Selecting corrosion-resistant materials is the most effective and proactive measure to ensure reliable operation of metal equipment.
Therefore, it is necessary to have an understanding of the corrosion resistance of various metals and alloys, understand the suitable working environment for each material, and only then can effective anti-corrosion measures be taken for the corrosion of metal equipment.
1. Corrosion resistance of iron-carbon alloys
“Iron-based alloys (steel and cast iron) are the most used metallic materials in engineering and present satisfactory corrosion resistance and good comprehensive mechanical properties in certain situations. Its corrosion resistance is closely related to the corrosion resistance of pure iron.
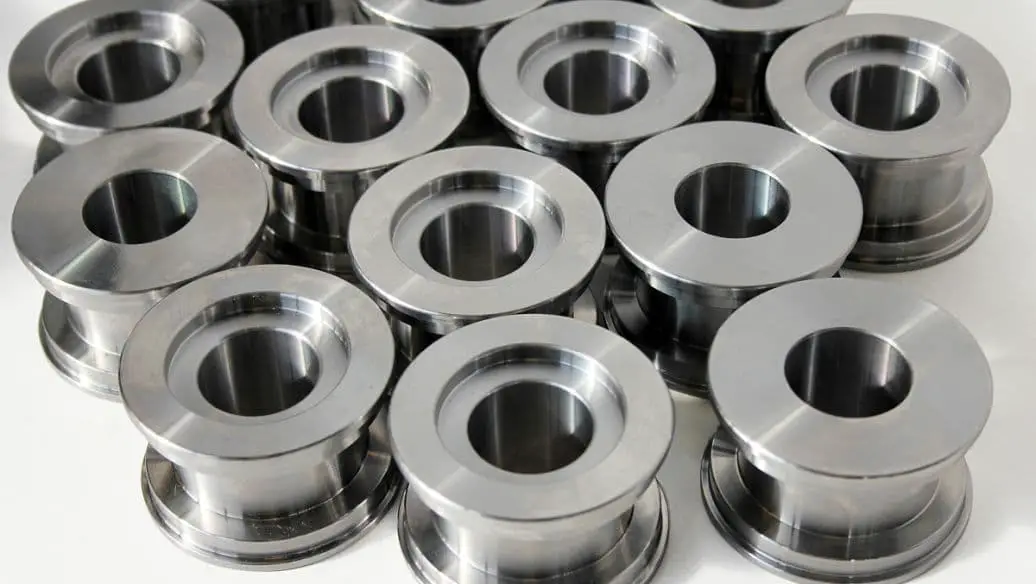
I. Corrosion resistance of iron
Iron is a thermodynamically unstable metal and has low corrosion resistance compared to metals close to their equilibrium potential, such as aluminum, titanium, zinc, chromium and cadmium.
In other words, compared to these metals, iron is the least resistant to corrosion in natural environments (atmosphere, soil, natural water, etc.). This is due to the following reasons:
The hydrogen and oxygen overpotentials of iron and its oxides are relatively low, facilitating hydrogen evolution corrosion and oxygen absorption corrosion.
The trivalent iron ions in iron rust and its solutions have good depolarizing effects.
Iron corrosion products have weak protective properties.
Iron is susceptible to corrosion due to the formation of an oxygen concentration cell.
Iron has poor passivation capacity under natural conditions.
Iron forms insoluble corrosion products, commonly known as rust, when corroded in most weakly acidic, neutral and alkaline solutions. Rust has a loose, porous structure and offers little protection.
In non-oxidizing acids, the corrosion rate increases exponentially with increasing acid concentration, but in oxidizing acids, the corrosion rate first increases with increasing acid concentration and then decreases rapidly due to the onset of passivation.
Organic acids are generally weak at corroding iron, but the corrosion of iron can be accelerated by increasing temperature and dissolving oxygen. Iron is stable in alkaline solutions at room temperature.
