Last updated April 28, 2022
There are many metal casting methods that have been used for centuries. Some of these methods are over 5,000 years old. One of the most modern and effective methods is pressure casting.
Pressure casting is a metal casting process in which molten metal is poured into a mold so that it solidifies and takes the shape of the mold. This metal forming technology allows for a variety of part sizes and shapes, even complex shapes with internal cavities or hollow profiles.
Casting is not limited to metals, but can also be used for non-metallic materials such as glass, ceramics and plastic. Most metal castings are made from non-ferrous metals such as zinc, aluminum, copper, magnesium and lead. This article explains the details and benefits of aluminum casting to help you choose the best material to produce your desired aluminum parts.
Aluminum die casting is one of the most widely used processes and is used in all major industries to produce aerospace, electronics, automotive components, etc. Learn more about how aluminum casting works.
What is aluminum casting?
Aluminum pressure casting is a process for producing aluminum parts with good texture or smoothness, good surface finish and high dimensional stability. The reasons why aluminum is used for metal casting are as follows:
-
It is light and very stable for complex shapes and thin walls.
-
It has high thermal and electrical conductivity.
-
It has good corrosion resistance.
-
It maintains its resistance even at very high temperatures.
Of the two basic types of die casting equipment and machines, hot chamber die casting machines and cold chamber pressure casting machines, aluminum castings are processed in cold chamber machines. Since the strength of the aluminum alloy is maintained even at very high temperatures, high pressure is required.
Therefore, the molten metal is melted in a separate furnace before being fed into the cold chamber machine. The machine then presses the molten metal into the mold using a pressurized piston.
How does aluminum casting work?
As with any typical die casting process, aluminum die casting involves pouring liquid aluminum into a mold, called a die, and allowing it to solidify into the desired shape. Die casting dies consist of at least two halves to allow for removal of the castings. The shape of the dies influences the very complex shapes and intricate characteristics of the casting. This is more or less the core of every casting technique.
The aluminum casting process can be divided into the following 9 steps:
1. Aluminum alloy ingots are subjected to high temperatures until they melt;
2. The two halves of the die are cleaned and lubricated before being fixed;
3. The mold is made using two steel dies that are formed into the desired shape and fixed together by a die casting press.
4. Molten aluminum is then injected into the cavity under high pressure, allowing it to solidify.
5. The process of transferring molten metal to a chamber before injection depends on whether a cold chamber or hot chamber pressure casting machine is used.
6. Cold chamber die casting machines are used to cast alloys with high melting points such as aluminum, magnesium, etc. Therefore, aluminum casting utilizes a cold chamber machine in which molten metal is hollowed out of the casting rather than being pumped through hydraulic cylinders;
7. The hot casting is allowed to cool and solidify. The molten metal fills the mold cavity and takes the desired shape of the mold design.
8. The two halves of the mold are separated and the casting is ejected;
9. Finally, excess aluminum casting material is removed through secondary operations such as sawing, cutting, etc.
Aluminum casting is one of the fastest and most accurate high-pressure casting processes. Reclaimed aluminum mold has good texture, is very hard, corrosion resistant and requires minimal surface processing. Steel molds are reusable unlike sand casting molds and therefore aluminum die casting is the most viable method for mass producing aluminum parts.
Aluminum alloy material for die casting parts
The most commonly used alloys for aluminum casting are A360, A380, A383 and A413. Each has its own advantages and therefore the choice of alloy depends on the project requirements. Some of the properties of these alloys are summarized in the table below.
Cast aluminum material |
A360 |
A380 |
A383 |
A413 |
toughness |
75 |
80 |
75 |
80 |
Elongation (% in 2 inches) |
2.5 |
3.5 |
3.5 |
2.5 |
Pure strength |
28 |
28 |
– |
25 |
Tensile strength (ksi) |
25 |
23 |
22 |
21 |
Maximum tensile strength (ksi) |
44 |
46 |
45 |
43 |
Thermal conductivity |
65 |
56 |
56 |
70 |
Electrical conductivity (% Cu) |
30 |
27 |
23 |
31 |
Density (lbs/in3) |
0.095 |
0.099 |
0.099 |
0.096 |
Is post processing necessary for aluminum casting?
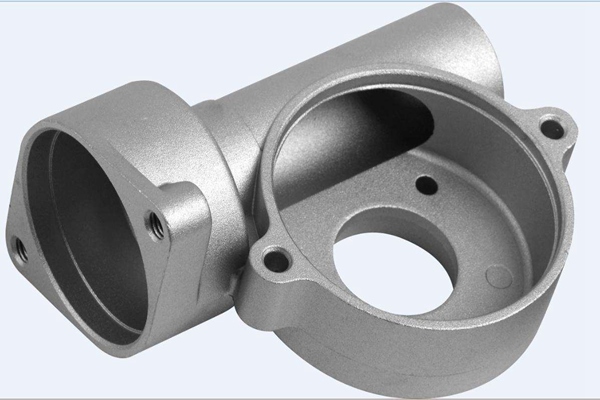
After a casting is removed from the mold, it still requires post-processing to improve the aesthetics and functional properties of the part. This post-processing can give the component shine, guarantee high corrosion resistance, increase wear resistance or protect it from environmental influences.
