The development of a country's aviation industry reflects the quality of skill and technical knowledge it possesses. The requirements for structural strength, precision, accuracy, quality and reliability are critical for this industry. The concept of improving aircraft design and speeding up production processes has always been a challenge.
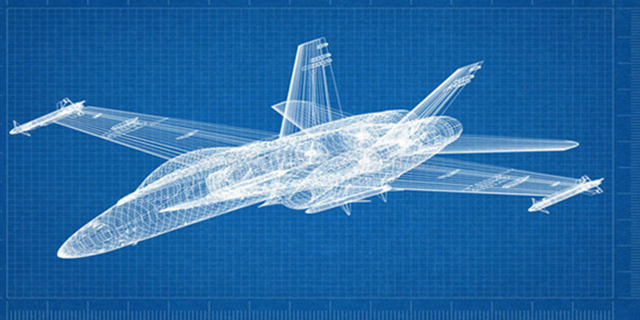
Therefore, CNC machining and prototyping have found their way into this industry. CNC machines that can meet strict tolerance requirements provide a great solution for meeting a variety of needs while keeping up with the pace of production. As the article progresses, we will discuss in detail the various parameters that play a role in the aviation industry and how CNC technology is revolutionizing it.
Why is CNC technology suitable for the aviation industry?
A Lufthansa article stated that Boeing needed 6 million parts to build the 747-800 plane. CNC technology offers several advantages to the aviation industry. Let's discuss some of them:
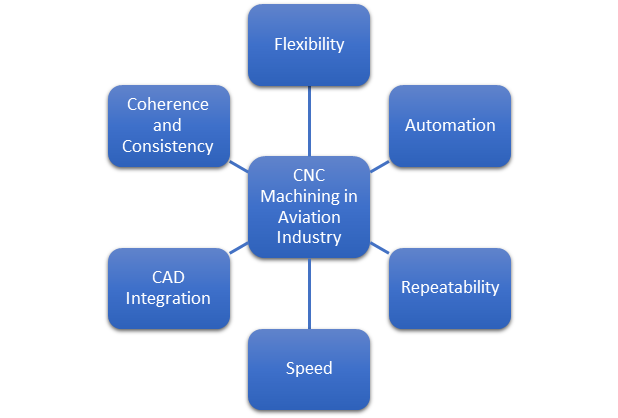
- Automation and flexibility are two important parameters in the aviation industry. Production lines are not redundant. CNC technology allows production lines to be quickly adapted to different parts. Therefore, various machining processes can be carried out. Multiple CNC processes can be performed on the same machine using a single fixture. This helps to significantly reduce processing and production time, thereby increasing profit margins and efficiency.
- Manufacturing parts using this method offers numerous benefits, including accuracy, repeatability, speed, and CAD integration.
- Unlike manual milling, which is controlled exclusively by humans, there are large variations between copies, while duplicates created with CNC milling always guarantee a perfect copy of the object. The integration of Computer Aided Design (CAD) into CNC milling machines allows for better performance and the production of perfect copies. You can design, modify or remodel any part as needed before production. The CAD carved design can be easily customized so that different programs can be created. When the design is fed into the CNC machine, the milling machine can produce a physical copy of the part. This can lead to quick and easy prototyping.
- Technological advancement not only in the commercial sector, but also in a country's armed forces, has increased the demand for aircraft with consistent quality and minimal defects. To produce perfect copies of parts with precision and meet the demand of companies like Boeing, Lockheed-Martin, Vickers and others, CNC machines are the best substitute. CNC machines guarantee consistency and coherence in the parts produced, allowing the manufacture and use of better quality products in the aeronautical industry. Many of today's aerospace parts must be made from a single solid piece of billet aluminum or forgings, or other materials such as stainless steel and other strong alloys so that they can lift heavy weights and provide structural strength to the aircraft. Copies of these parts can be easily made on CNC machines without any differences.