2. The corrosion resistance of carbon steel
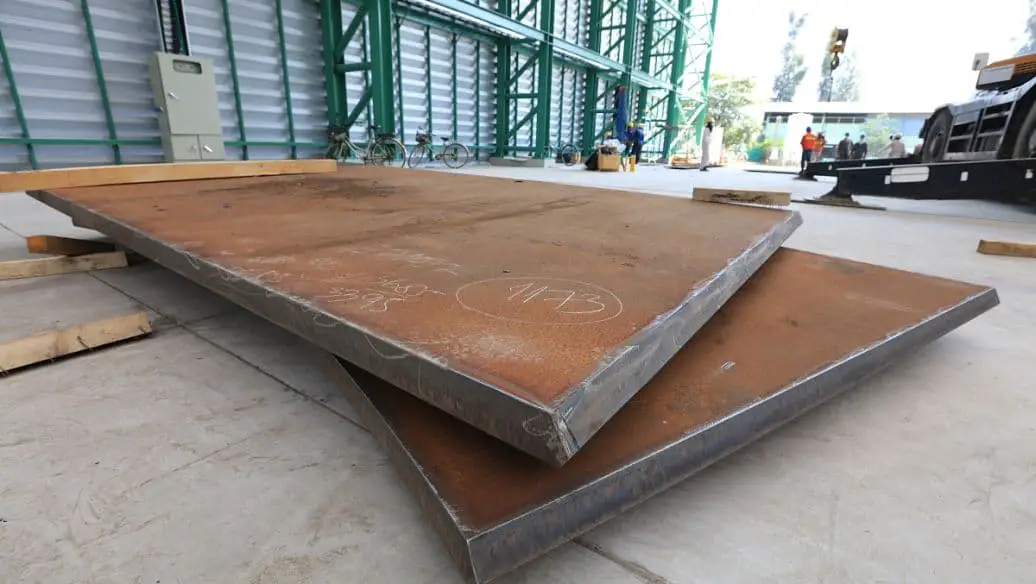
The factors that affect the corrosion resistance of carbon steel are:
1. Chemical composition
⑴ The impact of carbon: The carbon content in carbon steel has a significant impact on the corrosion rate of carbon steel in acidic solutions, but the impact is not obvious in neutral solutions.
In non-oxidizing and weakly oxidizing media, the corrosion rate of the material increases with increasing carbon content, because the more carbon content in the steel, the more carbon precipitation in the structure and the more microbatteries are formed, thus accelerating the corrosion rate .
In oxidative acids, the corrosion rate increases with increasing carbon content at the beginning, and then decreases when the carbon content reaches a certain level, which is due to the fact that the increase in carbon content is easy to promote the passivation of carbon steel, and the corrosion rate is weakened.
In a natural environment and in weakly acidic aqueous solutions, the impact of carbon content on the corrosion rate of carbon steel is not significant.
This is because oxygen depolarization corrosion is the main factor in such environments, and the performance of the protective film on the metal surface and the ease of oxygen reaching the cathode surface in the solution are the main factors, and carbon precipitation in the steel has little relation.
⑵ Silicon and manganese generally have almost no obvious impact on the corrosion rate.
⑶ The impact of sulfur and phosphorus
Sulfur is detrimental to the corrosion resistance of steel, and the dissolution rate in acidic solutions increases with increasing sulfur content.
Increased sulfur content in steel can easily cause local corrosion. This is because sulfur is usually present in carbon steel in the form of FeS and MnS, both anodic impurities, causing pitting fracture and sulfide stress corrosion cracking.
Phosphorus in steel is also an active and harmful cathode in acidic solutions such as sulfur. However, phosphorus can effectively improve the corrosion resistance of steel in atmospheric and seawater environments, especially when used with copper, with particularly good results.
⑷ The impact of impurities
For carbon steel, all kinds of impurities will reduce corrosion resistance.
2. Structural impact
The structure of the steel depends on its composition and the state of heat treatment. Generally speaking, the higher the carbon content in steel, the greater the impact of heat treatment on its corrosion resistance.
When the carbon content is the same, granular pearlite has better corrosion resistance than lamellar pearlite, and the greater the dispersion, the higher the average corrosion rate.
