The fiber laser cutting machine will produce dust and smoke during the processing and cutting process.
On the one hand, it will have adverse effects on the health of the operating engineer, and on the other hand, it will pollute the precise parts of the machine.
The impact may be small in a short time and will inevitably affect the machine's service life and cutting performance over time.
Therefore, being equipped with environmentally friendly and environmentally friendly dust removal equipment can effectively reduce the dust and smoke generated during the cutting process.
This article mainly introduces the dust removal methods of large format laser cutting machines – dry treatment and wet treatment.
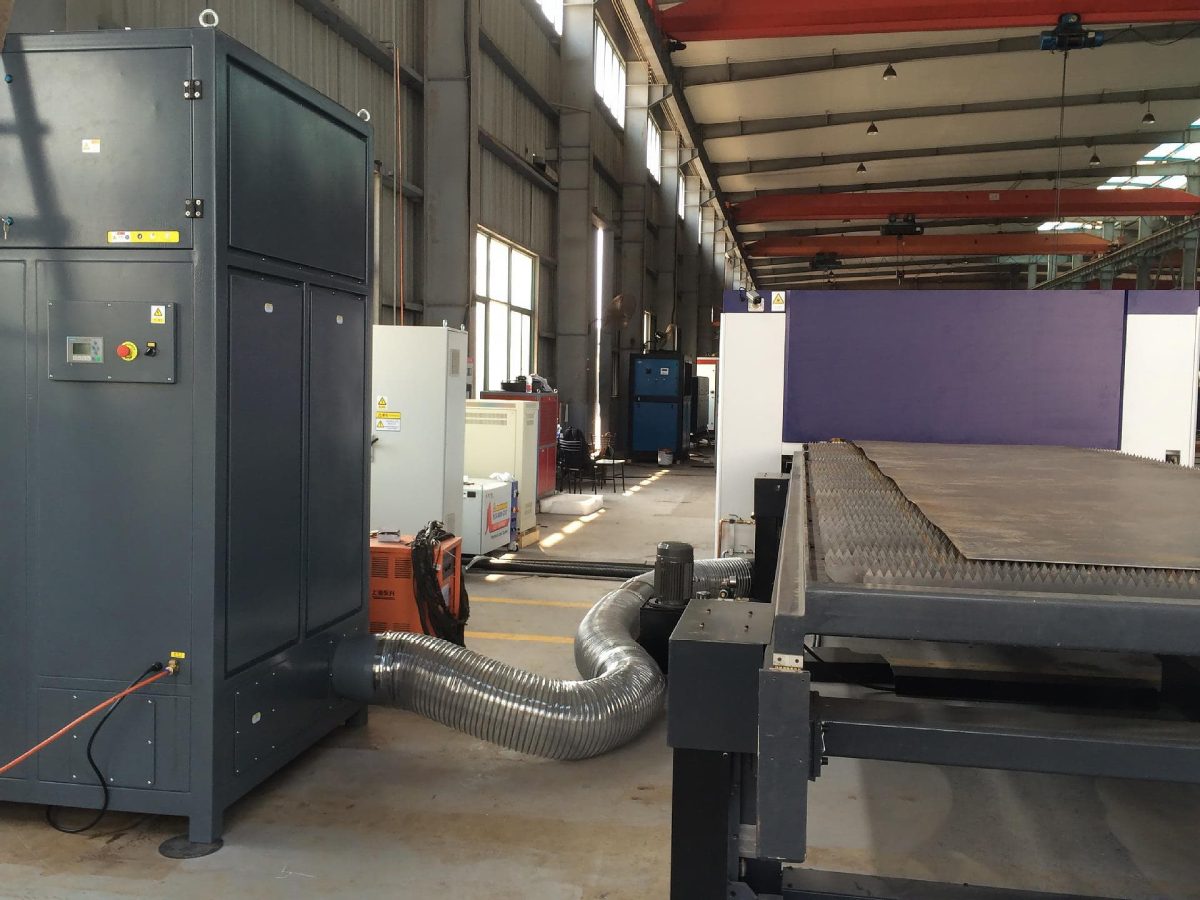
Dry treatment
The dry treatment method is also called dry cutting, that is, the exhaust working platform is installed at the bottom of the laser cutting machine, and the dust-containing gas is sent to the laser filtering and purification device. smoke and dust through pipeline dust removal, and then it is discharged after unified filtration treatment reaches the standard.
The smoke generated by cutting is basically formed below the cutting of the workpiece, so the aspirated negative pressure cutting platform has become the most common smoke collection device at present.
To save investment in equipment and improve air extraction efficiency, i.e. achieve greater amount of smoke and dust collection with a small amount of air suction – only the area in the cutting process is subjected to dust extraction treatment ( Fig. 1), so that the air outlet and air suction are installed on both sides of the cutting head, and move back and forth with the cross beam during cutting (side suction mobile air).
