1. Process Overview and Problem Statement
The welding shop can generally be divided into two main parts: material preparation and assembly welding. Harmful substances generated during the material preparation process are minimal.
Part assembly welding typically includes welding, accessory assembly, temporary spot welding, testing and inspection, acceptance, cleaning, painting and drying processes.
Different welding methods such as manual welding, automatic welding, semi-automatic welding, carbon dioxide gas shielded welding, argon arc welding and electric arc welding are used depending on the structure of the product.
Manual welding and carbon dioxide gas shielded welding are most commonly used in general workshops. The main hazardous chemical substance generated during welding is welding fumes, followed by harmful gases. Welding fumes are the main hazardous chemical substance in the welding shop.
“Hygiene standard for welding fumes in workshop air” (GB16194-1996) stipulated that the maximum allowable concentration of welding fumes in workshop air is 6mg/m 3 (with the main components being iron trioxide, iron oxide, manganese, sulfur dioxide and calcium oxide), and harmful gases include ozone, nitrogen oxides, carbon monoxide, fluorides and chlorides.
Furthermore, the “Industrial Enterprise Project Hygiene Standard” (TJ36-79) specifies that the concentration of manganese oxide should be 0.2mg/ m3, general dust should be 10mg/ m3 , and fluorides should be be 1mg/m 3 .
The maximum permitted concentration of welding fumes in the welding shop is 6mg/m 3 . The wind speed for manual welding should be less than 8m/s, and for gas shielded welding, it should be less than 2m/s. Relative humidity must be below 90%. Prolonged exposure to high concentrations of welding fumes can cause lung disease in the welder.
Therefore, addressing welding fumes in the welding shop is an urgent problem. The control of welding fumes must begin with the promotion of clean processes, such as the adoption of welding processes with little or no fumes, the development and use of welding materials with low dust content and low toxicity, and improving the level of mechanization and automation of welding operations.
Furthermore, a well-designed ventilation system is an effective measure to deal with welding fumes in the welding shop.
Table 1: Chemical Composition of Welding Fumes from Common Structural Steel Electrodes (%)
Welding Electrode Grade | Faith 2 Ó 3 | SiO2 | MnO | TiO2 | Dog | |
421 | 45.31 | 21.12 | 6.97 | 5.18 | 0.31 | |
422 | 48.12 | 17.93 | 7.18 | 2.61 | 0.95 | |
507 | 24.93 | 5.62 | 6.3 | 1.22 | 10.34 | |
Welding Electrode Grade | MgO | N/A 2 Oh | K 2 O | CaF 2 | K.F. | In F |
421 | 0.25 | 5.81 | 7.01 | – | – | – |
422 | 0.27 | 6.03 | 6.81 | – | – | – |
507 | – | 6.39 | – | 18.92 | 7.95 | 13.71 |
2. Warm up
The design indoor temperature for the welding shop during winter is set at 14°C, with additional heating of 5°C for work shifts. Heating is achieved through a combination of radiators and hot air fans.
Radiators ensure a heating temperature of 5°C for service shifts, while hot air blowers work together with the radiators to provide internal heating for the welding shop during winter.
The placement of hot air blowers should be in areas where there is the most human activity, and the airflows from the blowers should be coordinated while avoiding a strong airflow toward individuals.
To avoid heat loss inside the workshop, air curtains must be installed at the entrances. The heating system that uses radiators must be separate from the heating system that uses hot air fans and air curtains.
3. Ventilation Methods and Comparison
3.1 Zone of Maximum Welding Fume Concentration
During welding, a large amount of harmful fumes and gases are generated, which spread evenly throughout the workshop along its height.
However, there is a zone of maximum welding fume concentration within the welding shop, which can be referred to as the appropriate height. Values for appropriate height are listed in Table 2.
Table 2: “Appropriate Height” Determined by Current Strength
Current intensity (A) |
Welding electrode diameter (mm) |
Height of maximum dust concentration (m) |
120 | 4 | 4 |
140 | 4 | 4.7 |
180 | 4.0~5.0 | 6 |
200 | 5 | 6.6 |
280 | 5.0~6.0 | 9.3 |
300 | 6 | 10 |
350 | 6.0~8.0 | 11.6 |
400 | 6.0~8.0 | 13.5 |
500 | 8.0~9.0 | 17 |
3.2 Emission Standards
The welding fume exhaust system generally does not require purification measures and can be discharged directly to the outside.
If the exhaust system circulates indoors, purification measures must be taken and the concentration of harmful substances in the exhaust gases must not exceed 30% of the maximum concentration permitted in the workshop.
