1. girdling
Annealing is a metal heat treatment process that involves slowly heating the metal to a specific temperature, holding it for an appropriate time, and then cooling it at an appropriate rate.
The objective of this process is to reduce hardness, improve machinability, eliminate residual stresses, stabilize dimensions and minimize deformations and cracking tendencies.
Furthermore, it refines the grain structure, adjusts the microstructure and eliminates structural defects.
Definition of Annealing
Annealing refers to a metal heat treatment process where the metal is slowly heated to a certain temperature, held for a sufficient time, and then cooled at a suitable rate (typically slow cooling, but sometimes controlled cooling).
Its purpose is to soften materials or parts that have been cast, forged, welded or cut, to improve their plasticity and toughness, homogenize their chemical composition, eliminate residual stresses or acquire the desired physical properties.
Depending on its purpose, there are various types of annealing such as isothermal annealing, homogenizing annealing, spheroidizing annealing, stress relief annealing, recrystallizing annealing and stabilizing annealing, magnetic field annealing and more.
1. Metal tools may lose their original hardness due to exposure to heat during use.
2. Heating the metal material or workpiece to a specific temperature and holding it for a certain time allows for slow cooling. Annealing can decrease the hardness and brittleness of the metal and increase its plasticity. It is also known as mallation.
Purpose of Annealing
1) To reduce hardness and increase machinability;
2) Mitigate residual stresses, stabilize dimensions and reduce deformation and cracking tendencies;
3) To refine grain structures, adjust microstructure and eliminate structural defects.
In production, annealing processes are widely used. According to the different annealing objectives required by the part, there are various specifications for the annealing process, such as full annealing, spheroidizing annealing and stress relief annealing.
2. Normalizing
Normalization, also known as normalization, is a metal heat treatment process where the part is heated to a temperature of 30 to 50°C above Ac3 or Accm, held for a certain period and then removed from the furnace to cool in air or by water spray, mist or air blow.
Its purpose is to refine the grain size and homogenize the distribution of the carbide. Normalizing differs from annealing in that the cooling rate during normalizing is slightly faster than that during annealing, resulting in a finer normalizing structure and improved mechanical properties.
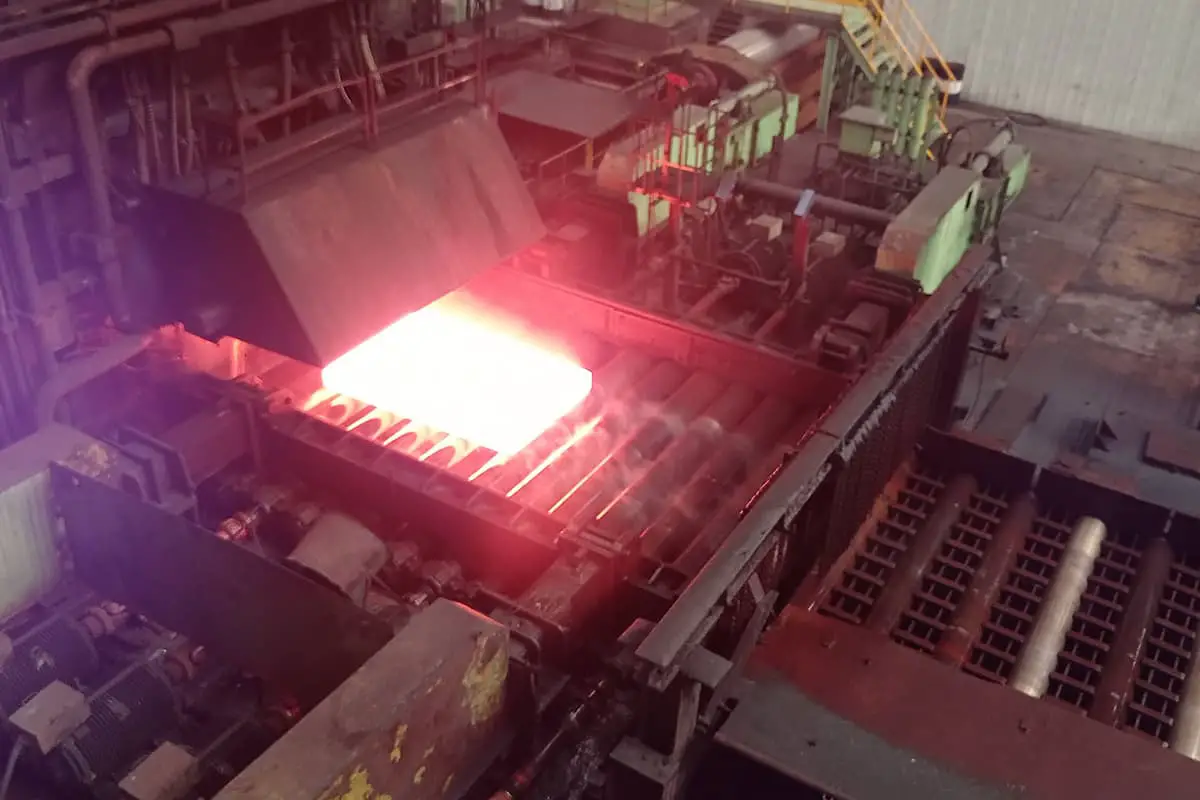
Furthermore, normalization by cooling outside the oven does not take up equipment, thus achieving a higher production rate. Therefore, normalizing is used as much as possible in production to replace annealing.
