I. Working principle
1. Electrolysis uses the polishing piece as the anode and an insoluble metal as the cathode. When both are immersed in an electrochemical bath and direct current is applied, selective anodic dissolution occurs, resulting in a highly smooth and shiny appearance on the surface of the stainless steel.
2. Electrolytic action ensures stainless steel is a consistent color inside and out, clean and shiny with long-lasting shine. Forms a thin, viscous film on the surface, increasing corrosion resistance.
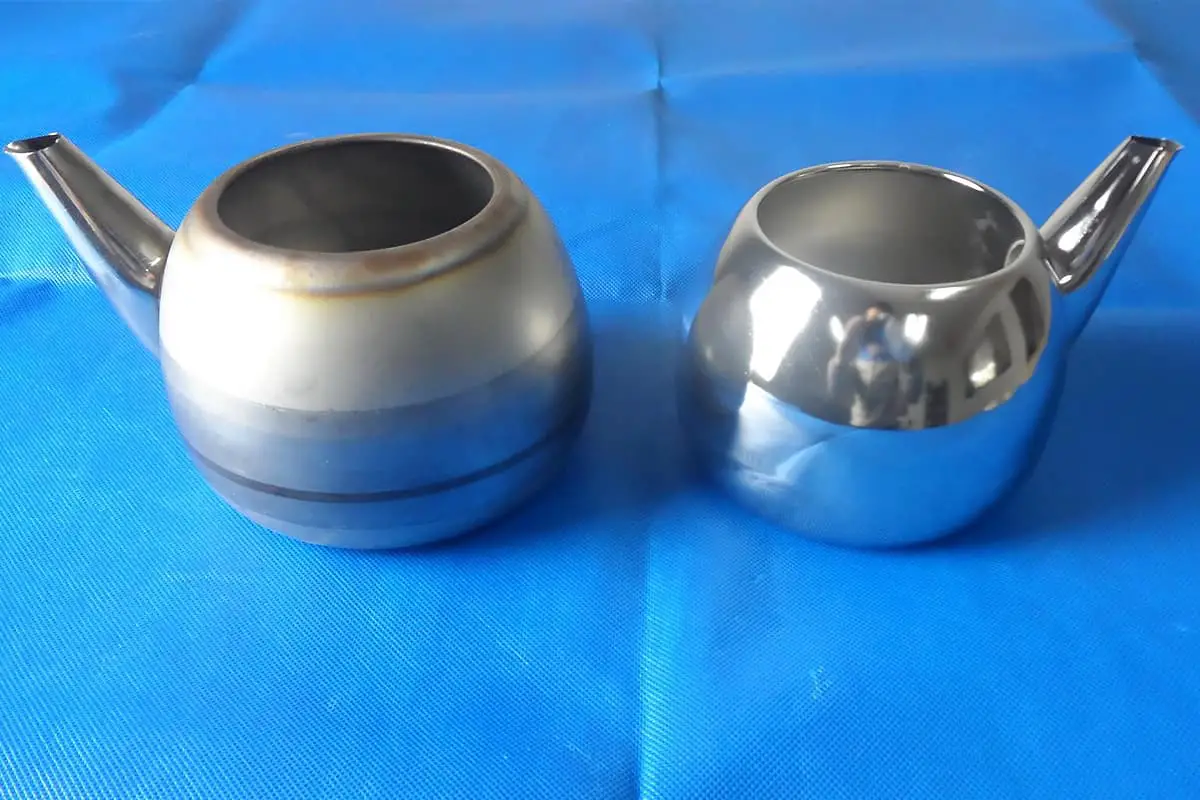
II. Composition of the Electrolyte Solution and Process Conditions
1. Phosphoric Acid:
It dissolves and forms a protective phosphate film on the surface of the stainless steel, preventing excessive corrosion. The ideal concentration is around 750mL/L.
(1) If the concentration is too high, the electrical resistance of the bath increases, the viscosity increases, leading to a higher required voltage and slower leveling.
(2) If the concentration is too low, it will cause uneven corrosion on the stainless steel surface due to higher activation and lower passivation tendencies.
2. Sulfuric Acid:
As an activator, it improves the conductivity of the solution, reduces resistance, thus reducing the bath voltage, saving energy and increasing the dispersion capacity and efficiency of the anode current. The ideal concentration is 180~210mL/L.
