The compressor is an essential device that can be used both in the home garage and in a professional workshop. Today we answer the question of which compressor is suitable for the workshop.
Using a compressor we obtain compressed air, an excellent source of energy. However, it must be emphasized that producing compressed air costs money. And that's a lot.
The compression process that takes place in the compressor is associated with large energy losses in the form of heat, which have a direct impact on our electricity bills.
There are many reasons why it is worth equipping your workshop with pneumatic tools. Firstly, they are much more powerful and therefore more efficient compared to power tools.
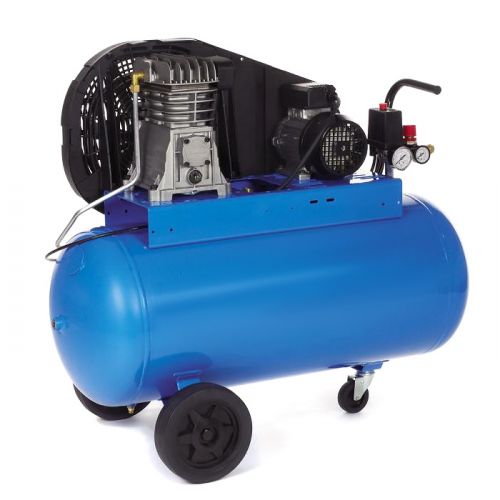
Secondly, pneumatic tools are often more durable and lighter. Thirdly, its work excludes the possibility of sparks.
And finally, there's the issue of cost: Although compressed air tools are more expensive to buy, they are significantly cheaper to repair and operate.
However, the variety of offers on the market sometimes makes decision-making difficult. A low price is important, but not the most important. When choosing a compressor, it is worth assuming a maximum limit for such a purchase.
However, before we answer the question of which compressor is suitable for the workshop, it is good to familiarize yourself with the general selection of compressors on the market (you can learn more about compressor types here).
Factors Affecting the Selection of the Appropriate Compressor
Choosing the right compressor for your workshop is crucial, as its efficiency and effectiveness depend on it. Before deciding to buy “which compressor for workshop?”, you should pay attention to several important factors such as capacity, power, pressure and efficiency.
Compressor capacity is one of the most important factors you should consider when choosing a compressor for your workshop. This is the amount of air it can store and deliver to your pneumatic tools. The larger the capacity, the better.
The performance of the compressor is equally important, as it determines its ability to work at different pressures. The more power, the better the compressor can handle heavier tasks. Which workshop compressor is right for your needs depends on which pneumatic tools you want to use.
Compressor pressure is another important factor to consider when choosing a compressor for your workshop. This is the force with which air is supplied to pneumatic tools. The higher the pressure, the better the compressor can handle heavier tasks.
Compressor performance is the last important factor you need to pay attention to when choosing the compressor for your workshop. Determines the amount of air the compressor can deliver per unit of time. The higher the efficiency, the better the compressor can handle heavier tasks.
In summary, capacity, power, pressure and efficiency are important factors to consider when choosing the right compressor for your workshop.
To ensure that the compressor selected for the workshop meets all requirements, you must carefully analyze your needs and requirements – only then can you answer the question of which compressor is suitable for the workshop. The capacity and performance of a compressor are important for its ability to operate at different pressures. A compressor's pressure is important to its ability to handle heavier tasks, and efficiency is important to its ability to deliver the right amount of air at the right time.
Remember that choosing the right compressor for a workshop is a long-term investment. Therefore, it is important to carefully consider your decisions.
Types of workshop compressors
The most popular are certainly:
– Piston compressors (oil and oil-free),
● Oil – they are more efficient and intended for intensive use. The compressor pump of this model requires regular oil lubrication
● Oil-free – much less efficient, maintenance-free and intended for simple household tasks, such as inflating tires or mattresses.
– screw compressors (oil and oil-free)
– Vane compressors
– Scroll compressors
The latter are characterized, for example, by their small size, simple construction and maintenance-free operation of up to 10,000 hours.
Decisions should not be made hastily. Investing in a compressor must be preceded by an analysis of your own needs, taking into account the intensity of the work and the tools used.
The basic criterion to take into account is the air flow that our workshop needs, that is, the sum of the compressed air needs.
This must be carefully calculated taking into account any equipment powered by compressed air. An important question must also be asked whether the compressor operates continuously or intermittently. This is crucial when choosing Compressor type.
In a small to medium-sized workshop, a medium-sized piston compressor with a power of 2 to 4 kW works best.