Normalization applications
1) For low carbon steel, the hardness after normalizing is slightly higher than that after annealing, and the toughness is also better, making it suitable as a pretreatment for machining.
2) For medium carbon steels, it can replace tempering as a final heat treatment, and also serve as a preparatory treatment for surface hardening conducted by induction heating.
3) For tool steel, bearing steel and carburizing steel, it can reduce or suppress the formation of network carbides, thus obtaining the ideal structure required for spheroidization annealing.
4) For cast steel parts, it can refine the casting structure and improve machinability.
5) For large forged parts, it can serve as a final heat treatment, thus avoiding a great tendency for cracks during hardening.
6) For ductile cast iron, it improves hardness, strength and wear resistance and is used in manufacturing important components such as crankshafts and connecting rods in automobiles, tractors and diesel engines.
7) For hypereutectoid steel, performing normalization before spheroidization annealing can eliminate secondary cementite from the network, ensuring complete spheroidization of cementite during spheroidization annealing.
Post-normalization structure: The structure of hypoeutectoid steel is F+S, eutectoid steel is S, and hypereutectoid steel is S + secondary cementite and is discontinuous.
The metal heat treatment process involves heating the part to an appropriate temperature (Ac3 or ACcm plus 30-50°C) (see steel microstructure) and then cooling in air after insulation. Normalization is mainly used for steel parts.
Normalized steel is similar to annealed steel, but it cools a little faster and has a finer structure. Some steels with a very small critical cooling rate can transform austenite into martensite by air cooling, but this treatment is not considered normalization, but rather called air cooling quenching.
On the contrary, some large-section parts made of steel with a higher critical cooling rate cannot obtain martensite even if they are quenched in water, and the quenching effect is close to normalization.
The hardness of steel after normalization is higher than that of annealing.
During normalizing, it is not necessary to cool the part with the furnace as during annealing, which saves furnace time, improves production efficiency, and is therefore generally replaced by normalizing as much as possible in production.
For low-carbon steel with a carbon content of less than 0.25%, the hardness achieved after normalizing is moderate, which is more conducive to cutting than annealing, and generally normalizing is used to prepare for cutting.
For medium carbon steel with carbon content of 0.25-0.5%, it can also meet the cutting requirements after normalization.
For lightweight parts made from this type of steel, normalizing can also serve as a final heat treatment.
The standardization of high-carbon tool steel and bearing steel aims to eliminate network carbides in the structure and prepare the structure for spheroidized annealing.
Heat Treatment Process for Steel Parts – Standardization
Steel heat treatment is divided into two categories: general heat treatment and surface heat treatment.
Common general heat treatments include annealing, normalizing, quenching, and tempering; Surface heat treatment can be divided into surface quenching and chemical heat treatment.
Normalizing is a heat treatment process in which the steel part is heated to a critical temperature above 30-50°C, held for an appropriate time and then cooled in still air.
The main objective of normalization is to refine the structure, improve the performance of the steel and obtain a structure close to the equilibrium state.
Compared with the annealing process, the main difference in normalizing is that the cooling rate of normalizing is a little faster, so the production cycle of normalizing heat treatment is shorter.
Therefore, when annealing and normalizing can meet the performance requirements of parts, normalizing should be chosen as much as possible. Most medium and low carbon steel raw materials generally use normalizing heat treatment.
Alloy steel blanks in general often use annealing. If normalized, due to the faster cooling speed, the hardness after normalization is higher, which is not conducive to cutting processing.
3. Difference between normalizing and annealing
The heat treatment process involves heating the part to a suitable temperature, maintaining that temperature for a period of time, and then removing it from the oven for outdoor cooling.
The difference between normalizing and annealing is that the cooling rate of normalizing is slightly faster than annealing, resulting in a finer structure in normalizing than in annealing, thus improving the mechanical properties.
Furthermore, the normalization of cooling outside the furnace does not occupy equipment, resulting in a higher production rate. Therefore, normalizing is used as much as possible in production to replace annealing. The main normalization applications include:
1. For low-carbon steels, the hardness after normalizing is slightly higher than that of annealing, with better toughness, serving as pre-treatment for cutting.