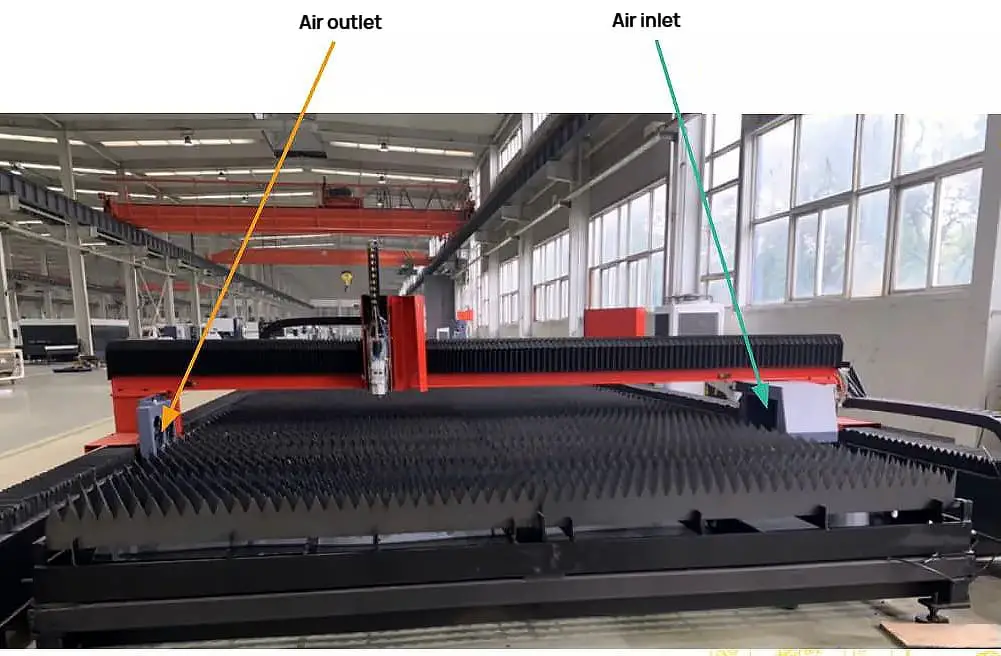
Fig. 1 Side suction movable suction opening
Although this treatment method has a relatively large investment in the initial stage compared with the wet treatment method, it overcomes several disadvantages in the application of the wet treatment method, is environmentally friendly and has good comprehensive benefits in the later stage.
The dry treatment method is widely used in two types: the damper type and the blowing and suction type.
Door type tracking cutting dust removal
An air extraction platform is installed under the cutting machine.
It will be divided into closed (uniform) areas along the main guide rail of the cutting machine for independent air extraction in sections.
Each air extraction area is equipped with independent valves.
Open and closed air extraction ports are arranged in the air extraction duct at the edge of the platform.
When the cutting head moves to the upper part of the exhaust chamber, the cutting machine cooperates with the control air valve to automatically open the exhaust port of the area where cutting is taking place, so that the exhaust area is connected with the dust removal system, so that the suction of the dust removal system can be effectively concentrated in the area around the cutting head, and the smoke and dust generated during the cutting process can be collected to the dust collector through the exhaust area, suction duct, etc. . for purification and then discharged.
It can be seen from the test that the air volume required for shock absorber type cutting and dedusting has a great relationship with the width of the cutting platform, therefore, according to the width of the platform, the cutting and dedusting system can be divided in one-sided lower exhaust damper type cutting and dust removal system and two-sided lower exhaust damper type cutting and dust removal system.
(1) Single-side bottom exhaust damper type cutting dust removal system.
Figure 2 shows the structure of the single-side descending door type cutting and dust removal system, which is applicable to the cutting platform with effective cutting width ≤ 4m.
The dust collector is connected to the movable air duct on one side of the machine body.
There is an independent movable exhaust port in the air duct. It opens when the cutting head moves to this area and closes when it leaves, ensuring the necessary air volume in the exhaust system.
