The torque wrench is mainly used to tighten screws, and its application torque is generally 20% to 90% of the twisting torque, which is continuously adjustable.
When using, first set the target torque and pull the handle.
When the torque reaches the target value, the wrench will have a slight vibration and a clear “vibration” sound.
After using a torque wrench for 3 months, the connecting rod between the head and handle broke.
To discover the cause of the fracture, the researchers carried out a series of inspections and physical and chemical analyzes and improved the heat treatment process to prevent the recurrence of such problems.
1. Physical and chemical inspection
1.1 Macro observation
The torque wrench is 1180 mm long and has a torque of 1200N·m.
The fracture occurred in the connection between the head and the handle, as shown in figure 1a).
As it is close to the head of the key, the tension here is high.
1b) is a connecting rod installed inside the key, which is mainly used to connect the head and handle, with a diameter of 16mm and a length of 350mm.
Fig. 1c) shows the macromorphology of the torque wrench fracture surface, which is divided into three areas:
Zone I is the crack source zone, located at the edge of the fracture, representing 1% ~ 2% of the fracture area;
Zone II is the fatigue expansion zone, which is bright white half-moon shaped, with obvious fatigue striations, accounting for 8% ~ 10% of the fracture area;
Zone III is a transient fracture zone with gray color and obvious torn edges, accounting for about 90% of the fracture area.
It can be seen that the connecting rod bears a large force when it breaks, which belongs to high-stress and low-cycle fatigue fracture.
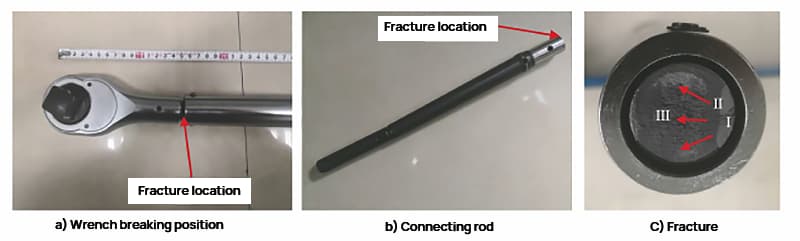
Fig. 1 Location of the fracture of the key, connecting rod and macromorphology of the fracture
1.2 Analysis of chemical composition
The connecting rod is made of 40Cr alloy steel. A cylindrical sample with a size of ϕ16mm×12mm is taken close to the fracture surface.
After being ground with a grinder and polished with a grinder, the chemical composition of the connecting rod is analyzed with a direct reading spectrometer.
It is verified that its chemical composition meets the technical requirements of the 40Cr steel alloy in structural steel alloys (GB/T 3077-2015).
1.3 Mechanical properties test
The hardness of connecting rod after quenching and tempering heat treatment is 22~26HRC.
A sample section with the size of ϕ10mm×5mm is cut from the connecting rod.
Tensile property is measured by universal material testing machine and hardness is measured by Rockwell hardness tester. The results are shown in Table 1.
The tensile strength, yield strength and elongation of the connecting rod do not meet the technical requirements.
Table 1 Connecting rod mechanical property test results
Performance Index | Tensile strength/MPa | Yield limit/MPa | Elongation after fracture/% | Hardness/HRC |
Standard value | ≥960 | ≥780 | ≥11 | 22~26 |
Measured values | 870 | 724 | 7.5 | 24 |
1.4 Observation of the microstructure
Cut the sample near the connecting rod fracture, corrode it with nitric acid ethanol, and observe it with a microscope.
It can be seen from Figure 2 that the dark gray structure is the quenched sorbite transformed from martensite after high-temperature tempering, and the lattice ferrite and acicular ferrite are distributed in parallel at the grain boundary of the original austenite.
The widmanstatten structure is distributed throughout the grain in the shape of an inverted triangle.
Ferrite in the widmanstatten structure is precipitated along the usual plane of the original austenite, and the crystal plane index of the usual plane is {11 1} γ .
In the quench cooling condition, when the temperature drops to the Ac3 line, in order to maintain the stability of the structure, the excess ferrite will be “discharged” from the solid solution to the surroundings, thus forming a network ferrite, which is a typical feature high temperature transformation.
The slower the cooling rate, the easier it is to form the lattice ferrite and Widmanstatten structure.
The connecting rod undergoes high temperature transformation during the cooling process, indicating that its heat treatment process is unreasonable.
