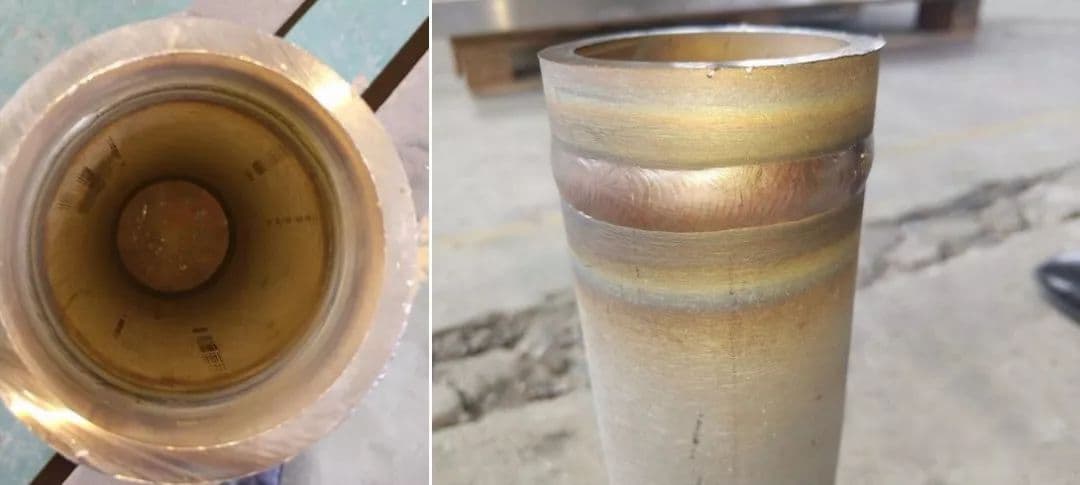
2. Analysis of plate butt welding and double-sided forming process
2.1 Preparation before welding
(1) Plate thickness: 12 mm, Specification: 300 × 200 mm.
Cut the board using oxygen and acetylene gas or use scissors and cutting machines, and then use mechanical methods such as planers or angle grinders to process V-shaped grooves.
Chamfers on the back of the grooves are not permitted.
Make sure the grooves are straight, smooth and free from burrs, bulges and other imperfections.
(2) To clean the test panel, use a file to remove the sharp corners of the groove, keeping the blunt edge size at 0.5-1.0mm. Remove rust, oil, oxides and other contaminants from the groove and within 20 mm on both sides, leaving a metallic shine.
(3) Test panel assembly and spot welding.
Perform spot welding on both ends of the back of the test board and allow for shrinkage allowance.
Set the weld end gap to 3.0-3.5mm, the weld end gap to 3.5-4.0mm, and the length of the positioned weld to about 10-15mm.
Make sure the weld in place is tight, especially at the butt end of the weld.
To avoid any negative impact on continuous welding or fracture during welding caused by reduction of the groove gap in the unwelded section due to weld shrinkage, reserve a margin of reverse deformation during position welding, i.e. a reverse deformation of the welding angle. 3°-4°.
(4) Welding equipment: ZXG series DC arc welding machine.
Power supply type and polarity: Ensure that the DC welding rod is not affected by moisture and deterioration, that the welding core is free from rust, and that the coating does not crack or fall off.
Bake the welding rod at 350-400℃ before use, maintain a constant temperature for 2 hours, and weld in four layers.
(5) Fix the test plate: Place the anti-deform test plate horizontally on the welding frame at an appropriate height.
The welder must not sit down while welding and must operate in a crouched position.
The test plate groove angle is 60°.
2.2 Welding operation
2.2.1 Welding of the lower layer
Primer welding can be carried out using general welding or end arc welding, or continuous arc welding.
To start the welding process, the arc must be lit on the inner side of the test panel groove and the lower arc must be pressed. The welding rod should be gently rocked back and forth between the two blunt edges of the groove until the molten iron on the edge combines with the molten drop from the welding rod, producing a “porphyrin” sound and forming the first puddle. melted.
At this stage, there should be a dissolution hole in front of the dissolution tank with a depth of 0.5-1.0 mm on both sides of the test plate groove.
The zigzag or crescent shaped transverse swing welding method is adopted for the operation of the welding rod. The length of the oscillating arc must be less than or equal to the electrode diameter. A short arc is used to send the molten iron through the groove root to the back of the weldment.