3.3 Local Exhaustion
In the welding shop, local exhaust ventilation should be implemented as much as possible at points where harmful substances are generated.
Local exhaust can be divided into fixed local exhaust systems and small-scale portable smoke and dust removal units. Control air velocities for different types of exhaust fans are shown in Table 3.
Table 3: Air speed control for different types of hoods
Type of hood | Controlled air speed (m/s) | |
Ventilation cabinet | 0.7 | |
External exhaust fan | Side suction | 1.0 |
Bottom suction | 1.0 | |
Superior suction | 1.2 |
3.4 Comprehensive Ventilation
When welding positions in the workshop are not fixed and local exhaust fans cannot be used, comprehensive ventilation must be implemented.
Comprehensive ventilation is a type of dilution ventilation that uses clean outdoor air to dilute harmful substances indoors and exhaust them outside.
The effectiveness of comprehensive ventilation depends on sufficient ventilation airflow and adequate airflow organization.
The exhaust air flow for comprehensive ventilation is determined based on the consumption of welding electrodes. However, in the absence of this data, the exhaust air flow can be calculated as 3500m3/h per welding point.
In terms of addressing the hazards of dust and toxic substances in the welding shop, if ventilation measures can meet the requirements for the highest allowable concentration of welding fumes, the concentrations of various harmful gases generated during welding operations can also be be reduced below the maximum allowed. concentration. Exhaust air flow for in-house produced welding electrodes can be found in Table 4.
Table 4: Exhaust air flow for in-house produced welding electrodes
Note | Exhaust air flow (m 3 /kg of welding electrodes) |
T-46 | 2000 |
T-47 | 2500 |
T-48 | 4000 |
T-49 | 4500 |
T-45 | 2000 |
T-51 | 4500 |
TU-55 | 2000 |
Stainless Steel Welding Electrode | 3,000 |
The consumption of welding electrodes can be roughly estimated based on the following indicators when data is missing:
- Structural steel welding for building structures: 7kg/t to 8kg/t of steel structure
- Steel plate welding: 10kg/t to 15kg/t of steel structure
- Welding plate type cranes: 22kg/t steel structure
3.4.1 Natural Ventilation
In areas of China where centralized heating is not available, comprehensive ventilation can be achieved using skylights and ridge fans. Single-span workshops are easier to arrange for natural exhaust ventilation compared to multi-span workshops.
However, when the height of the factory building significantly exceeds the suitable height, and when the area where the factory is located suffers more than half the year from rainy and cloudy days, mechanical ventilation must be added.
For small amounts of welding and shorter heights, single-span shops located near exterior walls can utilize high side windows for comprehensive exhaust ventilation.
- Advantages: No need for energy, relatively economical.
- Disadvantages: Susceptible to environmental changes, unstable ventilation air flow.
3.4.2 Mechanical Ventilation
1) Ducted exhaust:
Exhaust ducts are placed horizontally above the welding area in the workshop, with exhaust outlets installed at suitable heights. Ducts are connected to exhaust fans to discharge air to the outside.
Mechanical make-up air is also provided, with 50% to 80% (considering the upper limit in extremely cold regions and the lower limit in general regions) supplemented by mechanical make-up air from air conditioning units, while the remaining make-up air naturally seeps through doors and window gaps.
In winter heating regions, mechanical make-up air often uses air conditioning units with a heating section. The heat supplied by the heating section of the air conditioner does not account for the indoor heat load. The heat Q of the heating section is calculated as follows:
Q = Heat consumption from workshop exhaust + Heat consumption from cold air infiltration through door and window openings + Heat introduced by the heating section of the unit (from ambient temperature to supply air temperature)
When supplying air to workstations within 2 meters or up to 2 meters, the temperature of the supplied air must not exceed 45°C or be less than 25°C, and the outlet velocity must not exceed 1.5 m/s 2 .0 m/s. The supply air outlets must be positioned as low as possible and close to the welding area.
In unheated regions, mechanical make-up air in winter does not require heating, so fan make-up air can be used directly to save workshop space. Fans can be installed using hanging methods.
Make-up air should be directed away from the welding area, allowing the airflow to flow toward the welding area. The airflow speed inside the ducts must be between 6 m/s and 14 m/s (for steel ducts).
For workshops in heating regions with high exhaust air flow, if conditions permit, sensible heat recovery devices (such as metallic rotary air heat exchangers) can be used to recover heat from the exhaust air and provide it to complementary air.