The corrosion resistance of non-passivated carbon steel is closely related to its carbon content and heat treatment.
Generally, the higher the carbon content, the worse the corrosion resistance; the corrosion resistance of high carbon tempered carbon steel is worse, slightly improved after low temperature tempering, the maximum corrosion rate appears after intermediate temperature tempering, and after high temperature tempering, the corrosion rate decreases significantly due to to the reduction of the active cathode surface area.
3. Corrosion resistance of low alloy steel
Low alloy steel refers to alloy steel with a total amount of alloying elements less than about 5% in carbon steel. According to different purposes, there are many types of alloying elements added to steel, and the amount of these elements also varies greatly, so there are many types of low-alloy steel.
1. Low alloy steel resistant to atmospheric corrosion
Low alloy steel resistant to atmospheric corrosion is also known as weathering steel and is simply referred to as weathering steel.
Its effective alloying elements are copper, phosphorus and chromium, which enrich the steel surface and promote the formation of amorphous states, thereby improving the steel's resistance to corrosion in atmospheric environments.
Representative low alloy steels resistant to atmospheric corrosion include 16MnCu, 10MnSiCu, 09MnCuPTi, 15MnVCu, 10AuRe, 08MnPRe, etc.
2. Seawater corrosion resistant low alloy steel
In marine environments, the most severe corrosion conditions occur in the spray area which is alternately dry and wet, is difficult to protect and is subject to the impact of seawater.
Next is the shallow water soaking area.
The effect of alloying elements on the corrosion resistance of steel in different sections is different: copper is the most prominent in improving the corrosion resistance of steel in the spraying area, and phosphorus also has a significant effect.
The combination of the two has a better effect. Silicon, molybdenum can reduce the pitting corrosion tendency of steel in the spraying area, chromium and aluminum also have some effect.
For the corrosion resistance of steel under full immersion conditions, chromium has the most obvious effect, followed by phosphorus, copper, silicon and nickel.
Seawater corrosion resistant low alloy steels developed in China mainly include 10MnPNbRe, 09MnCuPTi, 10CrMoAl, 10NiCuAs, 10CrMoCuSi, etc.
3. Low alloy steel resistant to hydrogen and nitrogen corrosion at high temperature and high pressure
In the petroleum and synthetic ammonia hydrotreating industry, steel works in high-temperature and high-pressure hydrogen environments, and the carbon matrix is easily corroded by interaction with active hydrogen atoms that penetrate the steel.
Therefore, carbon alloying elements can be added to steel, which form stable carbides with carbon, thereby improving the hydrogen corrosion resistance of steel. Studies have shown that adding Cr, Mo and small amounts of V, Nb and Ti to steel can improve its resistance to hydrogen corrosion.
Low alloy steels resistant to high temperature and high pressure hydrogen and nitrogen corrosion in China mainly include 10MoWVNb, 10MoVNbTi, 12SiMoVNb and 0.8SiWMoTiNb; the typical foreign anti-hydrogen steel 2.25Cr1Mo is currently recognized as one of the best anti-hydrogen steels.
Almost all hydrotreating reactors in the petrochemical industry are made from this steel.
4. Low alloy steel resistant to sulfur corrosion
In the petroleum refining, natural gas and urban gas industries, a large number of low-alloy steels are required to manufacture pipelines, storage tanks and other equipment, which generally operate in sulfur-containing environments and are prone to severe sulfur corrosion.