When the welding rod is transported to both sides of the groove, a pause of 1-2s is required. This pause leads to good fusion of the filler metal and base metal and also prevents the formation of sharp corners at the weld and groove junction, which is useful for slag removal.
2.2.2 Electrode angle
The included angle of the direct welding direction is 70°-80°.
A proper electrode angle leads to separation of the molten slag from the cast iron, keeping the molten pool clean and shiny at all times and preventing settling.
Welding Rod Key Points: Look, Listen, Be Precise and Short.
The angle included for the direct welding direction must be between 70° and 80°.
A proper electrode angle helps separate molten slag from molten iron, keeps the molten pool clear and shiny, and prevents settling.
The main points for using a welding rod are: observe, listen, be precise and work efficiently.
“Observing” means paying attention to the shape of the weld pool and the size of the weld hole, which determines the height and strength of the subsequent weld.
The molten pool must be round or oval in shape and always shiny and transparent to separate the slag from the molten iron.
The fusion hole should be such that the arc melts all blunt edges on both sides and penetrates 0.5 to 1.0 mm into the base metal on each side.
When the hole is too large, the weld on the back is too high and, in severe cases, a weld bead or burn may occur.
To remedy this situation, the welding speed must be increased, the oscillation range of the electrode toward both sides of the groove must be increased, and the included angle between the electrode and the welding direction must be reduced.
When the hole is too small, the groove root is not fully welded and the fusion of the weld root is not good.
To solve this, the lower arc must be pressed to increase the angle of the welding rod in the forward direction, decrease the welding speed and oscillation amplitude, reduce the angle between the welding rod and the forward welding direction, and maintain the shape of the weld pool and the size of the weld hole.
During welding, it is essential to control the flow direction of the cast iron and solution.
The electric arc must always burn in front of the cast iron.
The reverse blowing force of the gas generated by the electric arc and coating melting is used to blow the molten iron to the rear of the molten pool, ensuring weld penetration, separation of molten slag and iron, and reducing possible welding defects. slag inclusion and porosity.
Furthermore, it is necessary to always observe the fusion of the welded groove.
The rear edge of the weld pool must be completely fused with the grooves on both sides.
“Listen” means that the welder should not be distracted during welding and should hear the “porphyrin” sound when the arc breaks the test plate.
If this sound is not heard, the groove root will not be broken by the arc and continuing to weld will result in a waterproof weld.
Generally, keep the electrode end 2 or 3 mm away from the groove root.
“Accurate” means that the arc contact position must be accurate. Each new weld pool must overlap the previous one by 2/3 to ensure that 1/3 of the arc is directly in front of the weld pool.
When the welder hears the “por por” sound, he must quickly extinguish the arc behind the weld pool. In this way, the protective effect of the arc on the molten pool can be fully exerted, preventing the formation of pores.
Short” refers to the arc extinction and butt welding time, which should be completed as quickly as possible; otherwise, cold shrinkage defects may occur and metal cracks may occur due to insufficient fusion between weld pools.
To avoid cold shrink holes, increase the arc extinguishing frequency and reduce the arc contact time. While the previous molten pool is still liquid, the next molten pool must already be formed, so that the molten pool remains in a high temperature state.
For the two-point breaking method, the arc extinguishing frequency should be about 50 to 60 times per minute, while for the single-click breaking method, the arc extinguishing frequency should be about 80 times per minute .
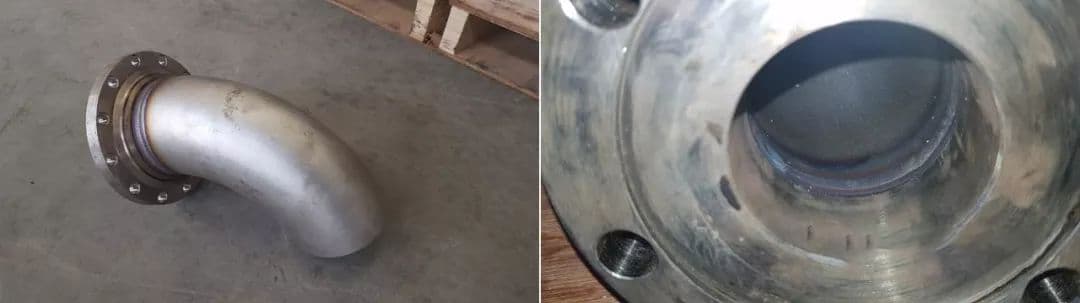
2.2.3 Joints
The different types of joints are categorized as hot connections and cold connections, and their descriptions are provided separately below.