- Increased demand from aircraft manufacturers looking for aircraft parts has paved the way for countless companies to invest millions of dollars in companies that provide CNC machining services in the commercial and military sectors. Large companies have gone so far as to produce enormous pieces measuring 50 inches in diameter, 60 inches in length, 40 inches in width and 32 inches in height. The total weight of CNC machined parts can exceed 100 pounds. These CNC machining service providers can afford and accommodate these large computer-controlled numerical milling machines and also provide manufacturers with parts that meet strict tolerance criteria. Areas in which tolerances are measured include flatness, roundness, and cylindricity; Flatness up to ±0.000002 inches, diameter roundness ±0.00005 inches and cylindricity ±0.001 inches. These tight tolerances play an important role in parts like the landing gear, of which Raymer says, “Of the many internal components that need to be defined when designing an aircraft, the landing gear typically causes the most problems.”
- Tolerances play an important role in parts where there is little room for sizing errors. There are CNC machining companies that specialize in producing these parts. The manufacturing of aircraft parts has forced companies to invest in equipment that allows them to complete manufacturing in a single setup.
CNC machining applications in the aviation industry
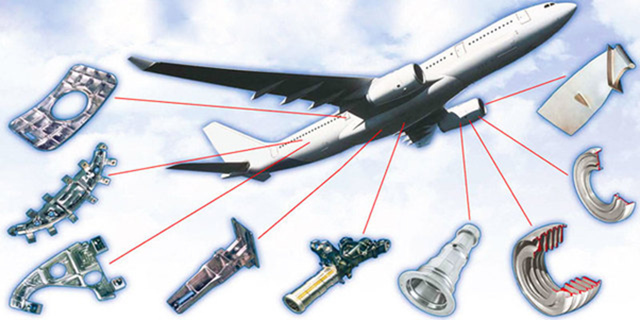
The increasing complexity of modern aircraft parts demands enormous precision. What began in 1903 with wood, wire and other basic materials quickly evolved into industry's use of modern composites and metals. Today's modern aircraft feature a complex avionics system, state-of-the-art hydraulic systems, aerodynamically optimized control surfaces, trim and servo flap systems, and revolutionary engine systems.
Because these systems are evolving rapidly, there is always a need for custom parts to improve existing aircraft. For some improvements, it is not always feasible to design completely new aircraft from scratch. To reduce costs, a list of upgrade options and spare parts for different types of aircraft is created. Orders for similar special parts are then combined, providing compatibility and cost savings. For example, an older Boeing 747 series that needs to be upgraded to the latest fly-by-wire control system does not require the entire aircraft to be manufactured from scratch. Instead, components of the respective system are processed.
Likewise, critical developments in the aviation industry require intensive testing. CNC prototyping is of great help in this regard. It is used in the manufacture of structural components, avionics, propulsion systems and aerodynamic parts.
After discussing the need for custom parts and prototypes, let us now discuss some important parts that are manufactured using CNC machining:
Paper | material | Manufacturing process |
aileron housing |
15-5PH H1025 Stainless Steel Thread |
5-axis CNC milling |
Reflectors for side headlights |
6061-T6 aluminum |
5-axis CNC milling |
Housing for the brake system control valve |
aluminum 2024-T351 |
4-axis CNC milling |
The seat of an airflow regulating valve |
347 stainless steel |
5-axis CNC machining |
Brake system check valve |
18-8 stainless steel, condition B |
Precision turning |
Flap hinge |
Inconel 718 |
3-axis CNC milling |
engine piston |
aluminum 7075-T651 |
Conventional CNC turning |
Swivel mount |
aluminum 2024-T351 |
4-axis CNC milling |
And this list doesn't end here!
Materials used in manufacturing include aluminum, titanium, stainless steel, Inconel, Kovar and copper. Types of machining generally used in aircraft parts manufacturing include 3-, 4-, and 5-axis CNC milling, turning, wire electrical discharge machining (EDM), deburring, micromachining, and sink EDM (EDM).
A notable example in this regard is Thompson Aero Seating, a provider of aircraft seating solutions in Northern Ireland. The company hired a CNC machining services provider to produce aluminum support rails for its commercial seating frames, with the aim of achieving shorter cycle times. By using CNC milling, cycle times have been reduced by 100%, from 61 minutes to just 32 minutes! Furthermore, the excellent surface processing by CNC milling made it possible to avoid deburring and polishing processes.
University Degree
Given the facts of this article, the central role of CNC prototyping and machining is quite obvious. From achieving precise tolerances to reducing cycle times, CNC machining offers a comprehensive solution. Furthermore, given the current innovation activity in the aviation industry, CNC prototyping provides all the machining steps necessary to comprehensively analyze performance, aesthetics and manufacturability.