Pneumatic Transmission
Pneumatic transmission involves the transfer of energy by gas or fluid pressure through compressed gas as the working medium.
The energy transfer system involves transferring compressed gas through tubes and control valves to the pneumatic actuator, which transforms the pressure of the compressed gas into mechanical energy.
The information transmission system involves using pneumatic logic elements or jet elements to carry out logic operations, also known as a pneumatic control system.
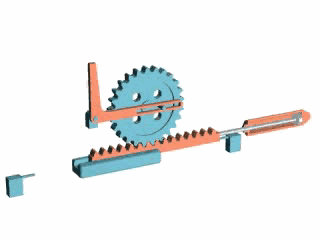
Features of pneumatic transmission
With a low working pressure, on average 0.3 to 0.8 MPa, pneumatic systems have low gas viscosity and minimal losses in the pipes, which makes them advantageous for supplying and transporting gas over moderate distances. These systems are also safe to use as they pose no explosion or shock hazards and have overload protection features. However, it should be noted that pneumatic systems require compressed air supply.
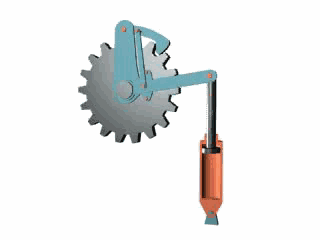
Pneumatic transmission composition
The pneumatic transmission comprises an air source, pneumatic actuator, pneumatic control valve and pneumatic accessories.
Air sources are normally supplied by compressors.
The pneumatic actuator converts compressed gas pressure into mechanical energy to drive functional parts such as cylinders and pneumatic motors.
Pneumatic control valve adjusts the direction, pressure and flow of air and is categorized into directional control valves, pressure control valves and flow control valves.
Pneumatic accessories include air purifiers, air lubricators, noise silencers and pipe joints, among others.
Aerodynamic sensors are also used to detect and transmit information in pneumatic transmission systems.
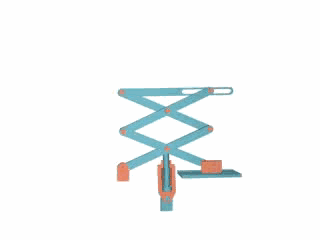
Advantages of pneumatic transmission
Pneumatic transmission uses air as a medium, which is an inexhaustible and easily accessible source that can be discharged directly after use without polluting the environment. Furthermore, the pipeline is not complex as there is no need for a return pipe.
Air has low viscosity and flow energy dissipation, making it suitable for centralized gas supply and long-distance transportation.
Pneumatic transmission is safe and reliable, does not require fire or explosion protection, and can operate in environments with high temperatures, radiation, humidity, dust and other conditions.
Pneumatic transmission is fast and the structure of pneumatic components is simple, making them easy to process and maintain with a long service life. The pipeline is not subject to clogging and the medium has no problems with metamorphic replacement.
Disadvantages of pneumatic transmission
The high compressibility of air can negatively impact the dynamic stability of pneumatic systems, resulting in a significant impact on working speed due to load changes.
The low pressure of pneumatic systems makes it difficult to produce great power and torque.
Air control signal transmission is slower than that of electronic and speed-of-light systems, making it unsuitable for complex, high-speed transmission systems.
Pneumatic systems generate a lot of exhaust noise.
Hydraulic Transmission
Hydraulic transmission is the transmission of power and control using liquid as the working medium.
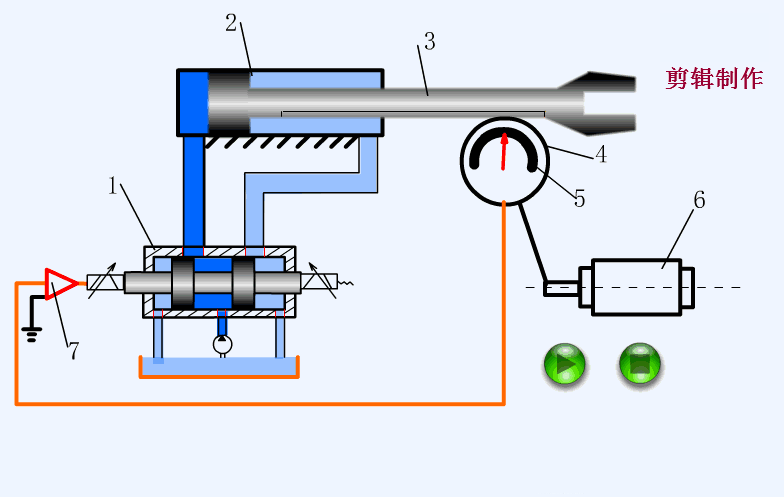
The basic principle of hydraulic transmission
Hydraulic pumps convert mechanical energy into liquid pressure energy, which is then transferred through changes in liquid pressure. A variety of control valves and tubes are used to transmit power to hydraulic actuators, such as hydraulic cylinders or motors, which convert liquid pressure into mechanical energy to drive the working mechanism, allowing reciprocating and rotary motion in a straight line.