Hot Connection:
To weld in the hot crater state of the arc, strike the arc on the slope, 10-15 seconds behind the crater. Weld toward the front arc stop to gradually increase the temperature at the crater floor. Then press the electrode along the pre-cast hole. When you hear the “porphyrin” sound, stop and lift the electrode for normal welding.
It is better to replace the electrode sooner rather than later.
Cold connection:
When the arc crater has cooled, remove the arc crater and the first 10 mm of molten slag from the carbon steel. Clean the area and replace the welding rod.
At the lowest point on the slope, quickly press the welding rod along the pre-cast hole. When you hear the “porphyrin” sound, pause for about 1 second before lifting the welding rod to start normal welding.
There are two methods for the arc break welding technique: the one-click and two-click drilling techniques.
For the two-click drilling technique, the arc is lit on both sides of the groove, and a drop of cast iron is first dropped onto the left blunt edge, followed by a drop of cast iron onto the right blunt edge, gradually alternating.
This welding technique is suitable for work with large gaps in the welding assembly.
For the one-click penetration method, the arc ignites the blunt edges on both sides of the groove and melts simultaneously.
The basic mode of operation is as follows: light the arc.
When welding, begin by forming an arc on the inside of the groove at the leading edge of the test panel. Preheat the starting piece with a long arc, then lower the arc and rock the electrode back and forth between the two blunt edges.
When the molten iron on the blunt edge of the groove combines with the metal droplet of the electrode and a “porphyrin” sound is heard, the first molten pool will be formed and the arc will extinguish.
At this point, the front end of the first molten pool will become a molten hole, which should be drilled 0.5-1.0mm deep on both sides of the test plate. Replace the welding rod gasket.
The method for changing the welding rod during arc burst welding is basically the same as that of continuous arc welding. Before changing the welding rod, in order to avoid cold shrinkage holes due to arc extinction, the arc should not be extinguished too quickly. Two or three drops of molten iron should be sent to the edge or north of the molten pool in advance, the later molten pool should be filled, and the temperature of the molten pool should be controlled to cool it slowly.
A weld hole must be formed in front of the weld pool. Press the arc into one side of the groove and weld about 10 mm before extinguishing the arc. This ensures that the molten iron in the rear molten pool is full and sufficient to prevent cold shrinkage defects.
After quickly changing the electrode, the arc should be started within 10-15mm of the front of the crater. Once lit, the arc must be drawn back and the metal to be welded must be preheated with a long arc.
Then, the arch should be pressed about 10 mm behind the crater. The welding rod must be operated continuously to the root of the crater.
After hearing the “porphyrin” sound, the arc must be stopped for about 2 seconds to extinguish it. Then, the original intermittent arc welding method should be used to continue welding.
Please note the following:
(1) The thickness of the primer weld in front and behind the groove should be between 1.5 and 2.0 mm.
(2) Welders must rotate the bar using their wrists flexibly.
(3) Four welds, each 300 mm long, must be completed.
2.2.4 Filler layer welding
After the welding slag from the previous layer has cooled, carefully remove any slag and spatter, paying special attention to the corners.
After removing the scum, use a wire brush to clean the area until the metal surface is exposed.
Start the arc 10 mm from the start of the weld and then return the arc to the starting point of the weld.
Use a crescent or sawtooth shaped electrode and pause briefly when the electrode swings to either side of the groove to stabilize the arc.
Move quickly through the middle of the groove, keeping the arc as low as possible. This will help facilitate the removal of impurities in the sharp corners of the deep channel and prevent slag inclusion.
Maintain balance in the molten pool and on both sides of the groove to prevent slag inclusion from forming at the junction between the filler metal and base metal. This is difficult to clarify.
The included angle between the welding rod and the welding progress should be 75°-85°.
Adopt a short arc when welding and make sure the welding puddle is round or oval with consistent shape and size.
Maintain a uniform welding speed and consistent welding slurry thickness.
Use thermal methods when welding the joint.
Before changing the welding rod to stop the arc, lightly add molten iron to the weld pool formed.
After a quick welding rod change, strike the arc about 10 mm in front of the arc crater.
Then draw the arc to 2/3 of the crater, fill the crater first and then continue with normal welding.
Stagger the connection joints of each layer of solder.
