Bearings are a critical component to the reliability, efficiency and life of your equipment. Most rotating process equipment today relies on roller bearings or fluid film bearings to counteract gravity and other forces on the equipment and allow the shaft to rotate freely. Choosing the right bearing for your equipment and application is essential for the proper functioning of that equipment.
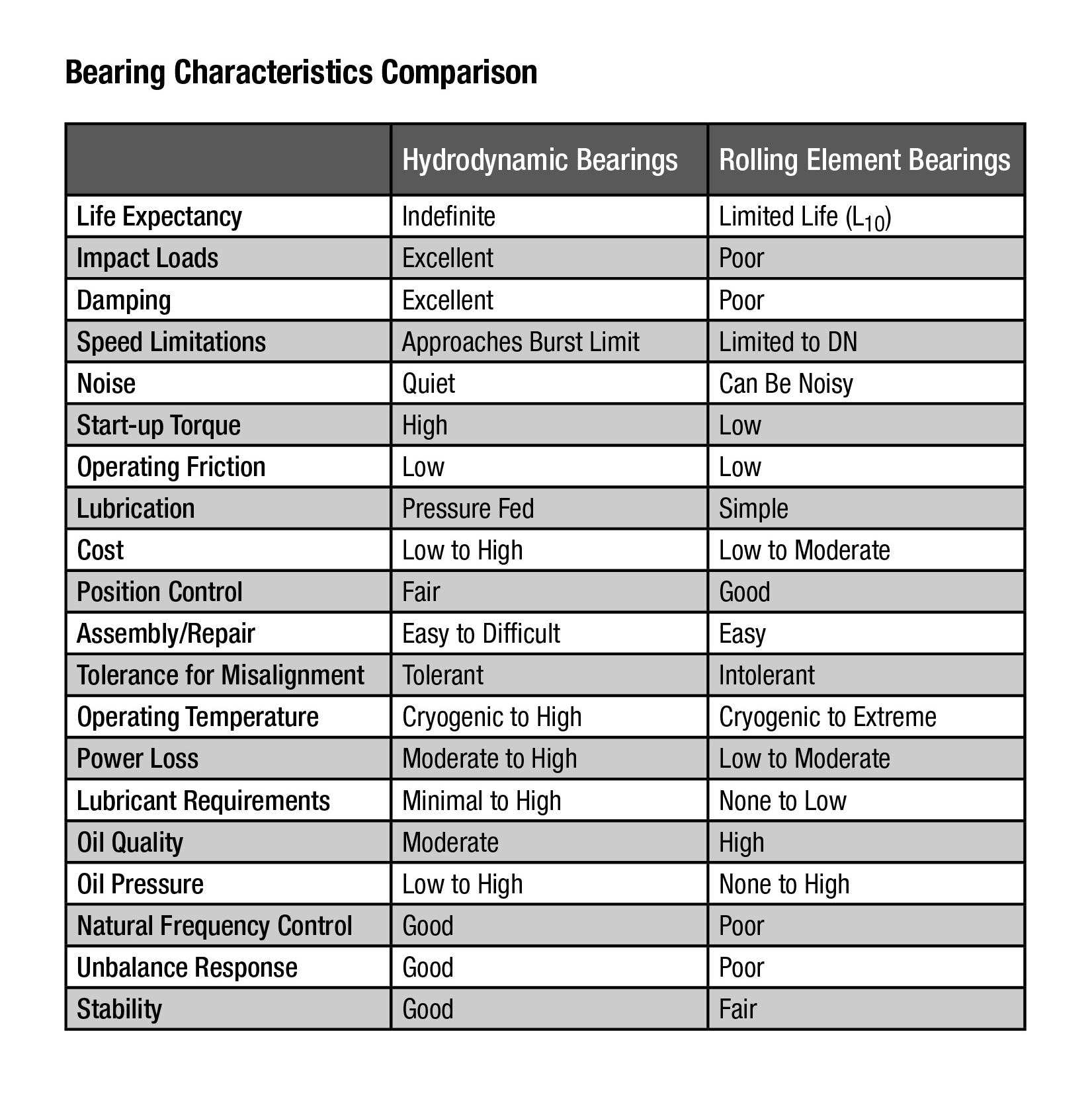
Table 1. Operators can compare the qualities of hydrodynamic bearings and rolling elements.