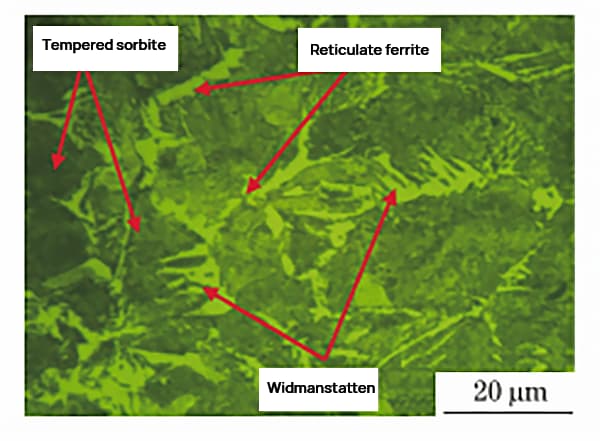
Fig. 2 Microstructure of connecting rod fracture
1.5 Fracture analysis
Fig. 3a) shows the microscopic morphology of the initial fracture area.
The initial area is located at the edge of the fracture. There are obvious concentric circular lines of bainite near the crack source.
This is a typical feature of fatigue growth, indicating that the fracture shape belongs to fatigue cracking. Power spectrum analysis is performed in the box of Fig. 3a), as shown in Fig. 3d).
The diffraction peaks of Fe, Cr, Mn and O are relatively obvious, indicating that the crack source is not caused by inclusions.
Figure 3b) shows the microscopic morphology of the expansion zone, and the fatigue groove is narrow, indicating that the stress is small during expansion.
Figure 3c) shows the micromorphology of the transient fracture zone, with many oval dimples, indicating that the connecting rod was finally fractured by tension.
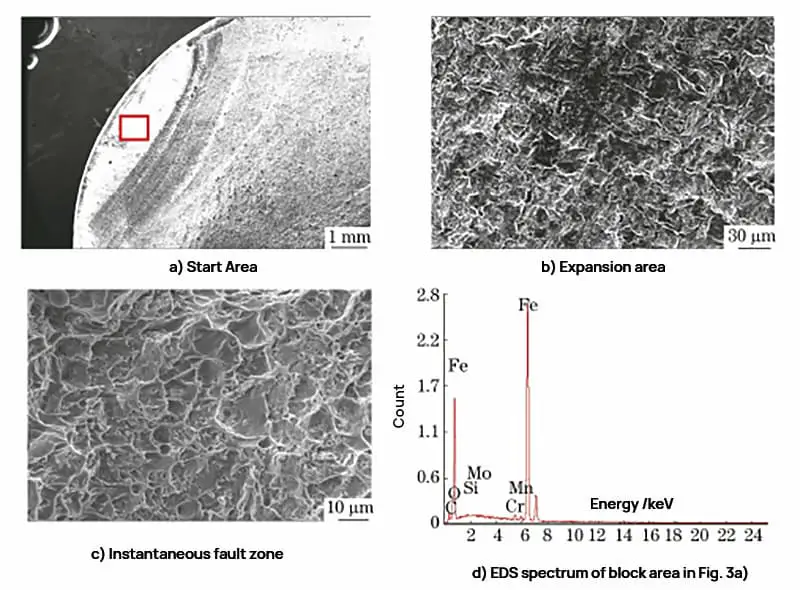
Fig. 3 Micromorphology at different positions of the connecting rod fracture surface and EDS spectrum of the box area in Fig. 3a
2 Analysis and discussion
Through the analysis of the fracture surface of the connecting rod, it can be seen that the fracture surface belongs to the fatigue fracture surface, with no inclusions on the fracture surface and no scratch damage on the surface, but its tensile strength, yield strength and elongation do not meet the technical requirements.
It can be seen from microstructure observation that the microstructure in the fracture is cross-linked ferrite and widmanstatten, which indicates that the temperature is high during the quenching and tempering process, and the austenite in the connecting rod has strong stability, leading to the formation of Widmanstatten.
Secondly, the retention time of heat treatment furnace parts in the quenching medium is long, which leads to the precipitation of ferrite at the grain boundary and the formation of a network, which reduces the interface strength and energy grain boundary, thus increasing the brittleness of the material.
Under the action of an external force, the crack begins and extends to the grain boundary, where the hardness of the ferrite is low, and the grain boundary becomes the crack propagation channel.