2. For medium carbon steel, it can replace quenching treatment as final heat treatment or serve as preparatory treatment before surface hardening using induction heating.
3. For tool steel, bearing steel and carburized steel, it can reduce or inhibit the formation of liquid carbides, thus obtaining the good structure required for spheroidized annealing.
4. For cast steel parts, it can refine the casting structure and improve machinability.
5. For large forged parts, it can serve as a final heat treatment, thus avoiding the greater tendency to cracks during quenching.
6. For ductile iron, it can improve hardness, strength and wear resistance, making it suitable for manufacturing important parts of vehicles, tractors, diesel engines, such as crankshafts and connecting rods.
The main difference between annealing and normalizing is in the cooling rate, with normalizing having a faster rate, resulting in a finer pearlite structure. Thus, for the same steel, normalizing produces greater strength and hardness than annealing.
The choice between annealing and normalizing should be based on specific situations, generally considering three aspects:
1) To improve machinability; low carbon steel must be standardized. Medium carbon steel with carbon content between 0.25% and 0.45% can be annealed or normalized. High-carbon steel with carbon content between 0.45% and 0.77% must be fully annealed, while hypereutectoid steel must undergo spheroidizing annealing. (Low and medium carbon structural steel – normalizing, medium and high carbon structural steel – full annealing, alloy tool steel – spheroidizing annealing)
2) Heat treatment processability; Complex shaped, large or important pieces must be annealed. Because annealing cools slowly, internal stress is minimized and the part is less likely to warp or crack. Normalization can be used for general parts.
3) Processing cost; normalizing is less expensive than annealing. To reduce costs and improve production efficiency, standardization should be used as much as possible while ensuring quality.
Table of Annealing and Hardening Processes
Process name | goal | Scope of application | Observation |
Complete Annealing | (1) Refine grain structure.
(2) Eliminate Widmanstätten and banded structures. (3) Reduce hardness and increase plasticity to improve machinability. (4) Mitigate internal stress. (5) For castings, remove coarse grains to improve impact resistance, plasticity and toughness. |
(1) For small and medium-sized hypoeutectoid steel castings, forgings and hot-rolled steel parts.
(2) For the preliminary heat treatment of hypoeutectoid steel. |
(1) Use on hypereutectoid steel is not advisable as it leads to the formation of mesh-like carbides, thus reducing the toughness of the material.
(2) For large castings and forgings, complete annealing is employed; however, due to the effects of tension, deformation and cracking may occur, requiring immediate stress relief. |
Incomplete Annealing | (1) Decrease hardness, increase plasticity and improve machinability.
(2) Eliminate internal stress. (3) Obtain spheroidized perlite. |
(1) Hypereutectoid steels, featuring a non-crosslinked carbide structure, are rarely used for hypoeutectoid steels.
(2) Heat pretreatment is used for high-carbon steels and bearing steels. |
When there are lattice carbides in hypereutectoid steel, it must be normalized first and then subjected to incomplete annealing. |
Spheroidizing Annealing | (1) Obtain spheroidized pearlite and eliminate small network structures in hypereutectoid steel.
(2) Reduce hardness, increase plasticity and strength. (3) Improve machinability. (4) Serve as preparatory heat treatment before tempering. |
This process is employed to improve the structure of carbon tool steel, alloy tool steel and bearing steel with a ωc greater than 0.65%. It improves its machinability and prepares the structure for final heat treatment, thus guaranteeing superior performance. | Spheroidizing annealing is a specific case and a progression of incomplete annealing. |
Isothermal Annealing | (1) The use of isothermal annealing results in a uniform pearlite structure due to the decomposition of austenite at constant temperature, especially for parts with a large cross section. This leads to consistent mechanical properties.
(2) Isothermal annealing allows steel, which is difficult to transform into pearlite through conventional annealing methods, to obtain a pearlite structure. This facilitates machining and shortens the production cycle. |
(1) Isothermal annealing, widely adopted in production due to its purpose, is especially used for hypoeutectoid steels and eutectoid steels.
(2) Annealing of alloy steels is almost entirely replaced by isothermal annealing, as opposed to the traditionally used total annealing. |
The grain size and hardness obtained at different isothermal temperatures vary. At higher isothermal temperatures, the grain is coarser and the hardness is lower. On the other hand, at lower temperatures, the grain is finer and the hardness is greater. |
Diffusion Annealing | Eliminate dendritic segregation in ingots and castings to unify composition and structure, thereby improving performance and facilitating machining operations. | (1) Mainly used for casting large-scale ingots and castings.