Current research believes that the microstructure of steel is the key factor affecting sulfur corrosion fracture of low alloy steels. The formation of martensitic microstructure in steel must be strictly
2. Stainless steel and acid-resistant steel
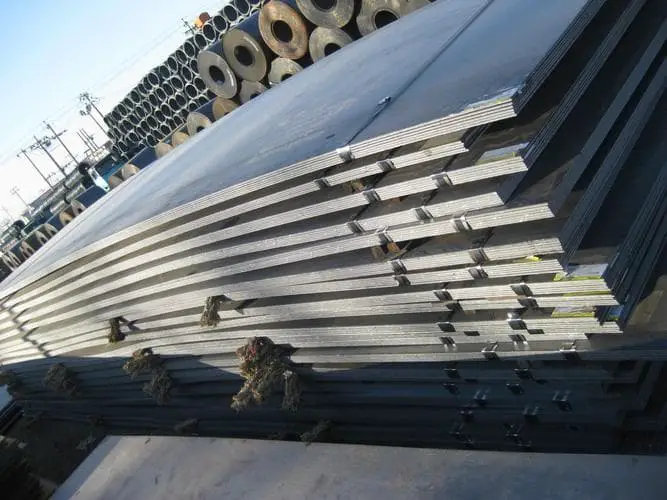
Steel that is resistant to corrosion in atmospheric conditions and neutral electrolytes is known as “stainless steel”, while steel that is resistant to corrosion in chemical reagents and highly corrosive media is known as “acid-resistant stainless steel”.
People often refer to stainless steel and acid-resistant stainless steel simply as stainless steel. Stainless steel generally refers to steels with a chromium content greater than 12%, and the term “stainless” is a relative concept. The same steel may be stainless in some environments but not in others.
Stainless steel classification:
Based on chemical composition, it can be divided into chrome steel, chromium-nickel steel, chromium-manganese steel, etc.
Based on microstructure, it can be divided into martensitic steel, ferritic steel, austenitic steel and austenitic-ferritic two-phase steel.
Based on usage, it can be divided into seawater resistant stainless steel, stress corrosion resistant stainless steel, sulfuric acid resistant stainless steel, etc.
I. Corrosion resistance of chrome stainless steel
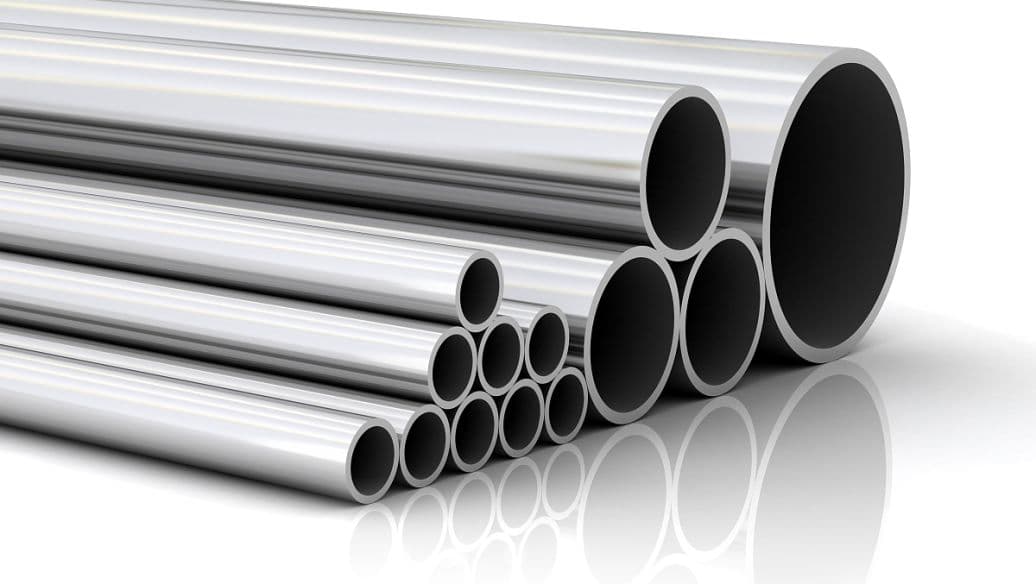
Chromium stainless steel refers to stainless steel that contains only chromium or is supplemented with a small amount of other alloying elements, excluding Fe and C.
Chromium is the most important alloying element in stainless steel and plays three important roles in improving the corrosion resistance of iron and steel materials:
First, it promotes the passivation of iron-based alloys, improving the material's passivation capacity;
Secondly, it increases the potential of the solid solution electrode (generally the anode of the corrosion cell), that is, the thermodynamic stability of the matrix structure;
Third, it makes the steel surface generate a dense and stable surface protective film, thereby improving the corrosion resistance of the steel.
