Carbide saw blades are the most frequently used tools for woodworking. The quality of carbide saw blades is closely related to the quality of processed products.
The correct and rational selection of carbide saw blades is of great importance for improving product quality, shortening processing cycles and reducing processing costs.
The parameters of carbide saw blades include the type of alloy cutting head, the substrate material, diameter, number of teeth, thickness, tooth shape, angle and opening; These parameters determine the processing capacity and cutting performance of the saw blade.
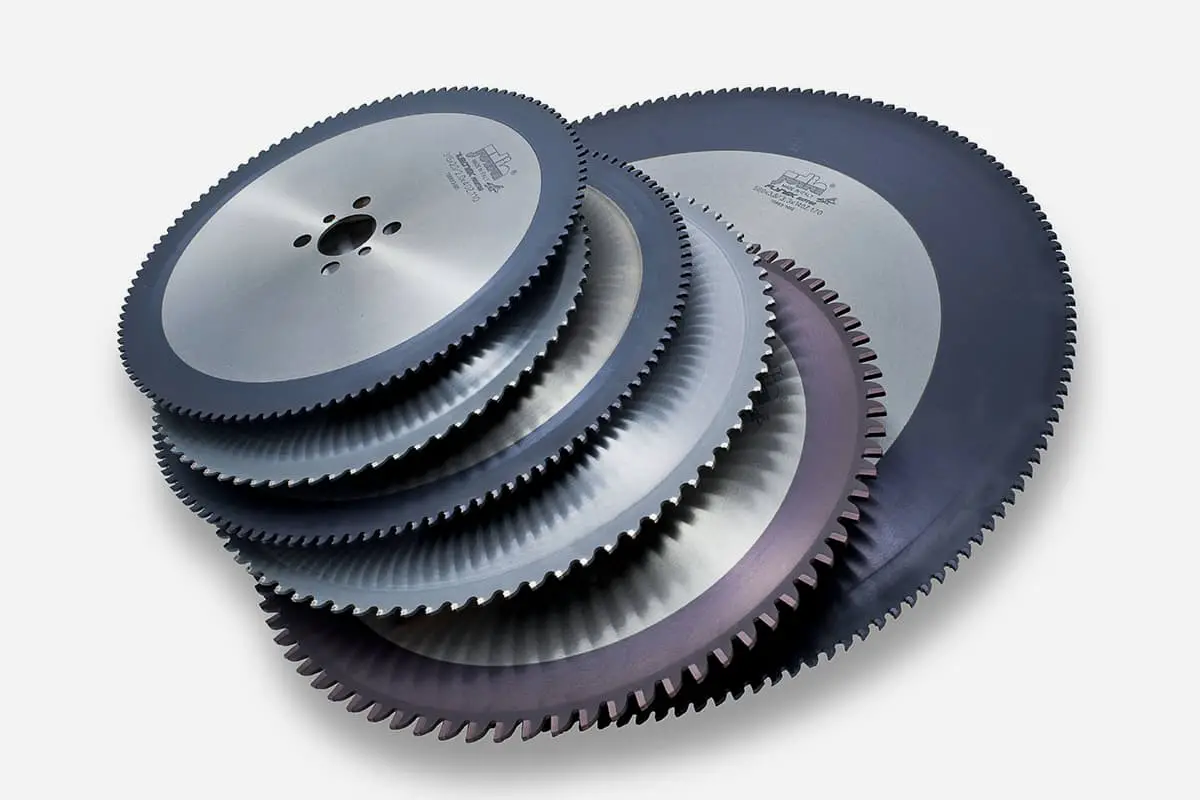
VIII. Correct use of alloy saw blades
A. Basic Requirements:
1. Choose the appropriate saw blade according to the equipment design requirements.
2. The corresponding equipment must have safety protection devices such as protective cover, shutdown brakes and overload protection.
3. Professional operators must install and use the equipment, wearing work clothes, safety glasses and ear protectors.
4. Operators must not wear gloves, long hair must be placed in a work hat, and ties and cuffs must also be monitored to avoid danger.
