CNC press brake
The CNC press brake is capable of meeting the requirements of various small batch products, including thin sheets such as car front walls, door lintels, car tops, bottoms and frames, as well as thick sheet products.
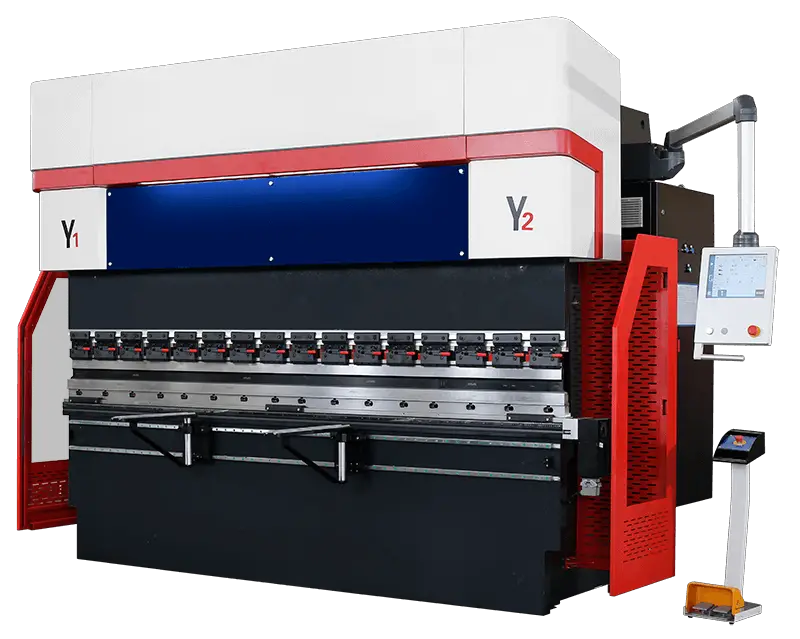
CNC folder
The CNC bending machine is equipped to meet the demands of a variety of small batch products, including thin sheet metal that requires lifting, such as walls, tops, bottoms and car frames, as well as medium thickness sheet metal products.
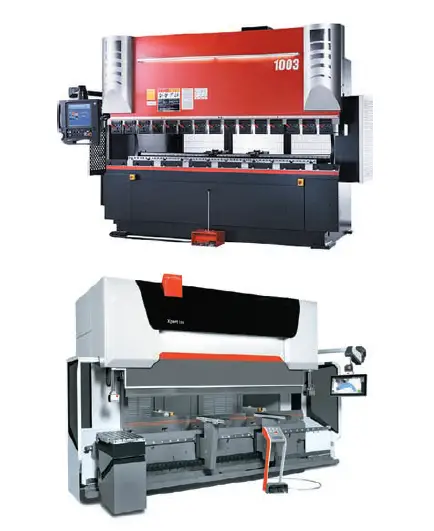
Fig.1 CNC press brake
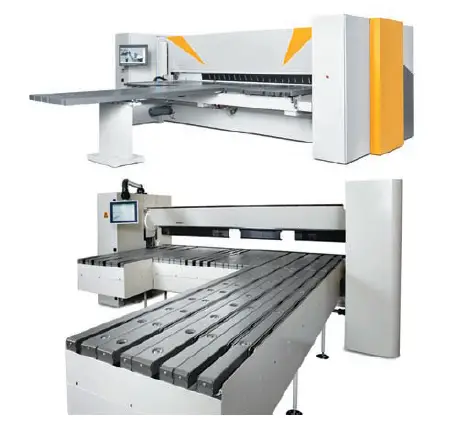
Fig.2 CNC folder
Working principle of CNC press brake and press brake
Working principle of press brake

The press brake has its punch and die fixed to the upper and lower working surfaces, respectively. It operates through the relative movement of the worktable, which is driven by hydraulic pressure, and the interaction between the shape of the punch and die to achieve the bending of sheet metal materials (see Figures 3 and 4).
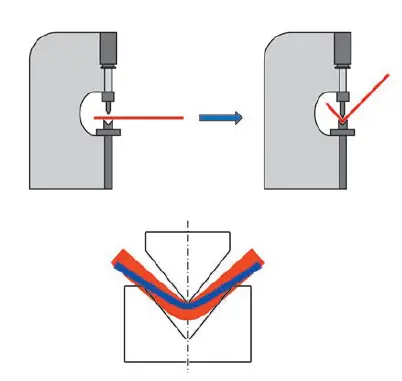
Figure 3. Press brake bend formation diagram
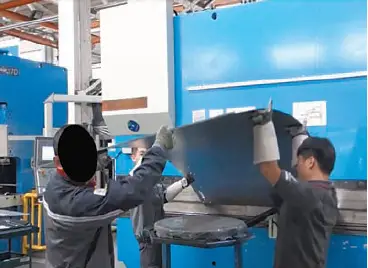
Fig.4 Attach the brake bend to the car wall
CNC folder working principle
The upper ram, driven by a motor, presses firmly against the metal sheet. The bending beam rotates upward to create the bend in sheet metal products (see Figures 5 and 6).