The liquid used is called working medium, and mineral oil is commonly used for this purpose.
The function of hydraulic transmission is similar to that of transmission elements in mechanical transmission, such as belts, chains and gears.
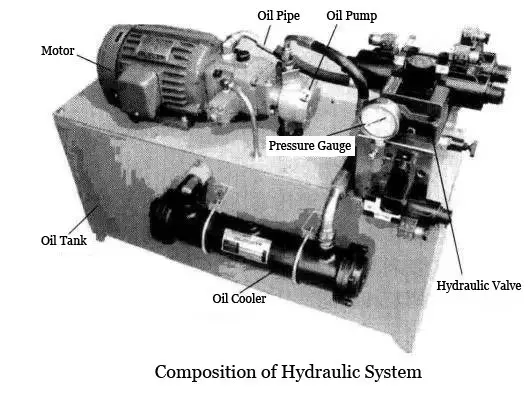
Hydraulic transmission system
The hydraulic system consists of a hydraulic pump, hydraulic control valve, hydraulic actuators (such as cylinders and hydraulic motors) and auxiliary hydraulic parts (including piping and accumulators, among others).
Press brakes are an example of a system that uses hydraulic transmission.
Hydraulic transmission system components
The hydraulic system comprises various components, including power components (such as hydraulic pump), actuators (including hydraulic cylinders and hydraulic motors), control elements, auxiliary components (such as fuel tanks, oil filters, pipes and joints, coolers, pressure gauges) and the working medium (i.e. hydraulic oil).
Power components, such as the hydraulic pump, convert mechanical energy into fluid kinetic energy (pressure and flow) and supply oil under pressure to the hydraulic system, acting as the system's energy source.
Actuators, such as hydraulic cylinders or hydraulic motors, convert hydraulic energy into mechanical energy and are isothermal. Hydraulic cylinders drive mechanisms to perform reciprocating or linear movements, while hydraulic motors perform rotational movements.
Control elements, which refer to various components, are used to control and adjust the pressure, flow and direction of fluid in the hydraulic system, ensuring that actuators operate according to required specifications.
Auxiliary components provide the necessary conditions for the correct functioning of the system and facilitate monitoring and control.
The working medium is transmission fluid, typically hydraulic oil. The hydraulic system uses this working medium, which also lubricates the moving parts of the hydraulic components.
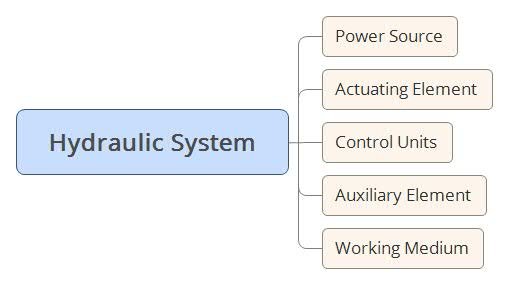
The working principle of hydraulic transmission system
Here is an example of a simple grinder.
The engine drives the hydraulic pump to remove oil from the tank, which transforms the engine's mechanical energy into liquid pressure energy.
The hydraulic medium enters the left cavity of the hydraulic cylinder through the butterfly valve and reversing valve, pushing the piston to move the right side of the table. The hydraulic medium is then discharged from the right cavity of the hydraulic cylinder, flowing back into the tank.
After passing through the reversing valve, the hydraulic medium enters the right cavity of the hydraulic cylinder, causing the piston to move to the left and push the table backwards.
The speed of movement of the hydraulic cylinder can be adjusted by changing the throttle opening.
Hydraulic system pressure can be adjusted using the relief valve.
When drawing a hydraulic system diagram, symbols are used to represent hydraulic components for simplification. These symbols are called functional symbols.
