Argon arc welding is a method of electric arc welding with the inert gas “argon” as the shielding gas.
Argon is sprayed from the nozzle to form a protective layer of inert gas in the welding area to isolate air invasion, so as to protect the arc and weld pool.
This welding method has many advantages:
- Good protection effect, high welding quality, no spatter and beautiful weld formation;
- Small welding deformation, can perform one-sided welding and double-sided forming, ensure root penetration, and can weld in multiple positions;
- Can weld various metals and alloys;
- Stable arc combustion, open arc operation, no slag, automation easy to realize.
Therefore, it has been widely used in practical production.
However, due to the poor wind resistance of argon arc welding, it is particularly sensitive to rust, water and oil, and has strict requirements on gas purity, groove cleaning and welding process, which is easy to produce pores .
Combined with production practice, this post analyzes the problem of porosity in argon arc welding and introduces some treatment and care methods.
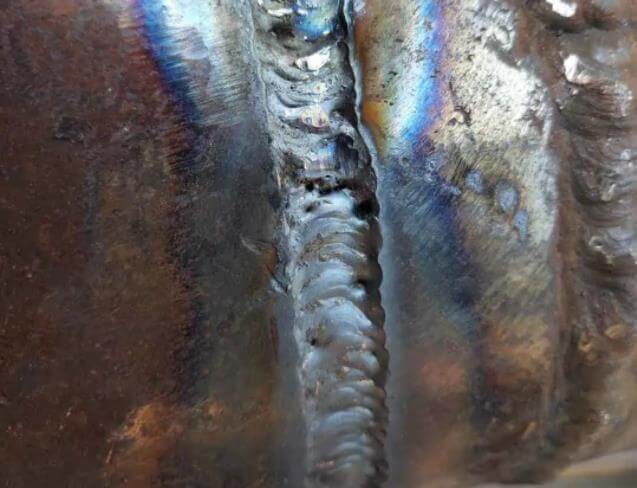
I. Characteristics and dangers of gas pores
1.1 Characteristics of Gas Pores
Gas pores are cavities formed in welding seams when gas bubbles in the molten pool are unable to escape during solidification, a common and important welding defect in TIG argon arc welding. Their shapes can be spherical, oval, spiral or worm-like.
Those within the welding seam are called internal gas pores, while those exposed on the surface of the seam are external gas pores. The size of the gas pores varies; they can exist individually, group together or be distributed continuously along the seam.
1.2 Gas Pore Hazards
Gas pores, being volumetric defects, significantly impact the performance of the welding seam. They mainly reduce the load-bearing capacity of the seam. This occurs because the gas pores occupy a certain volume of the welding seam, reducing the effective working cross-sectional area and, consequently, the mechanical performance of the seam.
This particularly reduces the plasticity of the seam, as well as its resistance to bending and impact. If gas pores penetrate the surface of the welding seam, especially if they penetrate the surface in contact with the medium, the medium will exist within the cavities.
When the medium is corrosive, concentrated corrosion occurs, causing cavities to become deeper and larger until corrosion penetration and leakage occur. This compromises the integrity of the welding seam and, in serious cases, can lead to the destruction of the entire metal structure.
Therefore, preventing gas pores in the welding seam and ensuring welding quality should be paid close attention.
II. Gas Pore Formation
2.1 Gas Pore Formation
Throughout the welding process, the surroundings of the weld pool are filled with complex gases, mainly from the surrounding air and impurities in the workpiece such as rust, paint and grease, which produce gas when heated.
All of these continuously interact with the pool of molten metal. Some gases enter the molten pool through chemical reactions or dissolution, causing the liquid metal in the molten pool to absorb significant amounts of gas. If these gases are expelled quickly, even if the weld pool crystallizes quickly, gas pores will not form.
However, if gases form during the molten pool crystallization process and the crystallization process is too fast for the gases to escape, they will remain in the weld seam and form gas pores.