(1) If the concentration is too high, the surface may be excessively corroded, resulting in uniform and dense corrosion.
(2) If the concentration is too low, it will cause severe and uneven corrosion.
3. Chromic Anhydride:
Strong oxidizer, forms a passivation film on the surface to prevent corrosion, contributing to a smoother surface. The ideal concentration is 50~60g/L.
(1) If the concentration of chromic anhydride is too low, it will be challenging to achieve a shiny surface.
(2) If the concentration is too high, sedimentation may occur under high current, reducing current efficiency and leading to pitting and other forms of excessive corrosion on the polishing surface.
4. Glycerol (Glycerin):
It plays a significant role in inhibiting corrosion. It reacts with phosphoric acid to form metallic complexes and derivatives, making the polished surface extremely shiny and delicate. Glycerol also prevents chemical corrosion of stainless steel in the electrolyte.
(1) If the concentration is too low despite a shiny polished surface, corrosion can make it rough.
(2) With higher concentration, it can overcome roughness, resulting in a shiny and delicate polished surface.
(3) If the concentration is too high, excessive foam may be produced, affecting operations and wasting material.
5. Saccharin: Increases shine.
(1) Saccharin, when involved in cathodic processes, can be adsorbed on metal surfaces, contributing to the shine and shine of the polished surface.
(2) In anode processes, saccharin forms an adsorption film on the anode surface, which protects the stainless steel surface from electrolytic erosion when there is no current. When power is applied, the electrical lines first break through the insulation film on the raised parts, initiating dissolution, while the recessed areas are effectively protected, resulting in selective dissolution for a smooth, shiny surface.
6. Current density:
(1) At low current densities, the metal is in an activated state, with the polished surface being eroded. Anodic dissolution products are minimal and chemical dissolution dominates electrochemical dissolution, leading to poor smoothness.
(2) When the current density exceeds the appropriate value, intense oxygen evolution occurs, causing overheating and excessive corrosion on the metal surface, leading to irregular dissolution and increased electrical energy consumption.
7. Temperature:
A moderate increase in temperature can speed up the leveling process and improve current efficiency, thereby increasing the smoothness and gloss of the surface.
(1) Too low a temperature increases the viscosity of the electrolyte, making it more difficult for anodic dissolution products to diffuse from the metal surface into the electrolyte and replenish the anode.
(2) Too high a temperature increases the amount of dissolved metal, producing steam and gas in the tank that displace the electrolyte from the metal surface, paradoxically slowing the rate of metal dissolution. Decreasing viscosity near the electrolyte accelerates the diffusion of dissolution products, leading to accelerated dissolution rates and impacting surface smoothness.
III. Preparation of the electrolyte solution
The solution should be prepared according to the volume content (% (V)) or mL/L and mass content (% (w)) or g/L in the formula, which will differ when calculating the dosage.
1. Volume content
Assuming the liquid volume of the tank is 1000L, the dosage calculation and preparation steps are as follows.
The. Phosphoric acid dosage: XmL/L×1000L=XL. Measure and add XL phosphoric acid to the tank.
B. Sulfuric acid dosage: XmL/L×1000L=XL. Measure and gradually add XL sulfuric acid to the phosphoric acid while stirring.
w. Water dosage: XmL/L×1000L=XL. Place in a separate container.
d. Chromic anhydride dosage: XmL/L×1000L=XL. Add heavy chromic anhydride to water and stir until it dissolves in a chromic acid solution.
It is. Gradually add the chromic acid solution to the phosphoric-sulfuric acid solution, stirring until uniform. The solution will appear yellow.
f. (1) Gelatin dosage: Xg/L×1000L=Xkg. Stir the heavy gelatin in hot water until smooth, then slowly add it in small batches to the phosphoric-sulfuric acid solution. This will initiate a strong reduction reaction and the electrolyte will turn yellow-green.
(2) Gradually add the calculated amount of glycerin to the tank while stirring. This will also initiate a strong reduction reaction and produce excess foam. To prevent the solution from overflowing due to foam, be especially careful when adding glycerin. The solution will also turn yellowish-green. Leave to cool undisturbed.
2. Bulk Content
The. Measure the specific gravity of the phosphoric and sulfuric acids used, assuming the measured density of phosphoric acid d1=1.7g/mL, density of sulfuric acid d2=1.8g/mL.