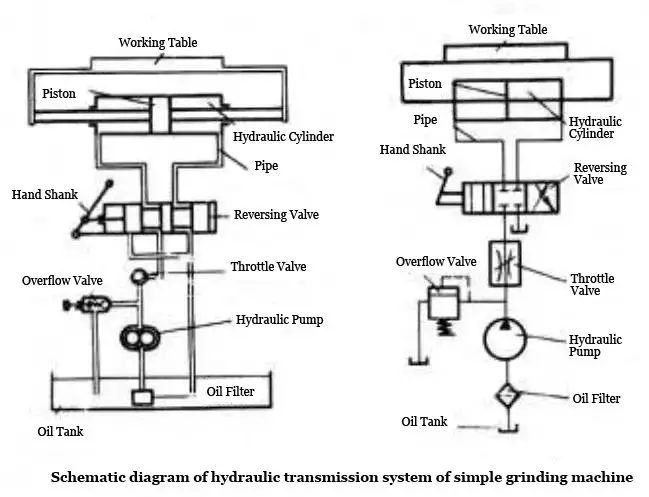
Basic circuit
A typical hydraulic transmission system comprises several hydraulic components that work together to achieve specific functions.
Any hydraulic transmission system is made up of several basic circuits, each with specific control functions. By combining these basic circuits, the movement direction, working pressure and movement speed of the actuator can be controlled.
Based on its control function, the basic circuit is divided into three types: pressure control loop, speed control loop and direction control loop.
1. Pressure control circuit
The pressure control valve is used to control the entire system or a local range pressure circuit.
Based on its function, the pressure control circuit can be divided into four circuits: pressure adjustment, pressure change, pressure release and pressure stabilization.
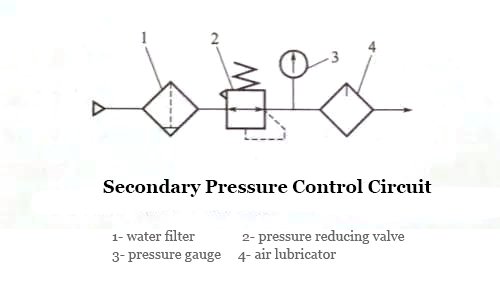
2. Speed Control Loop
This circuit controls the actuator flow by regulating the flow of the hydraulic medium. The function of the speed control loop is divided into two parts: the speed regulation circuit and the synchronization loop.
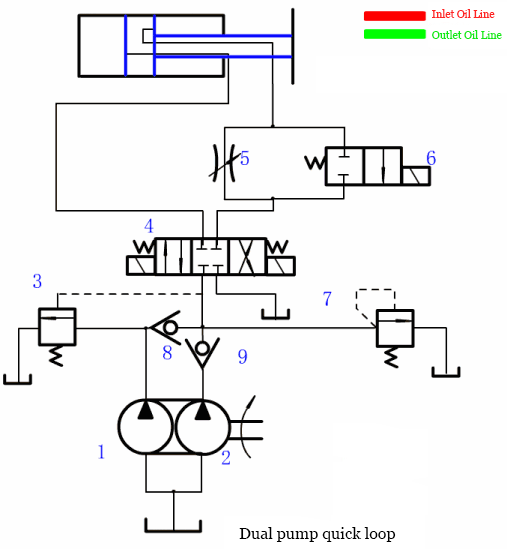
3. Direction control loop
This circuit controls the direction of flow of the hydraulic medium. The directional control valve controls the direction of movement of a single actuator, allowing it to move or stop in both positive and negative directions, which is known as a commutator circuit.
When the actuating element stops, the circuit that prevents external leakage due to load or other external factors is called the latching circuit.
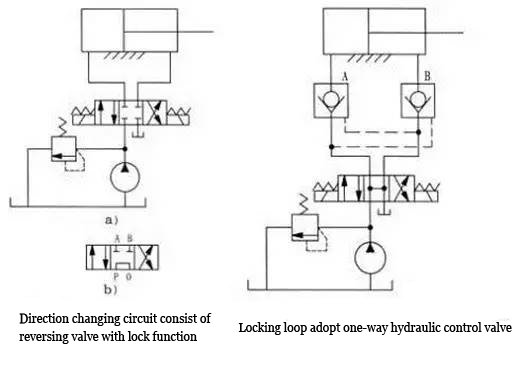
Hydraulic Drive
Hydraulic transmission involves the transfer of energy through net kinetic energy, using liquid as the working medium.
The impeller converts the rotational speed and torque input of an engine (such as an internal combustion engine, engine, turbine, etc.) and drives the machine's working parts through the output shaft.
