Grinding burn is the biggest danger in gear grinding after heat treatment.
Based on practice, this article presents an acid etching method to detect grinding burns and provides a comparative demonstration.
The purpose of gear grinding after heat treatment is to correct the deformation during heat treatment, improve gear precision and reduce noise.
The fatigue performance of gears is related to surface hardness, surface tension distribution and surface microstructure of the tooth surface.
The contact stress during gear operation and the improvement of contact accuracy between gear teeth after grinding reduce the possibility of contact fatigue stress concentration, which leads to the improvement of contact fatigue life.
The surface layer of gear parts will burn in the grinding process, which will greatly reduce the performance and service life of the product, or even cannot be used, causing serious quality problems.
Therefore, on the one hand, production enterprises must reduce and avoid grinding burn through implementing correct and scientific process specifications;
On the other hand, it is necessary to strengthen the process inspection of parts and components, find unqualified parts in time, and monitor the conditions of the grinding process in real time.
1. Grinding burning mechanism
During grinding with a grinding wheel, when the instantaneous high temperature (generally 900 ~ 1500 ℃) in the grinding area reaches above the phase change temperature, the metallographic structure of the workpiece surface will change, and some parts of most surfaces will be oxidized and discolored.
This reduces the strength and hardness of the metal surface, accompanied by residual stresses and even microcracks.
This phenomenon is called “grinding burn” and the process is shown in Fig.
When the grinding surface produces high temperature, if the heat dissipation measures are not good, it is easy to have secondary quenching and high temperature tempering on the surface of the workpiece.
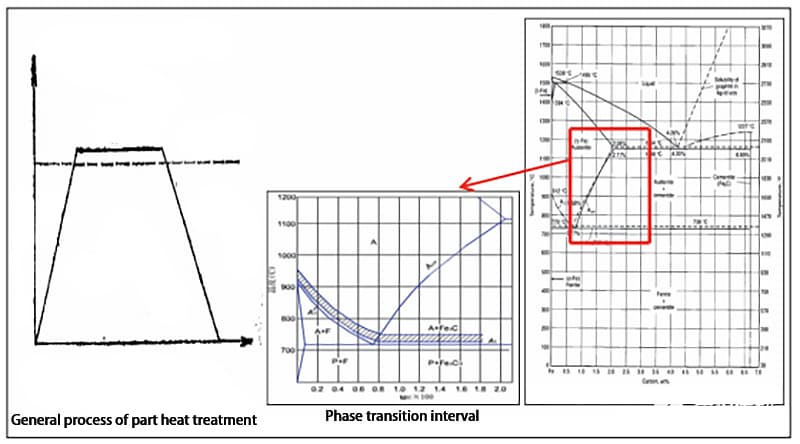
Figure 1 Grinding burn
2. Change and damage to the metallographic structure of the gear surface
After grinding burnout, the metallographic structure of the gear surface will change and produce some adverse consequences.
Quenching cracks:
The instantaneous temperature of the surface layer of the grinding part exceeds AC1 727+(30~50) ℃ of the steel grade, and the secondary quenching martensite is formed under the action of the coolant.
Under the surface layer, due to the large temperature gradient and short period of time, only high-temperature tempering structure can be formed, which will generate tensile stress between the surface layer and the underground layer, while the surface layer is a fine and brittle secondary temper martensite.
When the surface layer cannot withstand the tensile stress, cracks will be generated.
Extinguish burn:
When the temperature in the grinding area exceeds the AC1 phase transformation temperature 727+(30~50) ℃, local areas on the surface of the workpiece will become austenite, and then secondary quenched martensite will appear on the surface, an extremely thin due to the rapid cooling effect of the coolant and the heat conduction of the workpiece itself.
The secondary surface layer is sorbite quenched to greatly reduced hardness, which is called secondary quench firing.
Annealing burn:
If the temperature in the grinding area exceeds the phase change temperature and there is no coolant entering the grinding area, the metal surface will have an annealed structure and the surface hardness will drop drastically.
This type of burn is called annealing burn.
Temper Burns:
When the temperature in the grinding zone is significantly higher than the tempering temperature of the steel but still lower than the phase transformation temperature, the surface of the workpiece appears as quenched troostite or softened quenched sorbite structure.
3. Grinding burn detection method
At present, grinding burn detection methods include: color observation method, acid etching method, microhardness method, metallographic detection method and magnetoelastic method (Barkhausen noise method).
According to the actual demand and processing process, our company selects the acid etching method to detect grinding burns.
Acid etching method 1 (nitric acid solution acid etching method) includes 11 steps: pre cleaning → preheating → acid leaching etching (nitric acid solution + methanol) → washing → dehydration → bleaching (hydrochloric acid + methanol solution) → washing → neutralization → washing → dehydration → rust prevention.
Method 1 Etch solution must be prepared before each acid etching test for grinding burn.
After preparation of the solution, the volumetric percentage concentration of acid in the etching solution must be measured by acid-base neutralization titration.
The color of the secondary tempering area is light brown to black, that is, the color is darker than the uniform gray of the normal acid etching surface;
The re-extinction area is light gray to white with a light brown to black border around it;
Finally, the degree of burn was assessed.
Burn classification is based on the area and degree of grinding burn.
