In every electroplating solution, there is the presence of hydrogen ions as a result of the dissociation of water molecules.
As a result, during the galvanizing process, metal is deposited from the cathode (main reaction) and hydrogen is also deposited (secondary reaction).
Hydrogen evolution has multiple impacts, with hydrogen embrittlement being the most significant.
Hydrogen embrittlement is a major risk to quality in surface treatment and can lead to parts breaking during use, causing serious accidents.
It is crucial that surface treatment technicians have an in-depth understanding of techniques to prevent and eliminate hydrogen embrittlement in order to minimize its effects.
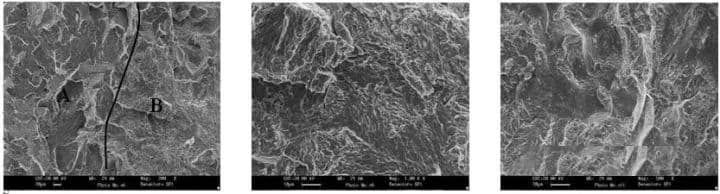
1. Hydrogen embrittlement
(1) Hydrogen embrittlement
Hydrogen embrittlement typically manifests as delayed fracture under stress.
Galvanized parts such as automobile springs, washers, screws and leaf springs are known to break just a few hours after assembly, with a fracture rate of 40% to 50%.
In the case of a special product with cadmium-plated parts, one batch showed cracks and fractures.
A national investigation was conducted and a rigorous dehydrogenation process was established.
Furthermore, some cases of hydrogen embrittlement do not result in delayed fracture.
For example, the electroplating bracket, made of steel wire and copper wire, may become permeated with hydrogen due to repeated electroplating, pickling and deplating, leading to brittle fracture after just one use.
Similarly, the center rod used for precision forging of hunting weapons may break after multiple chrome plating processes.
In some cases, parts tempered with high internal stress may crack during pickling due to severe hydrogen permeation. These cracks can occur without external stress and the original toughness cannot be restored by removing hydrogen.
(2) Hydrogen embrittlement mechanism
The occurrence of delayed fracture is caused by the diffusion and accumulation of hydrogen in the parts, specifically in areas of stress concentration that present metallic defects, such as dislocations or holes in the atomic network.
As hydrogen diffuses into these defects, hydrogen atoms combine to form hydrogen molecules, which generate high pressure.
This pressure creates a force in combination with the residual stress within the material and the external stress on the material.
If the resulting force exceeds the yield strength of the material, it will fracture.
The rate of hydrogen diffusion, and therefore the occurrence of hydrogen embrittlement, depends on the concentration gradient, temperature and type of material.
Materials with small atomic radii, such as steel and copper, are more susceptible to hydrogen diffusion, while it is more difficult for hydrogen to diffuse into cadmium, tin, zinc and their alloys.
The cadmium plating layer is particularly resistant to hydrogen diffusion, as the hydrogen generated during cadmium plating remains in the plating layer and the surface layer of the metal underneath, making it difficult to diffuse outward and remove.
Over time, hydrogen diffuses into the metal and can enter defects in the metal, making it difficult to remove.
Hydrogen diffusion is slow at normal temperatures and must be heated to remove it.
As the temperature increases, the solubility of hydrogen in steel also increases.
However, too high a temperature can reduce the hardness of the material.
It is important to consider the temperature for stress removal before galvanizing and hydrogen removal after galvanizing, so as not to reduce the hardness of the material, avoid the brittle tempering temperature of some steels and maintain coating performance.
2. Measures to avoid and eliminate
(1) Reduce the amount of hydrogen permeation in the metal
In the process of removing rust and scale, sandblasting should be used as much as possible.
If acid washing is necessary, a corrosion inhibitor such as rutin should be added to the solution.
For oil removal, chemical oil removal, cleaning agents or solvents with low hydrogen permeation should be used.
If electrochemical oil removal is chosen, the cathode must be followed by the anode.
In electroplating, the amount of hydrogen permeation is low in alkaline electroplating solutions or solutions with high current efficiency.
(2) Coated coating with low hydrogen diffusivity and low hydrogen solubility should be adopted
It is widely accepted that when electroplating with Cr, Zn, Cd, Ni, Sn and Pb, hydrogen can easily penetrate steel parts, while coatings made of metals such as Cu, Mo, Al, Ag, Au and W have low diffusivity of hydrogen and low hydrogen solubility, leading to less hydrogen permeation.
When the technical requirements of the product are met, coatings that do not cause hydrogen permeation can be used.