A key difference between bearings and fluid film bearings when it comes to process equipment maintenance is the expected service life of the bearings. Bearings typically have a predictable lifespan based on operating conditions. If designed and maintained properly, fluid film bearings can operate for decades. Additional comparisons of rolling element and fluid film bearing characteristics, such as lubrication needs and ability to handle shock loads, are provided in Table 1.
Correct selection of materials and mechanical design is the basis of the long service life of a fluid film bearing. Typical factors affecting material selection include load, speed, operating temperature, insulation requirements, and lubricant type and cleanliness. Depending on your needs, material options include babbitt (also known as white metal), bronze, aluminum pewter, polymer, ceramic, cermet
and diamond.
For mechanical design, the fluid film bearing designer must not only consider properly sizing the bearing to handle loads and minimize power loss, but also incorporate features to optimize film formation and tune the dynamics characteristics of the bearing. . Fine-tuning bearing characteristics improves bearing performance
process equipment.
Basic working principle
The stationary surface of a fluid film bearing is separated from the rotating surface by a thin film of lubricant, such as oil, air, water or process fluid. In hydrodynamic fluid film bearings, the film pressure that separates the surfaces and neutralizes the loads is created by the relative motion (rotation) of the surfaces as the lubricant is pulled into a converging geometry between the surfaces. Due to this separation force, surface contact does not occur during normal operation, reducing wear and energy loss compared to surface-to-surface contact.
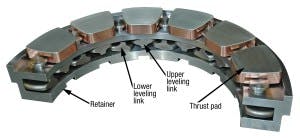
A self-leveling tilt bearing thrust bearing can accommodate misalignments.
Thrust bearings resist axial loads, which are loads along the axis of rotation, while thrust bearings support radial loads, which are perpendicular to the axis of rotation. The materials and design of thrust and trunnion fluid film bearings are selected to optimize bearing geometry for greater process equipment efficiency and fewer auxiliary equipment demands.
Materials
The selection of materials of construction for a fluid film bearing is based on two main factors: application requirements and operating environment.
Bronze can be used when operating temperatures are above the limit. Oil-lubricated bronze bearings are common in process equipment applications where the bearing surface can reach 150°C (302°F) and in some cases even higher. This may cause damage to the shaft or bearings in the presence of contaminants or misalignment. Additionally, care must be taken when selecting the rotating surface material when using bronze bearings to limit the potential for damage to rotating components.
For rotary and reciprocating process equipment that requires higher temperature or better formability and adjustability than bronze, tin-alloyed aluminum can be used as the bearing material. Aluminum tin can operate at higher temperatures of up to 160°C (320°F) and does not fatigue easily. Aluminum cans are applied to steel for greater strength or to chrome-copper for improved heat transfer. Both can be used against a variety of rotating components, including mild steels.