The filling height of the last layer should be 0.5-2.0mm lower than the base metal surface, and the shape should be high on both sides and concave in the middle.
Make sure the weld is smooth and the groove is excessive to ensure that the groove is clearly visible when welding the cover. This will help ensure the weld edge of the cap is straight.
2.2.5 Welding of the covering layer
The arch forming method for the cover layer is the same as that for the filling layer. Use a crescent-shaped or transverse sawtooth-shaped electrode.
The oscillation amplitude of the electrode should be slightly greater than that of the filling layer. Ensure that the swing amplitude is consistent throughout the swing and that the electrode speed is uniform.
The shape of the welding puddle is oval. Try to keep the shape and size of the pool approximately the same and use short arc welding.
When the welding rod swings to the edge of the groove, stabilize the arc and stop the tip. Fusion at the edge of the groove should be approximately 1.0-2.0 mm.
Both sides of the weld edges must be well fused to avoid undercutting.
The welding advance speed must be uniform to make the weld surface smooth and beautiful.
When using welding rod joints, adopt the hot joint method.
Before replacing the welding rod for arc quenching, lightly add molten iron to the weld pool.
After replacing the welding rod, strike the arc about 10 mm in front of the crater, then draw the arc back to 2/3 of the crater, fill the crater, and then perform conventional welding.
If the joint part is deviated, the joint part will be higher. If the joint is deviated, weld dejoining defect will occur.
3. Common defects of single-side welding and double-side forming
In summary, common defects that may occur during the plate-to-plate butt joint, one-sided welding, and two-sided forming process include: air pockets, incomplete penetration, incomplete fusion, and weld bead formation, among others.
In the following section, we will analyze and detail these potential defects in more detail.
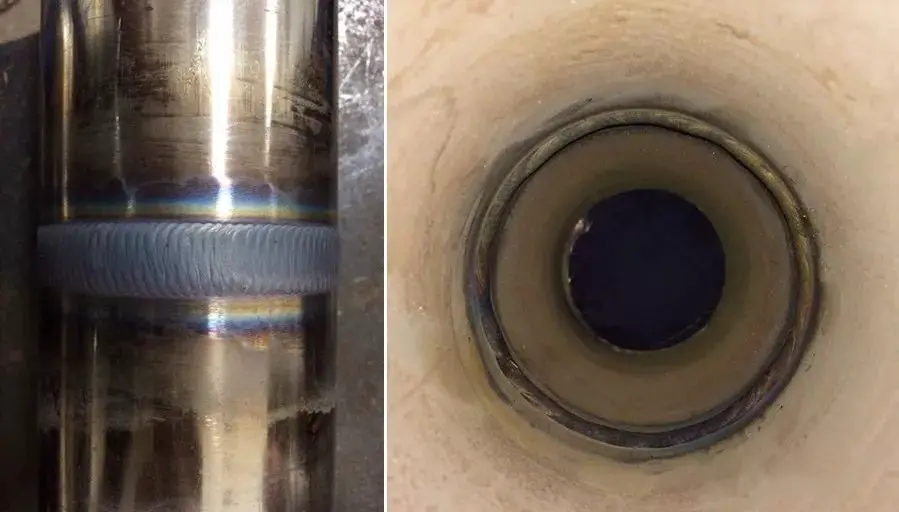
3.1 Porosity
Air holes are formed in the weld metal when the gas present in the weld pool cannot escape before the weld metal solidifies during welding.
This gas can be absorbed by the weld pool from the external environment, with hydrogen and carbon monoxide being the most common gases. It can also be produced as a result of metal reaction during welding.
For example, if the base metal contains an excessive amount of sulfur, gas pockets will form during the fusion process with the electrode metal.
(1) The main causes of porosity during welding are analyzed below:
The surface of the base metal or filler metal to be welded must be clean and free from impurities such as oil stains and rust.
It is important to ensure that the welding flux or electrode is completely dry before welding as the presence of moisture can cause it to decompose into gas during the welding process, leading to an increase in pore formation.
The low linear energy during welding results in rapid cooling of the weld pool, which makes it difficult for gas to escape from the weld metal in a timely manner.
Inadequate deoxidation of the weld metal can also lead to increased oxygen pore formation.
Environmental factors, such as excessive humidity on rainy or foggy days, can cause the weld to absorb moisture from the surrounding air during welding, further increasing the formation of porosity.