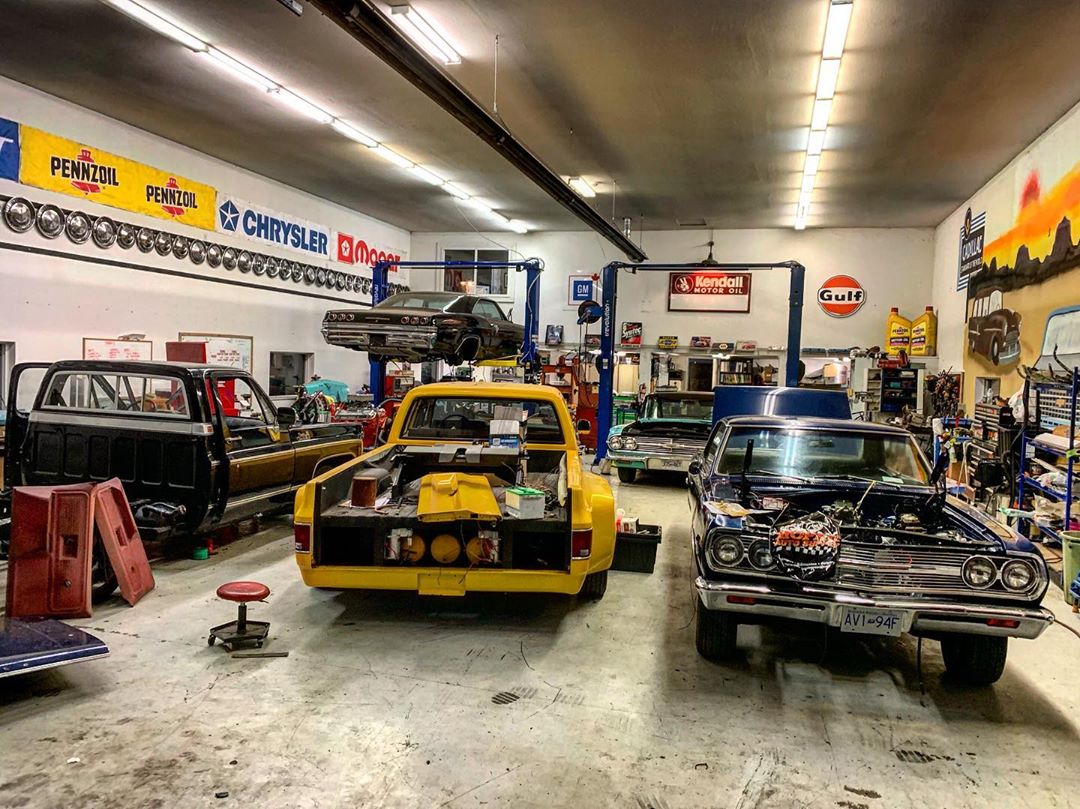
This performance should be sufficient as it is sufficient for most needs. If you have more air-powered devices, it is safer to choose a compressor with a power of 5.5 – 7.5 kW and a tank of 270 – 500 l.
However, if you have a larger workshop that requires large amounts of compressed air, a screw compressor is worth considering.
Among other things, because it is more difficult to achieve greater efficiency with piston compressors.
Furthermore, piston compressors are not as economical as screw compressors. A screw compressor has significantly greater energy efficiency, which means it produces greater quantities of compressed air with the same electric motor power.
And this, in turn, is reflected in electricity costs, which the screw compressor uses less.
It's also worth checking what level of noise the compressor produces. As you know, a piston compressor is not silent, but a screw compressor is. Yes, there are silent piston compressors on the market, but their price is higher.
When choosing a compressor for a workshop, pay attention to the quality of the components from which it is made. A good pump or screw module is essential because they are the “heart” of the compressor.
A very important issue is the availability of the website.
Below you will find some examples of compressed air requirements.
Carpentry and upholstery work
They are used for carpentry and upholstery work: staplers, mini nailers, staplers-nailers, jigsaws.
The right compressor for carpentry and upholstery work should be able to deliver the right amount of compressed air to power your tools. Below we present an example of the demand for carpentry tools:
- Angle grinder – 150-350 l/min
- nailer – 00-250 l/min
- drill – 120-400l/min
Grind
If you want to grind elements occasionally, you will need a compressor with a capacity of at least 4 – 5.5 kW and a tank of at least 2.5 kW 200 liters.
For professional use, we recommend screw compressors with significantly higher performance efficiency.
Painting
When choosing a painting compressor, it is important that it is capable of delivering the right amount of compressed air for continuous painting operations.
When painting smaller elements, a 100L compressor with a capacity of 200-250L/min can be used, while for painting larger elements we recommend a compressor with a tank capacity of at least 150-200L and a capacity greater than 300 l/min
vulcanization
For typical vulcanization work, it is worth choosing a compressor with a power of at least 3 kW. However, to ensure the best working comfort, it is worth choosing a compressor with a power equal to or greater than 4 kW, that is, at least 400-500 l/min.
Car mechanic
In these workshops, compressed air is most commonly used to drive pneumatic elevators, pneumatic wrenches, grinding machines, or for blowing.
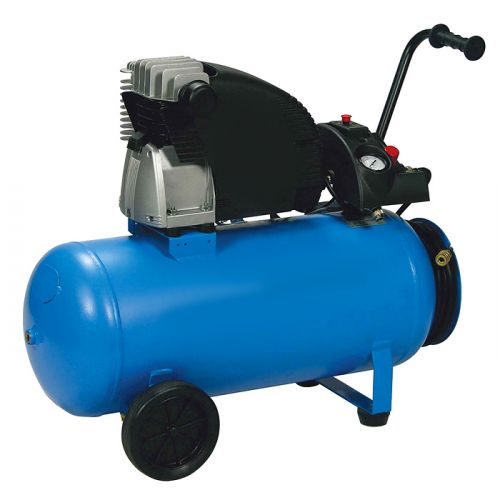
To achieve the required minimum, a compressor with a capacity of at least 200 liters and a capacity of at least 400-500 liters or more is required, depending on the number of compressed air tanks.
Criteria for choosing a compressor for the workshop
When choosing a compressor for a workshop, we must consider the specific tasks that require compressed air.
The basic criteria are efficiency, tank capacity, engine power and compressor type.
Other criteria when choosing a compressor are noise level, service availability, manufacturer (i.e. quality of finish) and, of course, price.