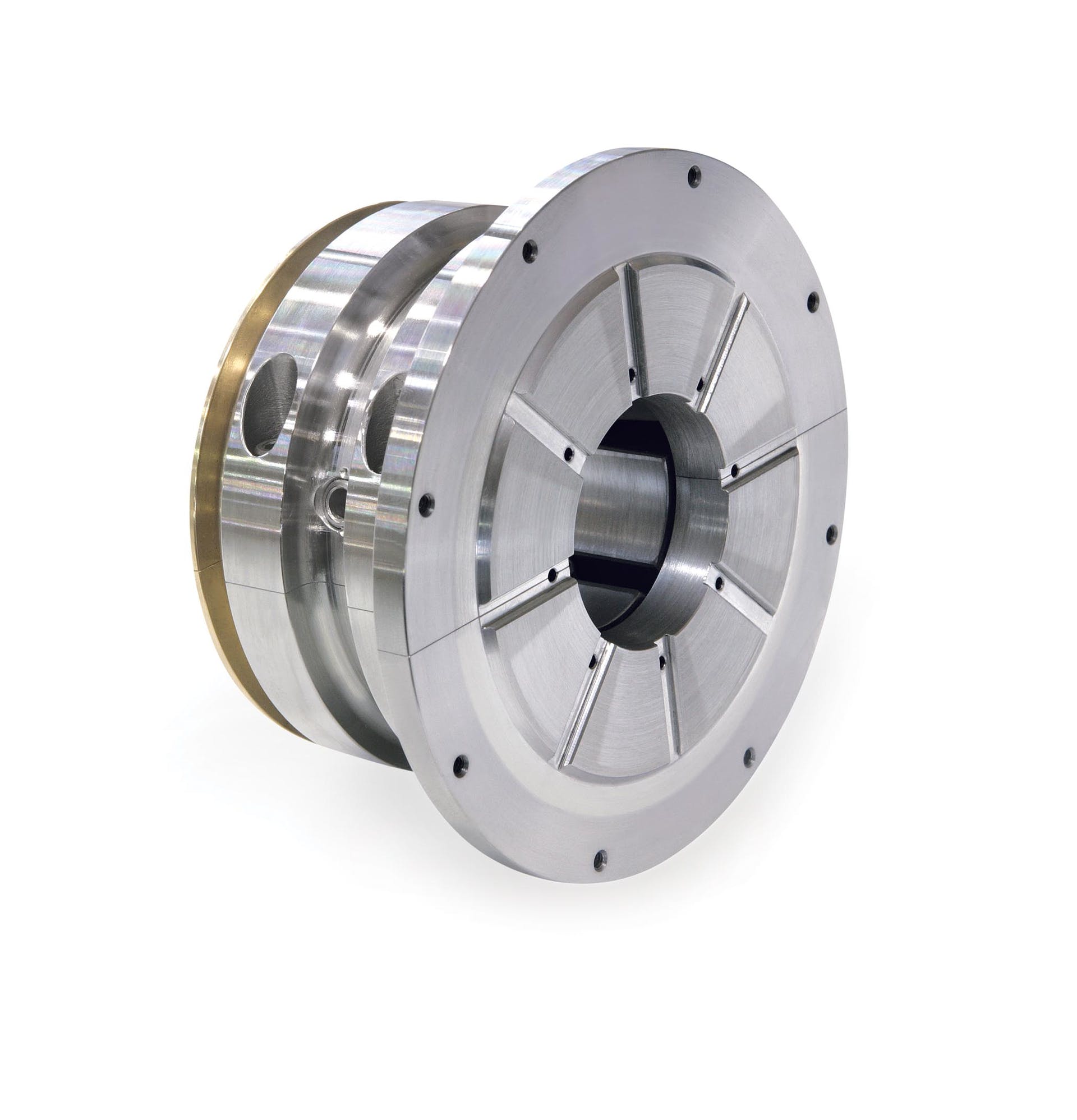
A combination of tapered fixed profile thrust bearings and tilt bearings
Polymers engineered as solid components or as coatings on steel supports are also widely accepted in process equipment. Polymer bearings feature embeddability and formability and can operate at higher temperatures and loads. Because they operate with relatively thin films, polymer thrust bearings are often used in oil-lubricated applications with unit loads up to 8 megapascals (1,160 psi), which is approximately twice the load generally accepted by Babbitt bearings, and temperatures of up to 200°C. (392°F).
Polymer bearings are also less susceptible to chemical attack, insulate against electrical currents, and function successfully in a variety of lubricants, including water and process fluids. With the correct material composition, polymer bearings can resist film breakage due to overload or temporary loss of lubrication.
