If you choose CNC machining as your part manufacturing method, you should know that depth of cut (DOC) is one of the three most important parameters that affect the quality of the machined product.
In this article you will learn what depth of cut means in machining, why it is necessary to control it, what is the difference between chip thickness and depth of cut and how it is calculated.
What is the cutting depth during machining?
In the machining process, depth of cut is simply the depth to which the cutting tool penetrates and cuts a workpiece to produce a chip. In an ideal cutting process, the CNC cutting tool produces a chip as it moves to the left on the surface of the part to a certain depth. This depth is called depth of cut or DOC. If you need a similar and easy application, you can check out how to cut chocolate chips or shavings.
Cutting depth is measured in inches or millimeters and generally varies between 0.1 and 1 mm.
Why do you need to control the cutting depth when editing?
The cutting depth has a direct impact on the machining process, for example:
- Heat builds up at the tip of the tool;
- tool wear rate;
- resistance of the processed product;
- The quality of the processed surface.
For example, annealed metals have a greater tendency to form built-up edges (BUE) during the cutting process than cold-formed metals. The BUE chip type consists of layers of chips that accumulate at the tool tip. If the cutting depth is too large, an uncontrolled built-up edge will also have a negative effect on the surface quality.
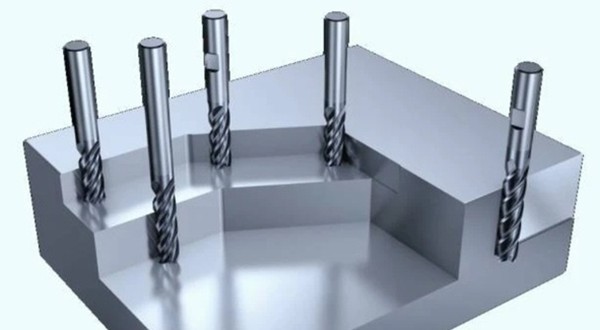
How does depth of cut interact with other machining factors?
The cutting depth is one of the independent factors that affect the machining process, that is, it is controlled by the operator. However, cutting depth interacts with other factors and affects the resulting surface of the part and its properties.
Cutting depth and coolant
As the depth of cut decreases, the chip curvature decreases and the chip becomes wavy. In this case and with the increase in heat at the tip of the tool, one might think that the addition of coolant would cool the process.
However, adding CNC coolant makes the chip even more curved, reduces tool-to-chip contact, and concentrates heat in the tool, significantly increasing tool wear. In this case, a chip breaker may be useful.
Cutting depth, inclination angle and cutting speed
Another example is the processing of thermoplastics. Thermoplastics generally have low thermal conductivity and a low modulus of elasticity. This means that they are strongly affected by heat fluctuations at the tool tip during machining. The cutting depth, rake angle and cutting speed need to be adjusted to each other to prevent temperature rise and the formation of sticky, rubbery chips at the tool tip.
It is also worth knowing that cutting depth is one of the three most important parameters that affect tool life, along with cutting speed and feed.
How do you calculate depth of cut?
The importance of quantitative relationships between different variables becomes clear when you need a depth of cut calculation, want to know why the tool temperature gets so high, why the surface finish is poor, why the cutting tool becomes wears out quickly and much more.
To calculate the cutting depth, you must specify the following parameters:
- What is the machining process (milling, turning, etc.)
- part material
- Tooltip properties
- Machine functions
- Required surface quality and tolerance
Cutting depth when turning
In CNC turning, the part rotates as the tool removes a layer of material as it moves along the length of the part. Depth of cut can be equal to feed or feed rate, which is simply the distance the tool travels along the part with each revolution over time, and the unit is mm/min.
Therefore, the depth of cut can simply be defined by the thickness of the material removed and calculated as follows:
Cutting depth when milling
In CNC milling, the tool rotates while the part remains stationary. Depth of cut is simply the depth that the tool cuts into the workpiece in one revolution. Typically, the cutting depth is four times the diameter of the cutting tool for large diameters above 20 mm and ten times the diameter for tools with smaller diameters.
Compare the chip thickness value with the cutting depth value
It is important to distinguish between chip thickness and depth of cut, as they are NOT the same thing and do NOT have the same value.
To explain this, we need to take a closer look at Figure 1 of the ideal cutting process. The value of cutting depth (denoted by to) is different from the chip thickness (tc).
Figure 1: Optimal cutting process
Chip removal is carried out by shearing in a precisely defined shear plane and with a defined shear angle ϕ, as shown in Figure 2 below. As a result, the chip thickness value is always greater than the cutting depth value.
Figure 2: Basic chip formation mechanism
Cut Rate vs. chip compression ratio
The relationship between cutting depth and chip thickness to/tc is called cutting ratio or chip thickness ratio, denoted by (r) and can be calculated as follows:
It can also be calculated from the shear angle ϕ and the tilt angle α as shown in Figure 1 as follows:
Where:
ϕ: shear angle
α: inclination angle
The reciprocal of this value is called the chip compression ratio or chip compression factor and indicates how great the chip thickness is in relation to the depth of cut.
Bonus: cutting depth versus cutting forces and performance
Knowing the cutting force and power is essential to calculate the DOC. They can provide important parameters such as:
- Tools with the necessary resistance to avoid rapid wear and guarantee excellent efficiency and surface quality.
- Supports and accessory parts that can withstand these forces with minimal deformation.
The required power is simply the product of the cutting force multiplied by the speed and can be calculated as follows:
Where Fc is the “cutting force” and is defined as the force exerted by the tool to cut the part and which acts in the same direction as the tool speed V.
Total specific energy is the total energy required to apply the shear force required to cut the surface (us), in addition to frictional specific energy, which is the energy required to overcome the friction between the tool and the surface (uf).
Specific shear energy and specific friction energy depend on the depth of cut and can be calculated as follows:
Chip speed is related to cutting speed as follows:
Therefore, it is important to point out that these formulas can be used in reverse to calculate the cutting depth if you have certain machine parameters.
WayKen is a trusted partner for your editing projects
Machining is a complex operation and it is not an easy process to define quantitative values for all parameters and determine the machinability of a given material.
Concluding
Cutting depth is a very important parameter that must be taken into consideration before starting the machining process. As already explained, the value of the cutting depth directly affects dependent machining parameters, such as machining forces and specific energies. The calculation of these values affects not only the resistance and surface quality of the part, but also the tool material, the type of fixing and the possibility of using coolant.