Martensitic stainless steel
Martensitic stainless steel mainly includes Cr13 type stainless steel (excluding 0Cr13). This type of steel has a high carbon content and can obtain greater strength and hardness through heat treatment, but its corrosion resistance is not as good as ferritic stainless steel and austenitic stainless steel, and the higher the carbon content, worse corrosion resistance.
This type of steel is suitable for situations where mechanical properties are required and corrosion resistance is not very high.
Increasing the chromium content of steel and adding a small amount of nickel can improve the corrosion resistance of martensitic stainless steel; for example, 1Cr17Ni2 is the most corrosion-resistant martensitic, with good resistance to oxidizing acids and most organic acids.
Ferritic stainless steel
Ferritic stainless steel includes Cr13 type, Cr17 type, Cr25-28 type, etc. Due to its high chromium content and low carbon content, its corrosion resistance and high temperature oxidation resistance are better than martensitic stainless steel, especially its stress corrosion resistance.
However, ferritic stainless steel has low resistance to intergranular corrosion and intergranular corrosion.
Ferritic stainless steel is mainly used to manufacture equipment and parts that are resistant to high-temperature oxidation, concentrated sulfuric acid corrosion, and sulfur gas corrosion.
2. Corrosion resistance of chromium-nickel stainless steel
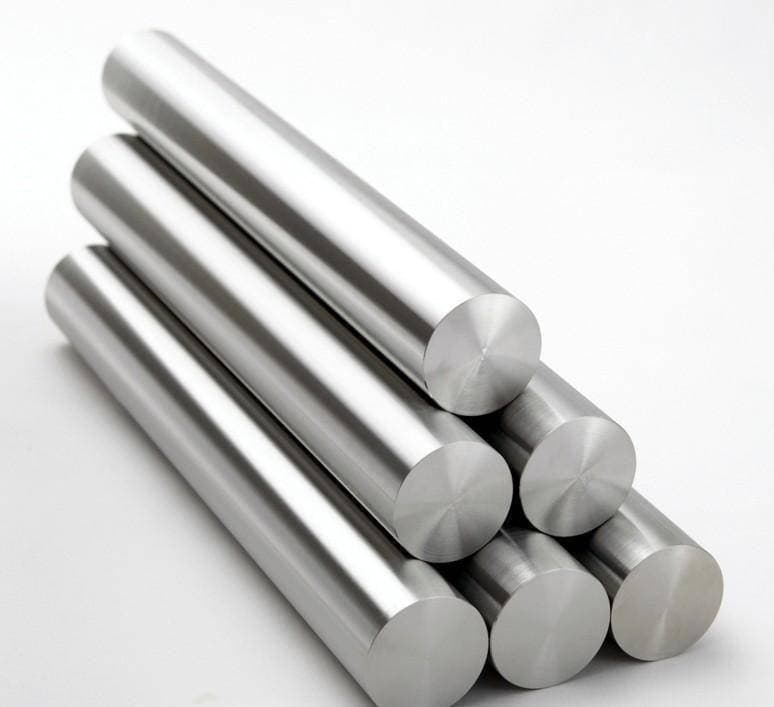
Nickel has stronger passive ability than iron and is also more thermodynamically stable, which is conducive to improving the corrosion resistance of steel.
Especially by adding a certain amount of nickel to stainless steel, a single-phase austenitic stainless steel structure can be obtained, significantly improving the toughness, plasticity and processing performance of the material.
Chromium-nickel stainless steel is the most typical austenitic stainless steel, containing more than 18% chromium and more than 8% nickel, forming chromium-nickel stainless steel grades such as 18-8 (or 18-9), 18- 12, 25-20 (HK40), etc.
Chromium-nickel stainless steel has excellent corrosion resistance in both oxidative and non-oxidative media, but its resistance to local corrosion such as stress corrosion cracking, intergranular corrosion and pitting corrosion is low.
Local corrosion can be inhibited by the alloy, such as controlling carbon content, reducing P and N content and increasing Ni, and adding Si, Mo, Cu, etc.