For example, Dacromet coating can be used as an alternative to zinc plating, without causing hydrogen embrittlement.
This coating offers 7 to 10 times improved corrosion resistance and has good adhesion.
The film thickness of 6-8um is similar to a thin zinc coating and will not affect the assembly.
(3) Remove tension before coating and remove hydrogen after coating to eliminate potential hydrogen embrittlement
If parts have high internal residual stress after quenching, welding or other processes, tempering treatment should be carried out before coating to reduce the risk of hydrogen permeation.
In general, parts with high hydrogen permeation during coating should be dehydrogenated as quickly as possible, as hydrogen in the coating layer and surface base metal will continue to diffuse into the steel matrix over time.
Draft international standards stipulate that dehydrogenation treatment should ideally be carried out within 1 hour after plating, but no later than 3 hours.
There are also similar patterns in China regarding dehydrogenation before and after galvanizing.
Post-coating dehydrogenation is commonly achieved through heating and cooking, with a temperature range of 150-300°C and isolation for 2-24 hours.
The exact treatment temperature and time must be determined based on the size, strength, coating properties and coating time of the parts.
Dehydrogenation is typically carried out in an oven, with temperatures for galvanized parts ranging from 110-220°C, and the temperature must be controlled based on the base material.
For elastic materials, thin-walled parts less than 0.5 mm and steel parts with high mechanical strength requirements, hydrogen removal treatment must be carried out after galvanizing.
To avoid “cadmium embrittlement”, the dehydrogenation temperature of cadmium-coated parts should not be too high, normally between 180-200°C.
3. Problems needing attention
Sensitivity to hydrogen embrittlement increases with material strength, which is a fundamental concept that surface treatment technicians must understand when preparing electroplating process specifications.
International standards require that steel with a tensile strength of σb > 105kg/mm2 undergo pre-coating stress removal and post-coating hydrogen removal treatment.
The French aviation industry requires a corresponding dehydrogenation treatment for steel parts with a yield strength of σs > 90kg/mm2.
As there is a strong correlation between the strength and hardness of steel, it is easier to assess the sensitivity of materials to hydrogen embrittlement by their hardness than by their strength.
Product designs and machining processes often include steel hardness, making it more convenient to evaluate.
In electroplating, it was observed that steel with a hardness of approximately HRC38 begins to present a risk of fracture due to hydrogen embrittlement.
For parts with hardness greater than HRC43, dehydrogenation must be considered after galvanizing.
If the hardness is around HRC60, dehydrogenation treatment must be carried out immediately after surface treatment, otherwise the steel parts will crack within a few hours.
In addition to the hardness of the steel, the following factors must also be taken into account:
- Part safety: Parts with high safety significance must undergo enhanced hydrogen removal.
- Geometry of parts: Parts with notches prone to stress concentration, small R, etc. must have enhanced hydrogen removal.
- Cross-sectional area of parts: Small spring steel wires and thin leaf springs are easily saturated with hydrogen, so hydrogen removal must be strengthened.
- Degree of hydrogen permeation in parts: Parts with a greater amount of hydrogen produced during surface treatment and longer treatment times should have enhanced hydrogen removal.
- Coating type: For example, the cadmium coating layer seriously blocks the diffusion of hydrogen, so the removal of hydrogen must be strengthened.
- Tensile properties of parts in use: Parts under high tensile stress must have greater hydrogen removal. Hydrogen embrittlement will not occur under compressive stress.
- Surface processing status of parts: Parts with high internal residual stress from processes such as cold bending, stretching, quenching and welding should have enhanced hydrogen removal after galvanizing and stress removal before galvanizing.
- Part history: Special attention should be given to parts with a history of hydrogen embrittlement, and relevant records should be kept.
Hydrogen embrittlement removal
The main issue is the “hydrogenation” phenomenon that occurs in the electroplating process. The unqualified products you are using are not necessarily a result of the electroplating process itself, as most electroplating methods (except vacuum galvanizing) will cause hydrogenation in the metal.
However, many metal surface treatment facilities omit the final step, specifically the “dehydrogenation” process, to save production costs. This process, which is essential for metal parts with strength requirements, involves heating the parts to a high temperature of 120-220°C for 1-2 hours after electroplating.
If the user is not aware of or has not requested or accepted this process, they can save 5 to 15% of the cost. This can cause coated screws, spring pads, and other parts to become “brittle.”
The specific conditions for dehydrogenation treatment must be controlled according to the requirements of the parts.