5. Keep away from sources of fire and humid environments.
B. Installation Requirements:
1. Make sure the equipment is in good condition, with no deformation on the main axis, no radial deviation, firm installation and no vibration.
2. Check the saw blade for any damage, make sure the tooth shape is complete, the saw plate is flat and smooth, and there are no other abnormalities to ensure safe use.
3. During assembly, make sure that the direction of the arrow on the saw blade corresponds to the direction of rotation of the equipment's main axis.
4. When installing the saw blade, keep the shaft, chuck and flange clean. The inner diameter of the flange must match the inner diameter of the saw blade to ensure a tight connection between the flange and the saw blade.
Install the positioning pin and tighten the nut. The size of the flange must be suitable, its outer diameter must not be less than 1/3 of the diameter of the saw blade.
5. Before starting the equipment, ensure safety, have a single operator operate the idle equipment to check whether the equipment rotation is correct and there is no vibration.
After installing the saw blade, let it run idle for a few minutes. If there is no sliding, rocking or jumping, it can start normal work.
C. Usage Requirements:
1. During work, make sure that the part is fixed and that the positioning of the profile is in accordance with the cutting direction to avoid abnormal cuts.
Do not apply side pressure or curved cuts. Advancement must be constant to avoid impact contact between the blade and the part, which could cause damage to the blade or ejection of the part, causing accidents.
2. If abnormal sounds, vibrations, rough cutting surfaces or unusual odors are detected during work, stop work immediately, check in time and eliminate the fault to avoid accidents.
3. Do not feed too quickly when starting and stopping cutting to avoid broken teeth and damage.
4. When cutting aluminum alloy or other metals, use a specific cooling lubricant to prevent the saw blade from overheating, causing teeth burns and other damage, affecting the cutting quality.
5. Make sure the chip removal groove and suction device are unobstructed to prevent accumulated slag from forming blocks, impacting production and safety.
6. When dry cutting, do not cut continuously for long periods to avoid affecting the service life of the saw blade and cutting effect. When cutting wet, add water to prevent electrical leakage.
D. Saw Blade Maintenance:
1. If the saw blade is not in immediate use, it should be stored flat or hung by the center hole. No objects should be placed or stepped on a flat blade, with attention to preventing moisture and rust.
2. When the saw blade becomes dull or the cutting surface becomes rough, it should be resharpened immediately. The regrinding process must not change the original angle or disturb the dynamic balance.
3. The factory must take care of any changes to the inner diameter of the saw blade and the machining of the positioning holes.
Poor workmanship can affect product performance and can be potentially dangerous. The hole enlargement should not exceed the original hole diameter by 20mm to avoid affecting the stress balance.
4. Choosing a light alloy grinding wheel.
1) Resin diamond grinding wheels have poor bonding strength, providing excellent self-sharpening during grinding.
They are less likely to clog, with high grinding efficiency, lower grinding force and reduced grinding temperature.
The disadvantage is their low abrasion resistance and high tool wear, making them unsuitable for grinding with heavy loads.
2) Ceramic bonded diamond grinding wheels have better abrasion resistance and bonding ability than resin bonded grinding wheels.
They provide accurate cutting, high grinding efficiency, are less likely to overheat and clog, have low thermal expansion and are easy to control precisely. However, they leave a rougher grinding surface and are more expensive.
3) Metal bonded diamond grinding wheels have high bonding strength, good abrasion resistance, low wear, long service life, lower grinding cost, and can withstand high loads, but they have poor sharpness and are prone to clogging.
4) The size of the abrasive grain has a significant impact on the clogging of the grinding wheel and the amount of cutting.
Compared to fine grains, coarse grains allow for greater depth of cut and greater abrasive edge wear, while fine grains are more likely to clog the grinding wheel.
5) The hardness of the grinding wheel significantly affects clogging. A high-hardness grinding wheel has a high heat conduction coefficient, which is unfavorable for surface cooling but beneficial for improving machining accuracy and durability.
6) The choice of grinding wheel concentration is an important feature, greatly affecting the grinding efficiency and processing cost.
Too low a concentration affects efficiency, while too high a concentration leads to easier grain precipitation. However, there is an ideal range for ligand concentration.