When high temperatures, corrosive materials or contaminated lubricants prevent the use of aluminum, tin, bronze and polymer, fluid film bearings can be manufactured with extremely hard surfaces. Ceramics and diamond have been used successfully when operating temperatures exceed 200°C (392°F), when films are very thin and/or when abrasives are present. Aluminum, tin and polymer, which can work against mild steels and other traditional shaft materials, ceramics and require a deliberate choice of material for rotating and stationary surfaces to achieve desired bearing life and performance, especially when abrasives are present or The films are extremely thin.
The best material for bearings can vary even within the same assembly, and material alone does not guarantee performance. Carefully selected materials must be combined with an optimal mechanical design.
Bearing design
Film formation is critical to the life and performance of a fluid film bearing. A viscous lubricant, relative movement between surfaces and convergent bearing geometry are essential for film development. Together, they create pressure to counteract gravity and other forces acting on the tree.
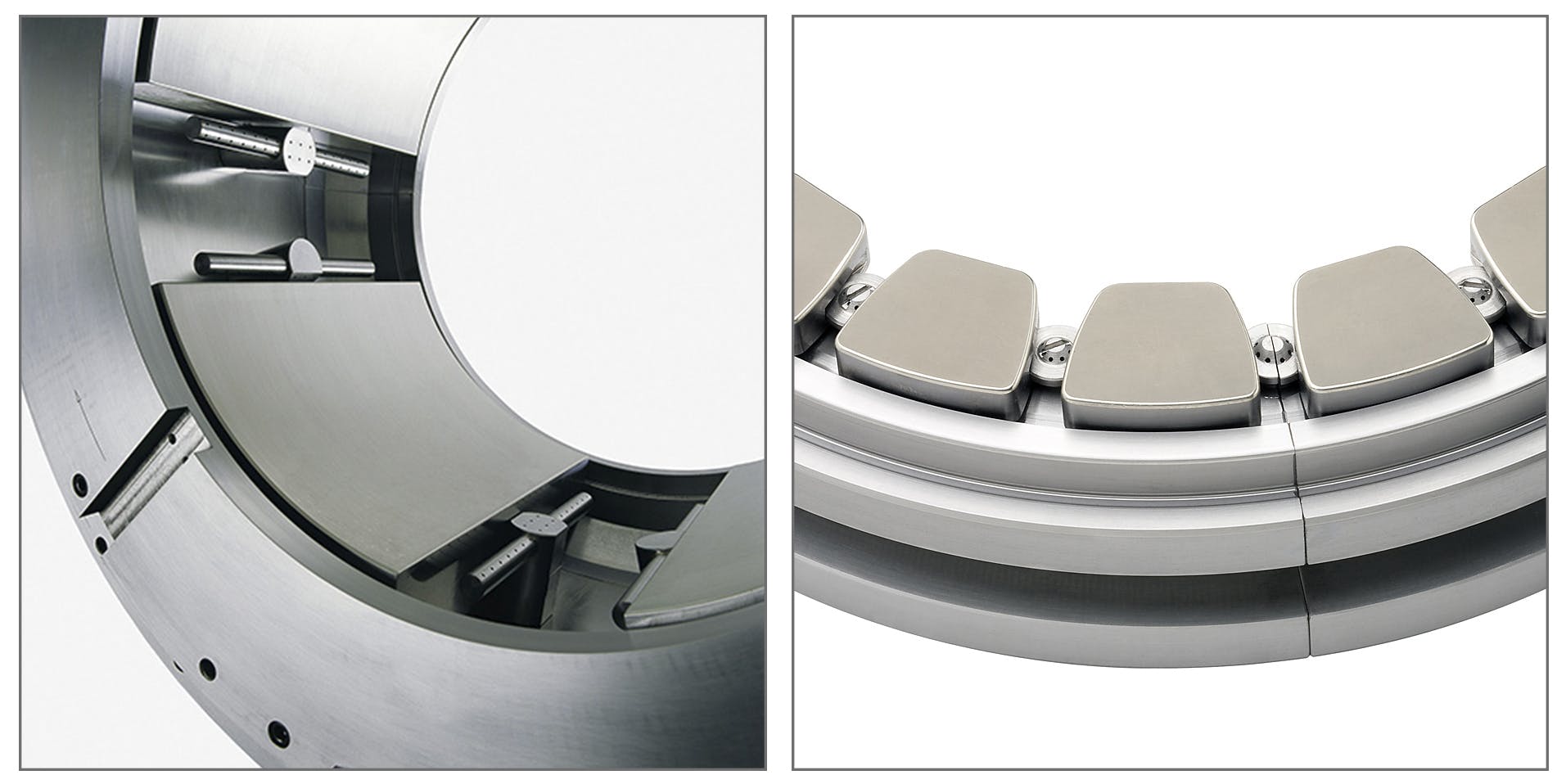
Plain (left) and thrust (right) bearings showing two styles of direct lubrication.
