Rail is the abbreviation for railway and is made of high hardness and toughness manganese steel.
Manganese steel is hard, wear-resistant and has a certain impact resistance, which meets the requirements for rail manufacturing.
In addition, the density of manganese steel rails is high, and when an oxidized rust film forms on the surface, it will protect the interior and will not affect its use.
Iron and steel are distinguished by the amount of carbon they contain. Iron-carbon alloys with less than 2% carbon content are called steel, while those with more than 2% carbon content are called pig iron.
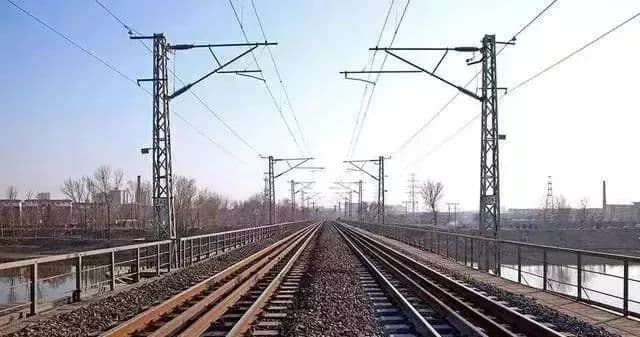
From a metallurgical point of view, there is no such thing as “stainless iron”. Stainless steel is also a type of steel. Steel rusts due to lack of corrosion resistance, and the main element that determines the corrosion resistance of stainless steel is chromium.
Steel with a chromium content of more than 10.5% will not rust. At this point, the reaction of chromium with the oxidizing agent in the corrosion medium forms an oxide film on its surface, which can prevent further basic corrosion.
The cost of producing iron is much lower than that of producing stainless steel. For some materials with a short service life and where iron can meet the material requirements, iron will be used.
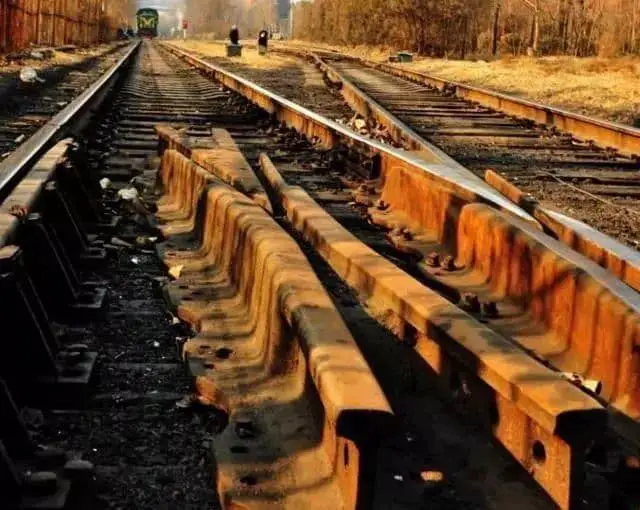
“Rail” is a commonly used term, but it is actually steel rail. Manganese is generally added to improve its compressive strength and wear resistance.
Stainless steel often contains chromium and molybdenum elements to resist oxidation and corrosion. When using steel rails, it is necessary to consider factors such as strength, wear resistance, flexibility, ductility and corrosion resistance.
However, high strength and wear resistance are the first choice, and stainless steel cannot meet these requirements and will not be used.
The reason why stainless steel cannot be used is that it is not durable enough and is easily damaged due to thermal expansion and contraction.
Under daily exposure to wind, rain and sun, stainless steel is easily damaged.
Although this high manganese rail looks rusty, it only has a layer of rust on the surface and the interior is still as good as new.
In addition, the density of manganese steel rails is high, and when an oxidized rust film forms on the surface, it will protect the interior and will not affect its use.
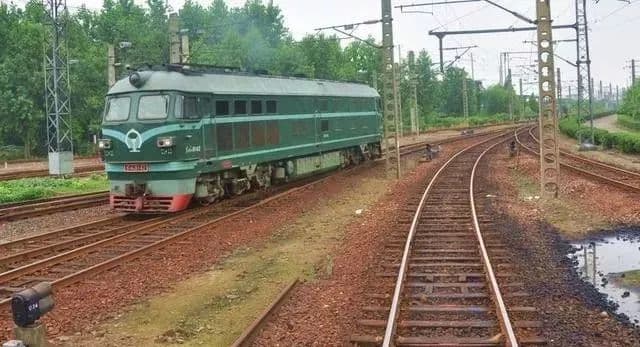
Firstly, from a technical point of view: people generally believe that stainless steel does not rust, but in reality stainless steel, like other alloys, does rust.
The difference is that after rusting, the surface forms an oxide film (rust) the same color as the stainless steel appearance. Furthermore, this oxide film is relatively dense, which can protect the internal structure from further oxidation and rust.
However, this oxide film can still be corroded under certain conditions, especially in a moist, acidic environment where corrosion is evident.
Therefore, there are many situations in which stainless steel cannot be used.
There are many types of stainless steel, and the hardness of stainless steel (especially austenitic stainless steel) is relatively low.
For example, stainless steel knives are difficult to sharpen, and even if they can be sharpened, they will dull quickly.
Experienced people know that polished stainless steel plates scratch easily due to their soft texture.
From a technical point of view, stainless steel is not rust-free, but rather its appearance after rusting is similar to its appearance before rusting. Its properties are also not suitable for use in all locations, therefore it cannot be replaced by other materials without exception.
From a resource perspective, the nickel and chromium used in stainless steel are relatively rare minerals, especially nickel, which is scarce. Useful and effective things need to be used in key areas and cannot be wasted.
From a cost point of view, when purchasing materials, manufacturing parts and assembling machines, cost is always considered.
The price of stainless steel is not just a little higher than that of ordinary steel, aluminum, magnesium-aluminum alloy, plastic and other materials, but several times higher.
As long as cheaper materials can meet the requirements, who would use more expensive materials?
Furthermore, even though other materials rust and are not corrosion resistant, there are now many surface treatment techniques that can protect materials from corrosion.
For example, painting, powder coating, electroplating, electrophoresis, surface oxidation, surface chemical treatment (nitriding, cyanidation, etc.) can improve the corrosion resistance of materials.
Therefore, materials that rust are not necessarily unsuitable for use in corrosive environments.
Overall, stainless steel cannot replace all other materials. Only after fully considering factors such as part function, material properties, working environment, part cost, processing performance and possibilities can a suitable material be selected for the part.
It is not appropriate to simply use stainless steel to replace all materials. In mechanical and materials engineering, there are specialized courses in materials that present how to select materials and their properties.
Train tracks are an established mode of operation for railways and an indispensable technology for operating trains.
As everyone may have noticed, almost all train tracks are rusty, even the newly built ones. Rusty iron products not only have a shorter lifespan, but also become very brittle.