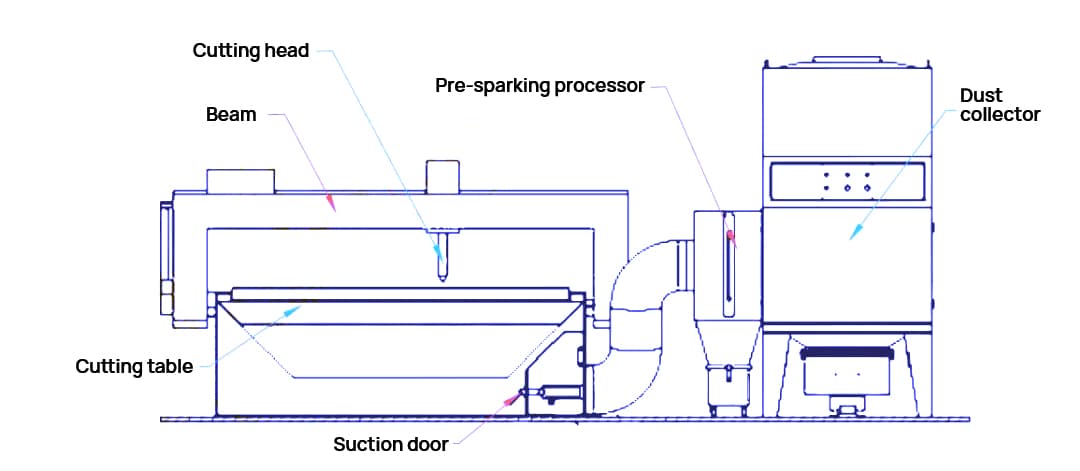
Fig. 2 Structural schematic diagram of single-side descending damper type cutting dust removal system
(2) Double side bottom exhaust damper type cutting dust removal system.
Figure 3 shows the structure of the cutting and dust removal system with double side lower exhaust damper, applicable to the cutting platform with effective cutting width ≥ 4m.
Large format laser cutting machines larger than 4 m are often equipped with double cutting heads. When the two cutting heads work at the same time, a large amount of smoke and dust will be generated.
Therefore, the double-sided bottom exhaust damper type cutting and dust removal method can be adopted, that is, both sides of the machine body are equipped with exhaust pipes.
When the two cutting heads move to the area, the exhaust valve on both sides will open at the same time, and the smoke and dust generated by the two cutting heads will be sucked into the tube to achieve the removal effect of dust.
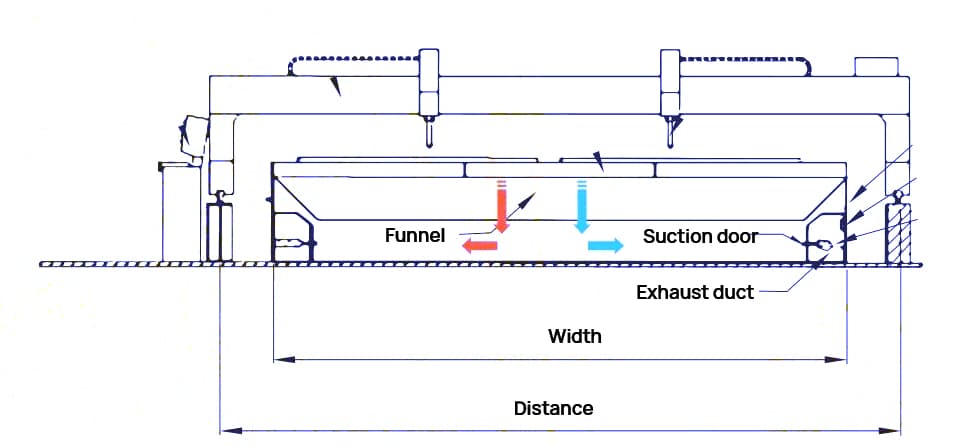
Fig. 3 Structural schematic diagram of double-sided descending damper type cutting dust removal system
Mobile cutting dust removal by blowing and suction
A square suction air duct is installed on one side of the cutting deck.
A sliding suction cart that can move with the cutting machine is installed above the air duct, and a blower is installed on the other side of the cutting deck.
The hair dryer, cutting head and sliding suction cart are three-point and one-line, and the platform grid air duct is formed using the dental plate of the working table on the cutting platform and the cutting plate. steel to be cut.
When cutting the steel plate, the blower will blow the cutting smoke and dust generated to the sliding suction cart through the grid air duct, which will be sucked into the suction duct and then enter the dust collector for purification and discharge.
The air volume required to remove cutting dust by blowing and suction has an optimal relationship with the cutting deck steel plate coverage on the platform.
The greater the coverage, the better the dust removal effect.
The square suction duct, sealing belt and sliding suction carriage are important components of the suction dust blowing and removal system, and their structural form is shown in Fig.
When working, the sealing belt is firmly fixed to the square suction duct under the negative pressure of the piping system to play a sealing function.
There are four rollers on the sliding suction cart, where the sealing belt is lifted by the rollers, so that the smoke and dust enter the square suction duct after passing through the internal structure of the suction cart, and finally are transported to the dust collector for purification and discharge.