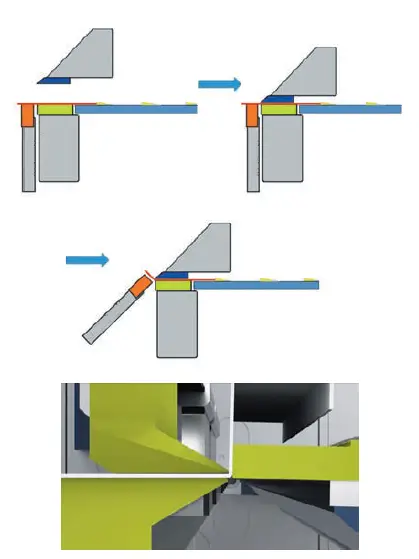
Fig.5 CNC folder bending formation diagram
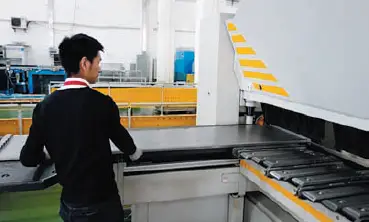
Fig.6 CNC folding car wall folder
The F Formation C Features of Press Brake and CNC Press Brake
Comparison between press brake and CNC press brake in sheet metal forming:
(1) Different training principles
Press the brake: The bend angle is controlled by adjusting the punch pressure. During the bending process, the short edge is on the inside, so operators must support most of the material from the outside. To bend heavy parts, the assistance of two or more workers may be required.
CNC paste: The metal sheet is placed flat on the workbench and the edge beam is pressed down to fix the plate. The bending beam moves up and down to perform edge bending operations. There is no need for manual intervention in positioning and auxiliary flanging during all edge bending operations.
(2) Different bending accuracy
Press brake: Dimensional accuracy control is based on the dimension accuracy of the short side of the backstop material positioning. After the bending process is completed, any final errors will affect the size of the internal space. Additionally, because the bending angle is controlled by adjusting the pressure of the top punch, the angle depends on the thickness of the material (see Figure 7).
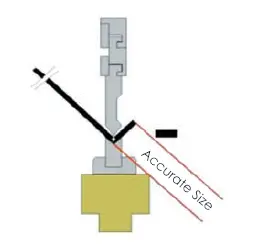
Fig.7 Press brake error accumulates in the size of the internal space
CNC folder: Dimensional precision control takes the first edge as a reference for positioning after the first bend. The final size control is precisely the size of the internal space specified by the customer. Furthermore, the bending angle is directly controlled by the bending angle and does not depend on the material thickness (see Figure 8).
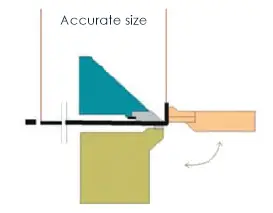
Fig.8 Internal space size of CNC folder control
(3) The problem of scratches on the material surface
Press the brake: During work, the material undergoes relative movement in the lower matrix, resulting in indentations without surface protection. When bending a large part, it is necessary to rotate the surface several times, causing inevitable scratches in the bending process.
CNC Folder: During operation, the edge pressing beam tool and bending beam tool remain stationary with respect to the material, preventing any damage to the surface. When bending a large part, all processing can be completed on one side of the board at the same time as it is placed horizontally, thus avoiding any damage to the surface.
(4) Different requirements for the worker ' skills
Press brake: Requires highly skilled workers for bending operations.
CNC Folder: Programming can be performed visually with finger painting or by engineers using offline software. The processing program can also be imported via USB or network connection. After programming is completed, the main tasks of workers are simplified to feeding and unloading, and there is no need for skilled benders.
(5) Punch and die
Press brake : Products with varying thicknesses and shapes require different top and bottom dies to accommodate their specific bending requirements. In some cases, such as arches, it may be necessary to change to a different tool or transfer the product to another machine, leading to increased transfer and temporary storage of semi-finished products.
CNC Bending : Rotating edge beam and simultaneous installation of two sets of edge beam tools allow you to perform all bending procedures in a single station. There is no need to change tools for circular arc bending or other special bending requirements, just to modify the procedure.
(6) Die life
Press the brake : Due to the relative movement of the workpiece between the punch and the die, the tooling will experience wear, which requires maintenance or replacement.
CNC paste : By preventing relative movement between the material and the tool, the tool can be used for a long time with minimal wear, greatly extending its service life.
(7) System activated
Press the brake : The hydraulic drive system requires more maintenance and is susceptible to environmental factors.
CNC folder : All-electric drive design reduces maintenance and is not affected by the environment, resulting in greater bending accuracy.
(8) Disadvantages of CNC Folder
- The bending radius of the press brake is larger than that of the press brake due to differences in bending principles.
- Parts with both sides facing down cannot be processed due to restrictions imposed by the support platform.
- The size of the part is limited by the compression area of the upper punch, so parts smaller than the size of the compression area cannot be processed.
- The bending machine is more efficient than the bending machine.
- The press brake has structural features and a diverse range of tooling options that make it easier to make complex shapes, while the press brake is less flexible in comparison.