- Advantages: This comprehensive ventilation method is more effective for ventilation in welding workshops and can effectively remove welding vapors accumulated at appropriate heights in the workshop. Since the ventilation equipment is located inside the workshop, it does not affect the external appearance of the workshop building.
- Disadvantages: Due to the presence of pipes and cranes in the welding shop, it can be challenging to lay horizontal ducts above the welding area. When using air conditioning units for make-up air in winter heating regions, it also takes up space in the workshop.
2) Roof ventilation fan and jet fans for exhaust:
When there are no skylights in the welding shop, ceiling fans can be installed on the roof of the shop for overhead exhaust. This method alone may not directly exhaust smoke and dust to appropriate heights in the workshop, so multiple jet fans can be installed in workshop columns to disturb the air and assist ceiling fans in exhausting.
Mechanical makeup air is also required, following the same method as ducted exhaust (see Figure 1).
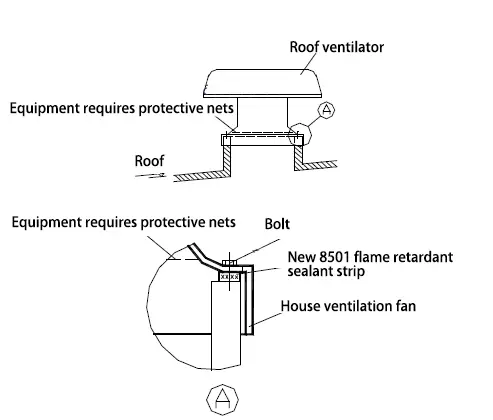
- Advantages: This comprehensive ventilation method avoids the difficulty of laying pipes in the welding shop.
- Disadvantages: Since the exhaust points are not directly adjusted to the appropriate height in the welding shop, the effectiveness of the exhaust is relatively lower compared to the ducted exhaust. Roof fans are installed on the roof of the workshop, and due to the large exhaust air flow in the workshop, the number of roof fans is more, which has a certain impact on the external appearance of the workshop building.
3) Roof ventilation fan exhaust:
When there are no skylights in the welding shop, ceiling fans can also be installed on the roof of the shop for exhaust. However, a duct needs to be extended from the ceiling fan to the appropriate height in the welding shop to remove a large amount of welding fumes accumulated at the appropriate height for exhaust. Mechanical makeup air is also required, following the same method as ducted exhaust.
- Advantages: This comprehensive ventilation method also helps to a certain extent to solve the problem of a large accumulation of welding fumes in the welding workshop.
- Disadvantages: Due to the presence of pipes and cranes in the welding shop, it can be challenging to extend a ceiling fan duct above the welding area. Roof fans are installed on the roof of the workshop, and due to the large exhaust air flow in the workshop, the number of roof fans is more, which has a certain impact on the external appearance of the workshop building.
4) Welding fume purification unit: Welding fume purification units are installed in the columns of the welding shop. Shop air containing welding fumes enters the unit from the rear, passes through filters to remove fumes, and is discharged from the front.
- Advantages: Simple equipment configuration.
- Disadvantages: Relatively expensive equipment.
5) Axial fan exhaust: For single-span, small-area, low-height workshops or when the welding area is located close to the outer walls of the workshop, multiple axial fans can be installed at higher positions on the outer walls close to the welding area for exhaustion. This method is commonly used in small businesses.
Therefore, when designing ventilation for welding shops, a combination of comprehensive mechanical ventilation, local mechanical exhaustion and comprehensive natural ventilation should be considered based on actual conditions.
4. Thermal Insulation and Cooling
Wall-mounted electric fans and portable electric fans are commonly used methods to cool and improve the working environment in the workshop during summer.
5. Airflow organization
When considering intake and exhaust airflow in single-span or multi-span welding shops, natural intake must be from both sides through doors and windows, mechanical makeup air must be supplied to the welding and horizontal ducts for mechanical exhaust must be installed above the welding area or ceiling fans must be installed on the roof to facilitate airflow movement in the workshop and more effectively remove welding fumes generated during welding.
6. Conclusion
1) Welding fume management in welding shops has been a challenging issue for a long time. The author believes that a combination of local exhaust and comprehensive ventilation, especially the use of horizontal ducts placed above the welding area for comprehensive mechanical exhaust when conditions permit, is currently an effective method.
2) With technological advancements, an increasing number of newly constructed large-scale welding shops are using aesthetically pleasing, lightweight steel roofs. This requires close coordination with civil engineering professionals when installing roof fans and overhead fans to resolve equipment load-bearing and vibration issues.
3) For users, the correct use of local exhaust and comprehensive ventilation equipment is also essential to ensure air quality in the workshop.