The fluid and impeller interact with each other at the input shaft, output shaft, and casing, producing a change in momentum to transmit power.
Hydraulic transmission differs significantly in principle, structure and performance from fluid pressure-based hydraulic transmission.
The input shaft and output shaft of the hydraulic drive are only connected to the working medium through liquid, and the non-direct contact between the components results in non-rigid transmission.
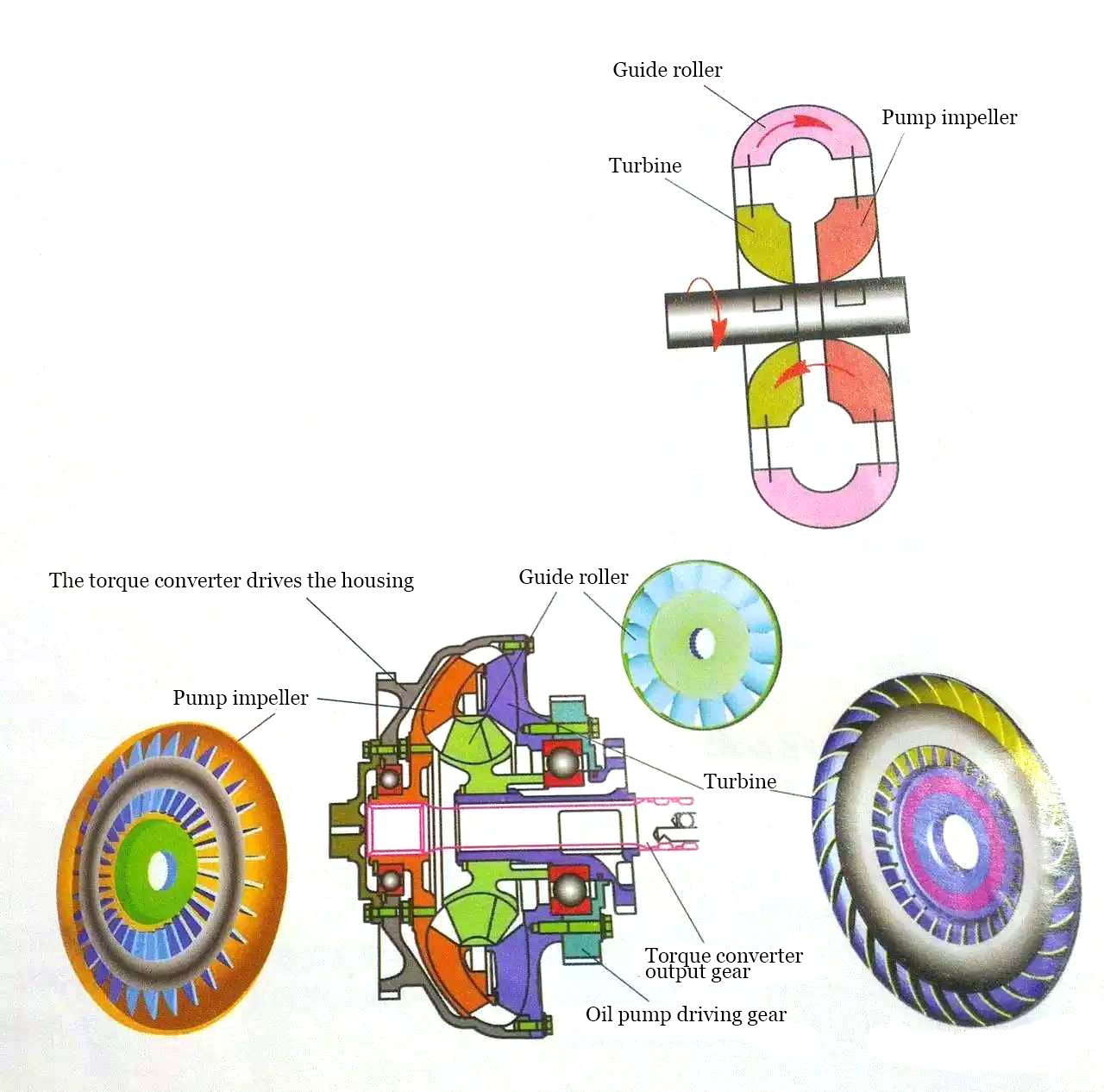
Features of the hydraulic drive
Automatic adaptability
The hydraulic torque converter can automatically increase or decrease its output torque with changes in external loads, and the speed can increase or decrease correspondingly, achieving stepless speed regulation within a wide range.