Austenite-ferrite two-phase steel is another type of chromium-nickel stainless steel, which combines the characteristics of ferrite and austenitic steel and has complementary performance.
In addition, precipitation hardening (PH) stainless steel also belongs to chromium-nickel stainless steel.
3. Acid-resistant steel
Acid-resistant steel refers to stainless steel with special corrosion resistance in some strong corrosive media.
For certain acid-resistant steels, it only shows excellent corrosion resistance in certain specific media.
Therefore, when selecting acid-resistant steel, it is necessary to comprehensively consider the properties and state of the corrosive medium and carry out appropriate feasibility tests to ensure that the material can function reliably in strong corrosive media.
3. Corrosion resistance of non-ferrous metals
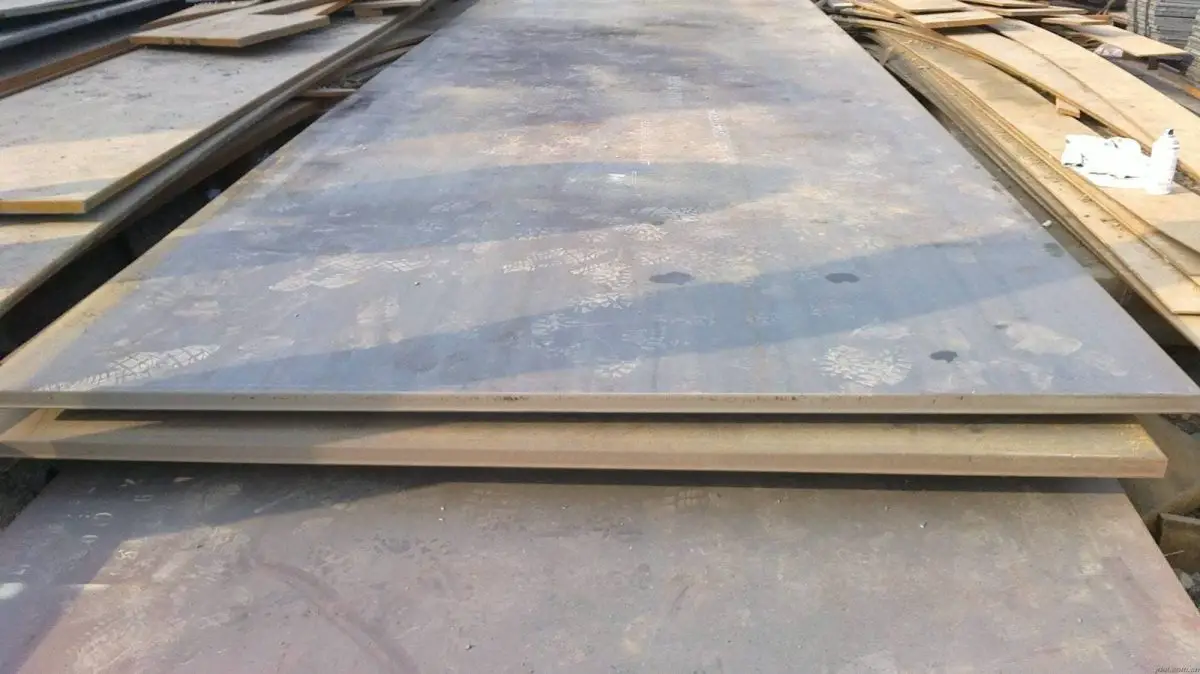
Common colored metals used in production include aluminum, copper, magnesium, titanium and others. In addition, colored metals such as zinc, tin, cadmium, gold, silver and lead are often used as plating and coating materials.
I. Aluminum and aluminum alloys
1. Corrosion resistance of pure aluminum
Pure aluminum has poor chemical stability, but it has good passivation performance, which can quickly generate a dense and well-protected oxide film in the air, and therefore has good corrosion resistance.
Al2O3 is amphoteric, therefore, when the pH of the medium is less than 4 or greater than 10, the oxide film becomes unstable and damaged, and protection is lost, causing aluminum corrosion to intensify. Aluminum has good corrosion resistance in air and water.