B. So, from the chemical data tables of the relative density of each acid, it can be seen that: in 100g of acid solution, the phosphoric acid content P1=86.25g, the sulfuric acid content P2=88g.
w. Calculate the required volume of phosphoric acid V1 and sulfuric acid V2.
V=xdo×1000/pd (L)
Where x is the mass percentage of the acid in the formula; do is the density of the solution, take the average value=1.65g/mL
d. Water volume=1000-V1-V2
It is. Chromic anhydride dosage.
As chromic anhydride is a solid acid, the required mass is calculated using the formula xd0×1000/100 (Kg).
f. Add the calculated amount of chromic anhydride to the required water and stir until dissolved.
g. Add the calculated amount of phosphoric acid to the chromic anhydride solution and stir until uniform.
H. Gradually add the calculated amount of sulfuric acid to the solution from step g while stirring.
3. Measuring the relative density of the solution:
After the prepared solution has cooled to room temperature, measure its relative density using a hydrometer.
1. If the relative density exceeds 1.7, add an appropriate amount of water to the electrolyte, diluting it until the relative density is in the range of 1.6 to 1.7.
2. If the relative density is between 1.6 and 1.7 but the electrolyte volume is insufficient, replenish the required amount of phosphoric acid, sulfuric acid and chromic anhydride according to the lack of volume.
3. If the relative density is below 1.6 and the volume is already sufficient or slightly exceeded, heat the electrolyte to 80°C and evaporate the moisture until the relative density reaches the range of 1.6 to 1, 7.
4. Electrolytic treatment: Hang a lead plate on the cathode and a stainless steel plate on the anode. At a temperature of 70 to 80°C, apply a current density of 60 to 80A/dm² with a duration calculated at 40Ah/L.
Then start trial production. If pitting corrosion appears on the surface of the workpiece or the surface gloss is not satisfactory, the addition of chromic anhydride, gelatin and glycerin can quickly increase the content of hexavalent chromium and trivalent chromium in the electrolyte to the required levels.
Electrolytic treatment can turn the electrolyte slightly green, indicating that a certain amount of nickel and chromium ions have dissolved in the electrolyte, allowing successful experimental production.
4. Electrolyte maintenance and process requirements:
1. Stainless steel must be thoroughly degreased before electrolysis to avoid oil contamination of the bath.
2. The relative density of the solution should be measured regularly during use and adjusted immediately.
3. Metallic elements of iron, chromium and nickel in stainless steel dissolve in the electrolyte during the electrolysis process. Once accumulated to a certain extent, they increase the viscosity and strength of the solution, resulting in a dull surface on stainless steel.
You can choose between two methods:
- Dilute the solution with an appropriate amount of water to reduce the acidity. Impurities such as iron, chromium and nickel can form localized phosphates and precipitate. Remove sediment from the bottom of the bath, heat and evaporate the water to restore the original relative density.
- Replace part of the solution, preferably retaining 20% of the old solution and supplementing with 80% of the new solution.
4. Cleaning the cathode lead plates: During electrolysis, the surface of the cathode lead plate accumulates a thick layer of impurities, such as iron and nickel, hindering the conductivity of the cathode surface and reducing the current. This impairs the anode current density and seriously affects the quality of electrolysis. It is crucial to remove these deposits in a timely manner to maintain the fluidity of the circuit.
5. Cathode-anode area ratio: The cathode area is maintained at 1/2 to 1/3.5 of the anode area to inhibit the increase of trivalent chromium. Excess trivalent chromium is oxidized to hexavalent chromium on the anode surface. An overabundance of trivalent chromium can lead to electrolytic aging.
6. Spacing between electrodes:
- A large distance increases resistance, energy consumption and can cause heating of the solution, affecting the quality of electrolysis.
- A small distance may cause a short circuit and darkening of the product. The ideal distance between the cathode and anode is 100-300 mm.
7. Cutting off the power supply when entering and leaving the tank: The power supply must be cut off when the work pieces are placed in or taken out of the tank. It is not advisable to transport or remove accessories with electricity as this may result in electrical sparks, cause electrolysis and potentially ignite a mixture of hydrogen gas and oxygen clumped on the surface of the tank.
8. Control the appropriate anode current density: The anode current density is proportional to the dissolution of the metal. Choosing the correct anode current density and controlling it within a certain anode potential range is essential for good electrolysis quality.
- If the anode current density is too low, general dissolution of the anode occurs on the surface of the part without any effect.