(2) Damage to stomata.
There are several specifications that regulate the number of pores allowed.
However, the presence of air holes during welding can reduce the effective sectional area of the weld, loosen the joint, reduce its strength and result in production accidents, such as leaks.
Porosity can also generate structural defects that cause concentrated stress and damage components, thus reducing their resistance and affecting their useful life.
Therefore, it is essential to analyze the causes of pores individually and avoid external factors that could lead to their formation. This approach will help minimize the occurrence of pores during welding.
3.2 Incomplete penetration and fusion
3.2.1 Causes of incomplete penetration
(1) The test plate groove angle may be reduced, the blind edge may be too large, or the mounting gap may be too small, resulting in insufficient spot welding length and a weld that is too thin. Tensile and shrinkage stresses during welding may cause the gap at the spot welding point to decrease or the selected electrode may be too large, preventing the deposited metal from reaching the root of the groove.
(2) Too fast welding speed or too small welding current may cause decreased arc penetration force, shallow weld pools and insufficient fusion of welding edges. The burning time of the burst welding arc on both sides of the groove may also be too short to form a hole of a certain size.
(3) Improper electrode angle or magnetic deviation of the arc may cause heat from the arc to be lost or diverted to one side, resulting in incomplete penetration.
(4) During primer welding, incomplete penetration of the joint may occur. This is a common occurrence in plate welding after changing the welding rod. The temperature of the impact arc decreases, causing a large temperature difference between the welded and non-welded parts, a large gap between the test plates and welding is carried out before the required preheating temperature is reached. As a result, the arc in the joint cannot quickly break through the blunt edge of the test piece, causing an incomplete penetration section in the joint and resulting in defects.
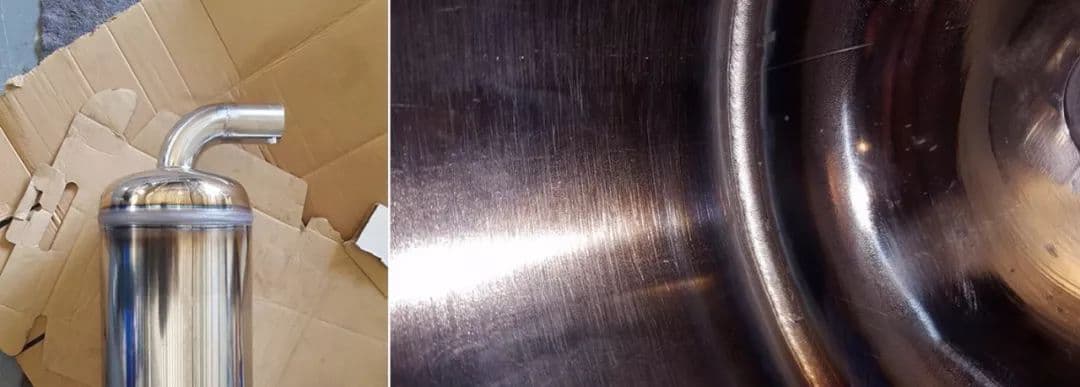
3.2.2 Measures to prevent incomplete penetration defects
(1) Choose the correct electrode angle.
When performing backing welding, it is important to control the welding speed appropriately to ensure that the arc completely melts the root.
(2) Thoroughly clean the groove weld to remove any oil, rust or other debris.
(3) During the welding process, if the eccentric electrode causes arc deflection, immediately adjust the electrode angle. Swing the electrode in the opposite direction of the arc deflection to align the arc with the weld pool, or replace the electrode.
(4) Closely monitor the fusion condition during welding to ensure proper fusion.
3.3 Overlay
(1) The chamfered edge is too blunt and the mounting gap is too large.
(2) During flat welding, excessive welding current and slow welding speed can cause the temperature and volume of the weld edge to increase. This can result in the liquid metal falling due to gravity.
(3) Incorrect welding rod angle can also be a problem during welding.
Prevention measures for welding overlap:
(1) Choose the appropriate size for the blind edge and mounting gap, and adjust the size of the fusion hole during the welding process.
(2) Strictly control the current and interim temperature.
(3) Choose an appropriate electrode angle and swing the electrode faster in the middle and slower on both sides.
(4) Carefully observe the state of the weld pool.
(5) If there are more small sparks emitted from the weld pool, extinguish the arc immediately to decrease the temperature of the weld pool before continuing with the welding process.