Although axial loads can be supported with flat bearing faces, geometry is typically machined into the surface of a fixed profile thrust bearing to create a converging wedge and increase the bearing's load capacity. A fixed geometry is designed for a specific condition, therefore thrust bearings with tiltable inserts are often used to adapt to changing conditions. Self-leveling tilt shoe thrust bearings compensate for misalignment between the bearing and collar, equalizing the load between the shoes.
Due to the different bearing and shaft diameters, a journal bearing naturally has a converging wedge when the shaft is not centered in the bearing. To improve static and dynamic performance, a defined profile can be machined into the bearing to reveal the appropriate film. Pivot tilt bearings are often used if stability is a concern, if variable conditions need to be accommodated, or if other bearing performance parameters require optimization.
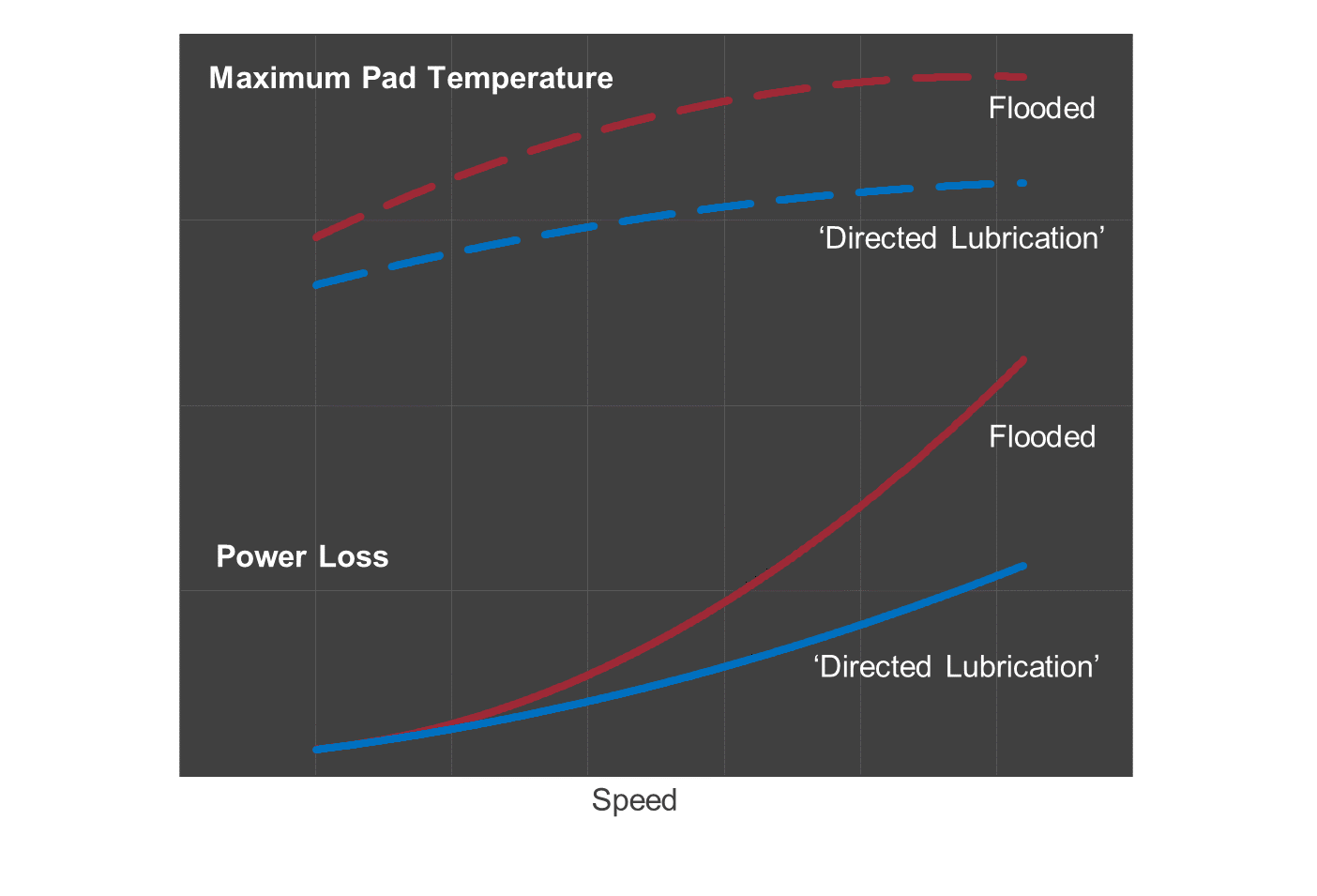
Changing from a lightly loaded bearing with flood lubrication (point A) to a smaller optimized bearing with direct lubrication (point B) can significantly reduce power loss.
Thrust and trunnion bearings are sized to handle application load requirements and fit into the specified enclosure. Other characteristics can be optimized to achieve specific static performance in thrust bearings and dynamic and static performance in trunnion bearings. The arc of the pad, or the part of the pad that develops pressure, can be adjusted to influence power loss and temperature. Offset, or the distance of the leading edge of the trunnion relative to the pad arc, has a significant effect on film formation and can influence bearing temperatures, power loss and, in the case of trunnion bearings, performance. dynamic.
In particular, in tilt-roller bearings, temperatures, power loss and dynamic performance can be significantly affected by bearing clearance (the difference between the bearing bore and shaft diameter), bearing length and preload. The preload represents the deviation of the machined insert hole in relation to the mounted bearing hole. It is positive when the shoe hole is larger than the bearing hole, zero when the shoe hole and the bearing are the same, and negative when the shoe hole is smaller than the bearing hole. If the preload is positive, a converging wedge is formed. A negative preload limits flow into the pad and