Therefore, it is necessary to improve the heat treatment process of the connecting rod.
3 . Improvement of the heat treatment process
Measures to improve the connecting rod heat treatment process are:
(1) The quenching temperature is reduced from 880 ℃ to 830 ℃.
Lower quenching temperature can increase the inhomogeneity of the austenite microzone composition, reduce the thermal stability of austenite, reduce the probability of high-temperature transformation of austenite decomposition into acicular ferrite, and promote the early transformation of austenite in the microzone ;
(2) Reducing retention time can prevent the growth of austenite grains and surface decarburization at high temperature;
(3) In the original heat treatment process, after the connecting rod is heated in a compact row in the cart furnace, it needs to be tempered after being loaded into the basket.
The transfer time is about 180s.
After upgrading, the connecting rod is dispersed and heated in the mesh belt furnace, which can quickly enter the quenching medium.
The transfer time is about 8s. Reducing the transfer time can inhibit the precipitation of mesh ferrite, promote the austenitic structure to quickly enter the low-temperature transformation zone, and thus produce the low-temperature martensite transformation;
(4) The connecting rod is thin and long, the tension after quenching is relatively uniform and not easy to break.
The original quenching medium is ordinary quenching oil, the oil cooling rate is low in the range of 550 ~ 650 ℃, and the average cooling rate is only 60 ~ 100 ℃/s.
The temperature range is at the “nose” of the continuous transformation C curve, which requires rapid cooling.
After 12% (mass fraction) PAG (polyalkylene glycol) solution is used, the cooling rate is accelerated.
The average temperature transformation in this temperature range can be reduced, so that a more ideal low-temperature martensite structure and a greater hardened layer depth can be obtained.
Table 2 Comparison of heat treatment process parameters before and after improvement
Process parameters | quenching temperature/℃ | Waiting time/min | Transfer time(s) | Quenching temperature/℃ | Quenching medium |
Original process | 880 | 60 | 180 | 560 | conventional quenching oil |
Improved process | 830 | 50 | 10 | 560 | 12% PAG Solution |
The improved process was used to heat treat the connecting rod and its mechanical properties were tested.
The tensile strength was 1054MPa, the yield strength was 880MPa, the elongation was 12% and the hardness was 23HRC, all meeting the technical requirements.
The microstructure after heat treatment is shown in Fig.
There is no lattice ferrite, Widmanstatten structure or massive ferrite, and the structure is uniform and stable.
After improved process heat treatment, the connecting rod has been in service for 18 months without fracture.
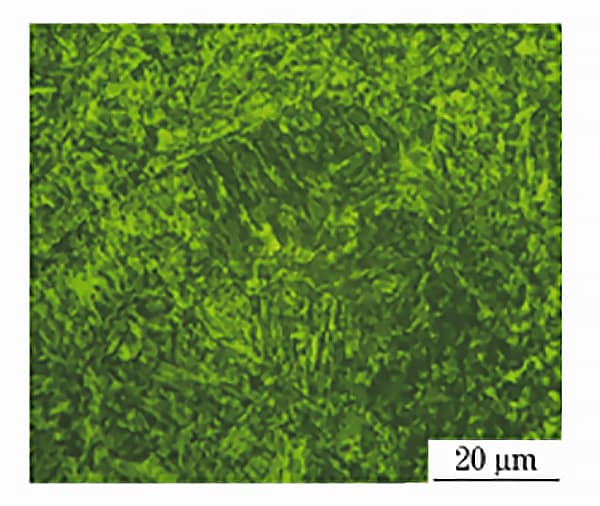
Fig. 4 Connecting rod microstructure after improved process heat treatment
4. Conclusion
(1) The hardness of the connecting rod is qualified, and the tensile strength, yield strength and elongation do not meet the technical requirements;
The microstructure is tempered sorbite+crosslinked ferrite+widmanstatten.
The fracture belongs to fatigue fracture. The crack originates on the outer surface of the connecting rod and there is no inclusion at the source of the crack.
(2) The reason for the fracture of the connecting rod is that the heat treatment process of the connecting rod is not qualified, resulting in its poor mechanical properties.
The heat treatment process is improved by reducing the quenching temperature, shortening the retention time and transfer time, and increasing the quenching cooling rate.
(3) After the improved process heat treatment, the mechanical properties and microstructure of the connecting rod meet the technical requirements, and the connecting rod has not been broken after 18 months of service.