- Edge bending machines are widely used in Europe and the United States, while Southeast Asian countries generally adopt the edge bending machine due to the influence of traditional Japanese processing concepts.
Press brake vs folding machine
In recent years, 30% of sheet metal factories in Europe and the United States have expressed a willingness to invest in using bending machines instead of press brakes to manufacture bends. This is mainly due to the fact that the operation of bending machines is more convenient and they offer numerous advantages as bending equipment.
Although both types of equipment have their own characteristics, I will compare them based on their working principles for your reference.
Press the brake:
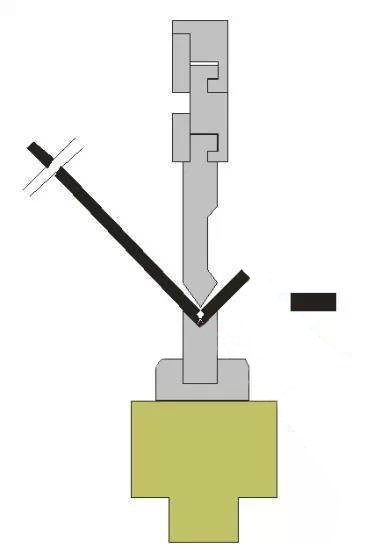
Throughout the bending process, the operator must manually hold the sheet and position it using the rear gauge. This method is not safe for operators handling large, heavy sheets, as the weight of the sheet can cause the bend angle to become greater. It is also difficult for a single operator to bend large parts.
The bending angle is determined by the depth of the upper die into the lower die, and even a small deviation in plate thickness can result in an inconsistent bending angle. Different sheet thicknesses require different punch and die configurations.
Machine installation and commissioning requires professional knowledge and a long start-up time. Furthermore, the cost of purchasing, replacing and maintaining molds is high. The maximum bending width is limited by the vertical.
Using a press brake can be more complex and requires trained and skilled workers. Each step in the process also requires a longer work cycle, and the repeat accuracy of the part depends on the skill and technology of the operator.
Folding Machine:
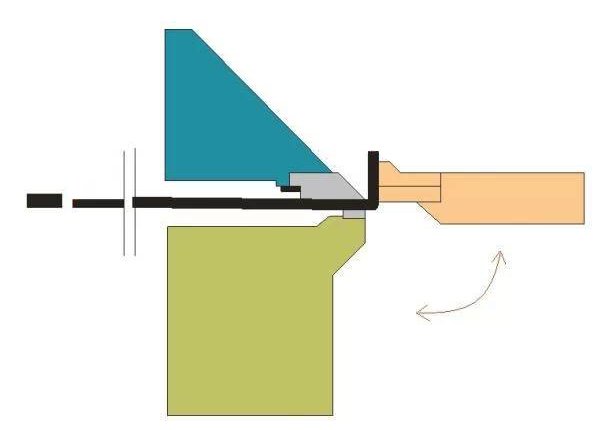
- In the bending process, the sheet material is positioned on the back gauge working table to ensure the correct bending distance and fix the plate.
- By using manual mode, operator safety is significantly improved.
- Small variations in sheet thickness will not affect bending accuracy.
- Bending plates of different thicknesses does not require mold replacement.
- Operator qualification requirements are low.
- This method provides high bending efficiency.
No. | Press Brake Features | Folding Machine Features |
1 | Large parts require multiple operators. | Large parts only require one or two operators. |
two | Braking can cause dents. | Completely free from fold marks and nicks on surface sensitive materials. |
3 | Fold size errors accumulate in the final fold. | The first bend corrects the cut size of the sheet, ensuring accurate internal dimensions. |
4 | Different tools are required for various bending requirements. | A universal folding machine tool meets most bending needs. |
5 | Bending accuracy is related to the thickness of the material. | The accuracy of the bending angle is independent of the material thickness. |
6 | The quality of the bend depends on the skill level of the operator. | No qualified operators required; the machine itself guarantees bending precision. |
7 | There are safety risks when bending large, heavy parts. | Flat processing of large metal sheets eliminates the need for support and safety risks. |
8 | Bending tools are subject to wear. | Tools for bending and fixing beams with a useful life of up to 20 years. |
9 | Setting up and adjusting parameters is challenging and it is impossible to simulate bending effects. | Chinese graphical control system for full simulation of bending effects, what you see is what you get. |
10 | Certain bending processes are difficult to complete with a press brake. | Some processes, such as arcing and bottom bending, are too simple for a press brake. |
11 | Inaccurate material cutting sizes can lead to waste. | The cut size tolerance is shifted to less critical edges, compensating for cut size deviations. |
12 | Insufficient bending accuracy increases subsequent welding and grinding workloads. | High-precision bending reduces labor hours for subsequent welding and grinding. |
13 | Multiple press brakes are required for different bending processes of a single part. | Combined with inverted clamping beams and up and down bending functions, one machine can complete all bending processes. |
14 | Using a hydraulic system increases maintenance work. | The press brake utilizes an all-electric drive system, significantly reducing maintenance workload. |