is not recommended.
In both main bearings and tilting thrust bearings, the journal is selected based on specific needs such as required service life (stress), stiffness, and ease of tilting the journal in one or more directions. Common pin types are point contact, linear contact, ball and socket, and flexible pin. Each of them has distinct advantages.
Another design choice that significantly affects bearing performance is the method of introducing and removing lubricant into the bearing. By supplying lubricant to the leading edge of the rocker shoe and allowing the lubricant to flow freely from the bearing and its housing, directly lubricated bearings operate with lower power losses and at lower operating temperatures than flooded bearings, where the lubricant is typically fed away from the film and flow out of the bearing is limited. Flood lubrication creates a shear of lubricant on the outside of the film that does not contribute to the bearing's load capacity.
Putting it all together
The combination of selected materials and design features will further optimize performance compared to materials or design features alone. For example, combining direct lubrication with advanced material bearings, which can withstand thinner films, higher temperatures and therefore higher loads, can significantly reduce power loss compared to a flooded design with traditional bearing materials. The use of advanced materials allows for a smaller bearing and the use of lower viscosity fluid, even process fluid, thus reducing power loss. If reducing power loss is not necessary, a greater safety margin can be achieved.
With the right materials and design, fluid film bearings can offer world-class dynamic performance, low friction, little to no wear and long service life, making them the right choice to meet the needs of modern process equipment.