It is divided into 4 grades, namely A, B, D and E, as shown in Figure 2-5.
Recently, the customer recommended the use of method 2 slag inhibitor technology for acid corrosion.
The slag inhibitor solution acid etching method includes six steps: pre-cleaning → preheating → nitric acid solution etching (nitric acid + water + slag inhibitor solution) → drying → washing → rust prevention.
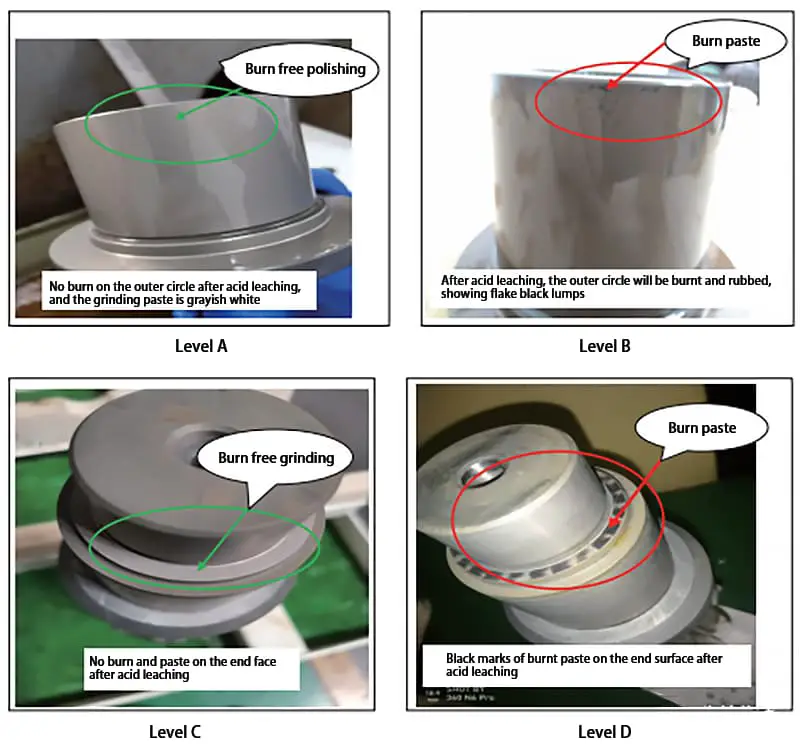
Acid Etching Process:
Put the cleaned parts into nitric acid corrosion solution (nitric acid solution + water + slag inhibitor), shake the parts continuously for a certain period of time, require the surface to form a uniform black oxide film, remove the parts and wash them, dehydrate them, place the pieces in bleach solution (hydrochloric acid + methanol solution) for bleaching after dehydration, shake continuously for a few seconds, and the surface will have a uniform gray color, wash them after remove them.
After neutralization, rinsing, dehydration and drying, the surface of the parts must be visually inspected to assess whether there is a grinding burn.
The evaluation method is the same as method 1.
The above two inspection methods are comprehensively compared.
Step comparison: method 2 has fewer steps, is simple and quick, and method 1 has more steps.
When the same part is soaked in acid to detect burns, method 2 is significantly more convenient than method 1.
Economic comparison: the chemical reagents nitric acid, hydrochloric acid and methanol used in method 1 are cheap.
The anti-slag additive anti Smut 100 used in method 2 is 25 kg per barrel, with a cost of about 30,000 yuan.
Consult the table for its characteristics.
Table anti-smut100 features
Anti Smut100 is an anti-slag additive for nitric acid etching solution |
|
Product Feature |
Restrict the adhesion of residues to the surface of the part during nitric acid attack; Very stable in nitric acid; Easily soluble in solution; Very good wettability. |
Application |
Anti Smut100 is recommended for various nitric acid etching solutions (such as chemical etching inspection on high-strength alloy steel parts); Anti Smut100 slag inhibitor should be dissolved in the etching solution at room temperature and gently stirred by hand to mix evenly; Typical etching solution compositions are as follows: 03%~5% V/V nitric acid; 3% ~ 5% slag inhibitor; The rest is water. |
According to annual usage, the cost of method 2 is still much higher.
In summary, it is concluded that the method has fewer steps, shortens the detection process, saves detection time, improves detection efficiency, has greater sensitivity to acid attack and uses fewer chemicals.
Since the aqueous solution of nitric acid is used, the solution is used for a long time and can be used for 4 to 6 months after it is prepared.
It is recommended to use this method for products with strict inspection requirements in the aerospace industry.
Method 1 has slightly more processes, a slightly longer detection time, and a short solution service time.
After a period of time, the solution becomes cloudy and needs to be replaced frequently.
Furthermore, the volume percentage of the solution needs to be detected each time and the sensitivity is not as high as Method 2.
It is generally suitable for routine inspection of automotive gear parts companies.
4. Conclusion
Grinding burn is the biggest danger in gear grinding after heat treatment, which must be overcome to avoid after-sales quality problems.
The acid etching method is a relatively simple, scientific and standardized method for detecting grinding burns.
Compared with the detection steps, the method is labor-saving, fast and more sensitive;
From an economic point of view, method 1 is economical and practical.
Each company can select according to its real needs.