- B. If the anode current density is too high, the membrane is punctured, oxygen is rapidly released in gaseous form, surface overheating occurs, electrolyte swelling intensifies, the membrane is ruined, no longer exists, and electrochemical corrosion occurs .
9. Control the bath temperature:
- The temperature must be maintained within the prescribed process range to maintain normal capping rate, reduce electrolyte viscosity, decrease anode membrane thickness, accelerate diffusion of anode dissolution products, accelerate solution convection, facilitate detachment of gas bubbles trapped in the anode and prevent stains or stains from occurring.
- If the temperature is too high, it can cause the solution to overheat, accelerating the conversion of hexavalent chromium to trivalent chromium (Cr 6+ +3e→Cr 3+), which can lead to surface corrosion.
- If the temperature is too low, it may increase the viscosity of the solution and the thickness of the anode surface membrane, inhibit the diffusion of anode dissolution products, and significantly reduce the leveling effect.
10. Optimal proportion of hexavalent chromium and trivalent chromium: The solution should maintain a yellowish-green color during the production process.
- If the color is predominantly yellow, it indicates that the electrolyte contains excess Cr 6+. Add an appropriate amount of gelatin or glycerin to partially reduce hexavalent chromium to trivalent chromium, or use a large cathode and a small anode for electrolysis to generate trivalent chromium.
- If the color is dark green, it means that the electrolyte contains excess Cr 3+. Dissolve a proportional amount of chromic anhydride in water and add it to the solution, or use a large anode and small cathode for electrolysis to partially convert trivalent chromium into hexavalent chromium, which can also improve the quality of the solution.
5. Medical Device Co., Ltd. Process Flow
(1) Using the chemical activation method, stainless steel is lightly etched before electrolysis to remove the passive film and activate the metal surface.
After gentle etching, it should not be left in the air for a long time, it should be immediately cleaned, dried and transferred to electrolysis.
Gentle etching process: Sulfuric acid: 3% ~ 5% Temperature: Room temperature Duration: 0.5 ~ 1min
(2) Components and working conditions of electrolyte solution
- Phosphoric Acid (H3PO4.85%) (d=1.65) (60%~70%) (Optimal: 70%)
- Sulfuric Acid (H2SO4.98%) (d=1.84) (8%~15%) (Optimal: 12%)
- Chromic Anhydride (CrO3) (5%~15%) (Optimum: 12%)
- Glycerol or Gelatin – 12% (8g/L)
- Water – Remaining Quantity
- Temperature (°C) – (50~100) (Optimum: 50~70)
- Voltage (V) – 10~20
- Anode current density A/d㎡ – (10~55) (ideal: 15~30)
- Relative density of the solution (g/cm 3) – 1.6~1.7
- Duration (min) – 30~45 (based on part size)
- Cathode to anode surface area ratio – (1~1.5):1
- Cathode Material – Lead
4. Analysis of common problems in electrolytic polishing of stainless steel
1 . Marks on the surface of the workpiece
The main cause is the uneven distribution of current density. There are several factors that influence this unequal distribution, including:
1. Inconsistent current density caused by the device structure. Modifying the fixture structure to ensure balanced, even contact with the workpiece can help. Ideally, we should increase the contact area between the accessory and the part, while ensuring the quality of the accessory.
2. The specific gravity of electrolytic polishing fluid drops or exceeds the maximum value. If it exceeds the required specific gravity range, the surface of the part will be subject to marking. The ideal specific gravity for electrolyte fluid is 1.72.
3. High temperature can increase the conductivity of electrolytic fluid and improve the surface gloss of the workpiece. However, it can also lead to uneven distribution of current density, resulting in marks.
4. Reworked parts tend to develop marks during the second round of electropolishing. To avoid this, the duration and current of the second round of polishing must be reduced.
5. Inadequate gas escape is mainly due to the improper angle of the accessory on the workpiece. The direction of the holes in the part must be upwards and the clamping angle must be adjusted to allow easy gas dispersion during electrolytic polishing.
6. Prolonged electropolishing time may cause marks due to excessive corrosion. Electrolytic polishing is a microscopic leveling process. When the surface of the part reaches a microscopic level of shine and smoothness, oxidation on the surface of the part stops. If electrolysis continues, excessive corrosion will occur, causing marking.