(2) For high-alloy steel forgings, diffusion annealing is implemented to prepare the microstructure for further heat treatment and machining. |
Due to the long production cycle and substantial electricity or fuel consumption in diffusion annealing, parts with less stringent requirements generally do not undergo this process. |
Recrystallization Annealing | (1) Metals subject to cold deformation can be relieved from hardening by recrystallization annealing. This process eliminates internal stresses, reduces hardness and increases ductility, thus facilitating further mechanical processing.
(2) After hot processing, due to rapid cooling, recrystallization is not complete, resulting in high internal stress and hardness, requiring recrystallization annealing. |
(1) Used to restore structure and performance before cold deformation (e.g. cold rolling, cold drawing and cold punching) while eliminating internal stresses.
(2) Implemented as an intermediate operation in cold deformation to facilitate further processing. |
When steel parts undergo irregular cold deformation or are subjected to critical amounts of deformation approximately between 5% and 15%, performing recrystallization annealing can easily result in a coarse-grained structure. |
Stress Relief Annealing | (1) Eliminate internal stress and stabilize dimensions to reduce deformation during machining and use.
(2) Lower hardness to facilitate cutting and machining. |
(1) Used for castings and forgings such as bed frames, engine blocks and transmission housings.
(2) Used for high-alloy steels, mainly to reduce hardness and increase machinability. (3) For high-precision parts, in order to eliminate stress after machining and stabilize dimensions, a lower temperature (200-400°C) is maintained for an extended period. |
(1) For large parts and when the furnace load is substantial, it is appropriate to extend the insulation time accordingly.
(2) When stress relieving standard castings, to avoid a reduction in strength due to secondary graphitization, the heating temperature should not exceed 600°C. |
High temperature annealing | Eliminate white mouth and free cementite, decompose cementite to improve machinability and increase plasticity and toughness. | Used for gray iron and ductile iron parts (when white mouth occurs). | Generally, malleable cast iron is not used. |
Mallebilizing annealing | By causing cementite to decompose, flaked graphite is obtained, which significantly increases strength and plasticity. | Used to convert white cast iron into malleable cast iron. | During the annealing cooling process, if air cooling occurs before reaching 650°C, the material maintains good toughness. However, brittleness may occur during oven cooling. |
High temperature graphitization annealing | Eliminate free cementite in the cast structure, improve machinability, reduce brittleness and improve mechanical properties. | Commonly used for ductile iron (when a certain amount of free cementite causes white mouth). | During cooling, brittleness appears if the temperature is gradually reduced in the range of 600 to 400 degrees Celsius. Therefore, after maintaining the annealing temperature, the furnace must be cooled to approximately 600 degrees Celsius and immediately removed for air cooling. |
Low temperature graphitization annealing | Obtain ductile iron with a high tenacity ferritic matrix. | Often used for ductile iron (when only pearlite appears in the cast structure, without free cementite). | When the presence of perlite is not allowed in the base structure, the heat preservation time must be extended appropriately; otherwise it may be slightly reduced. |
Low temperature annealing | Reduce the brittleness of castings, improve machinability and improve toughness. | Commonly used for gray cast iron and ductile iron (when no cementite appears, only pearlite is present). | If free cementite is present in the cast structure, high temperature annealing is used instead of this annealing process. |
Normalizing | (1) Increase the hardness of low carbon steel to improve its machinability.
(2) Refining the grain structure (such as eliminating Widmanstätten structure, banding, large ferrite grains and network carbides) to prepare for final heat treatment. (3) Relieve internal stresses, enhancing the performance of low carbon steel as a prerequisite for final heat treatment. |
(1) Mainly used for low carbon steel, medium carbon steel and low alloy steel. High-carbon steel and high-carbon alloy steel are not commonly used except when cross-linked carbides are present, as these materials undergo martensitic transformation after normalization.
(2) Employed for quenching repair parts, this technique mitigates internal stress and refines the structure to prevent warping and cracking during re-quenching. |
Compared to annealing, normalizing has a shorter production cycle and higher equipment utilization. Furthermore, it can improve the mechanical properties of steel. Therefore, depending on the material and technical requirements, normalizing can be used as a substitute for annealing in certain situations. |
High temperature normalization | Improving uniformity within the structure, improving machinability, increasing strength, hardness and wear resistance or eliminating white mouth and free carbides. | Mainly used for ductile iron parts that require high strength and excellent wear resistance. | When free cementite is present in the cast structure, the annealing temperature should be adjusted to the upper limit. Castings with high silicon content must be cooled more quickly to prevent graphitization. |
Low temperature normalization | Achieving excellent strength, toughness and ductility. | Mainly used for ductile iron components where high strength and toughness are required, but the demand for wear resistance is not particularly high. | During the process of using local pig iron to smelt ductile iron, it is challenging to ensure adequate plasticity and strength due to the high sulfur and phosphorus content. Employing low-temperature annealing can effectively compensate for the lack of plasticity and toughness induced by this problem. |