2.2 Factors Influencing the Formation of Gas Pores
The formation of gas pores in TIG welding beads is often the result of the combined action of several gases, with H 2 and 2 playing the main roles. A detailed analysis is as follows:
Effects of H 2 :
H 2 in the welding zone comes from several sources. Some compositions, crystalline water and impurities on the surface of the part contain hydrogen components. Furthermore, the steel smelting process also contains hydrogen.
Under the high temperatures of the electric arc, these components form bubbles that quickly dissipate outward. If the H 2 cannot fluctuate during the cooling process of the welding seam, it will form gas pores.
Effects of N 2 :
N 2 comes mainly from the air. The weight percentage of N 2 in base metals and welding wires is not very high and exists in steel and other iron alloys as solid oxide solutions and other forms.
The solubility of N2 in steel varies drastically with temperature, and the precipitated N2 forms bubbles that are expelled from the weld pool. Bubbles that cannot be expelled in time remain in the welding seam and form gas pores. Gas pore formation occurs when the arc and metal in the welding weld pool are exposed to air without sufficient protection.
III. Factors influencing stomata
1. Argon is impure
When welding carbon steel, the purity of argon should not be less than 99.7%, when welding aluminum, it should not be less than 99.9%, and the purity of argon used for welding titanium and titanium alloy is up to 99 .99%.
Method for detecting argon purity:
(l) Weld the polished steel plate or tube without welding wire, and then re-melt it into the welding bead several times. If there are pores, it indicates that the argon is impure.
(2) During welding, there is a very small spark around the arc, which also indicates that the argon is impure.
(3) Sometimes, when the purity of argon is close to the purity requirements of welding requirements, it cannot be detected by the above two detection methods, but when welding gap welded joints, intermittent pores will be generated at the root of the weld , or surface pores will be generated during overlay welding, or there is an oxide layer on the surface of the weld bead.
(4) Solder some spots on the nickel plate. If the stain is silvery white and the surface is like a mirror, it indicates that the purity of argon is qualified.
2. Argon flow
The argon flow is very small and the anti-wind interference ability is weak;
Too large, the gas flow rate is too large, and the near-wall laminar flow formed when passing through the nozzle is too thin.
After the gas is ejected, it will quickly become disordered and it will be easy to envelop the air, which will deteriorate the shielding effect of the weld pool.
Therefore, the argon flow must be appropriate to stabilize the gas flow.
3. Air leak in the air belt
Air leakage at the pneumatic belt interface or pneumatic belt will cause very small gas flow during welding, and the air will be sucked into the pneumatic belt, resulting in poor protection effect.
4. Influence of the wind
If the wind is slightly strong, the argon protective layer will form turbulence, resulting in poor shielding effect.
Therefore, wind protection measures must be taken when the wind speed is > 2m/S;
When welding pipes, the pipe hole must be blocked to prevent ventilation into the pipe.
5. Influence of welding gun nozzle
The nozzle diameter is too small. When the effective protection range of argon around the arc is smaller than the weld pool area, it will cause insufficient protection and produce pores.
Especially for field operation and large pipe welding, larger diameter nozzles should be used to effectively protect the arc and weld pool.
6. Distance between welding gun nozzle and workpiece
The distance is small and the crosswind sensitivity is small;
The distance is far and the ability to resist wind interference is poor.
7. The pressure in the cylinder is too low
When the pressure in the gas cylinder is less than 1MPa, it should be stopped.
8. The angle of the welding gun is too large
If the angle of the welding gun is too large, on the one hand, air will be brought into the weld pool, on the other hand, the argon flow on the long arc side will deteriorate the shielding effect of the arc and weld pool .
9. Influence of hydrogen flow meter
Unstable gas output from the flow meter, whether large or small, will affect the protection effect.
10. Impact of the operation
When using the argon arc welding gun with control button, vent the gas before welding to avoid excessive pressure in the gas zone, resulting in instantaneous excessive gas flow and air holes during arc lighting.