7. High current may result in corrosion spots. If the current passing through the part during electrolytic polishing is too high, the dissolution rate of the part surface exceeds the oxidation rate, resulting in excessive corrosion and pitting.
two . Superficial burns on the workpiece
Several factors can lead to this defect:
1. If the part is not correctly positioned in the fixture before electropolishing, it may become loose and wobble during the process. This looseness can lead to poor contact with the device or direct contact with the device's cathode, causing a short circuit and subsequent burns.
2. If the operator does not perform a short circuit test on the accessory after assembling the part and proceeds directly to electropolishing, a short circuit may occur. Without testing, it is uncertain whether the assembled part is in contact with the cathode. If contact occurs, the part may burn.
3. Fixing problems may arise after prolonged use, especially when the accessory comes into direct contact with the part. If the contact points on the fixture become uneven, the current density supported by the part's contact surface during electrification may vary, causing burns in areas with higher current density.
3. Bleaching, darkening and yellowing of the surface of parts
1. Surface bleaching: The main cause of part surface bleaching is subsequent operations, especially during the oven baking process. If the temperature inside the furnace is too high and moisture in the air and on the surface of the part cannot be expelled effectively, the problem arises. To mitigate this situation, the oven temperature must be controlled at around 80±2°C, and it is preferable to use an oven with a good gas circulation system.
2. Surface darkening: This undesirable phenomenon occurs mainly where the part comes into contact with the fixture and is predominantly due to the fixture itself. Once the electrolytic polishing of the previous piece has been completed, the piece must be removed from fixation in 10% diluted nitric acid. After removing the part, the accessory must be thoroughly cleaned with water before moving on to the next part.
3. Surface yellowing: This problem appears mainly where the part comes into contact with the accessory. When the contact area between the workpiece and the accessory anode is relatively small, the contact point can generate high temperatures and heat during electrolytic polishing. Since the contact area is not in contact with the electrolyte for cooling, slight burns may occur, resulting in yellowing. The solution to this problem mainly involves reasonable improvements to the accessory contact points or adjustment of electropolishing parameters.
4. Black and burnt marks on the workpiece
The formation of these marks is due to the high current required for the electrolytic part, which exceeds the maximum current that the hanger can withstand. Solutions include:
1. Choosing a material with better conductivity for the hanger:
Generally, the conductivity of copper is more than 20 times that of titanium, so copper brackets have stronger conductivity than titanium brackets and are less likely to form marks. Phosphor bronze can be used, as it has good elasticity and hardness. However, the useful life of the hanger and its resistance to corrosion, where titanium stands out, must also be considered.
2. Increasing the number of suspension points:
First, determine the condition of the suspension points after electrolysis. If only small marks form under current conditions, increasing the number of suspension points may solve the problem.
3. Reducing Voltage Appropriately:
Higher voltages accelerate the light emission process, which can reduce electrolysis time and increase production efficiency. For this reason, factories generally operate at slightly higher than normal voltages. However, if the tension set is too high, it may exceed the maximum load of the suspended wire and create marks.
4. Decrease or control the electrolyte temperature:
When the electrolyte temperature is high, the conductivity of the hanger decreases significantly and the current required by the part increases dramatically. This can overload the hanger and create marks. In this case, lowering the electrolyte temperature may solve the problem. If the temperature exceeds 80 degrees and streaks form, a cooling trough can be constructed around the electrolyte tank, with circulating water continually cooling the electrolyte.
5. Analysis of other causes of polishing defects
Polishing defects | Reasons: | Solution: |
Presence of stains or small stains on the surface | Presence of oil marks or rust on the surface | Clean thoroughly to remove oil and rust. |
Excessive corrosion on the edges and ends of the workpiece | Excessive current, high temperature or prolonged duration | Adjust the corresponding parameters. |
White stripes on the surface of the workpiece | Dense electrolyte solution | Dilute with water to a density of 1.72. |
Variable quality of workpieces from the same groove | Too many work pieces or mutual interference | Reduce the number of work pieces or modify accessories. |
Excessive foam on the electrolyte surface | Dirty part | Make sure the workpiece is completely clean. |
Opaque surface with white spots | High chromic anhydride content | Consider using environmentally friendly electrolyte solution |
Exorbitant electricity costs | High current density | Consider using environmentally friendly electrolyte solution |
Sparks observed during electrolysis | Poor contact between accessory and workpiece | Change accessories and increase touch points. |