However, an aluminum mold requires minimal to no post-processing because it already has a very good surface finish by casting standards. Small surface imperfections can be easily corrected by sanding, using an abrasive material such as sand to smooth the surface.
Other finishing processes, such as sandblasting and powder coating, can also be carried out on the metal part to improve wear resistance or apply a protective layer.
Advantages of aluminum castings
Aluminum casting is one of the most used casting processes worldwide. It is the best economical alternative to other procedures. Some of the main reasons why aluminum castings are exceptionally good are as follows:
– As aluminum is a lightweight metal alloy, lightweight parts can be produced without compromising their strength.
-It is versatile and allows the production of thin-walled parts, simple or complex shapes with high precision
-Aluminum castings are well textured or smooth depending on the need
-As the process is very fast, tens of thousands of parts can be produced in less time and at a lower cost
-This mass production is very economical compared to other die casting processes
-The parts are highly resistant to corrosion and are excellent conductors of heat and electricity
Aluminum Die Casting VS Sand Casting VS Vacuum Die Casting
The decision of which casting process to use depends on the design features needed for a specific part. There are different types of casting processes, each with its own advantages related to injection systems, such as aluminum die casting, sand casting, and vacuum die casting.
Cast aluminum
In aluminum pressure casting, aluminum is injected into mold cavities at high speed and high pressure. The entire process is very efficient and fast, making it ideal for high volume production. The casting has a good surface finish and requires minimal post-processing. Due to its light weight, aluminum is often preferred for producing thin-walled parts without compromising its strength.
Aluminum has a high melting point and is processed in a cold chamber die casting machine. However, due to high pressure injection, gas inclusions may occur in the casting, causing porosity.
Sand casting
Sand casting involves pouring molten metal into sand molds without applying pressure. It is the oldest and most commonly used low-cost casting process for producing blanks or complex parts such as engine blocks, crankshafts, and automotive cylinder heads. As the sand mold has to be removed to remove the casting, this is a very slow process and not suitable for mass production.
Vacuum Casting
Vacuum pressure casting is an advanced casting process that uses a vacuum to suck liquid into the mold. This prevents air entrapment in the cavity and removes dissolved gases that cause porosity on the part surface.
Vacuum casting allows you to cast thin sections with good surface finish, improving the mechanical properties of the casting and reducing the need for additional machining for finishing. However, the mold sealing structure is complex and the cost of the entire process is high.
Design Tips for Cast Aluminum Parts
To get the best results with aluminum castings, there are a few important factors to consider.
Material selection
As explained above, several aluminum alloys are commercially available. Based on the project requirements, you can choose between the alloys considering properties like hardness, strength, conductivity, melting point, fluidity and compressive strength, etc. When selecting materials, great care must be taken to obtain the desired properties of metal parts.
Machining allowance
To ensure that the casting retains its properties and has a uniform density, a sufficient machining margin must be maintained. Machining allowance is the removable material from a finished casting. A very small addition causes defects on the surface of metal parts, while a very large addition increases the process execution time. Therefore, a balanced addition is important to obtain optimal results.
Shrinkage during construction
Shrinkage is an important design consideration in any manufacturing process. Any material, including metal, shrinks when cooked or solidified. Since thicker areas tend to shrink more than thinner areas, you may want to consider incorporating thinner sections into the design to avoid porous and uneven surfaces.
Wall thickness
Achieving uniform thickness of aluminum castings is very difficult. Thin-walled castings are in high demand as they have lower material costs and make the part lightweight. However, a slight imbalance in the thickness uniformity of thin-walled parts can affect the strength of the component.
Part strength
As already mentioned, different aluminum alloys have different strength spectrums. Therefore, alloys must be carefully selected for the required strength of the part. Another factor that influences the resistance of the part is the pressure casting technology. In general, vacuum casting is an excellent option for improving part strength and minimizing surface porosity.
assembly process
It is important to properly plan the assembly of parts to avoid defects in the casting design. Since the assembly of simple structures is different from the assembly of complex structures, it is best that the necessary assembly process is properly identified and planned.
Project appearance
When the aesthetics of a casting are important, finishing processes such as electroplating, shot peening or sand blasting can be carried out depending on the appearance requirements of the component. These techniques improve the appearance of the component without compromising its durability and properties.
Concluding
Aluminum pressure casting is a very practical, economical and high-precision casting process for mass production of complex parts. The choice of material and casting process depends on the desired design features. Therefore, all aspects must be considered and planned effectively to achieve the best results.
Common questions
Here you will find answers to some of the most frequently asked questions about aluminum die casting.
1. Is aluminum suitable for die casting?
Yes, aluminum has high electrical and thermal conductivity and is resistant to corrosion. Its low density and good mechanical and thermal properties make it a good alloy for pressure casting.
2. How stable is cast aluminum?
Although aluminum casting is not as strong as steel casting, it is very stable and durable compared to sand casting and magnesium or zinc casting.
3. Can steel be produced by pressure casting?
Yes. However, it is a ferrous metal and contains iron, which is why it is not corrosion resistant and therefore not preferred.