11. Inappropriate welding gun accessories
The tungsten electrode clamp is not compatible, the blocked gas path is not smooth, and the shielding gas flows from one side of the nozzle, which cannot form a complete shielding ring.
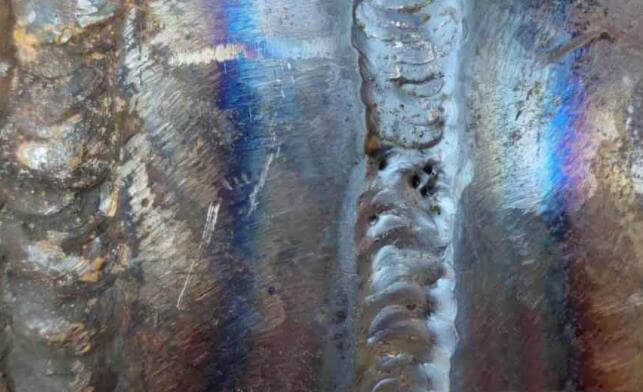
4. Influence of welding materials
1. Influence of welding wire type
Submerged arc welding wire should not be used to replace manual TIG welding wire, otherwise intermittent or continuous pores will be generated.
2. The welding wire is not clean
Rust, oil stains and water on the surface of the welding wire will directly promote a large number of pores in the weld.
V. Influence of basic metallic material
1. Influence of plate or tube quality
If there is an intermediate layer in the plate or tube, the impurities in the intermediate layer will promote the generation of pore defects.
2. Influence of steel type
Boiling steel (with a high oxygen content and many impurities) cannot be welded by argon arc welding.
SAW. Influence of tungsten electrode
1. Influence of the extreme part of tungsten
The extreme part of the tungsten is not sharp, the arc drift is unstable, the argon protective area is destroyed, and the metal in the molten pool is oxidized to produce pores.
2. Poor protection due to arc rising during arc firing
When high-frequency arc striking equipment is used, the temperature of the extreme part of the tungsten is low at the beginning of the arc striking, therefore it does not have sufficient electronic thermal emission capacity.
Electrons are easily emitted from the oxide film site and rise along the electrode to meet the oxide site.
At this time, the arc is lengthened and the shielding effect of argon on the weld pool worsens.
When the temperature of the tungsten electrode increases, electrons are emitted from the front end of the tungsten electrode.
The arc length and phase deformation are short.
At this time, the oxide on the surface of the tungsten electrode can be eliminated as long as it is polished and cleaned.
VII. Influence of the Welding Process
1. Groove cleaning
The surface of the groove and the 10mm strip on both sides of the groove must be polished to prevent the magnetic generated by the arc during welding from sucking the rust near the molten pool into the molten pool.
2. Influence of welding speed
The welding speed is very fast.
Due to the influence of air resistance on the shielding gas flow, the argon gas flow will bend and deviate from the center of the electrode and the weld pool, which is not good for the weld pool and arc shielding.
3. Influence of arc extinguishing method
During arc extinction, the arc extinction method of current attenuation or adding welding wire should be adopted, bringing the arc to the groove side and reducing the arc.
Do not stop the arc suddenly, resulting in the separation of the high-temperature molten pool from the effective protection of the argon gas flow, so as to avoid pores or shrinkage in the arc well.
4. Influence of welding current
The welding current is too small, the arc is unstable, and the arc deflects irregularly at the end of the tungsten electrode, damaging the protective zone.
If the welding current is too large, the arc will disturb the air flow and the shielding effect will worsen.
5. Influence of tungsten electrode extension length
If the tungsten electrode extends for a long time, the shielding effect of argon on the arc and weld pool will worsen.
VIII. Measures to prevent the formation of porosity
Although there are several causes of porosity, choosing the right welding process and improving the welder's operational skills are key ways to avoid it.