Vibration isolation
As the working medium between the impellers is liquid, their connection is not rigid, enabling the absorption of shocks and vibrations from the engine and external loads. This ensures stable starting, acceleration and uniform operation, extending the life of parts.
Penetration performance
When the rotational speed of the pump is constant and the load changes, the input shaft (that is, the pump wheel or motor shaft) changes.
Different types of hydraulic elements can be used to meet engine requirements for different working machines, improving mechanical power and economic performance.
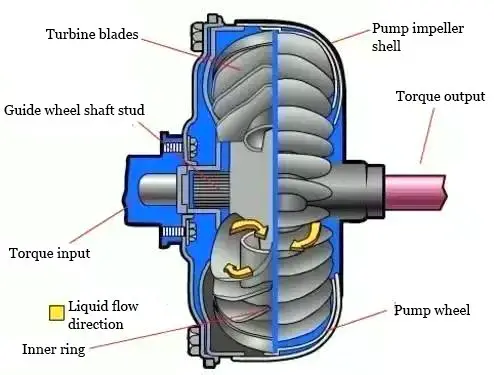
The basic principle of hydraulic drive
The original energy source (such as an internal combustion engine, engine, etc.) drives the rotation of the pump wheel, increasing the speed and pressure of the working fluid and converting mechanical energy into net kinetic energy.
The working liquid, now with kinetic energy, hits the turbine and releases energy to the turbine, causing it to rotate and power the output, transferring energy.
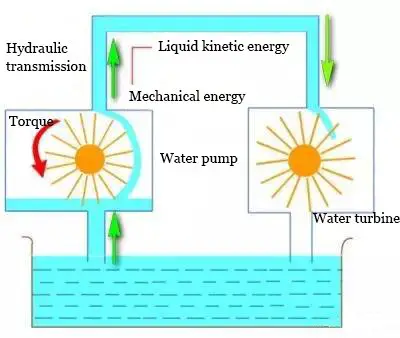
Hydraulic transmission device
Hydraulic transmission uses net kinetic energy to transfer power and generally includes hydraulic couplers, hydraulic torque converters, and hydraulic mechanical components.
1. Hydraulic coupler
A hydraulic coupler, also known as a hydraulic coupling, is a mechanical device used to connect a power source (usually a motor or engine) to a running machine to provide rotational power.
In addition to use in automobile automatic transmissions, hydraulic couplers are widely used in marine and heavy industries.
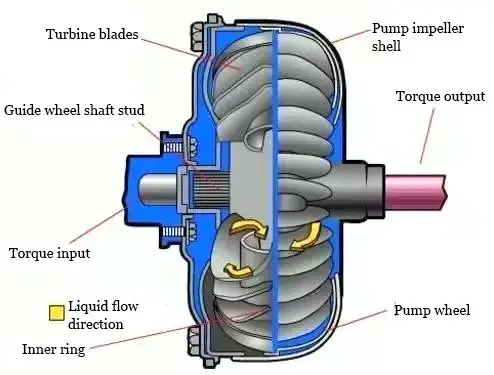
2. Torque converter
A hydraulic torque converter is a hydraulic element consisting of a pump wheel, turbine and guide wheel. It is installed between the engine and transmission and uses hydraulic oil as the working medium to transmit and convert torque, adjust speed, and provide disconnect functionality.
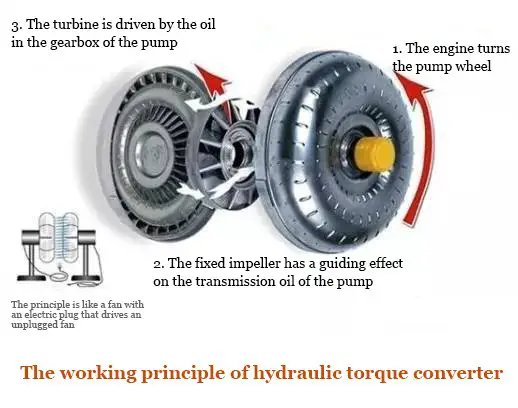
Hydraulic drive application
The use of hydraulic transmission in modern machines began in the early 20th century, mainly as naval power equipment and transmission mechanisms between propellers to solve the problem of limited speed due to high power and high-speed steam or gas turbines. who suffer from “cavitation”. ”
Today, hydraulic transmission is widely used in automobiles, tractors, construction machines, railway locomotives, armored vehicles, oil drilling machines, lifting and transport machines, fans, pumps and other equipment.