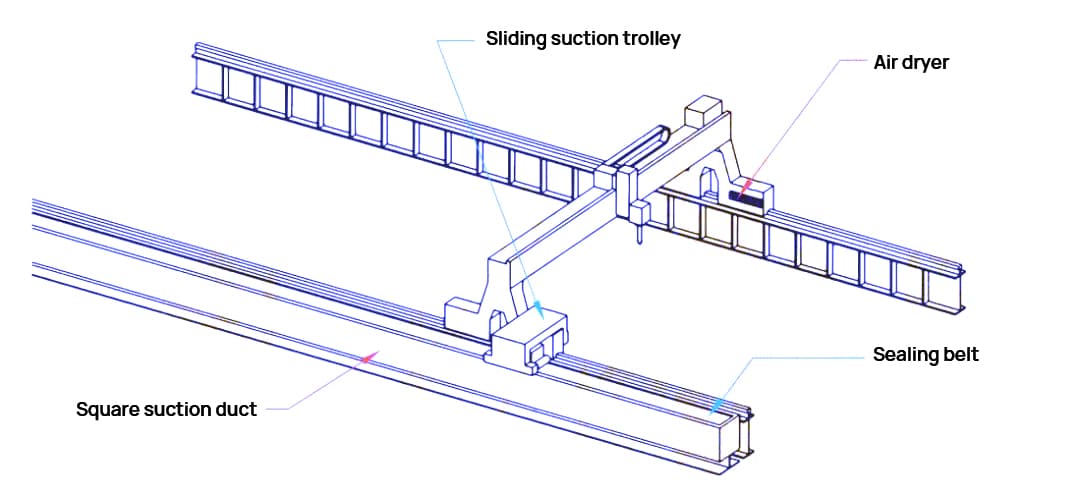
Fig. 4 Square suction duct, sealing strap and sliding suction carriage
Wet treatment
The wet treatment method, also called wet cutting, is actually to make a waterbed cutting platform (Fig. 5), place the steel plate in the water or on the surface of the water, and then complete the cutting operation under water or near the water surface.
Use water to capture the smoke and dust generated in the cutting process, in order to achieve the objective of purifying the environment.
But the new problems brought by this route are water pollution and the subsequent treatment of wastewater.
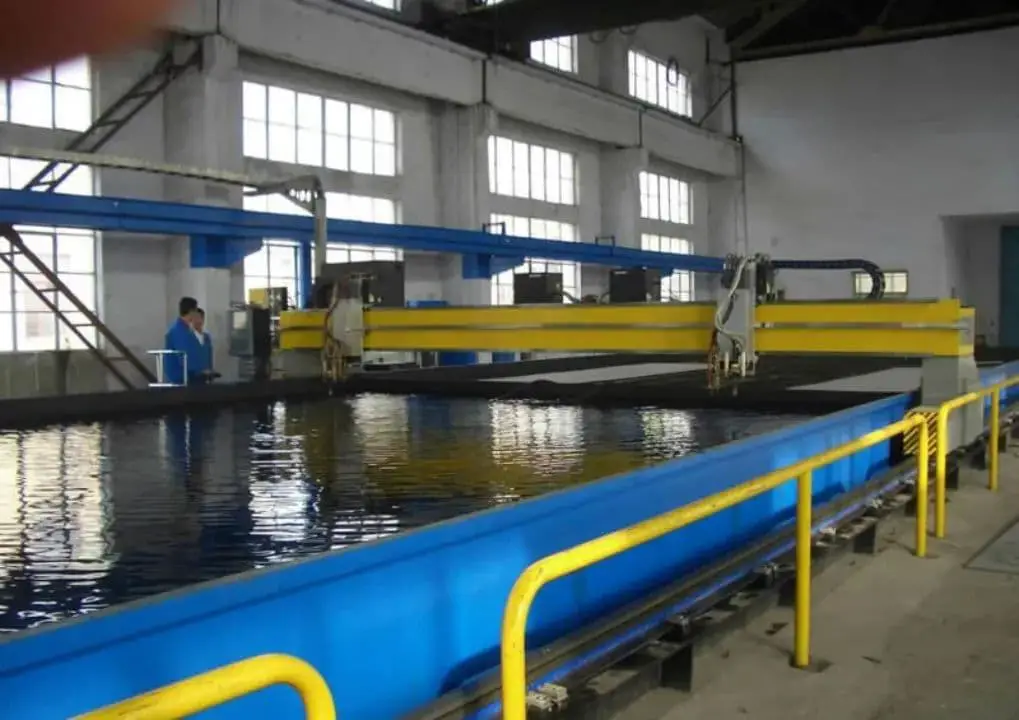
Fig. 5 Waterbed cutting platform
Conclusion
In order to improve production capacity and speed up the process, laser cutting machines with increasingly wider machine tool processing ranges and higher power have come into people's eyes.
At the same time, the monitoring of industrial environmental protection by relevant national departments also paid more attention to the emission of smoke and dust in the workshop.
Therefore, the rational allocation of dust removal and purification equipment is also an inevitable development trend of the current era.
This article presents two main types of dust removal treatment methods – dry and wet treatment methods.
Considering the economic cost and practical effect, the dry dust removal treatment method is the most common.