1. Pre-welding treatment of the workpiece and welding wire
TIG welding is particularly sensitive to oil, rust and water, which can easily lead to porosity, therefore a high surface quality of the base material is required. It is crucial to carry out rigorous cleaning before welding, polishing the area between 10-15mm inside and outside the bevel of the workpiece to remove surface oxide films, impurities such as oil and moisture, and expose the metallic luster.
Likewise, the oil and rust on the surface of the welding wire need to be sanded off until the metal shines.
2. Purity of Argon
Argon is an inert gas that does not decompose at high temperatures or react with the weld metal to cause oxidation. During argon arc welding, the purity of argon must be greater than 99.95%. Furthermore, when the pressure inside the argon cylinder drops below 2.0 MPa and the moisture content increases, its use should be stopped.
The argon flow rate must be adequate, determined by the following empirical formula: Q=K·D, where Q represents the argon flow rate, D is the nozzle diameter and K is a coefficient (0.8-1.2). Thus, the argon flow rate is generally 6-9L/min. The gas path must also be kept unobstructed, with no blockage or leaks occurring.
3. Nozzle diameter
The nozzle diameter can be determined by the following empirical formula: D=(2.5-3.2)d, where D represents the nozzle diameter and the tungsten electrode diameter. Based on this formula, the appropriate nozzle diameter is generally 6 to 12 mm.
4. Extension length of tungsten electrode
If the extension length of the tungsten electrode is too large, the distance between the nozzle and the workpiece increases, reducing the protective effect. On the other hand, if the extension length is too short, although the protection effect may be good, it may obstruct the welder's line of sight and cause the tungsten electrode and welding wire to collide, causing short circuit and preventing welding.
5. Welding speed
Welding speed is one of the main welding parameters. If the speed is too fast, the shielding gas will bypass the tungsten electrode and the pool, leading to reduced shielding effect and porosity. It can also impact the formation of the weld seam, therefore, an appropriate welding speed must be selected during welding.
6. Pre-gas flow and post-gas flow
Sending argon 3-4 seconds before arc initiation can expel air from the tube, ensuring the arc is started in a gas-shielded environment and preventing the tungsten electrode and puddle from oxidizing and creating pores. Delaying gas shutoff can provide a cooled and protected pool, as well as prevent defects such as arc pits, cracks and porosity at the arc termination point. Therefore, mastering the correct arc extinguishing method is essential.
7. Operational Skills
Proficiency in operational skills is a vital step in preventing porosity, and every welder needs to possess a solid foundation of these essential skills. The welding torch, wire and workpiece must maintain a correct position and relative angle, with coordinated movements.
During welding, the arc needs to be stable, with a consistent height, and abrupt fluctuations are strictly prohibited to prevent gas from instantly entering the weld pool and causing porosity. At the same time, it is important to observe changes in the molten pool to increase the ability to expel porosity.
When welding in all positions, the welding torch, wire and workpiece must maintain a certain distance from each other. The direction is generally from bottom to top, that is, in the order of top – vertical – plane. When extinguishing the arc, it is essential to avoid the appearance of grooves and shrinkage holes, ensuring that the weld seam is not inferior to the base material.
This can be achieved by increasing the weld seam, i.e., decreasing the welding speed when extinguishing the arc, increasing the backward tilt of the torch, and increasing the wire feed when the weld pool temperature is too high. If necessary, the arc can be extinguished and reignited until the arc pit is filled.
In conclusion, TIG argon arc welding has excellent welding characteristics. Long-term production practice has proven that adopting the above-mentioned process measures can effectively control the generation of porosity, significantly improving the first-time flaw detection rate and the quality of the welded joint.
IX. Conclusion
Although there are many factors that cause pores in manual TIG welding, as long as we understand the characteristics of argon arc welding, we will investigate the influencing factors one by one according to the actual situation, and eliminate all the factors that cause pores in the weld during argon arc welding, we can improve the welding quality in actual production.