2. Corrosion resistance of aluminum alloys
Aluminum alloys are generally stronger than pure aluminum but less resistant to corrosion. Aluminum alloys have high corrosion resistance in industrial, marine, freshwater and seawater atmospheres, but they can corrode.
Aluminum alloys have high resistance to corrosion in oxidative media due to their ease of passivation, but are easily subject to local corrosion such as pitting corrosion, crevice corrosion and stress corrosion cracking in non-oxidative media.
2. Magnesium and magnesium alloys
1. Corrosion resistance of magnesium
Magnesium is unstable in most inorganic and organic acids, but is quite stable in chromic acid and hydrofluoric acid, due to the protective film on the surface that enters the passive state. Magnesium is not resistant to corrosion in marine and industrial atmospheres.
2. Corrosion resistance of magnesium alloys
In terms of corrosion resistance of magnesium alloys, deformable magnesium alloys are less corrosion resistant than cast magnesium alloys as they are more sensitive to SCC.
However, in general, the corrosion resistance of magnesium alloys is low, and it is necessary to take effective protective measures during use.
3. Copper and copper alloys
1. Corrosion resistance of copper
Copper has relatively high chemical stability and a positive electrode potential, so it generally does not corrode in acidic solutions.
In non-oxidizing acids, copper has a high degree of chemical stability, but its corrosion resistance is poor in oxidizing acids.
Copper is also subject to strong corrosion in other oxidizing media.
Copper has good corrosion resistance in various atmospheric conditions, but is subject to strong corrosion in humid air containing SO2, H2S and Cl2 gases.
Furthermore, it also corrodes in ammonium hydroxide and cyanide solutions due to the formation of complex ions.
2. Corrosion resistance of copper alloys
Copper alloys generally exhibit better corrosion resistance than pure copper due to the combined effect of the high thermodynamic stability of the base copper and the surface protective film formed by the alloy elements.
Therefore, the corrosion pattern of copper alloys sometimes also exhibits some characteristics of passive metals.
In non-oxidizing acids, copper alloys show a high degree of chemical stability.
Copper alloys have good resistance to corrosion in various atmospheric conditions. Other corrosion resistance is the same as copper.
There are many types of copper alloys, which can be divided into two categories: brass and bronze. Relatively speaking, the corrosion resistance of brass is low, especially in terms of its tendency to stress corrosion cracking (seasonal brass cracking) and selective corrosion (brass dezincification).
4. Titanium and titanium alloys
1. Corrosion resistance of titanium
Titanium has low thermodynamic stability and active chemical properties, but in oxidizing media, a dense protective oxide film is formed on its surface, which is in a stable passive state.
On the one hand, the protective film has good self-healing properties, and on the other hand, it is also very stable in various solutions (including chloride solutions). As a result, titanium has excellent corrosion resistance in many corrosive media and has been widely used in engineering applications.
2. Corrosion resistance of titanium alloys
Corrosion-resistant titanium alloy elements can be divided into two groups: one group is formed by precious metals such as Pd, Ru, Pt, and the addition of traces can significantly improve the corrosion resistance of the alloy.
The other group is Ta, Nb and Mo, which are cheaper, but only have a noticeable anticorrosive effect when the content is high.
There are not many commercially available titanium alloys with good corrosion resistance. Titanium alloys can suffer forms of corrosion, such as crevice corrosion, hydrogen brittleness, stress corrosion, welding area corrosion and natural explosive corrosion during use.
In conclusion, titanium and titanium alloys not only have good corrosion resistance, but also have higher strength and heat resistance than other materials, making them an indispensable structural material for many fields, with very promising application prospects.
4. Conclusion
This post mainly introduces the corrosion resistance of some commonly used metals and alloys.
Through the study of this chapter, the focus should be on mastering the corrosion resistance and influencing factors of iron-carbon alloys, stainless steel and some colored metals, as well as understanding the main functions of corrosion-resistant alloy elements and the scope of application of corrosion-resistant alloys.