This article explains the causes of arc magnetic blow and the factors that affect the size of magnetic blow, and presents the impact of magnetic blow on welding quality.
From design and technology aspects, measures are proposed to control the influence of magnetic blowing on welding quality.
Introduction
Arc straightness refers to the property of the arc as a flexible conductor to resist external interference and strive to keep the welding current flowing along the electrode axis.
When the electrode is tilted, the direction of the arc also tilts, and the center line of the arc extends in the direction of the electrode tilt, which is called magnetic strike.
1. Magnetic Strike Production
1.1 The reasons for the magnetic strike are:
(1) Improper connection position causes magnetic impact.
The welding current generates a magnetic field in space. When the electrode is perpendicular to the workpiece, the magnetic field density on the left side of the arc is greater than that on the right side.
The uneven distribution of the magnetic field causes the denser side to exert momentum on the arc, causing it to deviate from the axis.
(2) Asymmetric ferromagnetic materials cause magnetic impact.
When welding, placing a steel plate (magnetic conductor) on one side of the arc, due to the much higher magnetic conductivity of ferromagnetic materials than air, most of the magnetic field lines on the side of the ferromagnetic material form sharp curves, reducing the density of magnetic field lines between the arc and the ferromagnetic material, therefore, under the action of electromagnetic force, the arc tends to blow to the side of the ferromagnetic material.
(3) The movement of the arc at the end of the steel plate causes magnetic strike, as shown in the figure below.
This is because when the arc reaches the end of the steel plate, the area of magnetic flux changes, causing an increase in the density of magnetic field spatial lines near the edge of the part.
Therefore, under the action of electromagnetic force, a magnetic blow is produced pointing towards the inside of the part.
As shown in the following image:
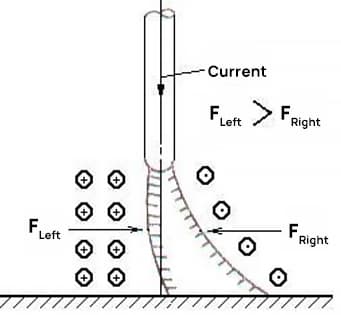
(1) Magnetic deflection caused by the position of the wire connection
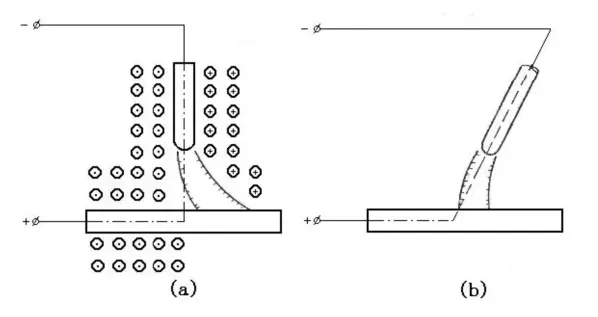
(2) Magnetic deflection caused by ferromagnetic material near the arc

(3) Magnetic deflection blow generated when the arc is at the end of the workpiece
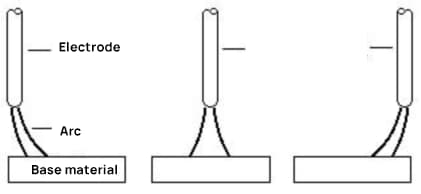
1.2 Risks of Blowing due to Magnetic Deflection:
During the welding process, due to the interference of the gas flow, the eccentricity of the electrode coating and the magnetic force of the magnetic field, the phenomenon of deviation of the arc center from the electrode axis occurs.
That is, if some reason destroys the uniformity of the magnetic field distribution and the load on the arc is tensioned unevenly, this will cause the arc to deviate to one side.
In other words, the welding arc magnetic deflection blow caused by the electromagnetic force generated by the welding circuit during DC arc welding is called welding arc magnetic deflection blow.
Magnetic deflection blowing not only makes arc burning unstable, increases spatter, and loses protection when molten droplets fall, but also seriously affects weld formation.
2. Solutions
According to the causes of magnetic deflection blowing, the following methods can be used in production and installation to overcome and eliminate the influence of magnetic deflection blowing on the welding arc:
(1) Appropriately change the position of the ground wire when welding to make the magnetic field lines around the arc distributed as evenly as possible;
(2) Adjust the electrode tilt angle appropriately during operation and tilt the electrode in the direction of the deflection blow;
(3) The use of segmented back welding and short arc welding can also effectively overcome magnetic deflection blowing;
(4) Use AC welding instead of DC welding. When using AC welding, the change of magnetic field produces induced current in the conductor, and the magnetic field produced by the induced current weakens the magnetic field caused by the welding current, thereby controlling the magnetic deflection blow;
(5) Place ferromagnetic materials that generate symmetrical magnetic fields, and try to distribute the ferromagnetic materials evenly around the arc;
(6) Reduce residual magnetism in welding.
Residual magnetism in welding is mainly caused by the ordered arrangement of atomic magnetic domains.
In order to disturb the arrangement of magnetic domains in welding and reduce or avoid magnetic deflection blowing, local heating should be applied to parts with residual magnetism in welding at a temperature of 250-300°C.
This method has a good demagnetization effect in production and use.
Additionally, a magnet can be added to balance the magnetic field in the residual magnetism part of the welding.
(7) Use the demagnetization method. That is, let the welding produce a magnetic field opposite to the residual magnetism in the welding to overcome and eliminate the influence of magnetic deflection blown into the welding arc.
Taking pipeline welding as an example, the application of magnetic deflection blow prevention is introduced.
When welding pressure pipes, magnetic deflection blow is prone to occur in the butt welding process of thick-walled pipes, making it impossible to carry out manual tungsten and argon arc welding in the root pass.
According to the occurrence of magnetic deflection blowing, magnetic deflection blowing mainly occurs in the joint of thick-walled pipeline and occurs in various welds when the pipeline is about to be closed.
Thick-walled pipelines with ferromagnetic materials exhibit residual magnetism during manufacturing and processing.
The longer the pipeline, the more residual magnetism accumulates, which manifests itself at the final closing joint, causing magnetic deflection blowing.
Specific measures: Use the welding cable to wrap both sides of the joint.
When the arc is started, the welding current generates an induced magnetic field through the cable winding to neutralize residual magnetism and overcome magnetic deflection blow.
The welding effect can be adjusted by the following two methods:
1) When the welding current is constant, the intensity of the induced magnetic field generated in welding can be adjusted by adjusting the number of cable windings to be equal in magnitude and opposite in direction to the intensity of the residual magnetic field;
2) When the number of cable windings is constant, the welding current can be changed within the allowable range to adjust the intensity of the induced magnetic field generated in welding to be equal in magnitude and opposite in direction to the intensity of the residual magnetic field, thus eliminating residual magnetism in the joint and overcoming the influence of magnetic deflection blowing into the welding arc.
3. Conclusion
In real welding environments, the causes of magnetic deflection blow are not the same due to different welding environments.
Therefore, it is necessary to combine with the actual situation on site to find out the causes of magnetic deflection blowing and deal with them based on the experience summarized above to ensure the welding quality in field welding.